In dieser Fallstudie wird die Entwicklung eines Multimetall- und Multitechnologie-Kolbenkopfes vorgestellt. Ziel war es, die Verschleißfestigkeit und Leistung sowie die internen Kühlkanäle zu verbessern.
INDUSTRY
Automotive
CHALLENGE
Utilize two different Additive Manufacturing technologies and materials to create a single part.
NO SUPPORTS
PERFORMANCE
MASS REDUCTION
Geschichte
Kolben werden traditionell im Gießverfahren hergestellt, bei dem geschmolzenes Metall in eine Form gegossen wird und dort erstarrt. Anschließend durchläuft der Kolben Bearbeitungsvorgänge wie Fräsen, Bohren und Honen, um die genauen Abmessungen und die für den Einsatz in einem Motor erforderliche Oberflächengüte zu erreichen.
Herausforderungen
Die herkömmliche Kolbenherstellung ist mit mehreren Herausforderungen verbunden, darunter Materialauswahl, Präzisionsbearbeitung, Abfallerzeugung und Energieverbrauch. Die Auswahl des richtigen Materials für Haltbarkeit und Hitzebeständigkeit ist entscheidend. Das Erreichen der erforderlichen Abmessungen durch maschinelle Bearbeitung kann kostspielig und zeitaufwändig sein und zu Werkzeugverschleiß und Wartungsproblemen führen. Diese Verfahren erzeugen auch Abfall und haben Auswirkungen auf die Umwelt, was sie weniger nachhaltig macht. Die Einhaltung von Kosten- und Zeitvorgaben kann für die traditionelle Kolbenfertigung eine große Herausforderung darstellen.
Lösung
Eine mögliche Lösung zur Bewältigung der mit der Herstellung und Leistung von Kolben verbundenen Herausforderungen besteht in der Einführung neuer Fertigungstechniken. Die additive Fertigung ermöglicht komplizierte und maßgeschneiderte Kolbendesigns mit internen Kühlkanälen, weniger Abfall und verbesserter Effizienz. Sie kann auch die Verwendung verschiedener Materialien und komplexer Geometrien ermöglichen, die mit herkömmlichen Fertigungsmethoden nicht ohne weiteres zu erreichen sind. AddUp hat ein Konzeptteil erstellt, bei dem sowohl Powder Bed Fusion (PBF) als auch Directed Energy Deposition (DED) zum Einsatz kommen, um den Wert und die Vorteile der additiven Fertigung für die Fertigungsindustrie aufzuzeigen und die richtigen Werkzeuge für die richtige Aufgabe einzusetzen.
Results
The piston was printed in two stages. The first stage used Powder Bed Fusion and the FormUp 350 to print the core of the piston. No supports were used during the entire printing process.
Lattice was added into the geometry to provide an overall lighter weight structure. Reducing the mass can lower stress on engine components, putting less stress on other engine components like the connecting rods and crankshaft. Fuel efficiency is also enhanced by reducing the mass the engine needs to move, leading to better mileage. Internal channels were added to increase the performance and improve heat dissipation, lowering the piston’s temperature, expansion, and emissions. These channels are essential for managing heat and ensuring the reliability, durability, and performance of internal combustion engines.
After the core of the piston was complete, the next stage was to deposit wear resistant ring grooves with Directed Energy Deposition. While the full part could have been printed fully in PBF, it would require support material on the rings. Without the use of supports and the need for powder bed recoating, DED was able to reduce both the print and post processing time required by depositing only the amount of material needed for the rings directly onto the base.
DED was able to deposit a second material with the ability to provide enhanced wear resistance and heat dissipation properties in the piston ring grooves. Not only can DED be used to add high performance material, but can also allow for the repair of piston ring grooves in damaged engine blocks by restoring the grooves to their original dimensions.
