Discover how Michelin produces over one million tire sipes a year for their production molds using metal 3D printing
When Michelin found that the metal AM machines on the market did not meet their high-quality requirements for tire sipe production, they partnered with Fives to create a machine that met these requirements. Learn about the history of tire sipes, the challenges Michelin faced, and the solutions that resulted.
INDUSTRY
Automotive
CHALLENGE
Traditional manufacturing of tire sipes is costly and
time consuming.
KEY BENEFITS
- Limitless personalization options
- Manufactured and replaced on demand
- Significant weight and material waste reductions
- Minimal post processing
Creative Shape
Lead Time
Weight
Performance
History
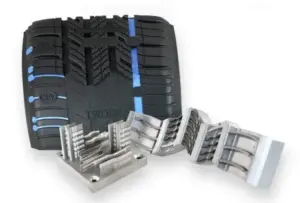
Siping was invented in 1923 by John F. Sipe, as a means to provide better traction on the bottom of their shoes. The process was not largely applied to tires until the 1950s as a means to improve traction. One of the technological innovations of the 2000s was the arrival of metal 3d printed sipes. Sipes for tires are designed to heavily improve road holding on wet or wintery roads, while still allowing the rubber to remain rigid, and maintain these levels of rigidity when the tire is new or worn. The shape and size of the sipes directly affect the tire’s noise pattern and traction characteristics. Using Additive manufacturing to create metal-printed sipes opened a new world of possibilities.
Challenges
Conventional manufacturing and installation of tire mold inserts involve a light metal casting of an aluminum-silicon alloy, which allows for rapid heat removal, shortening production time. Tire mold segments are made by casting or milling with finishing carried out manually. Broad sipes can be inserted into the mold segments, but narrow inserts less than 3mm are not easy to work with due to the hardness characteristics of the alloy. Steel sipes are used as inserts in their stead, made by stamping and cold bending; a major cost and time element of the process.
SOLUTIONS
Michelin has been utilizing AM since the early 2000s to manufacture tire sipes used within their tire molds. After years of using AM technology, Michelin found that the metal AM machines on the market simply did not meet their high-quality requirements for serial production. So, they partnered with another industrial manufacturing powerhouse, Fives, and sought to develop a Laser Powder Bed Fusion (L-PBF) machine that could build tire mold inserts and industrial parts with quality, accuracy, and repeatability. From this collaboration, AddUp was formed and the FormUp® 350 PBF machine was created.
AddUp’s high-precision, fully digitalized, and highly flexible process allows Michelin to produce the complex forms required to make molds and sipes for its tires. Critically important features to Michelin’s tire sipes:
- resolution down to 0.2mm features
- shallow overhangs as low as 15 degrees
- surface finish as low as 4 Ra μm, as printed
The FormUp®350 is built to use extremely fine powders (5-25μm). This coupled with a roller recoating system enables support-free production and superior surface finishes. For Michelin, sipes can be manufactured and replaced on demand with minimal post-processing needed. This technique not only provides a quick assembly, but also provides weight savings, reduces raw material wastage, and provides limitless personalization opportunities.
Results
Today, Michelin produces over one million tire sipes a year for their production molds using AddUp’s FormUp® 350. Lead designers continue to create increasingly sophisticated sipe shapes to improve traction for wet and snowy conditions. For example, a winter tire mold can contain up to 3,000 sipes and over 200 different sipe designs! AddUp’s FormUp Powder Bed Fusion technology stands up to the task and can produce these sipe shapes efficiently and to the highest quality standards.
By completely transforming the processes used to produce parts, the metal additive is changing manufacturing as a whole. Now there is no longer any need to go through several preliminary steps or assemble different components to obtain the desired part, instead, the final product can be produced in a single step. Digital files are the only information needed to reproduce the exact same part, and parts can be modified at any time to make the process more flexible than ever before.