Für die medizinische Industrie, die chirurgische Implantate im 3D-Metalldruck herstellen möchte, gibt es viele Kriterien zu beachten: Qualität, Sicherheit, Produktivität und Rückverfolgbarkeit. Lesen Sie diesen Blog, um mehr über den Einsatz von AM in der Medizinbranche zu erfahren.
Qualität, Sicherheit, Produktivität, Rückverfolgbarkeit… Für die medizinische Industrie, die chirurgische Implantate mittels Metall-3D-Druck herstellen möchte, gibt es viele Kriterien zu berücksichtigen. In diesem Bereich hat die FormUp® 350 Maschine von AddUp viele Vorteile zu bieten.
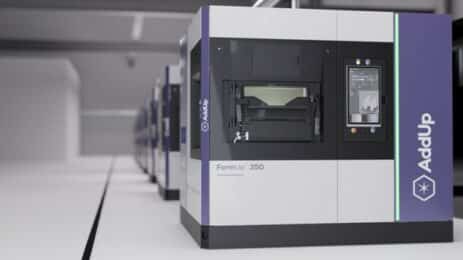
Der Markt für chirurgische Implantate und patientenspezifische Lösungen befindet sich in einem tiefgreifenden Wandel. Die Hersteller in diesem Sektor sind bestrebt, den Ärzten effizientere und individuellere Geräte zu für die Patienten akzeptablen Kosten zu liefern und gleichzeitig die besonders strengen Zertifizierungsanforderungen zu erfüllen. D i e neuen Generationen von 3D-Druckern erreichen ein hohes Produktivitäts- und Qualitätsniveau und können Teile aus biokompatiblen Materialien wie Titan herstellen. Die neuen und verbesserten Drucker ermöglichen es den Implantatherstellern, für viele Anwendungen die Umstellung auf die additive Fertigung von Metallen zu erwägen.
3D-gedruckte Implantate
Chirurgische Implantate sind Medizinprodukte, die sich speziell an den Knochen und das Gewebe anpassen
Morphologie des jeweiligen Patienten. Darüber hinaus müssen ihre Oberflächen so beschaffen sein, dass sie sich in die Knochenstruktur des Patienten integrieren; dies wird als Osseointegration bezeichnet und bezieht sich auf die Fähigkeit des Implantats, den festen und dauerhaften Wiederaufbau des Knochens zu fördern. Aus all diesen Gründen s i n d Implantate, die mit herkömmlichen Techniken wie der maschinellen Bearbeitung hergestellt werden, sehr teuer. Bei maßgeschneiderten Implantaten müssen die Hersteller nämlich zahlreiche Varianten jedes Modells mit den entsprechenden Werkzeugen für jede einzelne Geometrie bereitstellen. Darüber hinaus werden Oberflächen, die die Rekonstruktion von organischem Gewebe fördern, durch zusätzliche Oberflächenbehandlungen erzielt, die sowohl zeitaufwändig als auch schwierig zu realisieren sind.
Der 3D-Druck von Metall eignet sich hingegen besonders gut für die Herstellung komplexer und kundenspezifischer Teile. Aus diesem Grund sind die Hersteller von Medizinprodukten seit ihrem Erscheinen Anfang der 2000er Jahre an dieser Technologie interessiert. Die ersten Anwendungen kamen aus mehreren Gründen nur langsam in Gang. Erstens wurden von den medizinischen Zulassungsbehörden drastische Auflagen in Bezug auf Sicherheit und Qualität gemacht. Zweitens erlaubten die Produktivität und die Wiederholbarkeit der Maschinen den Herstellern nicht, ihre Investitionen rentabel zu machen. In den letzten Jahren haben sich jedoch dank der Fortschritte der Hersteller von 3D-Metalldruckmaschinen die Anwendungen vervielfacht, und die Technologie verbreitet sich rasch in der gesamten Branche.
Was ist eine Maschine für den medizinischen Bereich?
Die FormUp® 350 Maschine bietet zahlreiche Vorteile, um die Erwartungen der Hersteller chirurgischer Implantate zu erfüllen. Diese 3D-Maschine, die von AddUp, einem von den französischen Konzernen Michelin und Fives gegründeten Unternehmen, entwickelt und hergestellt wird, verwendet eine Technologie namens Laser Powder Bed Fusion (L-PBF). Dieses Verfahren eignet sich besonders gut für die Herstellung komplexer, maßgeschneiderter Metallteile mit hohen mechanischen Eigenschaften. Es ist auch eine der ausgereiftesten Technologien auf dem 3D-Druckmarkt für Metall. Mehrere Hersteller, darunter auch AddUp, bieten Rezepte für die Verwendung biokompatibler Materialien an. Im Bereich der medizinischen Implantate ist das gängigste dieser Materialien eine Titanlegierung namens Ti6Al-4V ELI, auch als Titan Grad 23 bezeichnet.
