La fabrication additive dans l’industrie médicale
La FA permet de produire des modèles très complexes et personnalisés qui peuvent correspondre précisément à l’anatomie du patient, garantissant ainsi un ajustement et une fonction optimaux. La FA permet également la complexité géométrique nécessaire à la création de structures en treillis, non seulement pour réduire le poids, mais aussi pour créer une surface poreuse qui améliore l’intégration de l’os dans le corps humain. Ces avantages offerts par la FA améliorent les résultats pour les patients et réduisent la nécessité d’interventions chirurgicales ou de modifications supplémentaires.
Maîtriser le processus. Reproduire la perfection
L’industrialisation de la FA en vue d’une production en série nécessite une plate-forme reproductible et fiable. La machine FormUp 350 Powder Bed Fusion (PBF) d’AddUp a été conçue pour la productivité. Notre système à 4 lasers réduit les temps de fusion jusqu’à 75 % par rapport à un système à un seul laser, offrant ainsi un débit maximal pour répondre aux exigences du marché des dispositifs médicaux. Il en résulte une efficacité opérationnelle des équipements (OEE) accrue et un coût total de possession (TCO) globalement plus faible.
La FormUp 350 offre une grande flexibilité en termes d’utilisation de la poudre. Elle peut être utilisée avec la poudre moyenne standard du marché, mais elle est également capable de traiter une poudre plus fine. Grâce à notre technologie de mise en couche par rouleau, il est possible d’obtenir une finition de surface lisse avec des caractéristiques fines et une résolution de réseau directement telle qu’elle est imprimée. L’AddUp FormUp 350 offre la liberté de concevoir des implants avec une complexité géométrique et des structures de support minimales, réduisant ainsi la nécessité d’un post-traitement approfondi.
Nous comprenons les besoins des fabricants de dispositifs médicaux et nous leur apportons une aide précieuse tout au long du processus d’adoption de la FA. Nos experts travaillent avec vous pour développer votre application et nous avons les connaissances et l’expérience pour vous aider à réduire votre temps de mise sur le marché tout en offrant une voie de validation avec des processus IQ, OQ, et PQ, ainsi que des directives de réutilisation des poudres.
Rendement maximal
La FormUp 350 fait plus que doubler le rendement des systèmes à laser unique, répondant ainsi à la demande de l’industrie médicale tout en réduisant les coûts pour les fabricants d’appareils médicaux.
Finition de surface supérieure
Obtenez une finition de surface lisse avec des caractéristiques fines et une résolution telle qu’imprimée grâce à notre technologie de recouvrement des rouleaux.
Supports réduits
Réduisez considérablement les exigences de post-traitement et économisez sur les coûts des matériaux.
Un partenaire de confiance
Expérience et parcours de validation avec les processus IQ, OQ et PQ, ainsi qu’une qualification accélérée grâce aux installations certifiées d’AddUp.
Paramètres de machine ouverts
Certains concurrents gardent secret le fonctionnement de leurs machines, mais pas nous. Faites-en plus avec notre plateforme ouverte en adaptant les paramètres comme selon vos besoins.
Assurance qualité
La surveillance en cours de processus offre à nos utilisateurs une tranquillité d’esprit et une assurance qualité en temps réel, ce qui leur permet de s’assurer de la qualité des pièces, d’une fabrication à l’autre et d’une pièce à l’autre.
« La FormUp350 est l’une des seules machines sur le marché à pouvoir exploiter à les poudres LPBF standards et celles beaucoup plus fines. Cela nous donne la flexibilité nécessaire pour répondre à certaines applications difficiles que nous pourrions rencontrer à l’avenir ».
Rachel Levine
Applications clés dans l’industrie médicale
La FA peut améliorer l’efficacité des chirurgies de remplacement car les implants fabriqués de manière additive sont plus légers, plus stables et ont une meilleure ostéointégration. Cela signifie que les implants ont un cycle de vie plus long avec moins de risque de défaut ou de complications de l’implant et donc un meilleur résultat pour le patient et une meilleure qualité de vie.
La FormUp 350 est actuellement utilisé par les clients d’AddUp dans le monde entier pour créer des centaines d’implants orthopédiques certifiés chaque année. AddUp possède une vaste expérience dans le domaine des grands implants orthopédiques, notamment les cupules acétabulaires de la hanche, les implants tibiaux du genou et les implants de l’épaule. Nous avons également de l’expérience dans une variété d’implants rachidiens ainsi que dans les implants spécifiques au patient (sur mesure). La FormUp 350 offre une différenciation accrue des produits et des caractéristiques de conception avancées grâce à notre technologie de mise en couche par rouleau qui permet d’obtenir des caractéristiques d’une précision inégalée.
