Quality, safety, productivity, traceability — these are crucial criteria for the medical industry, especially when manufacturing surgical implants via metal 3D printing. In this field, AddUp’s FormUp® 350 machine offers numerous advantages, addressing these vital needs effectively.
Read this blog to learn more about the diverse applications of Additive Manufacturing (AM) in the medical industry, focusing on how these criteria are met and surpassed in the production of surgical implants.
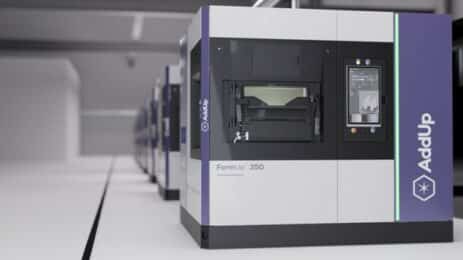
The market for surgical implants and patient-specific solutions is undergoing major changes. Manufacturers in this sector are seeking to provide doctors with more efficient and personalized devices, at costs acceptable to patients, while complying with particularly strict requirements for certification. New generations of 3D printers are achieving high levels of productivity/ quality and can produce parts in biocompatible materials like titanium. The new and improved printers allow implant manufacturers to consider the migration to metal additive manufacturing for many applications.
Diverse Applications of AM in Medical Procedures
Innovative Use in Prosthetics and Orthopedics:
Additive Manufacturing (AM) is revolutionizing the field of prosthetics and orthopedics. With the ability to create highly customized and complex structures, AM is being used to produce prosthetic limbs that are tailored to the individual needs of patients, enhancing comfort and functionality. Similarly, in orthopedics, AM is used to manufacture implants such as knee and hip joints, which are designed to mimic the natural movement of human joints more closely.
Dental Applications:
In the dental sector, AM is making significant strides. From crowns and bridges to orthodontic devices, 3D printing allows for rapid production and customization. This not only speeds up the dental restoration process but also increases the comfort and fit for patients.
Surgical Planning and Anatomical Models:
Surgeons are increasingly turning to 3D-printed anatomical models for pre-surgical planning. These models, created from patient-specific imaging data, allow surgeons to plan and practice complex procedures, thereby reducing surgery times and improving patient outcomes.
Bioprinting and Tissue Engineering:
A frontier area in AM is bioprinting, where living cells are printed to create tissue-like structures. This technology holds the promise for future applications like organ transplants and skin grafts for burn victims.
Customization and Personalization in Patient Care
Tailored Solutions for Improved Outcomes:
The ability of AM to produce customized medical devices is one of its most significant advantages. Custom-fit implants and prosthetics not only improve the comfort for patients but also reduce the risk of complications and improve recovery times.
Patient-Specific Implants:
With AM, implants are no longer one-size-fits-all. They can be designed to match the exact anatomical features of individual patients. This is particularly beneficial in complex cases where standard implants may not be suitable.
Personalized Surgical Instruments:
AM also allows for the creation of surgical tools that are specifically designed for individual surgeries or patients. This can lead to more precise and efficient surgical procedures.
Enhancing Patient Experience:
The customization capabilities of AM extend beyond physical devices to the overall patient experience. Take prosthetics, for example. They can be customized to do more than just fit perfectly; they can also be designed to match the patient’s unique style and personal preferences, adding a touch of individuality to each piece.
Future of Personalized Medicine:
As additive manufacturing technology advances, it’s opening the doors to an exciting new phase in personalized medicine. This means treatments and medical devices are crafted specifically for each individual, enhancing the effectiveness of healthcare and making it more centered around the patient’s unique needs
What is a machine designed for the medical sector?
The FormUp® 350 machine offers many advantages to meet the expectations of surgical implant manufacturers. Designed and produced by AddUp, a company created by the French groups Michelin and Fives, this 3D machine uses a technology called Laser Powder Bed Fusion (L-PBF). This process is particularly well suited to the production of complex, customized metal parts with high mechanical properties. It is also one of the most mature technologies in the metal 3D printing market. Several manufacturers, including AddUp, offer recipes for the use of biocompatible materials., In the medical implants field, the most common of these materials is a titanium alloy called Ti6Al-4V ELI, also referred to as Grade 23 Titanium.
AddUp’s L-PBF machine, the FormUp® 350, differs significantly from machines on the market in the following ways:
- Medium or fine powder usage. The flexibility to use metal powders with a small particle size (less than 25 microns) allows the machine to build parts with low roughness surfaces, fine feature details, and “lattice” features that promote osseointegration.
