AddUp optimized the design of a rocket nozzle to improve the performance of a micro-launch vehicle.
Metal additive manufacturing can lead to fuel and production savings in aerospace. In this case study, you will see how AddUp optimized the design of a rocket nozzle to improve the performance of a micro-launch vehicle. 3D printing is already the future of the aerospace industry. Read the case study about an optimized design of a 3D printed rocket nozzle.
INDUSTRY
Aerospace
CHALLENGE
To print an innovative rocket nozzle to optimize engine performance in space
KEY BENEFITS
- Mass reduction
- Printed parts with complex geometries
- Resistance to high temperatures
Mass Reduction
Creative Shape
Function Integration
Performance
History: AddUp & Aerospace
In the aerospace industry, new design freedom that comes with additive manufacturing allows for lighter parts, leading to fuel savings. Customization opportunities and absence of tooling are also seen as an advantage in this industry, where production volumes are quite low. Aerospace experts believe that the performance gains and reduced production costs will lead to 3D printing taking over as the manufacturing method of choice in the industry.
One of the leading trends in the field of space transportation is the rise of smaller launchers, able to send payloads of less than 500 kg into orbit. It is one of the most promising aspects of the New Space: micro and mini launchers provide flexibility and responsiveness that make them a complementary solution to conventional launchers.
Challenges of printing innovative rocket nozzles
A nozzle is a component of a rocket responsible for producing thrust. Hot exhaust gases are accelerated from the combustion chamber through a tighter throat, then expanded out the exit. This process converts the energy in the combustion gases into kinetic energy.
The complete development of an orbital launcher engine is a long and complex process requiring several iterations of design, manufacturing, and static firing tests. This presents a demanding task from the project management side.
With the field of micro and mini launchers becoming such a competitive environment, rapid iteration is both a technological and commercial necessity.
Considering technical challenges: the high temperature inside a nozzle requires cooling the walls as close as possible to the heat source, to avoid any components melting. This cooling is usually done via tubes attached to the nozzle and becomes more complex when the nozzle is more compact to meet the propulsion needs of smaller launchers.
Solution for a 3D printed rocket nozzle
In rocket engine nozzles, the exhaust gases heat up to approximately 3000°C. During the design of the nozzle, it was important to keep in mind that any available alloys wouldn’t hold up when exposed to such high temperatures.
All the cooling functions where integrated into the nozzle, allowing it to conduct the hot gases while maintaining its shape and performance. Prior to combustion, the fuel acts as a coolant. The propellants are stored at low temperature and run through the internal channels of the nozzle before being captured and injected into the combustion chamber to be burned.
Results and benefits of additive manufacturing
The part was printed on a PBF (laser – powder bed fusion) machine, AddUp’s FormUp® 350. This system, with open parameters and an integrated powder recycling module promotes rapid iterations, reducing the time between builds by making build file preparation quick and easy. The several recoating systems (roller, brush, and silicon wiper) allow for minimal design constraints and a wide selection of metal powders. These advantages are crucial in the development of nozzles and other rocket components.
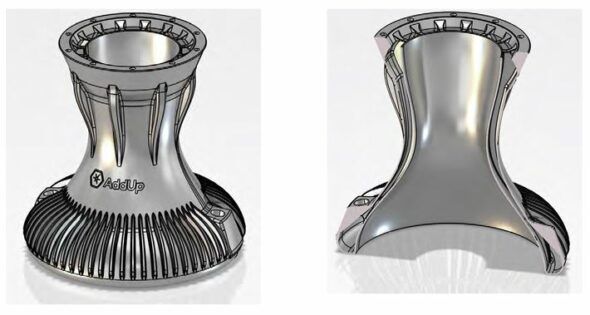
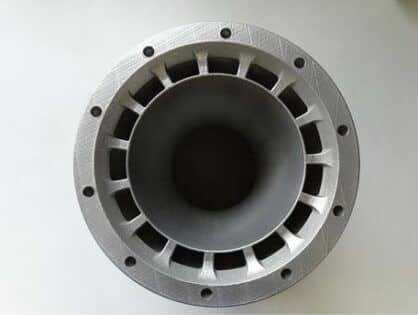
Metal additive manufacturing made it possible to create complex, integrated cooling channels; something impossible with conventional techniques on small engines. This nozzle, which normally requires months of work with traditional welding methods, took only 49 hours to produce. The experts at AddUp chose to use Inconel® 718 to print this new nozzle. This material has excellent mechanical properties and can withstand very high temperatures.
Rocket engine designers can now iterate faster to improve the nozzle shape, running more tests in a smaller timeframe. Engineers can also take advantage of the new design freedom brought about by additive manufacturing, enabling them to push further to optimize engine performance.