Die L-PBF-Maschine von AddUp, die FormUp® 350, unterscheidet sich in den folgenden Punkten wesentlich von den auf dem Markt befindlichen Maschinen:
Verwendung von mittlerem oder feinem Pulver. Die Flexibilität bei der Verwendung von Metallpulvern mit einer kleinen Partikelgröße (weniger als 25 Mikrometer) ermöglicht es der Maschine, Teile mit Oberflächen von geringer Rauheit, feinen Details und „gitterartigen“ Merkmalen herzustellen, die die Osseointegration fördern.
- Die Möglichkeit, eine Vielzahl von Pulverstreuvorrichtungen, einschließlich der Walzenvorrichtung, zu verwenden. Die Walzenvorrichtung erzeugt ein hochdichtes Pulverbett, das für die Herstellung von freitragenden Teilen geeignet ist, was die Kosten für d i e Nachbearbeitung erheblich reduziert. Der Walzenrückstreuer bietet diesen Vorteil sowohl bei feinen als auch bei mittleren Pulvergrößen.
- Sicherheit ist für AddUp von größter Bedeutung. Titanlegierungen in Pulverform stellen ein Risiko sowohl für die Anlagen als auch für die Bediener dar. Dieses Risiko wird durch den FormUp® 350 gemindert, da sich das Pulver immer in einer inerten Umgebung befindet. Der FormUp® 350 ist die einzige Maschine auf dem Markt, die die Zufuhr und das Recycling des Pulvers ohne Kontakt mit der Umgebungsluft ermöglicht. Dadurch wird das Risiko einer Exposition des Anwenders vermieden, während gleichzeitig und durchgängig Teile hergestellt werden, die die Industrienormen erfüllen oder übertreffen.
Über diese Eigenschaften hinaus übertrifft die LPBF-Maschine von AddUp die Anforderungen der Industrie und die Erwartungen der OEMs in Bezug auf Produktivität, Qualität, Wiederholbarkeit und Rückverfolgbarkeit.
Produktivitätskriterien
Die FormUp® 350 Maschine wurde auf der Grundlage des frühen Einsatzes der additiven Fertigung von Metall bei Michelin entwickelt. Die Herausforderung bestand nicht in der Technologie, sondern vielmehr in der Konsistenz und dem Durchsatz in einem anspruchsvollen Fertigungsumfeld. Die FormUp® 350 Maschine wurde von einem Hersteller für Hersteller entwickelt und auf eine hohe Produktivität abgestimmt. Ein Beispiel dafür ist die Verwendung von großen Bauplatten (350 x 350 mm) mit einem Schnelllade- und Nivelliersystem, das jeglichen Verlust an Nutzfläche vermeidet. Außerdem werden vier 500-Watt-Laser eingesetzt, von denen jeder die gesamte Fläche der Bauplatte abdecken kann. Der Vorteil für den Anwender ist eine große Flexibilität bei d e r Platzierung der Teile auf der Plattform und bei der Zuordnung der Laser (ein oder mehrere je nach Bedarf) zu den zu fertigenden Teilen.
Der FormUp® 350 maximiert den Teil des 3D-Druckprozesses, in dem die Laser brennen und Material zu den Teilen hinzufügen, was in einer Produktionsumgebung von Vorteil ist. Der gesamte Prozess ist so konzipiert, dass die Stillstandszeiten vor dem Bau, während des Baus und in den Nachbearbeitungsschritten optimiert werden. Die Einrichtung der Bauplatte wird durch die automatische Nivellierung und Referenzierung der Bauplatte rationalisiert. Auch die Inertisierungszeiten sind kurz. Der
Sauerstoffgehalt erreicht innerhalb von 15 Minuten 500 ppm. Während des Aufbaus selbst ist das bidirektionale Pulverauftragesystem 40 % schneller als die herkömmliche Methode. Jeder der vier Laser arbeitet im Einklang über den gesamten Baubereich, um das Material so effizient wie möglich zu schmelzen. Nach Abschluss des Bauprozesses setzt das aktive Kühlsystem ein, um die erhitzte Plattform auf eine angemessene Temperatur zu bringen. Diese Kühlung ermöglicht e i n e n früheren Beginn der Pulverabsaugung, die in der Inertkammer durch eine Glovebox erfolgt. Ein zusätzlicher Vorteil ist die Möglichkeit, dem System neues Pulver zuzuführen, und die Beschaffung von Pulverproben kann ohne Produktionsunterbrechung erfolgen.