- The ability to use a variety of powder-spreading devices, including the roller device. The roller device creates a high-density powder bed that is suitable for the manufacture of unsupported parts, which greatly reduces the costs associated with post-processing operations. The roller recoater provides this advantage with both fine and medium powder sizes.
- Safety is of the utmost importance to AddUp. . Titanium alloys, in powder form, present risks for both equipment and operators. This risk is mitigated in the FormUp® 350 because the powder is always in an inert environment. The FormUp® 350 is the only machine on the market that allows for the supply and recycling of the powder without any contact with the ambient air. This prevents the risk of user exposure while simultaneously and consistently building parts that meet or exceed industry standards.
Beyond these characteristics, AddUp’s LPBF machine exceeds the industry requirements and expectations of OEM’sgiven the demands of productivity, quality, repeatability, and traceability.
Productivity criteria
The FormUp® 350 machine was designed based on Michelin’s early adoption of metal additive manufacturing. The challenge was not the technology but rather the consistency and throughput in a high-demand manufacturing environment. Developed by a manufacturer for manufacturers, the FormUp® 350 machine has been fine tuned to promote high productivity. One example is the use of large build plates (350 x 350 mm) with a quick loading and leveling system that avoids any loss of useful surface. In addition, four 500-watt lasers are used, each one with the ability to cover the entire surface of the build plate. The advantage for the user is great flexibility in the placement of the parts on the platform and in the assignment of the lasers (one or more based on need) to the parts to be manufactured.
The FormUp® 350 maximizes the portion of the 3D printing process where the lasers are firing and adding material to the parts making it more advantageous in a production setting. The entire process is designed to optimize downtime before the build commences, during the build, and in the post-production steps. The build setup is streamlined with automated build plate leveling and referencing. Inerting times are short as well. Oxygen levels reach 500 ppm in 15 minutes. During the build itself, the bidirectional powder spreading system is 40% faster than the conventional method. Each of the four lasers works in unison over the entire build area to melt material as efficiently as possible. When the build finishes, the active cooling system kicks in to bring the heated platform down to a suitable temperature. That cooling allows for an earlier start of powder vacuuming, which is performed in the inert chamber through a glovebox. An additional benefit is the ability to supply new powder to the system and powder sample acquisition can happen without interrupting production.
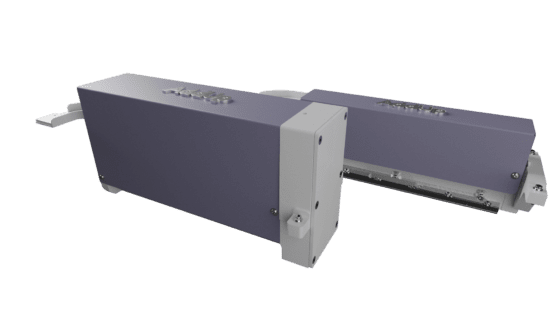
Quality criteria
The AddUp platform possesses several solutions to ensure high-quality production parts, with additional technologies in development. One of the production features currently available is active monitoring systems, and the recoating quality control system. These work together to analyze the surface condition of the powder bed in real time. Algorithms developed in-house assign a quality score to each new layer of powder. As soon as a defect is detected, for example, an unwanted deposit or a lack of powder, the system can restart a new powder spreading cycle immediately. This solution does not impact productivity, as the analysis is performed in a few tenths of a second. Most importantly, it prevents a whole batch of parts from being scrapped, which is the case when recoating defects are detected after printing. Every corrective action triggered by the machine is tracked and mentioned in the print report generated by the system after production.
Other active technologies include the fume collection system, which avoids possible drifts due to filter clogging thanks to an automatic filter cleaning system, and the Cross Jet device, which ensures the constant cleanliness of the laser windows during production.
AddUp also offers an in-situ solution to track the melting across the build. The system called “Melt Pool Monitoring” measures three essential parameters of the manufacturing process; the variation of the laser position, the variation of the power supplied by the laser, and the temperature of the melt pool. All this data is collected continuously during the printing process and is then mapped and overlaid on the CAD models of the parts. This allows not only to detect the presence of possible defects but also to locate them with great precision. The location of a pore or defect can be considered to downselect a region of interest for non-destructive evaluation. This tool will also detect defects on support structures, which are often acceptable. In this manner, Melt Pool Monitoring can reduce the cost and lead time of post-process inspection.
