What Is Metal 3D Printing?
Metal 3D printing is a manufacturing method that employs high-performance metal alloys in a high-speed process that produces prototypes and end-use parts without molds or tooling.
The basic principle of metal 3D printing is additive manufacturing (AM), or the layering of materials to create three-dimensional objects. Unlike traditional, or subtractive manufacturing, it is a more agile process that enables the creation of complex metal parts faster and at a lower cost.
A brief history
The first patent for laser melting of metals was filed in 1995 in Germany, followed by slow growth of the technology at the beginning of the 21st century. In 2012, with the expiration of the original patents, investments by GE, HP, and others industry leaders spurred new growth and interest. Today, the global metal 3D printer market is taking off and is expected to grow at a significant rate through 2031.
Key types of metal 3D printing
Type of metal AM | How it works | Applications | AddUp Technology |
---|---|---|---|
Powder bed fusion (L-PBF) |
|
| FormUp 350 FormUp 350 Evolution |
Directed energy deposition (DED) |
|
| Modulo 400 Magic 800 |
Material Extrusion (Metal FDM): Ideal for prototyping and small batch production: Material Extrusion, also known as Metal FDM, utilizes a metal filament to create parts layer by layer. Here’s a closer look at the process:
- A metal filament is loaded into the printhead.
- The printhead heats the filament to its melting point.
- The molten metal is extruded through a nozzle in a controlled pattern, building the part layer by layer.
- After printing, the part undergoes a sintering process in a furnace to achieve its final density and strength.
Electron Beam Melting (EBM E-PBF): Produces parts with exceptional density for demanding applications: Electron Beam Melting (EBM) is a specialized PBF technology known for its high-quality outputs. Here’s a breakdown of the EBM process:
- A thin layer of metal powder is spread across the build platform.
- A high-powered electron beam is generated within a vacuum chamber.
- The electron beam selectively melts the metal powder according to the CAD design.
- The build platform lowers, and another layer of powder is spread. This process repeats until the part is complete.
Binder Jetting: Enables rapid production of complex geometries: Binder Jetting leverages a unique approach using a liquid binder to build parts layer by layer. Let’s explore the steps involved:
- A thin layer of metal powder is spread across the build platform.
- A print head selectively deposits a liquid binder onto the powder, adhering particles together according to the CAD design.
- The build platform lowers, and a new layer of powder is spread. This process repeats until the part is complete.
- The “green” part is removed from the powder bed and undergoes a sintering process to fuse the metal particles and achieve its final strength.
Cold Spray Technology: Extends the lifespan of parts through material deposition: Cold Spray Technology offers a unique method for repairing or adding material to existing parts. Here’s a look at how it works:
- Metal powder is accelerated to supersonic speeds using a high-pressure gas stream.
- The powder particles are directed through a nozzle towards the target surface (substrate or existing part).
- Upon impact, the particles deform and bond to the surface without fully melting, building up material layer by layer.
- This process can be used to create new parts or repair/coat existing components.
THE POWDER BED FUSION (PBF) PROCESS
PBF can be viewed as an ingeniously complex process:
- A thin layer of a high-strength alloy (metal powder) is spread across the build platform
- A high-powered laser scans the component and melts or fuses the powder in locations designated by the original CAD design
- A roller places another layer of metal powder across the component. (This step is repeated until the process is completed.)
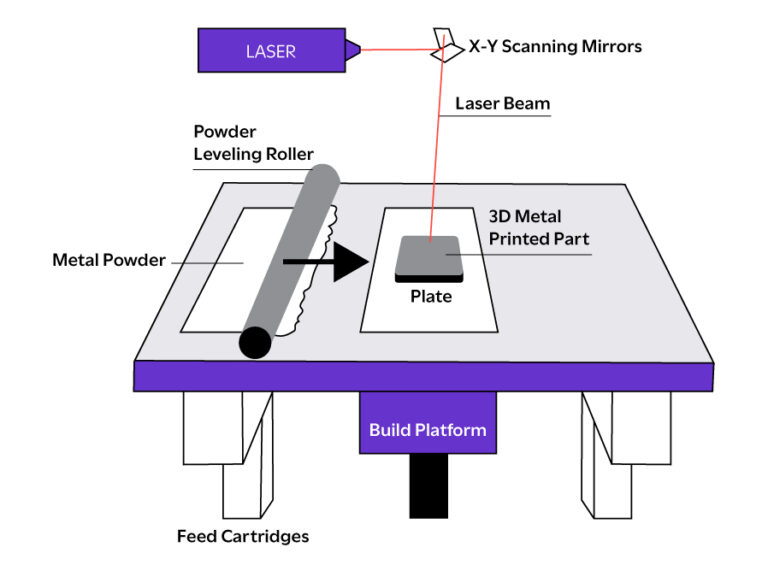
Feedstocks and Energy Sources
Metal 3D printing’s versatility is significantly enhanced by the variety of feedstocks (metal powder, wire) and energy sources (laser, electron beam, wire arc) it employs. This diversity not only broadens the spectrum of achievable part properties, including mechanical strength and corrosion resistance but also optimizes the manufacturing process to meet specific application requirements.