Cupules acétabulaires de hanche
Ces implants sont utilisés lors d’une chirurgie de remplacement de la hanche, le plus souvent pour traiter l’arthrite, l’arthrose et la polyarthrite rhumatoïde. La FormUp 350 d’AddUp peut fabriquer 34 implants de hanche en seulement 12 heures grâce à un plateau de fabrication de 350 mm de côté exploitable en intégralité par chacun des 4 lasers. Ces implants sont créés sans structures de soutien sur la face inférieure, ce qui réduit considérablement la quantité de post-traitement nécessaire et le matériel utilisé.
Plateau tibial genou
Le plateau tibial est une partie importante de l’implant nécessaire pour une chirurgie de remplacement du genou. Lorsqu’il est fabriqué de manière additive, cet élément de l’implant permet d’améliorer l’ostéointégration, ce qui se traduit par de meilleurs résultats pour le patient après l’opération. La FormUp 350 peut fabriquer 22 plateaux tibiaux en seulement 17 heures. Ces implants sont imprimés avec un minimum de supports, ce qui réduit considérablement la quantité de post-traitement nécessaire, réduisant ainsi les coûts globaux pour le fabricant de l’appareil.
Implants d’épaule
Les implants d’épaule sont un élément essentiel de la préservation de la fonction de l’épaule. L’articulation de l’épaule de chaque patient présente des caractéristiques uniques, et la possibilité de personnaliser les implants est un avantage significatif de la FA. Elle permet de concevoir et de fabriquer des implants spécifiquement adaptés à l’anatomie d’un patient, tout en incluant des structures internes complexes et des surfaces poreuses pour une meilleure intégration avec l’os environnant.
Implants pour la colonne vertébrale
La fusion vertébrale permet de relier deux ou plusieurs vertèbres à l’aide d’un greffon osseux placé à l’intérieur d’un implant en titane. Cette opération permet de traiter des troubles tels que la discopathie dégénérative, la scoliose, le spondylolisthésis et les fractures. AddUp possède une vaste expérience dans la création d’implants vertébraux de différentes tailles avec des structures de soutien uniques. Cette expérience, combinée à la productivité de la FormUp 350, permet de réduire les coûts pour les fabricants de dispositifs médicaux. La FormUp 350 peut imprimer 152 implants rachidiens de grande taille en seulement 32 heures.
Implants spécifiques au patient
Les implants spécifiques au patient (PSI) sont des implants fabriqués à partir des données de tomodensitométrie d’un patient, transférées dans un fichier de CAO, puis fabriquées de manière additive. Les PSI sont généralement trop complexes à usiner et à découper, c’est pourquoi ils sont idéalement fabriqués par FA. AddUp dispose d’une grande expérience dans la fabrication de chevilles, d’épaules et de dispositifs vertébraux spécifiques aux patients. La FormUp 350 dispose d’un grand plateau de fabrication qui permet d’imprimer de nombreux implants de formes et de tailles différentes au cours d’une même construction. La possibilité de fabriquer plusieurs cas chirurgicaux individuels sur une seule plaque de construction rationalise le processus entre le site de fabrication et l’hôpital. Chaque patient peut ainsi bénéficier d’un implant entièrement personnalisé qui répond à ses besoins uniques, tout en réduisant les coûts de l’opération et les délais de rétablissement.
Aerospace
Antenne Cassegrain
Antenne prête pour le vol dans un lit de poudre Fusion Thales Alenia Space est un constructeur aérospatial français qui joue un rôle important dans l’exploration spatiale depuis plus de […]
Michelin lamelles de pneus
Lorsque Michelin a constaté que les machines de fabrication additive métallique sur le marché ne répondaient pas à leurs exigences en terme de qualité pour la production de lamelles de pneus, ils se sont associés à Fives pour créer une machine qui réponde à ces besoins. Découvrez l’histoire des lamelles de pneus, les défis que devait relever Michelin et les solutions qui ont été apportées avec l’impression 3D métallique.
Tuyère imprimé en 3D
AddUp optimise le design d’une tuyère de fusée pour améliorer les performances d’un micro-lanceur.
Implants pour la colonne vertébrale
Cette étude de cas se concentre sur les implants rachidiens et les défis auxquels ils sont confrontés dans leur processus de fabrication aujourd’hui. La fabrication additive (AM) offre des avantages tels que la conception en treillis et la rugosité de la surface, ce qui permet d’améliorer les résultats pour les patients.
