The Critical Role of Surface Finish in Fluidic Aerospace Applications: Unveiling its Importance for Heat Exchangers and Turbo Housings.
Author: Mark Huffman, Aerospace and Defense , AddUp
Heat Exchangers: Optimizing Thermal Performance
In the world of aerospace engineering, where safety and reliability are paramount, even the smallest details can have a significant impact. One crucial aspect that often goes unnoticed is the role that surface finish plays in parts and specimens, particularly those created with Laser Powder Bed Fusion (LPBF) technology. Surface finish plays a critical role in the fatigue behavior LPBF parts, influencing stress concentration, crack propagation, residual stress, contact fatigue, and specimen preparation. In this blog, we will delve into how surface finish affects fatigue, thermal integrity, and aerodynamic efficiency with LPBF parts, highlighting its immense importance to the aerospace industry.
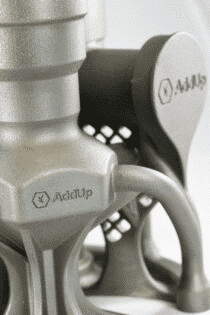
In the realm of heat transfer, efficient airflow is vital for optimal thermal exchange between fluids. The surface finish of LPBF-manufactured heat exchanger components plays a crucial role in facilitating and optimizing airflow, thereby maximizing heat transfer efficiency.
A smooth and uniform surface finish achieved through LPBF reduces surface irregularities, such as roughness, burrs, or surface defects. These irregularities can disrupt the flow of air, leading to turbulence and increased pressure losses. By minimizing surface irregularities, LPBF technology allows for smoother airflow across the heat exchange surfaces.
With improved surface finish, LPBF-manufactured heat exchangers facilitate better contact between the fluid and the heat exchange surfaces. This enhanced contact promotes more efficient heat transfer, as it minimizes the formation of boundary layers. Boundary layers are thin layers of stagnant or slow-moving fluid that can form along the heat exchange surfaces. These layers act as thermal insulators, impeding heat transfer efficiency. By minimizing the boundary layer formation through a smooth surface finish, LPBF-manufactured heat exchangers enable more effective heat dissipation and temperature regulation.
Moreover, a high-quality surface finish achieved with LPBF technology helps reduce the potential for fouling or deposits on heat exchanger surfaces. Fouling occurs when contaminants or deposits accumulate on the surfaces, impeding heat transfer and reducing overall performance. The smoother surface finish provided by LPBF minimizes the adherence of contaminants and promotes easier cleaning, ensuring long-term thermal performance and efficiency.
Turbo Housings: Enhancing Aerodynamic Efficiency
Turbochargers are critical components in aerospace propulsion systems, boosting engine power and efficiency. The surface finish of turbo housings significantly affects their aerodynamic performance. Smooth and well-finished internal surfaces reduce friction and improve airflow, enhancing turbocharger efficiency. A high-quality surface finish minimizes turbulence, pressure losses, and energy wastage. It ensures optimal gas flow, which translates into improved engine power, fuel efficiency, and overall performance. By meticulously controlling the surface finish of turbo housings, aerospace engineers can enhance aerodynamic efficiency, resulting in better engine performance and reduced fuel consumption.
AddUp’s Solution
The integration of fine powder and a roller recoater system in AddUp’s LPBF technology in the FormUp350 can revolutionize the surface finish of aerospace components. By utilizing fine powder with smaller particle sizes and implementing a roller recoater for controlled and uniform powder deposition, manufacturers can achieve superior surface finishes, mitigate stress concentration points, and enhance the fatigue resistance of FormUp350-produced parts and specimens. These advancements pave the way for improved reliability, safety, and performance of aerospace components under cyclic loading conditions.
In fluidic aerospace applications, the significance of surface finish cannot be overstated. Whether in heat exchangers or turbo housings, surface finish optimization directly impacts thermal performance, aerodynamic efficiency, boundary layer separation, and corrosion resistance. By prioritizing a high-quality surface finish, aerospace manufacturers can maximize heat transfer, improve engine performance, enhance fuel efficiency, reduce drag, and ensure the longevity and reliability of critical components. The careful control and optimization of surface finish in fluidic aerospace applications pave the way for safer, more efficient, and more reliable aircraft and propulsion systems, ultimately advancing the capabilities and success of the aerospace industry.