As the demand for patient-specific implants continues to grow beyond the ability of manufacturers to keep up, healthcare leaders like Mayo Clinic and the U.S. Veterans Administration are busy making plans to establish their own facilities and start 3D printing metal implants on-site.
Currently, the most common healthcare use cases for additive manufacturing are developing anatomical models to help patients understand their upcoming procedures and customizing surgical instrumentation.
All signs point to a future in which healthcare organizations will be manufacturing devices at the point of care (POC). That means that hospitals will soon be the newest members of the medical device manufacturing (MDM) industry, a proposition with real institutional and infrastructure challenges. “After all, this is not what healthcare facilities are really set up for,” says Severine Valdant, chief commercial officer for QuesTek Innovations, a leading materials engineering firm, and a founding member of the AddUp medical advisory board. “It takes a different way of thinking for a hospital.”
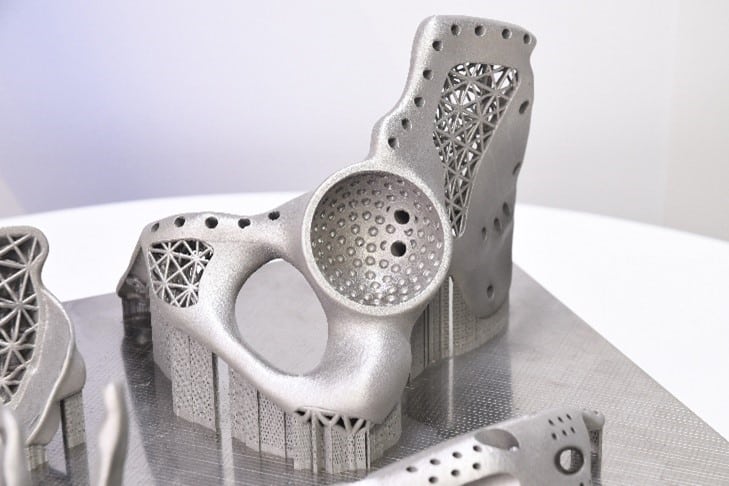
The AddUp Medical Advisory Board was established in 2023 in order to provide the company with nonbiased, holistic perspectives on the application of metal 3D printing technologies for healthcare. Severine Valdant provides her unique perspective as a leader in the development of medical devices and 3D printing. Before joining QuesTek, she led the transformation of Oxford Performance Materials into an additive manufacturing leader, helping it become the first company to receive FDA approvals for 3D printed polymeric implants.
Key stakeholders recognize value of 3D printing
Even with the challenges that additive manufacturing brings for healthcare organizations hoping to leverage 3D printing at the point of care, the concept is gaining widespread acceptance among healthcare executives and other key stakeholders.
- OEMs are making big advances. “If printer manufacturers can deliver an all-in-one solution, it makes it much less difficult to implement AM at the point of care and we’re not that far away,” says Valdant. The good news is that companies like AddUp are bringing new printers to the marketplace that can be easily integrated with other established systems and processes.
- The FDA is on board. “In fact, they see a lot of value in POC manufacturing and they’re working with players on the healthcare and OEM side to figure out what regulations or guidelines are needed to make it happen.”
- Surgeons are enthusiastic about the possibilities. “I’ve talked to a lot of them and they’re pretty excited about the etools, but we need to be careful that they don’t stop being doctors and become engineers,” Valdant continues.
- Administrators play a key role. “They’re the big decision makers. If we bring AM to the point of care, they need to see a good ROI.”
Future Applications
The future of healthcare is personalized medicine and POC manufacturing will play an important role. We expect that there are many new uses cases on the horizon that will push the boundaries of the technology and broaden its possibilities. These include advances in the just-in-time manufacture of single-use, procedure- and patient-specific instrumentation to replace traditional systems at affordable costs.
The sweet spot for future applications of POC AM will be procedures for which there is not a convenient or effective off-the-shelf implant option—including complex surgeries for knee, hip, and pelvis reconstructions; spine surgeries; and tumor modeling for cancer patients.
In addition, AI and machine learning will soon enable the automation of workflows and speed production of patient-specific implants, improving development times from as long as 18 months to a matter of days. This is expected to improve patient outcomes exponentially, while also reducing operative times and the need for additional corrective surgeries.
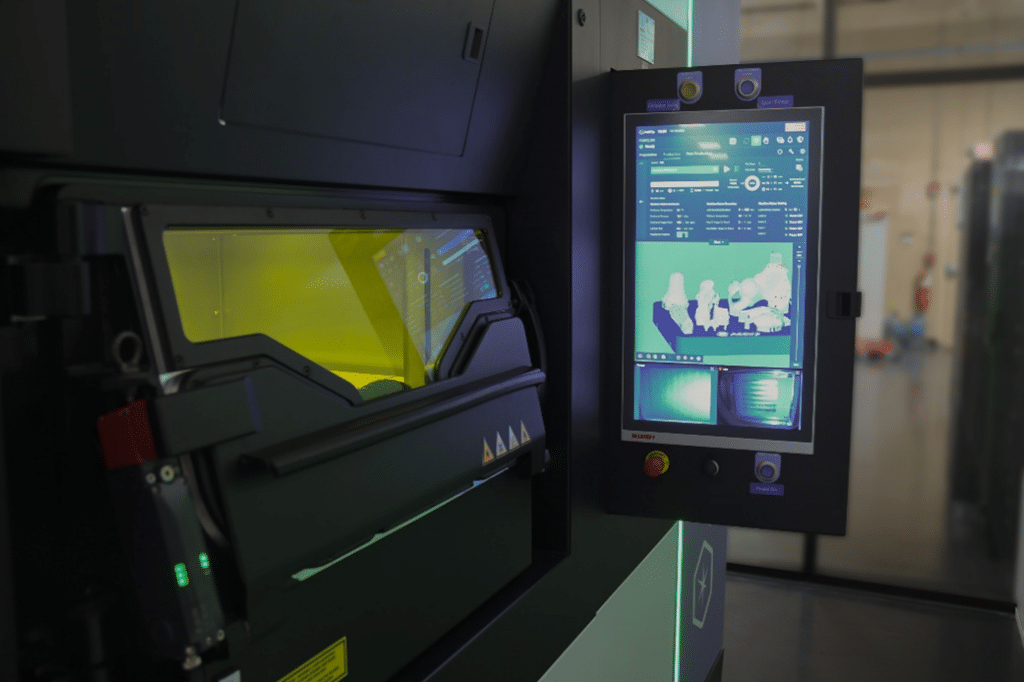
The Right OEM
POC manufacturing will need to be an effective partnership between healthcare facility and OEM. “I think we’re a lot further ahead than we were 10 years ago, because collaboration between the two is happening,” Valdant continues. “With our deep knowledge of the medical market and a solution that is very efficient and integrated, AddUp will be a great partner on the OEM side.”