Aérospatiale
Étude de cas Isogrid
Cette étude de cas présente le développement d’un échangeur de chaleur optimisé pour la machine Form Up® 350. L’objectif était d’améliorer la dissipation de la chaleur et d’adapter les dimensions pour faciliter l’installation.
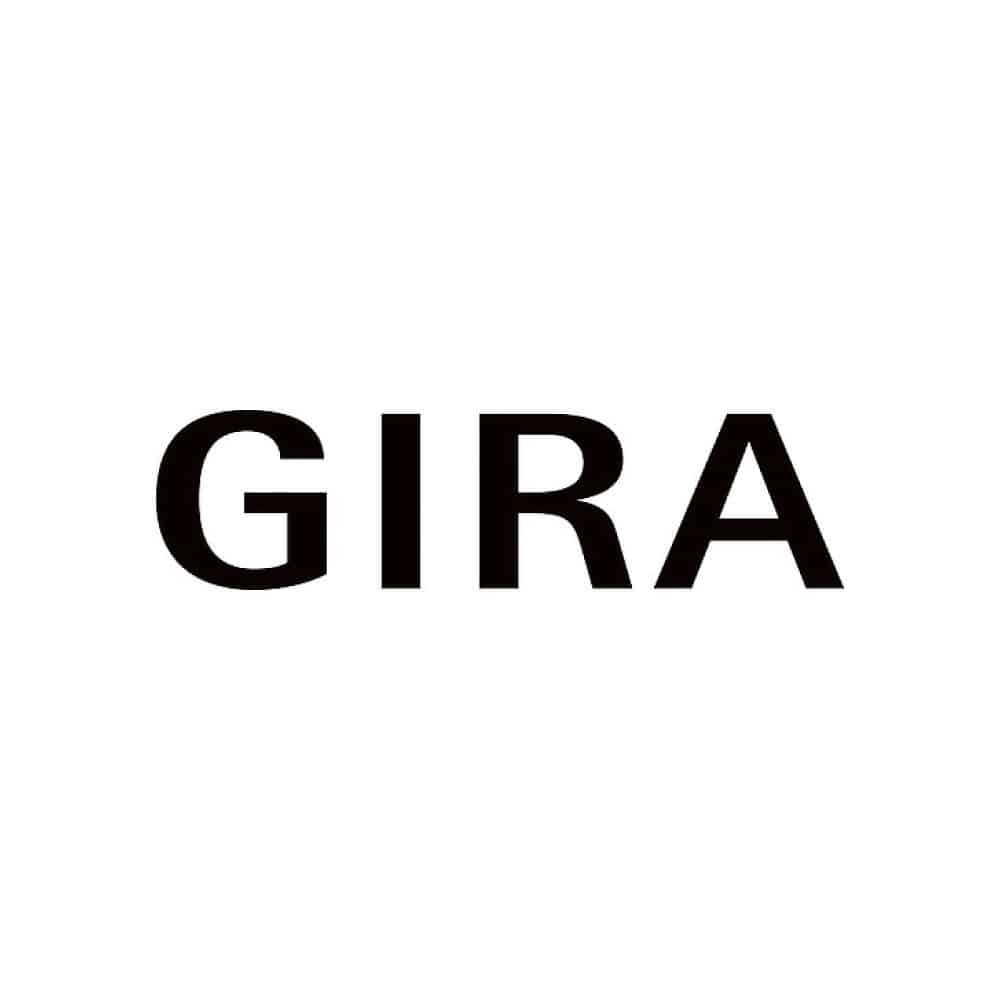
Outillage et moulage
Étude de cas Gira
Combiner la fabrication traditionnelle et la fabrication additive Ajout de caractéristiques grâce au dépôt d’énergie dirigée
Automobile
TÊTE DE PISTON MULTI-MÉTAUX ET MULTI-TECHNOLOGIES
Cette étude de cas présente le développement d’une tête de piston multi-métaux et multi-technologies. L’objectif était d’améliorer la résistance à l’usure et les performances, ainsi que les canaux de refroidissement internes.
Échangeur de chaleur FormUp
Optimiser le flux d’évacuation des fumées de fusion. Le projet de réalisation d’un échangeur thermique pour la machine FormUp® 350 est né de la volonté de profiter du savoir-faire développé par PrintSky, une société commune créée par AddUp, fabricant de machines d’impression 3D métallique, et Sogéclair, fournisseur de solutions innovantes pour une mobilité plus sobre et plus sûre. Il s’agissait d’évaluer l’intérêt d’une solution optimisée en fabrication additive en la comparant avec le système actuel, produit par des méthodes conventionnelles.