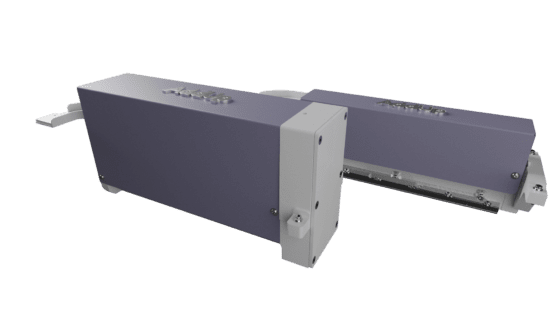
Qualitätskriterien
Die AddUp-Plattform verfügt über mehrere Lösungen zur Gewährleistung qualitativ hochwertiger Produktionsteile, wobei weitere Technologien in der Entwicklung sind. Zu den derzeit verfügbaren Produktionsfunktionen gehören aktive Überwachungssysteme und das Qualitätskontrollsystem für die Wiederbeschichtung. Diese arbeiten zusammen, um den Oberflächenzustand des Pulverbettes in Echtzeit zu analysieren. Eigenentwickelte Algorithmen vergeben für jede neue Pulverschicht eine Qualitätsnote. Sobald ein Fehler festgestellt wird, zum Beispiel eine unerwünschte Ablagerung oder ein Mangel an Pulver, kann das System sofort einen neuen Pulverauftragszyklus starten. Diese Lösung wirkt sich nicht auf die Produktivität aus, da die Analyse in wenigen Zehntelsekunden durchgeführt wird. Vor allem aber wird verhindert, dass eine ganze Charge von Teilen verschrottet wird, wie es der Fall ist, wenn nach dem Druck Fehler in der Wiederbeschichtung festgestellt werden. Jede von der Maschine ausgelöste Korrekturmaßnahme wird nachverfolgt und in dem vom System nach der Produktion erstellten Druckbericht erwähnt.
Weitere aktive Technologien sind das Rauchabzugssystem, das dank eines automatischen Filterreinigungssystems mögliche Abwanderungen aufgrund von Filterverstopfungen vermeidet, und die Cross-Jet-Vorrichtung, die die konstante Sauberkeit der Laserfenster während der Produktion gewährleistet.
AddUp bietet auch eine In-situ-Lösung zur Verfolgung des Schmelzvorgangs während des gesamten Fertigungsprozesses. Das „Melt Pool Monitoring“ genannte System misst drei wesentliche Parameter des Herstellungsprozesses: die Variation der Laserposition, die Variation der vom Laser gelieferten Leistung und die Temperatur des Schmelzbades. All diese Daten werden während des Druckvorgangs kontinuierlich erfasst und anschließend auf den CAD-Modellen der Teile abgebildet und überlagert. Auf diese Weise können mögliche Fehler nicht nur erkannt, sondern auch mit großer Präzision lokalisiert werden. Die Lage einer Pore oder eines Defekts kann berücksichtigt werden, um einen Bereich von Interesse für eine zerstörungsfreie Bewertung auszuwählen. Mit diesem Werkzeug können auch Defekte an Stützstrukturen erkannt werden, die oft akzeptabel sind. Auf diese Weise kann die Schmelzbadüberwachung die Kosten und die Vorlaufzeit für die Nachprüfung reduzieren.
Überwachung der Wiederbeschichtung
Kriterien für die Wiederholbarkeit
Die Hersteller von Medizinprodukten sind bei der Zertifizierung ihrer Anwendungen mit strengen Auflagen konfrontiert. Die Zertifizierungsverfahren sind schwierig zu erlangen und verlangen von den Herstellern die Kontrolle aller Herstellungsparameter: Sie müssen nachweisen, dass das Verfahren konforme Teile liefern kann und dass die Qualität während der gesamten laufenden und künftigen Produktion aufrechterhalten wird.
Zu den Technologien, die in das FormUp® 350 eingebettet sind und zur Wiederholbarkeit beitragen, gehören die 3-Achsen-Laserscansysteme. Im Gegensatz zu passiven Systemen, die das Die 3-Achsen-Systeme sind in der Lage, die Brennweite des Laserstrahls dynamisch anzupassen, um eine homogene Fokussierungsqualität und Strahlform an jedem Punkt der Plattform und damit eine einheitliche Fusionsqualität unabhängig von der Position des Teils auf der Bauplatte zu gewährleisten.
Ein weiteres Problem der Wiederholbarkeit ist das Pulver selbst. Auf der AddUp-Plattform sorgt das Pulvermanagementmodul dafür, dass das Pulver systematisch gesiebt und getrocknet wird, bevor es in die Herstellungskammer gelangt, und vermeidet so die Schwankungen der Pulvereigenschaften, die auftreten können, wenn das Pulver gelagert und durch verschiedene Behälter transportiert wird. Das Modul behandelt das Pulver immer in einer inerten Umgebung, wodurch auch die Sauerstoffaufnahme reduziert wird.