Watch the video showing the real piston in Powder Bed Fusion and Directed Energy Deposition here:
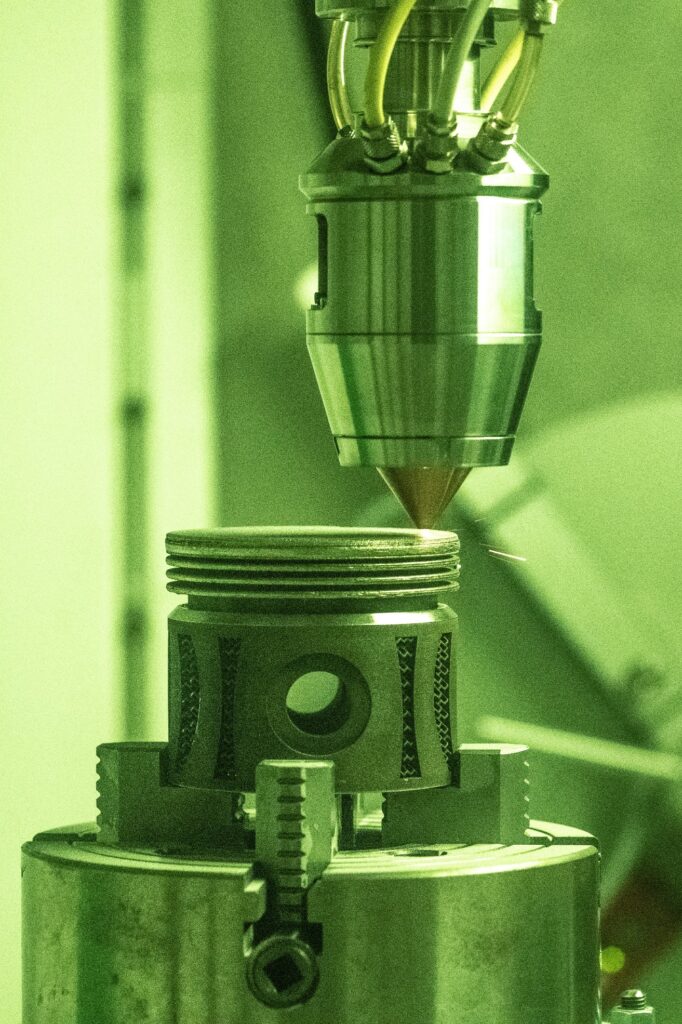