Matériaux utilisés dans l’industrie médicale
Les matériaux typiques utilisés dans les implants orthopédiques doivent être légers, durables et biocompatibles. Les matériaux utilisés dans la production d’instruments chirurgicaux doivent être durables, rentables et avoir une bonne durée de vie.
Titane Ti64ELI
Le titane Ti64ELI est le plus souvent utilisé dans les implants orthopédiques en raison de ses caractéristiques. Il s’agit d’un matériau solide, léger et très biocompatible. AddUp a optimisé les paramètres de ce matériau pour les couches de 30 et 60 microns.
Acier inoxydable 316L
L’acier inoxydable 316L est un acier chirurgical et peut être utilisé pour créer des instruments chirurgicaux rentables.
Acier inoxydable 17-4 PH
L’acier inoxydable 17-4 PH est également un bon matériau pour la fabrication d’instruments chirurgicaux. Il est non seulement économiquement pertinent, mais présente également une résistance exceptionnelle.
Machines industrielles
Avec plus de 20 ans d’expérience dans la fabrication additive, nos machines ont été conçues pour maîtriser les détails et optimiser la productivité.
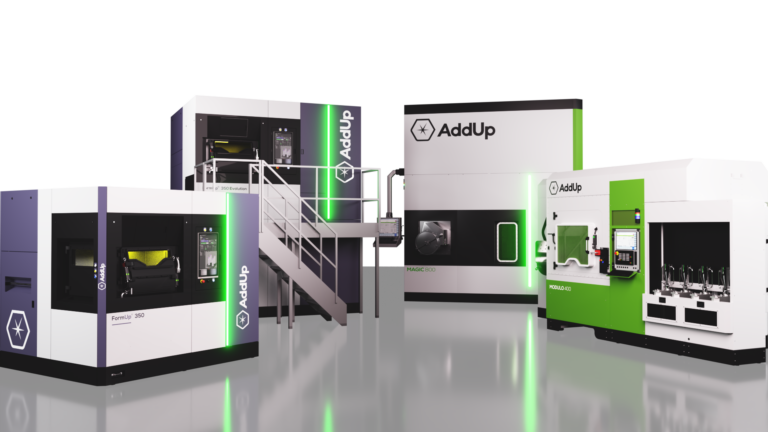
Logiciel intelligent
Dans l’industrie médicale, la qualification et la réglementation des implants et des dispositifs sont obligatoires. AddUp est à la pointe du progrès en matière de contrôle en cours de fabrication, en garantissant la qualité des pièces grâce à une suite complète de logiciels de contrôle d’assurance qualité permettant de réduire, voire d’éliminer, la nécessité d’effectuer des tests rigoureux après l’impression d’une pièce. De la préparation des pièces à la simulation, au contrôle et à la production, chaque maillon de la chaîne numérique AddUp offre un haut niveau de performance avec des logiciels accessibles.
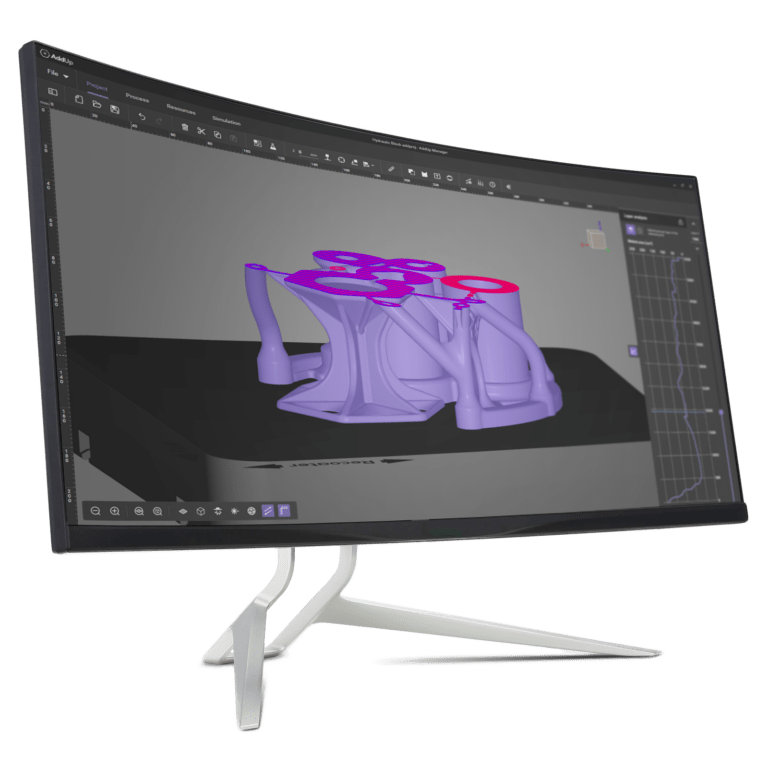
Débuter avec AddUp
Réalisez le potentiel que la fabrication numérique a à offrir. Commencez avec AddUp et découvrez comment la FA fournit des solutions innovantes pour résoudre les défis les plus complexes.