Schließlich ist der Walzenüberzieher des FormUp® 350 ein robusteres Streugerät als eine herkömmliche harte Klinge oder ein Abstreifer. Dies bedeutet flachere, gleichmäßigere Formen des Pulverbettes von einem Produktionslauf zum nächsten.
Rückverfolgbarkeitskriterien
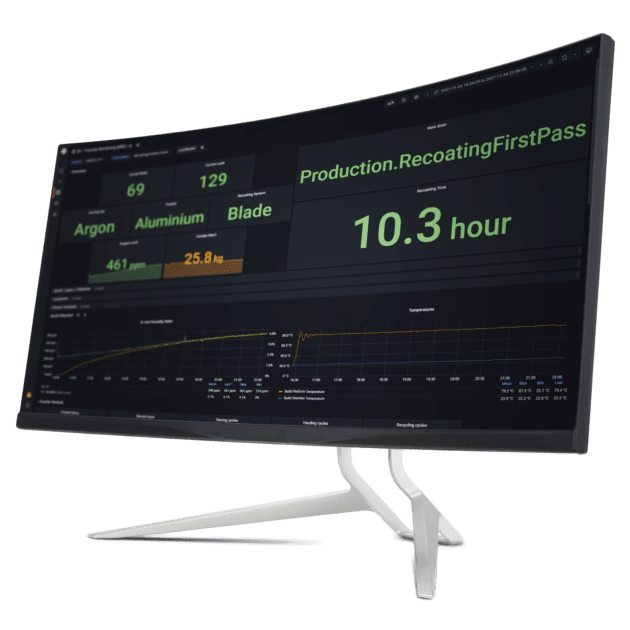
Sobald die Zertifizierungsbehörden die Qualifikation einer Anwendung genehmigt haben, müssen die Implantathersteller Systeme einführen, die eine lückenlose Rückverfolgbarkeit aller produzierten Teile gewährleisten. Der PBF-Prozess ist komplex, mit vielen Einflussgrößen, die die Qualität der Teile steuern.
Um den Herstellern zu helfen, alle Produktionsparameter zu überwachen, bietet AddUp Dashboards eine Echtzeitlösung für die gesamte Datenproduktion und -visualisierung. Mehr als 80 Parameter werden verfolgt, mit Zeitstempel versehen und ohne Zeitlimit in einer Datenbank gespeichert.
Die Benutzer können dann benutzerdefinierte Dashboards erstellen, entweder zur Maschinenüberwachung, zur Erkennung von Wartungsproblemen oder zur Analyse von Produktionsrisiken. Sie können auch verschiedene identische Produktionen vergleichen, um Unterschiede zwischen ihnen zu erkennen.
Im Gegensatz zu anderen Systemen bietet AddUp Dashboards auch Zugriff auf den spezifischen Bezeichner der Projektdatei, den GUID (für Globally Unique IDentifier). Dieses 128-Bit-Etikett, das für jeden Bauauftrag erstellt wird, ändert sich automatisch bei Projektbearbeitungen. Dadurch werden Bedenken hinsichtlich der Rückverfolgbarkeit im Qualitätsprozess reduziert, wenn nicht gar beseitigt. Diese Maschinen wurden von Anfang an für ein hohes Maß an Produktivität und Qualität konzipiert, aber sie wurden im Laufe der Jahre auch verbessert. Jede Maschinen- und Softwaregeneration behebt frühere Probleme bei jedem Schritt im additiven Fertigungsprozess. Dank der in ihren Werkstätten gesammelten Erfahrungen nutzen die AddUp-Experten ihre Maschinen, um ihren Kunden neben der Maschinenlieferung auch Dienstleistungen im Bereich der Teilefertigung anzubieten. Heute wird die FormUp® 350 von einem der weltweit führenden Implantathersteller eingesetzt, der sich mit der FormUp® 350 verfügt über Produktionsstätten in Europa und den Vereinigten Staaten und führt e i n e qualifizierte und großtechnische Produktion durch.
Alles in allem hat die FormUp® 350 Plattform die Erfahrung der Michelin Gruppe geerbt. Die Maschine wurde viele Jahre lang in realen Produktionsumgebungen getestet. Die Massenproduktion von Reifenformteilen mit globalen Effizienzanforderungen ist ein solider Stammbaum, der nun auf den medizinischen Sektor übertragen wird. Die Qualitätssysteme und Produktionserwartungen für die Michelin-Fertigung und die medizinische Fertigung sind nahezu identisch. Da der Schwerpunkt auf Qualität, Konsistenz, Sicherheit, Produktivität und Wiederholbarkeit liegt, lässt sich diese Plattform problemlos auf andere Branchen übertragen.