The interview with Zeda’s Director of Additive Technologies highlights how the flexibility of the FormUp 350 platform helps develop challenging applications and maximize productivity. The AddUp partnership is driven by a shared goal of large-scale part production and a commitment to open collaboration.
As the AddUp and Zeda partnership continues to grow, we get insight from Zeda’s Director of Additive Technologies, Rachel Levine, on how the flexibility of the FormUp 350 helps her develop challenging applications and maximize productivity.
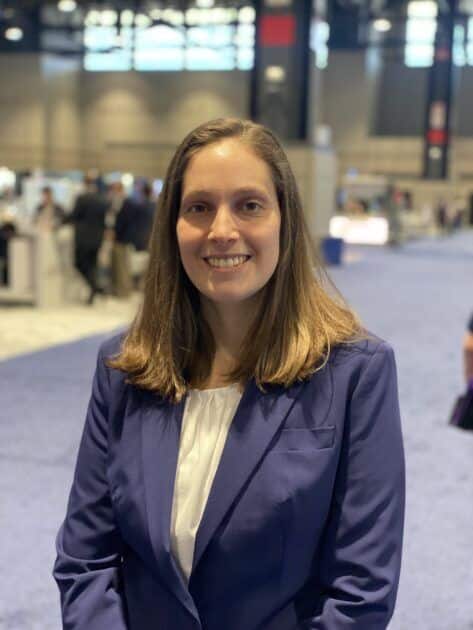
1. Why are you passionate about additive?
In my junior year of college I took a class called Rapid Prototyping. From that moment on, I was hooked. Up until that point, I thought I was going to join the toy industry after graduating, as I’d already begun pursuing that career with a co-op the semester before. Once I saw the potential that Additive held, I couldn’t go back to an industry that relied on older, established technologies. My favorite thing about Additive is that there are still so many unexplored applications… there are still new frontiers that only a handful of people in the world truly have the knowledge, resources, and skill to explore.
2. What excites you about the AddUp partnership and FormUp 350 platform?
This partnership feels novel in a lot of ways. Our teams have been working together now for almost a year, and rarely have I had the pleasure of working with another company that is truly willing to engage in a partnership that works towards a greater goal. Too often partnerships are constrained by mistrust and an unwillingness to share information, but the Addup team has really committed to the partnership with open minds and a shared goal to drive towards large scale part production. Not to mention the FormUp opens the door to productivity improvements with its quad laser setup, open parameters, and long life filter.
3. How does AddUp Manager’s open parameters help Zeda engineers achieve their goals?
The right parameters make all the difference when it comes to productivity, buildability, quality, and material properties. Zeda understands that high volume, fine-featured medical production may require different parameters than large space parts because they need to be optimized for different requirements. The ability to edit parameters for lattice or other specialized features is something we hope to leverage going forward. Of course, all parameters must be validated and qualified against the needs of the product; a process that we are well versed in.
4. How does the FormUp350 differ from other platforms on the market?
FormUp350 is one of the only machines on the market that can run both the typical LPBF powder cut and a much finer cut of powder. This gives us flexibility to meet certain challenging applications we may come across in the future. I’ve also recently been given a sneak peek of some future developments that make me even more excited about our partnership and the benefits we will be able to bring to our customers.
5. How does the FormUp’s 350×350 platform and 4-lasers unlock applications for Zeda customers?
As a contract manufacturer, we see a wide variety of parts. For small parts, AddUp’s full-field overlap quad laser system allows us to improve productivity. The size of the platform allows us to reach a wider range of larger parts.
6. How significant is powder management to the overall process?
Without powder reuse, Additive becomes cost prohibitive for almost all industries. With proper validation and quality monitoring, AddUp’s internal powder loop allows us to move towards infinite reuse. The validation of powder life within AddUp’s internal system is a key project Zeda will be engaging in with AddUp.
7. How does the FormUp’s Autonomous Powder Module change this for Zeda?
Powder reuse becomes somewhat of a nightmare to track once powder leaves a system where it can then be accidentally exposed to moisture or contaminated equipment. For alloys such as Titanium, the offline powder movement and sieving process can also be dangerous. FormUp’s internal, inert system removes the common contamination risks as well as the exposure and explosion risk to the operator.