Software for Additive Manufacturing
Manufacturing preparation, simulation, in-process control, traceability… AddUp offers a complete suite of software to reap the full potential of FormUp machines.
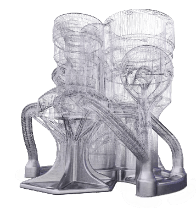
DESIGN
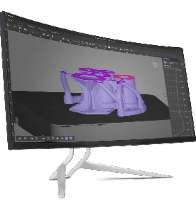
ADDUP MANAGER
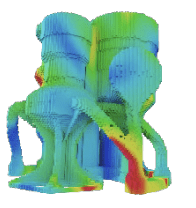
DISTORTION SIMULATION ADDON
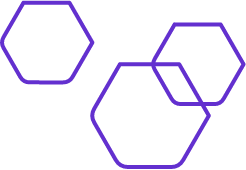
INTEROPERABILITY COMPONENT ADDUP NTWIN
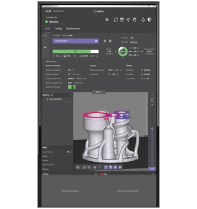
NCORE
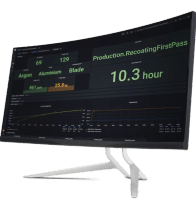
ADDUP MONITORING
- Addup Dashboards
- Recoating Monitoring
- Melting Monitoring
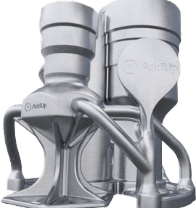
FINAL PART
ADDUP MANAGER: WHERE IT ALL STARTS
With AddUp Manager manufacturing preparation software, take control of all machine parameters. Whether you are looking for maximum productivity, metallurgical or geometric quality, or whether you want to develop a recipe for a new material, AddUp Manager gives you complete freedom in your machine adjustment choices.
- Ultra fast trajectory generation engine
- More than 250 variables and parameters that can be modified
- Creation of custom melting strategies
- Ergonomic and intuitive interface, visualization of laser trajectories
- Compatibility with most CAD files format: Catia, NX, Pro/E, Inventor, Solidworks, etc.
- Large CAD file management
- Creation of plans of experiments
- Automatic marking of parts and platforms
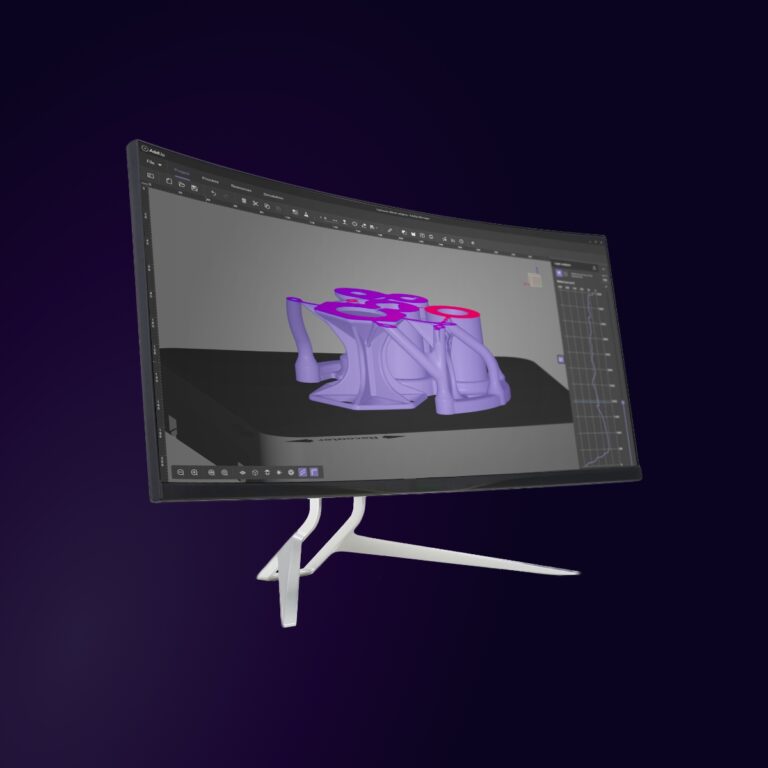
“AddUp has demonstrated a set of capabilities that enable us to address unique design and application challenges faced by our growing base of aerospace, space, and defense customers.”
Greg Morris
“AddUp group has enabled our complex designs to become a reality using metal Additive Manufacturing, a state-of-the-art process. This will change the way we create and customize a motorcycle. Our creativity is now limitless, which was impossible with traditional metal manufacturing processes.”
Simon Dabadie
“The AddUp team has proven to live within their proclaimed values… delivering a beneficial experience, being a trusted partner, and encouraging innovation. As I navigate through projects, I have been impressed with the level of attentiveness and service they exhibit. Each interaction is laced with education, professionalism, and care.”
Shannon VanDeren
“The FormUp350 is one of the only machines on the market that can run both the typical LPBF powder cut and a much finer cut of powder. This gives us flexibility to meet certain challenging applications we may come across in the future.”