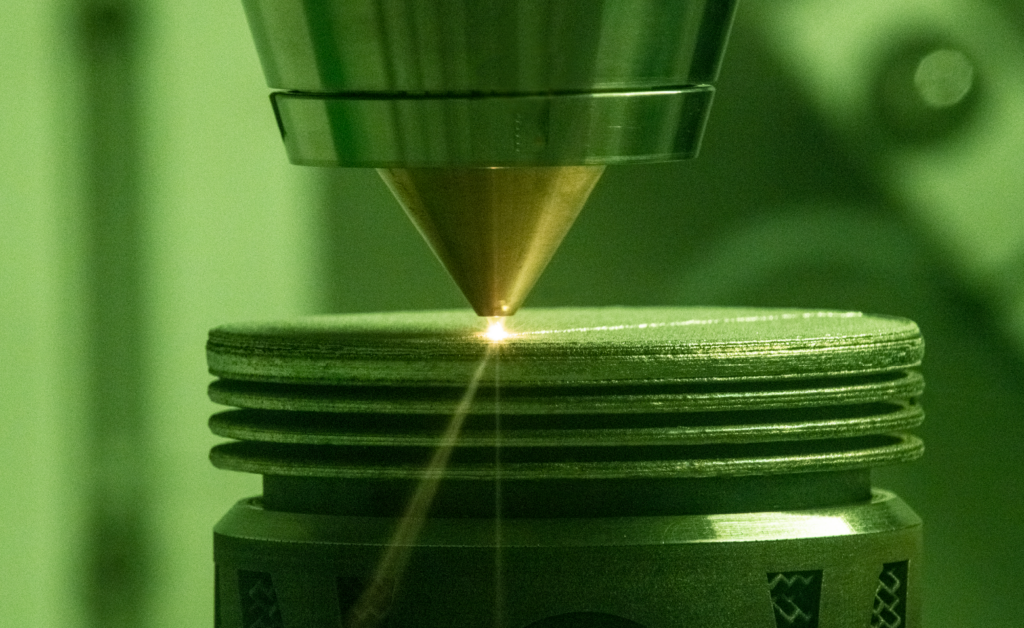
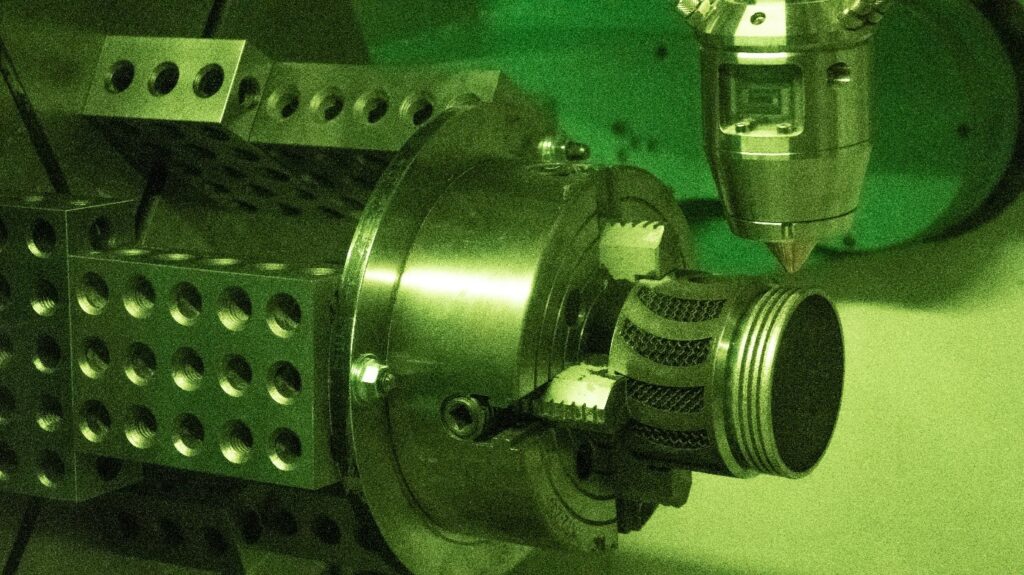
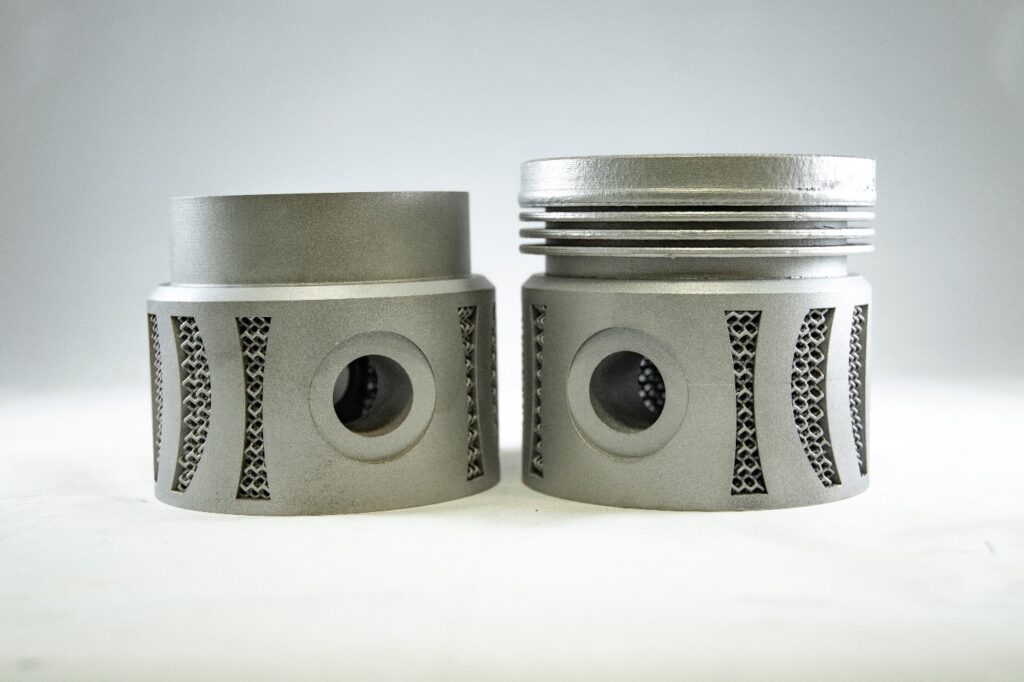