Recoating monitoring
Repeatability criteria
Medical manufacturers are faced with severe constraints for the certification of their applications. The processes for certification are difficult to obtain and require manufacturers to control all the manufacturing parameters: they must prove that the process can deliver compliant parts and that the quality will be maintained throughout current and future production.
Among the technologies embedded in the FormUp® 350 that contribute to repeatability are the 3-axis laser scanning systems. Unlike passive systems that distort the focal plane of the laser beam, 3-axis systems are capable of dynamically adjusting the focal length of the beam to guarantee a homogeneous focusing quality and beam shape at any point on the platform, and thus a uniform fusion quality regardless of the position of the part on the build plate.
Another repeatability concern is the powder itself. On AddUp’s platform, the powder management module ensures that the powder is systematically sieved and dried before being sent to the manufacturing chamber, thus avoiding the variations in powder properties that can occur when the powder is stored and transferred through different containers. The module always handles the powder in an inert environment, reducing oxygen pickup as well.
Finally, the roller recoater on the FormUp® 350 is a more robust spreading device than a traditional hard blade or scraper. This means flatter, more consistent powder bed shapes from one production run to another.
Traceability criteria
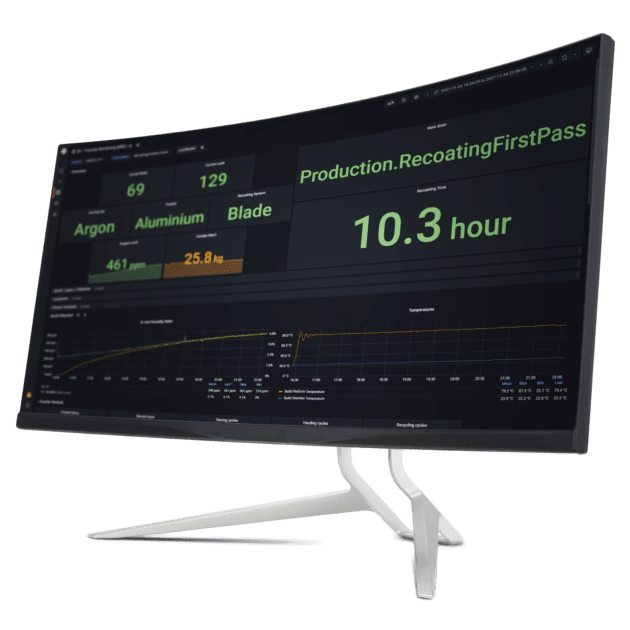
Once certification authorities have approved the qualification of an application, implant manufacturers must implement systems to ensure seamless traceability of all parts produced. The PBF process is complex, with many influencing variables that control part quality.
To help manufacturers monitor all the production parameters, AddUp Dashboards offers a real-time solution for all the data production and visualization. More than 80 parameters are tracked, time-stamped, and stored without a time limit in a database. Users can then create custom dashboards, either for machine monitoring, detection, maintenance issues, and analysis of production hazards. They can also compare different identical productions to detect differences between them.
Unlike other systems, AddUp Dashboards also offers access to the specific project file identifier called the GUID (for Globally Unique IDentifier). This 128-bit label, created for every build job, automatically changes upon project edits. It reduces if not eliminates any traceability concerns in the quality process.
These machines have been designed from the very beginning to achieve high levels of productivity and quality, but they have also been improved over the years. Each generation of machine and software addresses previous pain points at every step in the additive manufacturing process. Thanks to the experience acquired in their workshops, AddUp experts use their machines to offer part manufacturing services to their customers in addition to being machine supplier. Today, the FormUp® 350 is used by one of the world’s leading implant manufacturers, which has equipped itself with the FormUp® 350 in production facilities in both Europe and the United States and carries out qualified and large-scale manufacturing.
All in all, the FormUp® 350 platform has inherited the experience of the Michelin group. The machine has been tested in real-world manufacturing environments for many years. Mass production of tire mold parts with global efficiency expectations is a solid pedigree that is now being applied to the medical sector. The quality systems and production expectations for Michelin manufacturing and medical manufacturing are nearly identical. With a focus on quality, consistency, safety, productivity, and repeatability, this platform is easily convertible between industries
»Link to the Michelin Sipes case study