Rachel Levine
“AM is in a state of exponential growth with the biggest challenges in adoption being qualification and certification. NSL is focused on partnering with companies who are passionate about driving innovation for metal 3D printing.
Over my past three years working with AddUp they have demonstrated a commitment to industrializing additive technology. The evolution of the FormUp 350 has made significant advancements in its full-field, 4-laser system and its monitoring suite which helps to accelerate the qualification process. Advancements like this prove AddUp to be a major player in the growing AM industry.”
Ed Herderick
NCORE: THE BRAIN BEHIND THE MACHINE
The integrity of production information and the control of all the machine components are guaranteed by the NCore embedded software. Separated by different user-roles, the NCore interface provides immediate access to key functions: preparation cycles, job selection, and real-time status monitoring.
- Start preparation cycles
- Production oriented workflow
- Check the geometrical and time progression of the build
- Follow the main parameters of the machine
- Visualize a chart of important parameters
- View the progression of the build on a 3D view
- View photos and videos of what is being built on the machine
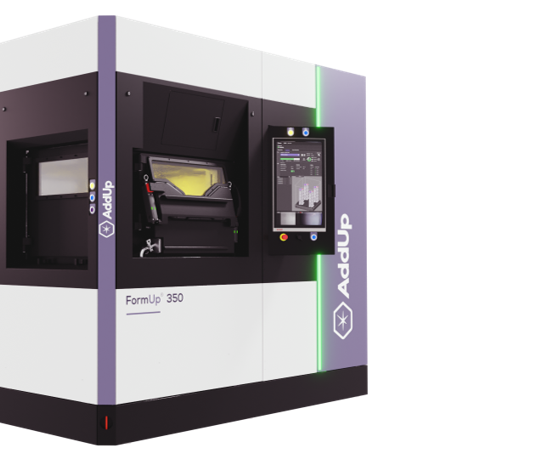
QUALITY ASSURANCE ORIENTED
AddUp offers a robust suite of monitoring solutions to ensure real-time validation and quality control of printed parts during production. These tools provide our customers increased confidence and can help to reduce the amount of post-production inspections.
GET A DEMOAddUp Dashboards
- Dashboards is the monitoring software that comes as an option with AddUp machines. It collects all production data in real time and presents it as dashboards tailored to the needs of different users.
- Based on Grafana, the most advanced data visualization solution, AddUp Dashboards is fully configurable, capable of emitting different alarms, and will help you improve the efficiency of your manufacturing, conduct analysis in case of defects on a part, and monitor a workshop composed of several machines.
- Real time data information (customizable refresh rate down to 5 seconds)
- Powerful Time Range feature: see the big picture for the last month or check what happened during last layering cycle
- Dozens of variables available, from “Oxygen Level” to “Remaining Build Time”
- Over 25 data visualization styles available (Graph, Heatmap, Traffic Light, Text, …)
- Fully customizable dashboard pages: move, resize, duplicate, edit your data panels easily
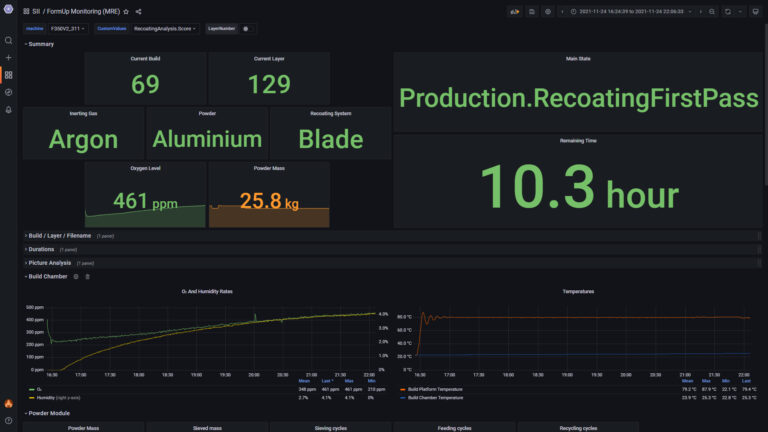
Recoating Monitoring
- The layering phase is a key step in the metal parts production based on L-PBF technology. Any defects can cause melting problems or lead to a production interruption.
- One of the key elements in the Monitoring AddUp offer is the analysis of the quality of the layering which can proactively corrects faults during production. Operating on a closed loop principle, this analysis during production checks the homogeneity of the powder bed, revealing the possible presence of deposits or lack of powder. The algorithms developed by AddUp allow users to assign a score and trigger a correction sequence when necessary.

Melting Monitoring
- FormUp 350’s monitoring capabilities are impressive! The most advanced solution in AddUp’s Monitoring Suite provides visibility of printing execution at the microscopic scale. Several parameters are measured at very high frequency, such as the position of the laser spot, the power actually delivered and the emissivity of the melt pool. This data is available in real time.
- This system makes it possible to characterize any defects without destroying the part, which is beneficial for unique one-off builds. And in the case of mass production, it can be used to create a footprint to serve as a point of comparison for all future production builds.