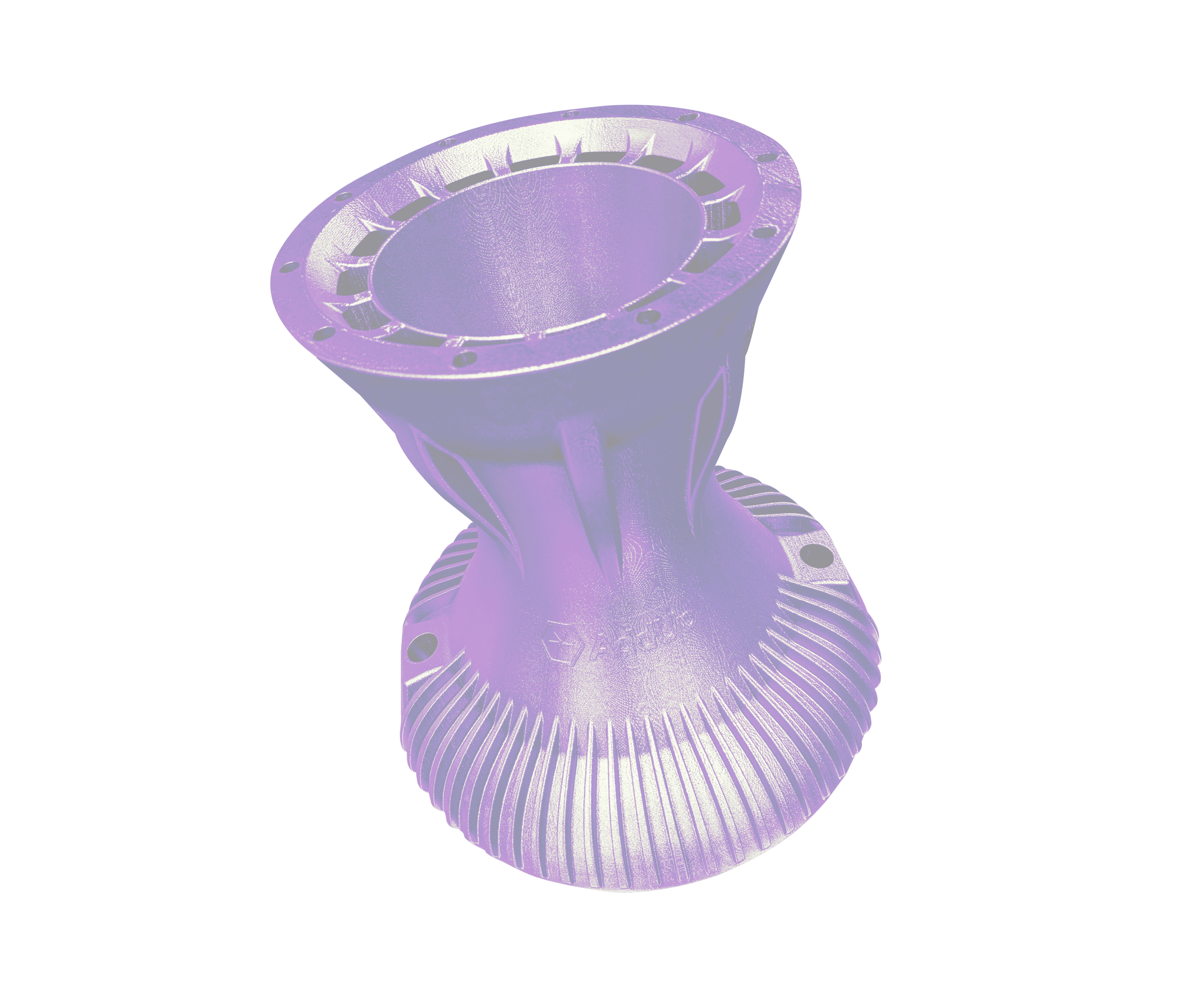