Read the case study to understand how to obtain a viable heat exchanger with good thermal and mechanical properties in a reduced time frame.
AddUp and PrintSky join forces to increase the Technology Readiness Level (TRL) of a new-generation heat exchanger. They produced a high-performance part with complex geometries in Aluminum using metal additive manufacturing. Read the case study to understand how to obtain a viable heat exchanger with good thermal and mechanical properties in a reduced time frame.
INDUSTRY
Aeronautics
CHALLENGE
To 3D print a heat exchanger with complex geometries and internal channels
KEY BENEFITS
- Good corrosion resistance.
- Mass reduction.
- Complex geometries
Mass Reduction
Creative Shape
Performance
History
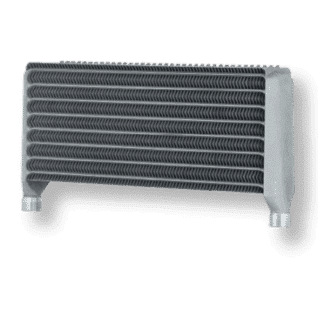
Heat exchangers are commonly used for cooling or heating purposes. A heat exchanger is a system used to transfer calories between two fluids (gas or liquid). Depending on the application, the fluids may be separated to prevent them from mixing or being in direct contact. In the aviation industry, heat exchangers can be used to cool down the engines or warm the fuel.
PrintSky is a joint venture between the AddUp group, which specializes in metal additive manufacturing, and Sogéclair, a leader in the integration of high-value-added solutions in aeronautics, space, civil and military transport. PrintSky has associated both expertise of AddUp and Sogéclair to increase the Technology Readiness Level (TRL) of a new generation heat exchanger. With its innovative design by PrintSky, this part allows the heat exchange between glycol water on one side and airflow on the other. The heat exchanger is designed to be installed in an air stream on a rack placed on a helicopter.
Challenges
The design of heat exchangers using traditional processes of stamping, brazing, machining, etc., strongly constrain the design possibilities. Also, expensive tools must be created to produce heat exchangers with those methods.
Not being dependent on these tools by using metal 3D printing reduces costs and time to market. Freeing ourselves from design constraints allows us to look for more efficient concepts better adapted to each case.
SOLUTIONS
The metal additive manufacturing technology allows to create compact and efficient exchangers. Improving the performance, reducing pressure loss during flow, and increasing the exchange surfaces while avoiding the creation of a thick boundary layer are necessary. Combining knowledge in additive manufacturing and thermo-fluidic laws allows the creation of innovative structures capable of reconciling all these constraints to achieve optimum performance.
Printing metal parts on an AddUp FormUp® 350 powder bed fusion (PBF) machine allows for the optimization of production times. For example, a design update to increase or decrease the heat exchange capacity does not require a tooling redesign and setting heavy industry into motion. A printout can follow a simple design update to obtain a viable heat exchanger in a reduced time frame.
The wide range of powders that can be used on the FormUp 350 machines makes it possible to adapt the material to the application. In this case, the temperature, mass, and corrosion constraints led us to use AlSi7Mg aluminum alloy powder. This alloy’s good mechanical and thermal properties and fine grain size allow for smooth surfaces and optimized thicknesses.
Results
The heat exchanger was produced with 0.5mm thin walls and 0.2mm external and 0.35mm internal fins. The FormUp 350’s roller coating system, coupled with the use of a fine-grain powder, allows the printing of parts with a very good surface finish.
There are several advantages to printing an exchanger with Powder Bed Fusion:
- Independence from suppliers
- Easier system development
- Less tooling
- A single design can cover a wide range of use cases
The challenge is met by producing a newly optimized metal part using the least amount of material possible. Moreover, metal additive manufacturing allows an industrialist to free himself from the constraints imposed by the foundry or forge and to produce high-performance parts with complex geometries.