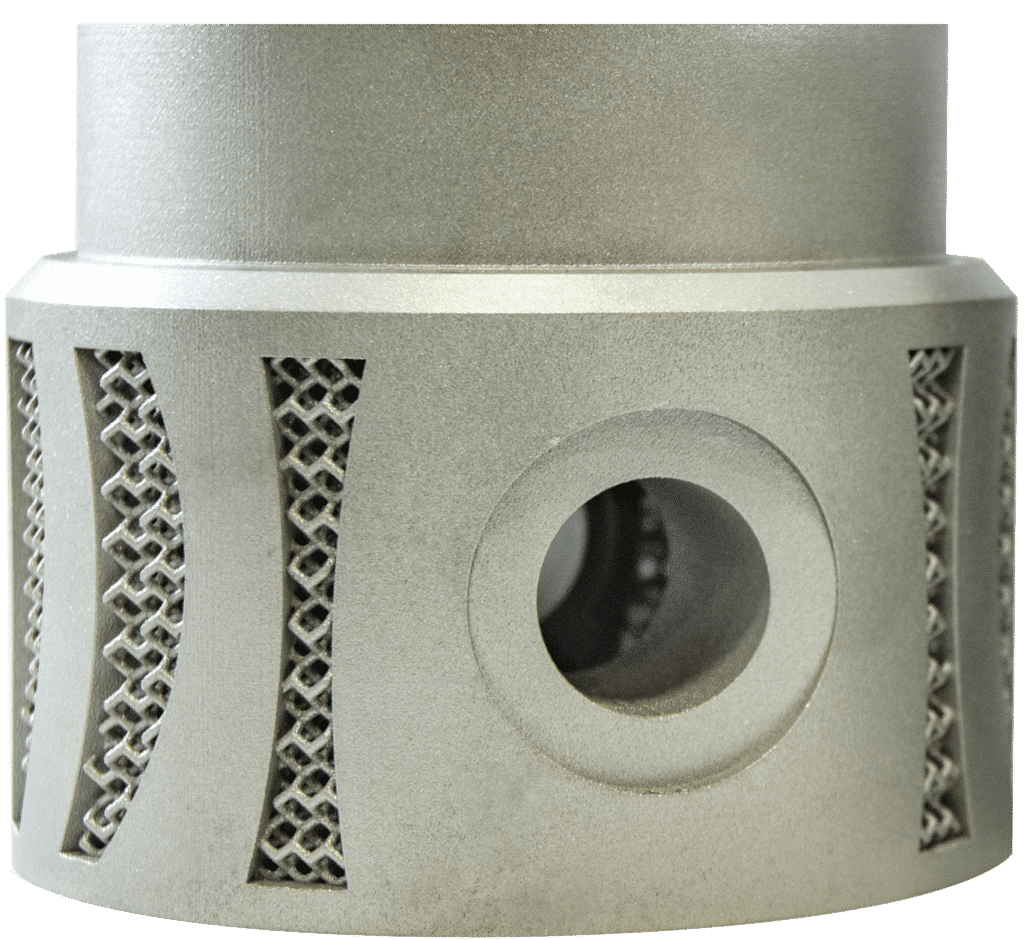
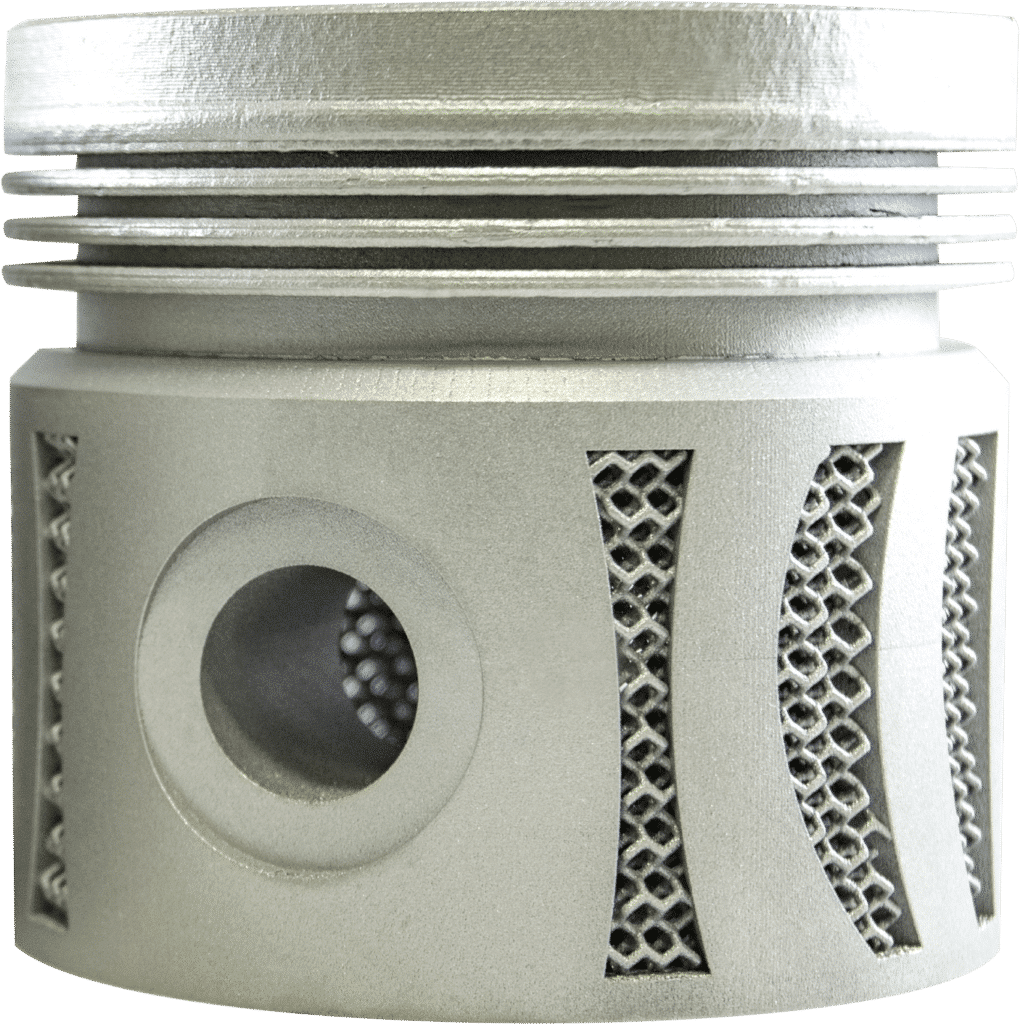
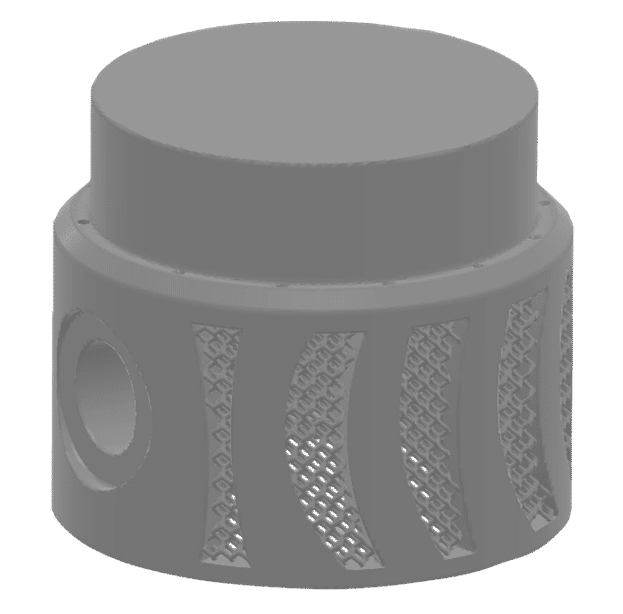
