INDUSTRY
Medical
CHALLENGE
Significantly reduce production costs when additively manufacturing large spinal implants using a multi laser system and a larger build plate
KEY BENEFITS
- Cut production costs by up to 30%
- Increase the output by 2.61 parts per hour
- Fine feature resolution and optimal osseointegration
- Reduced post-processing
- Lower total part cost
Integrated Features
Reduced Lead Time
Performance
History
Large spinal fusion devices are typically produced on small-format machines using Powder Bed Fusion (PBF) or machined from polyetheretherketone (PEEK) bar stock.
When manufactured additively, these larger spine implants are usually printed on small-format machines with limited build plates and only one or two lasers. The standard approach is to orient the implants with their anterior face upwards in Z, and to rely on multi-step processes that often create worst-case production scenarios.
Production costs are driven largely by the process itself, not just by materials. While additive manufacturing (AM) can increase cost, the value for large spinal implants is found in the lattice design and improved surface roughness, which support better osseointegration and ultimately better patient outcomes.
Another reason AM is preferred for spinal fusion devices is material performance. AM enables the use of titanium, which offers greater fracture toughness and higher tensile strength than PEEK. In contrast, PEEK implants lack ideal osseointegrative features and the material itself poses stability and supply chain challenges. For this reason, producing these implants additively is increasingly the preferred route, despite the lingering inefficiencies in legacy production approaches.
Challenges
Although AM enables greater osseointegration, higher-strength materials, and improved patient outcomes, manufacturing LLIF devices on small platforms with only 1–2 lasers drives up finished part costs. These implants are often built in the Z orientation which increases build times; an issue compounded by limited laser counts.
When using scraper or brush recoating systems, the underside of the anterior face usually requires breakaway supports, and removal often involves electrical discharge machining (EDM), adding another step and another charge to the process. These inefficiencies are baked into small build platforms and slow recoating cycles, making traditional AM systems a costly solution for large spinal fusion implants.
Strategy
The FormUp 350 challenges the industry’s reliance on small-format platforms by increasing both the build area and laser count, enabling up to 152 large spinal implants in a single build, about 1.5x more than typical systems.
The four-laser architecture drives higher throughput, cutting print times and lowering cost per part. More importantly, the machine’s powder roller recoating system minimizes the need for dense supports and improves surface uniformity, which directly translates to less post-processing and more predictable part quality.
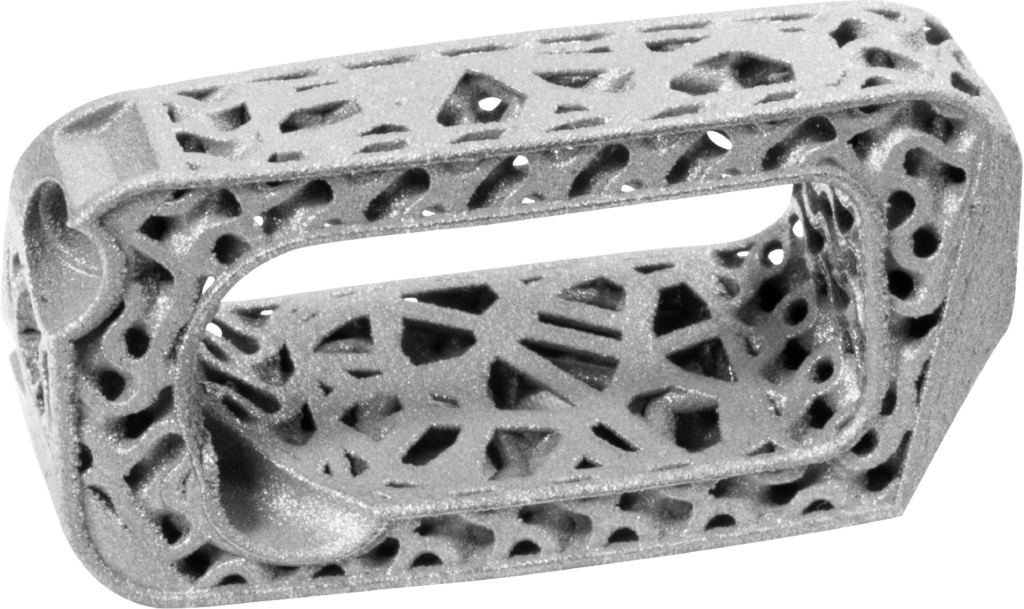
By tackling the constraints that slow down legacy systems like limited build space, slow recoating, and excessive supports, the FormUp 350 shifts the economics for manufacturers. The result: the ability to produce large, complex spinal implants at scale, without the historical trade-offs in cost, speed, or finishing.
Results
When benchmarked against typical small-platform solutions, the FormUp 350 consistently delivers lower cost per part and nearly doubles annual throughput (29,079 parts/year vs. 13,710). This isn’t just incremental improvement, it’s a fundamental shift in production economics.
For manufacturers of large spinal implants, this means the ability to scale production without being bottlenecked by build size or laser limitations. The process becomes more reliable, predictable, and ultimately more commercially viable for devices that have historically been costly to manufacture additively.
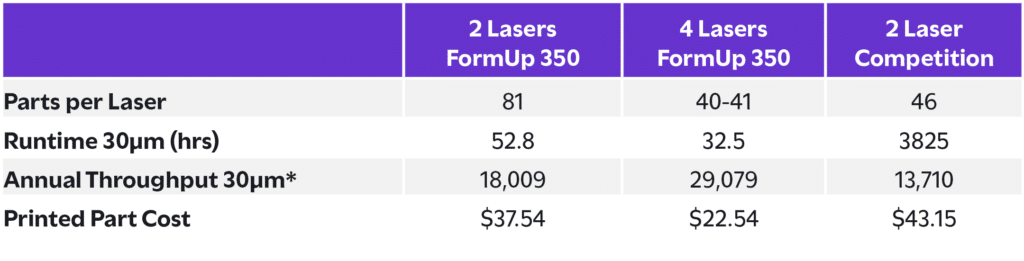
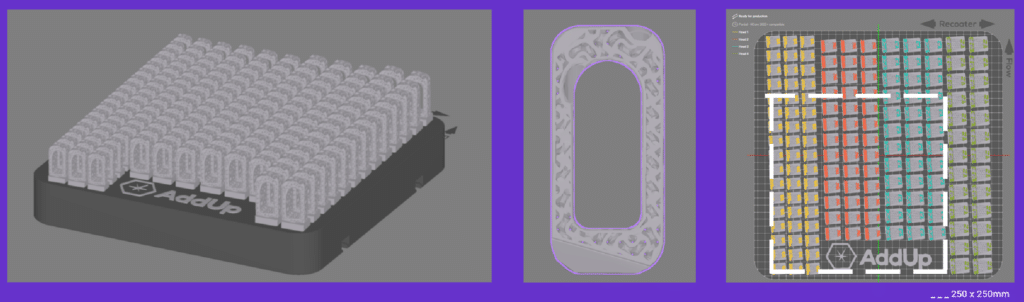