A one-piece optimized coolant nozzle that delivers coolant flow into precise locations. The nozzle was officially installed grinding machine, optimizing its performance.
INDUSTRY
Tooling & Molding
CHALLENGE
Traditional manufacturing of this nozzle is difficult and requires impossible internal geometries.
KEY BENEFITS
- Optimal flow provided to cutting zone
- Time saved – Printed in days rather than weeks
- Monolithic for maximum strength
- Corrosion resistance in wet nozzle application
Custom Shape
Lead Time
Integrated Features
Performance
History
Fives is an international industrial engineering group with over 200+ years of experience and has grown through various industrial revolutions to offer innovative solutions and products, boosting the performance of major industry leaders worldwide.
Fives Landis Corp., known worldwide for their leading-edge precision grinding systems, and AddUp, a joint venture between Fives group and Michelin specializing in metal additive worked together to design and metal 3D printed custom coolant nozzle.
Challenges
Using traditional production processes, fabricating this complex part is difficult and requires multiple pieces, and ideal interior geometries are impossible to create. Metal additive manufacturing allows this type of nozzle component to be realized from the digital design to the final custom metal 3D printing part in only a few steps and a matter of days, not weeks.
The custom nozzle design allows the flow position and shape to precisely match the challenging wheel geometry with fewer components in the assembly while also providing optimum flow to the metal cutting zone in the grinding machine. This increases the performance of the machine and optimizes the grind cycle.
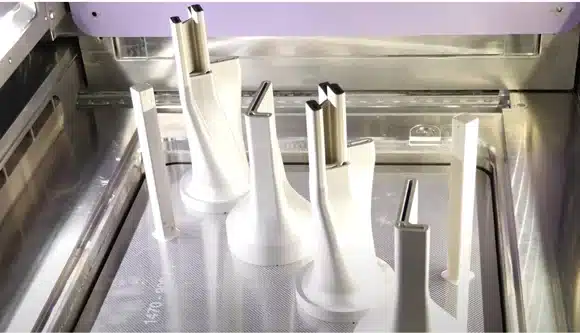
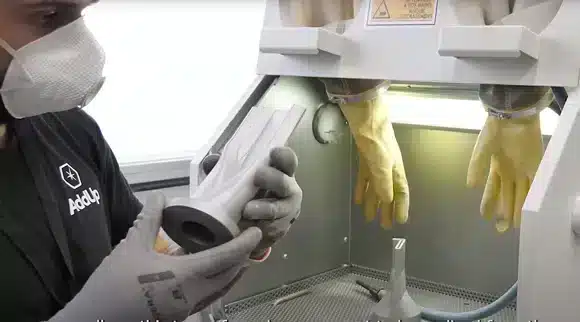
Solution
AddUp teams first started by laying out the part in the 3D build preparation software, AddUp Manager™, then developed the best manufacturing recipe for the print, including melt strategy and build orientation, before transferring the file to the AddUp FormUp® 350 Powder Bed Fusion machine.
The nozzle is printed in stainless steel using the AddUp FormUp® 350 Powder Bed Fusion machine in only a few hours. In this machine, parts are made in successive horizontal layers. For each layer, metal powder is spread across the build plate, and a laser melts the areas that need to be solidified.
Lastly, post-processing operations, including stress relief, wire EDM, and bead blasting, complete the part, making it ready for assembly on the grinding machine.
The FormUp® ensures accurate and repeatable part performance with:
- resolution down to 0.1mm features
- 99.99% material density
- shallow overhangs as low as 15 degrees
- surface finish as low as 4 Ra μm, as printed
Results
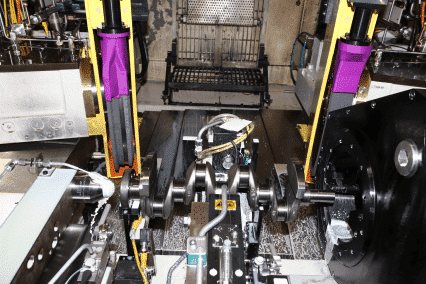
The final result was a one-piece optimized coolant nozzle that accurately delivers coolant flow into precise locations. The nozzle was officially installed on a rebuilt Landis LT2 grinding machine, optimizing the machine’s performance.
The nozzles could deliver coolant precisely to the grinding zone for applications with complex wheel shapes. They were proved to have the required strength and integrity to withstand operating in mass production for now over one year with no failure. Examination of nozzles shows no signs of fatigue or corrosion.