See how AddUp and PrintSky develop a good rigidity/mass balance with a high technical and economic value for an aeronautical part.
The CEA (French Alternative Energies and Atomic Energy Commission) has joined forces with AddUp to create the Famergie platform to help energy sector manufacturers develop projects for the production of parts using metal additive manufacturing. The first project resulting from this partnership is a demonstrator of a methanation exchanger-reactor. This device converts CO2 into methane, which can be used as synthetic fuel. As the methanation reaction occurs at high temperatures and pressure, the design of the exchanger is crucial for the efficiency and control of the entire methane production. Read the case study about additive 3D printing of the aerospace support part using the FromUp 350® machine.
OBJECTIVE
Print a lightweight metal 3D support part
RESULTS
- 40% mass savings compared to the maximum target of 600 g given
- Compliance with the dimensions of the original part, for fastening and assembly.
Context
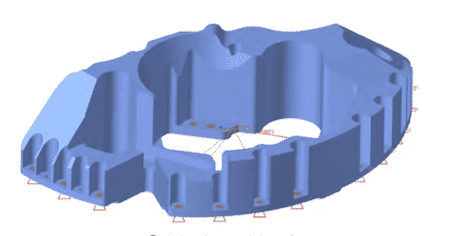
PrintSky is a joint venture between the AddUp group, an expert in metal additive manufacturing, and SOGECLAIR specialized in the integration of high-value-added solutions in the fields of aeronautics, space, civilian and military transport. The CEA (French Alternative Energies and Atomic Energy Commission) commissioned Printsky to redesign a typically machined support part using the possibilities offered by additive manufacturing to reduce its mass. This support must also precisely ensure its functionalities to hold the equipment it has to support and resist the stresses it is subjected to.
Implemented Means
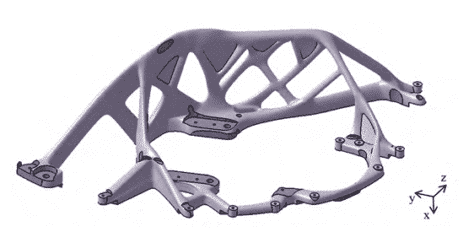
PrintSky was in charge of the design part of the project, developing its own experience and methodology to implement the characteristics of the metal part, in terms of mechanics and manufacturability. The production was then entrusted to AddUp experts who 3D printed the aerospace part using their FormUp350® machine.
Advantages of 3D Metal Printing
After topological optimization, additive manufacturing makes it possible to develop complex shapes, improve performance and reduce the volume of a metal part. It also allows the manufacture of very robust parts. Indeed, the material is added only where necessary, either to support forces or to ensure functionality such as fastening, support surface, or other. A good rigidity/mass balance with a high technical and economical value for an aeronautical part.
Results
The optimized support fulfills the same functions as the original support, but with a significant mass reduction, impossible to achieve with conventional technologies.
The use of fine powder allowed to obtain a good surface finish and finally the part was manufactured without support, which allows a significant time-saving in post-processing.
The AddUp Advantage
The mastering by AddUp of the material characteristics obtained on FormUp350® and of the additive manufacturing simulation tools has allowed us to anticipate the thermo-mechanical distortions and to obtain compliant parts after only one iteration.