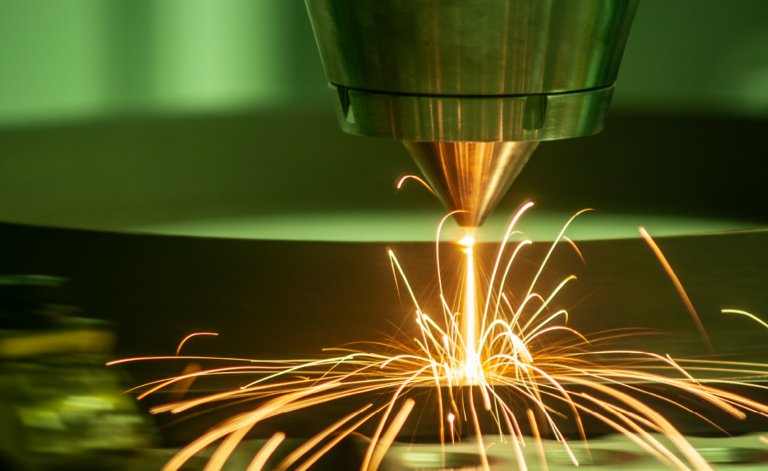
Metal 3D printing materials
The materials used in the metal 3D printing process directly impact the design possibilities. Each features unique properties—such as strength, flexibility, and heat resistance—to meet the specific requirements of the project.
The AddUp suite of materials, which have been validated on our PBF and DED, machines include:
Material | Description | Applications |
---|---|---|
Stainless steel 316L | Low-carbon stainless steel alloy that provides excellent mechanical and corrosion properties at room temperature, with a high creep strength at elevated temperatures | Medical Industry Nuclear |
Inconel 718/625 | High-strength and corrosive-resistant, precipitation-hardening allow | Aerospace Oil and gas Automotive Marine |
Tool steels—Maraging steel, H11, H13, 420 steel Printdur HCT | Combine high strength and excellent corrosion resistance | Tooling Aerospace Marine Nuclear Defense |
Aluminum AISi7Mg0.6 | Aluminum alloy that offers good mechanical properties, thermal conductivity, and corrosion resistance with high weldability | Aerospace |
Ti64 Titanium Ti64ELI | Strong, lightweight Strong, lightweight, and very biocompatible | Aerospace Medical |
Design considerations for Metal 3D printing
Even though it opens a world of possibilities for creating complex designs, there are some factors to keep in mind in designing for metal 3D printing. These include:
- Pinpoint the critical dimensions of the part and make sure they are flat or parallel to the print bed
- Maximize the contact that the part has with the bed
- Design for fewer supports
- Avoid overhanging structures.
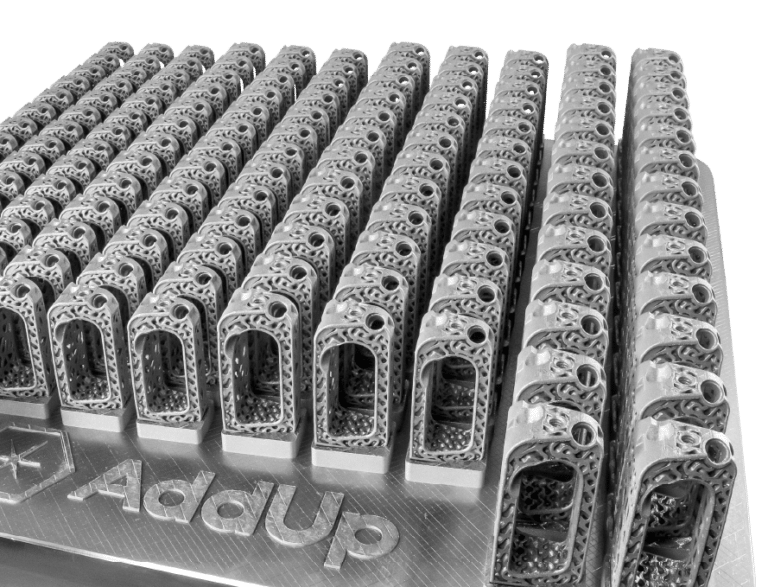
APPLICATIONS FOR METAL 3D PRINTING
Metal 3D printing is transforming the way a wide range of high-value industries fabricate with metal.
Learn MoreAerospace and aviation
Metal AM enables the creation of generative designs for complex components that are stronger and lighter and deliver enhanced performance.
Automotive
Metal 3D printing makes it possible for automotive manufacturers to develop tooling, molds, and dies for rapid prototyping and production of parts with complex geometries and intricate designs.