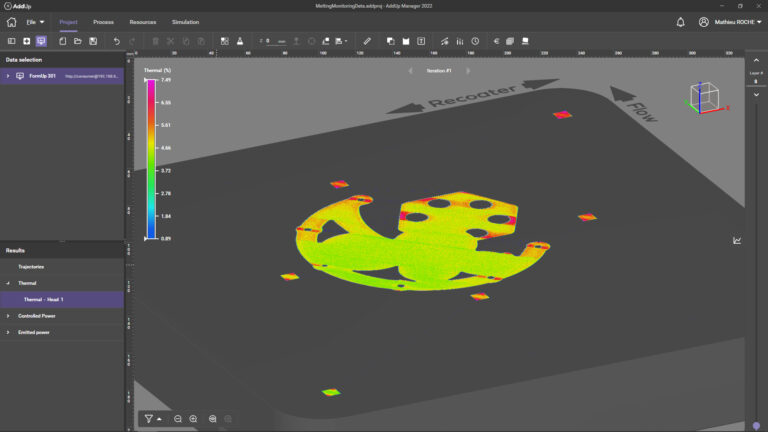
Request A Demo
Want to see the software in action? Request a personalized demo below.
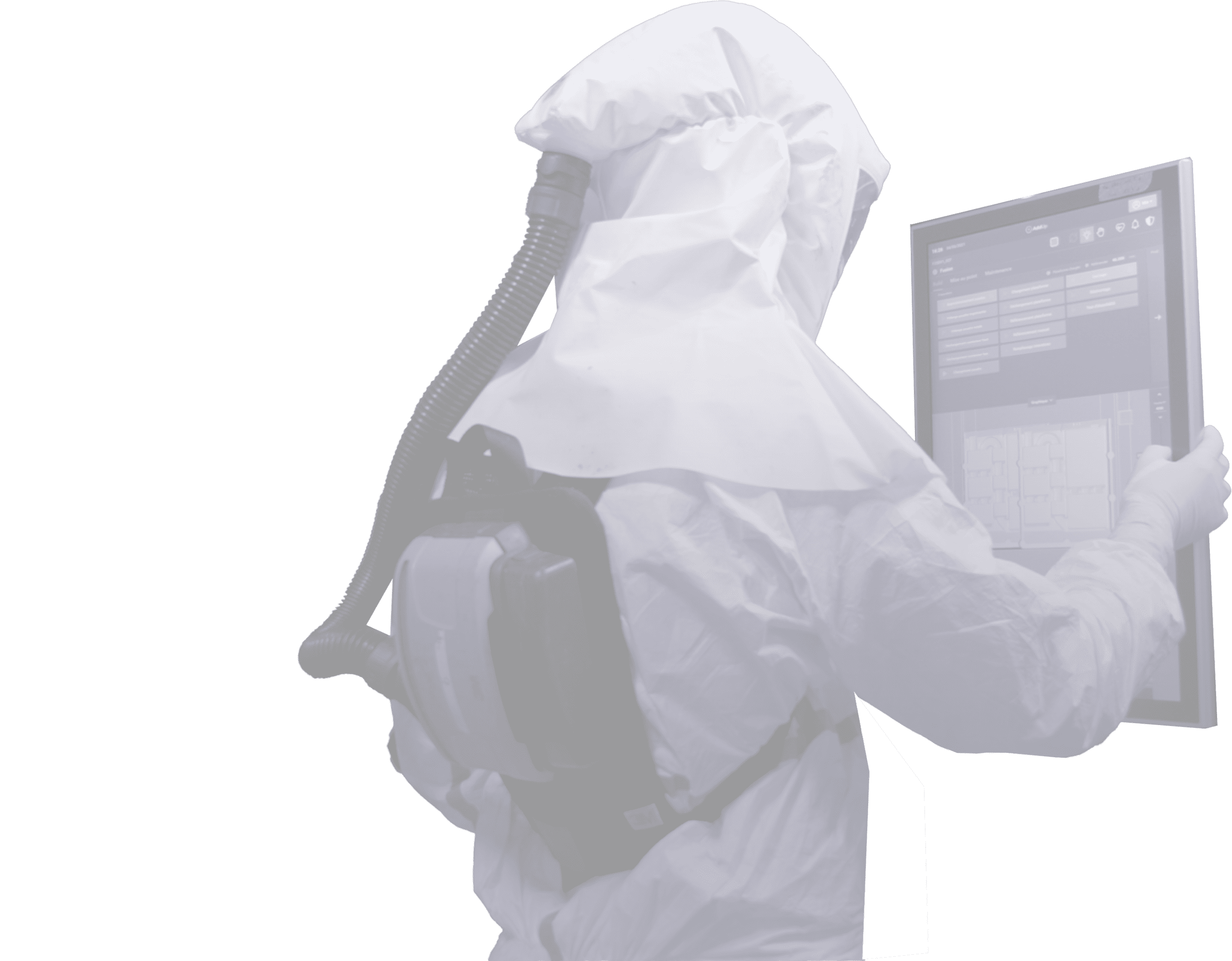