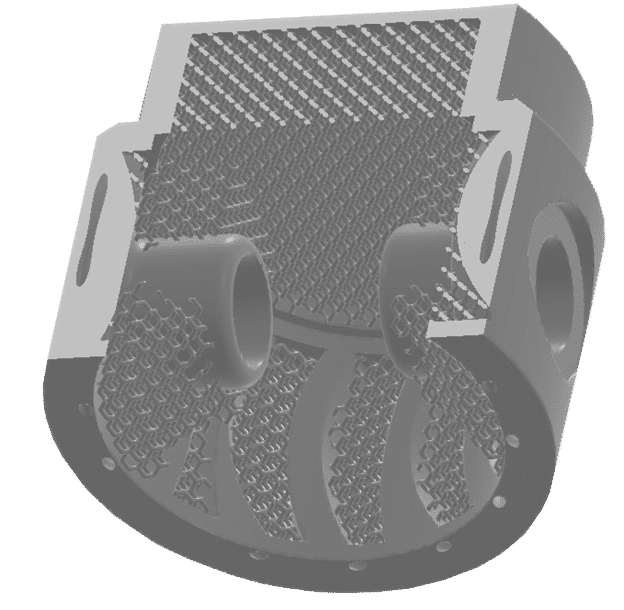
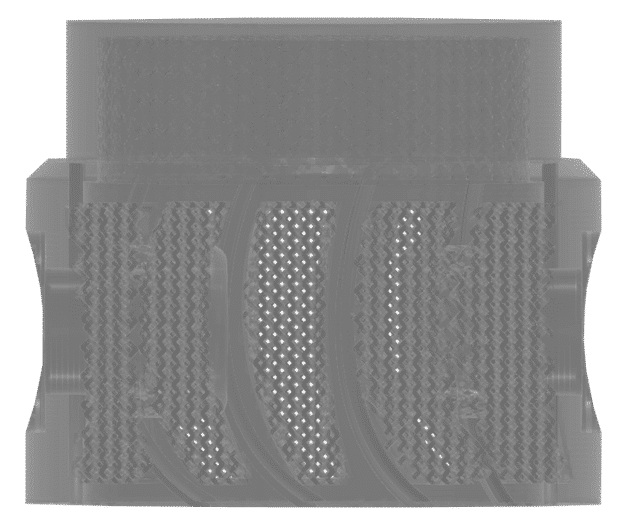
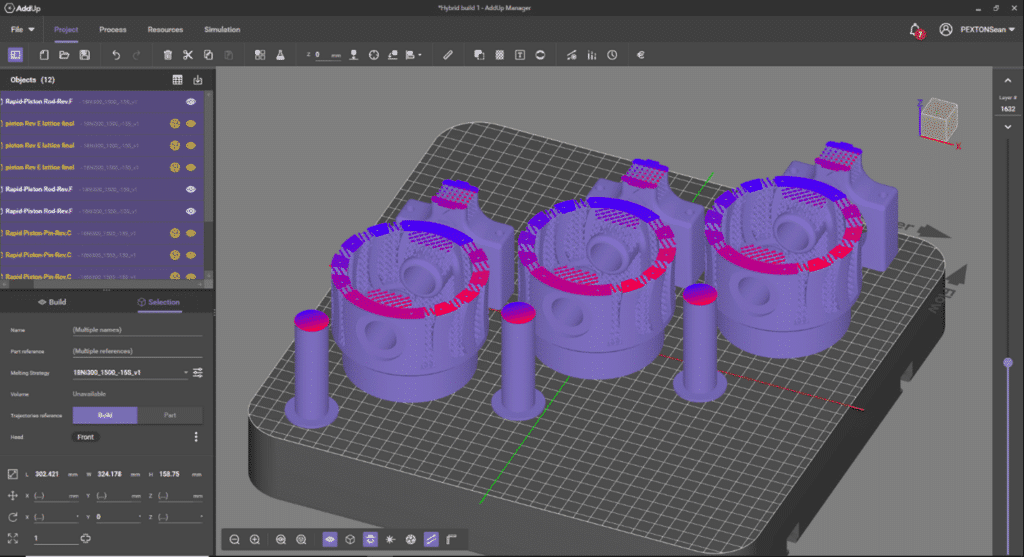