Medical and dental implants
Metal 3D printers enable the high levels of productivity and quality needed to provide parts in biocompatible materials like titanium for production of prosthetics and orthopedics, as well as crowns and bridges and orthodontic devices.
Jewelry and fashion
These industries are discovering the benefits of metal AM in creating custom designs and surface textures that enhance aesthetics and value.
Custom tools and components
Metal 3D printing can manufacture tooling at a fast pace with a lower cost per component.
Molds and inserts
Metal 3D printing reduces cycle time by reducing cooling time.
PROS AND CONS OF METAL 3D PRINTING
Metal 3D printing is faster at producing parts than traditional manufacturing methods. Here are some of its business and technical benefits, as well as some of its limitations.
Benefits of Metal AM
Metal 3D printing can be used to design and manufacture previously impossible designs. You can expect to:
- Produce lightweight parts that maintain significant strength
- Eliminate the need for molds and tools reduces lead times
- Reduce the cost of raw materials
- Achieve rapid prototyping
- Enjoy Increased service life
A Few Disadvantages
Adoption of metal 3D printing comes with a few tradeoffs that you should consider.
- A steep learning curve
- Need for precise process control limits build volumes
- Relatively high cost compared with traditional manufacturing
- High initial investment in infrastructure and post-processing equipment
THE FUTURE OF METAL AM
Metal 3D printing is quickly gaining traction as a method of speeding and streamlining the manufacture of final part production. The future of metal AM is bright.
New additive manufacturing technologies are being developed with the potential to enable higher speeds, lower costs, larger build volumes, and multi-material capabilities.
The integration of metal AM with technologies that include artificial intelligence (AI), robotics, and IoT will make it possible to automate, optimize, monitor, and verify the entire manufacturing process.
Researchers have been exploring the use of more exotic metals like Inconel, a superalloy that can withstand extreme heat and pressure—as well as precious metals for electronic and jewelry applications. Metal composite materials are also being developed for creating parts with greater strength or reduced weight.
The Jointless Hull machine, the world’s largest additive manufacturing and subtractive manufacturing apparatus was developed to provide the U.S. Army with large-scale printing in materials not previously printable at scale.
GETTING STARTED
Thinking about getting in the metal AM game? Consider this: There are more than 10 technology types and hundreds of printable metals that are available to manufacturers.
What to consider when choosing a metal 3D printer
When you’re ready to purchase a metal 3D printer, you should consider what you will be printing, how the printer will be used, your printing volume, the materials that you will use, and, of course, your budget.
Tips for Beginners
If you’re just getting started with metal 3D printing, you should learn as much as you can about the technology. Some manufacturers and service providers even offer test drives and sample metal 3D-printed components.
To develop your business case for entering the metal 3D printing arena, you need to understand and calculate all the costs involved—from the cost of the printer itself to the materials and post-processing—as well as the added value savings you will realize.
Resources for learning and exploration
The additive manufacturing industry is rife with educational opportunities, including online courses offered by leading universities.
Qualification and creation of operators are essential for the success and expansion of the metal 3D printing industry. To help meet the demand for more skilled 3D printing operators, ISO/ASTM International, have launched an Additive Manufacturing Quality Certification program for manufacturers using metal AM.
Now is the time to get on board
With its ability to produce complex metal prototypes and parts, metal 3D printing has tremendous potential for revolutionizing manufacturing as we know it.
Major auto manufacturers are ramping up the use of metal 3D printing to produce their most complex components. Aerospace and aviation companies are leveraging it to help them with light weighting parts. And the technology promises to expand its applications in healthcare. The technology is expected to become more accessible and cost-effective, as the variety of metals for use in producing high-strength parts expands.
Isn’t it time you explored the exciting new world of metal 3D printing?
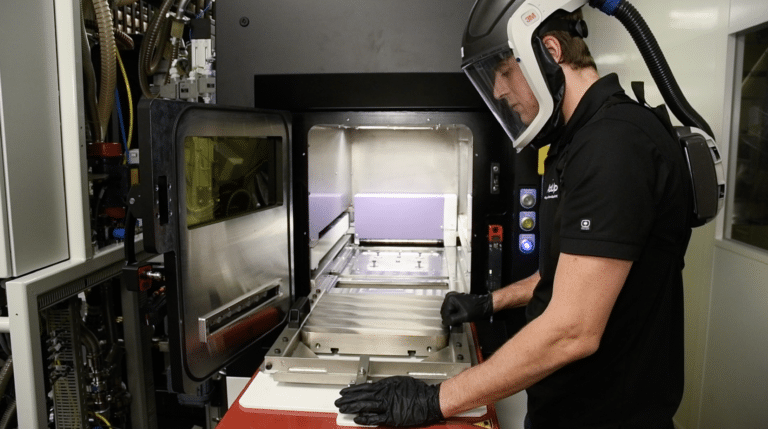
Step into The Future of Metal Manufacturing
Learn how AddUp Solutions can help you speed and streamline production of components and end-use parts.