Das Interview mit dem Director of Additive Technologies von Zeda zeigt, wie die Flexibilität der FormUp 350 Plattform die Entwicklung anspruchsvoller Anwendungen und die Maximierung der Produktivität unterstützt. Die AddUp-Partnerschaft wird durch das gemeinsame Ziel der Großserienproduktion von Teilen und das Engagement für eine offene Zusammenarbeit angetrieben.
Während die Partnerschaft zwischen AddUp und Zeda weiter wächst, erfahren wir von Rachel Levine, Director of Additive Technologies bei Zeda, wie die Flexibilität des FormUp 350 ihr hilft, anspruchsvolle Anwendungen zu entwickeln und die Produktivität zu maximieren.
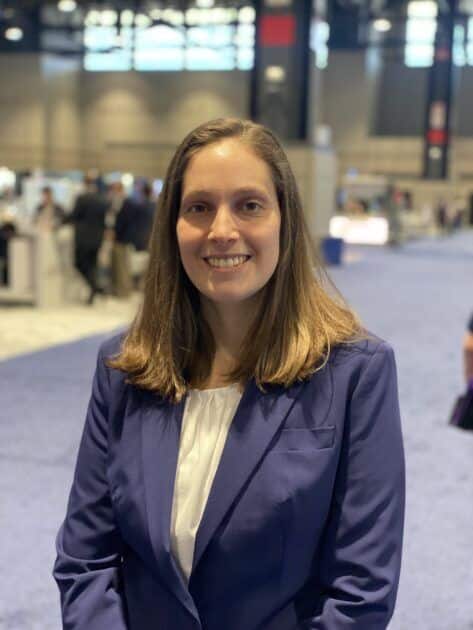
1. Warum begeistern Sie sich für Additive?
In meinem ersten Jahr am College belegte ich einen Kurs namens Rapid Prototyping. Von diesem Moment an war ich süchtig. Bis zu diesem Zeitpunkt dachte ich, dass ich nach meinem Abschluss in die Spielzeugindustrie gehen würde, da ich diese Karriere bereits im Semester zuvor mit einem Co-op begonnen hatte. Als ich das Potenzial von Additive sah, konnte ich nicht mehr in eine Branche zurückkehren, die sich auf ältere, etablierte Technologien stützt. Was mir an Additive am besten gefällt, ist, dass es noch so viele unerforschte Anwendungen gibt… es gibt immer noch neue Grenzen, zu deren Erforschung nur eine Handvoll Menschen auf der Welt wirklich das Wissen, die Ressourcen und die Fähigkeiten haben.
2. Was reizt Sie an der AddUp Partnerschaft und der FormUp 350 Plattform?
Diese Partnerschaft fühlt sich in vielerlei Hinsicht neu an. Unsere Teams arbeiten jetzt seit fast einem Jahr zusammen, und selten hatte ich das Vergnügen, mit einem anderen Unternehmen zu arbeiten, das wirklich bereit ist, sich auf eine Partnerschaft einzulassen, die auf ein größeres Ziel hinarbeitet. Allzu oft werden Partnerschaften durch Misstrauen und die mangelnde Bereitschaft, Informationen auszutauschen, eingeschränkt, aber das Addup-Team hat sich der Partnerschaft wirklich mit offenem Geist und dem gemeinsamen Ziel verschrieben, die Produktion von Teilen in großem Maßstab voranzutreiben. Ganz zu schweigen davon, dass der FormUp mit seinem Vierfach-Laser-Setup, den offenen Parametern und dem langlebigen Filter die Tür zu Produktivitätssteigerungen öffnet.
3. Wie helfen die offenen Parameter des AddUp Managers den Zeda-Ingenieuren, ihre Ziele zu erreichen?
Die richtigen Parameter machen den Unterschied aus, wenn es um Produktivität, Baubarkeit, Qualität und Materialeigenschaften geht. Zeda ist sich bewusst, dass die Produktion von medizinischen Teilen in hohen Stückzahlen und mit feinen Merkmalen andere Parameter erfordert als die Produktion von großflächigen Teilen, da diese für unterschiedliche Anforderungen optimiert werden müssen. Die Möglichkeit, Parameter für Gitter- oder andere spezielle Merkmale zu bearbeiten, ist etwas, das wir in Zukunft nutzen möchten. Natürlich müssen alle Parameter im Hinblick auf die Anforderungen des Produkts validiert und qualifiziert werden – ein Prozess, mit dem wir uns bestens auskennen.
4. Wie unterscheidet sich die FormUp350 von anderen Plattformen auf dem Markt?
Die FormUp350 ist eine der wenigen Maschinen auf dem Markt, die sowohl den typischen LPBF-Pulverschnitt als auch einen viel feineren Pulverschnitt ausführen kann. Das gibt uns die Flexibilität, bestimmte anspruchsvolle Anwendungen zu erfüllen, auf die wir in Zukunft stoßen könnten. Außerdem habe ich kürzlich einen kleinen Einblick in einige zukünftige Entwicklungen erhalten, die mich noch mehr von unserer Partnerschaft und den Vorteilen, die wir unseren Kunden bieten können, begeistern.
5. Wie erschließt die 350×350-Plattform von FormUp und die 4-Laser Anwendungen für Zeda-Kunden?
Als Auftragsfertiger haben wir es mit einer großen Vielfalt von Teilen zu tun. Bei kleinen Teilen ermöglicht uns das AddUp-Vierfach-Lasersystem mit Vollfeldüberlappung eine höhere Produktivität. Die Größe der Plattform ermöglicht es uns, ein breiteres Spektrum an größeren Teilen zu erreichen.
6. Welche Bedeutung hat das Pulvermanagement für den Gesamtprozess?
Ohne die Wiederverwendung von Pulver wird Additive für fast alle Branchen unerschwinglich. Mit einer angemessenen Validierung und Qualitätsüberwachung ermöglicht uns der interne Pulverkreislauf von AddUp eine unendliche Wiederverwendung. Die Validierung der Lebensdauer des Pulvers im internen System von AddUp ist ein Schlüsselprojekt, an dem Zeda zusammen mit AddUp arbeiten wird.
7. Wie verändert das autonome Pulvermodul von FormUp diese Situation für Zeda?
Die Wiederverwendung von Pulver wird zu einem Alptraum, sobald das Pulver ein System verlässt, in dem es versehentlich mit Feuchtigkeit oder kontaminierten Geräten in Berührung kommen kann. Bei Legierungen wie Titan kann die Offline-Bewegung des Pulvers und der Siebvorgang ebenfalls gefährlich sein. Das interne, inerte System von FormUp beseitigt die üblichen Kontaminationsrisiken sowie das Expositions- und Explosionsrisiko für den Bediener.