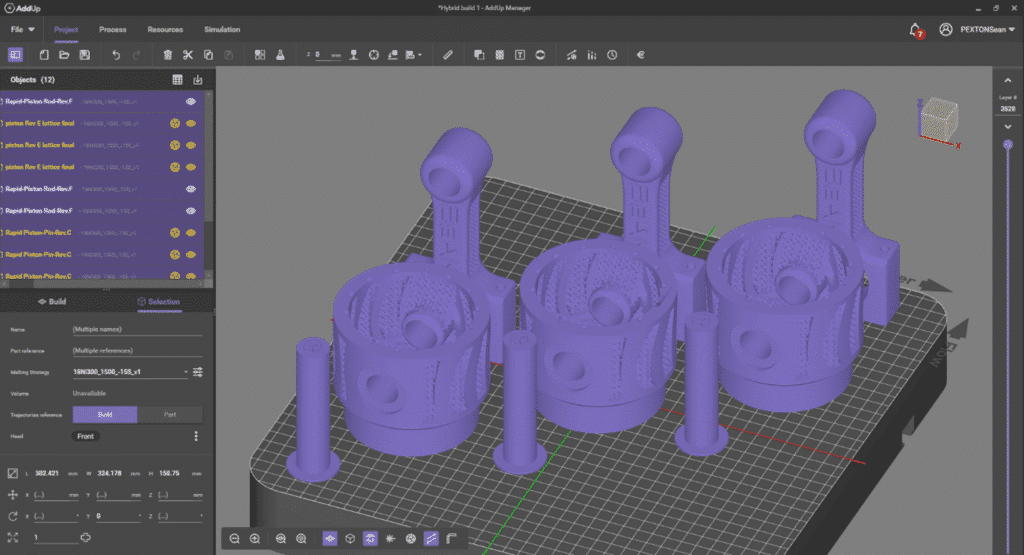
Internal cooling channels
Improved wear resistance and performance
Features added to existing part