INDUSTRIE
Automobile
CHALLENGE
Reduire les temps et les coOts de production tout en ameliorant les performances par rapport a la fabrication traditionnelle en optimisant la strategie de numerisation.
KEY BENEFITS
- Strategie de numerisation optimisee pour un meilleur etat de surface des geometries de roue
- Le PBF s’est revels etre une option viable pour les roues dans l’industrie automobile, tant en termes de cout que de performance
- Comparaison des methodes d’essai et d’inspection pour l’uniformite geometrique et de densite des pieces additives par rapport aux pieces traditionnelles
Increased Productivity
Cette étude de cas explore la faisabilité de l’utilisation de la fabrication additive, en particulier la machine Form Up 350 PBF, pour produire plus de 100 000 roues Impeller par an pour Ford, en remplacement des techniques d’usinage traditionnelles.
HISTOIRE
Ford utilise des méthodes de fabrication traditionnelles pour fabriquer plus de 100 000 roues de turbines par an . Ford, Oak Ridge National Labs et AddUp ont mené une étude pour déterminer la faisabilité de la production des roues à aubes par Fabrication Additive à l’aide de la FormUp 350.
Ford s’appuie sur sa vaste expérience de plus d’un siècle dans le domaine de l’automobile. Oak Ridge National Labs optimise la stratégie de numérisation et le nombre de passes de contour. AddUp apporte son expertise en matière de conception, de fabrication et d’automatisation pour la production à grande échelle grâce à sa machine industrielle FormUp 350 (L-PBF).

DÉFI
Ford fabrique actuellement ses roues à aubes en utilisant des techniques d’usinage traditionnelles. Le défi proposé à AddUp était d’étudier les performances de la technologie PBF afin de remplacer l’usinage traditionnel, pour la fabrication en série de ces pièces. L’objectif était de réduire les délais et les coûts de production tout en améliorant les performances par rapport à la fabrication traditionnelle.
Le résultat devrait permettre de fabriquer efficacement 100 000 hélices en Fabrication Additive et d’élaborer une stratégie d’impression optimale pour la performance, en tirant parti de la liberté de conception offerte par la Fabrication Additive tout en optimisant la stratégie de numérisation pour l’état de surface et la productivité.
SOLUTION
La pièce a été testée avec 1 passe de contour puis 5 passes de contour. Lors de la fusion avec 5 passes de contour, la surface présentait une porosité accrue par rapport à une seule passe. Par conséquent, une seule passe de contour est suffisante, compte tenu de sa position au-delà des lignes de hachures, permettant d’éliminer les motifs de hachures. Les tolérances de l’imprimante étaient également suffisantes. Comme il fallait un matériau robuste et résistant à la chaleur, le choix s’est porté sur l’Inconel 718. L’utilisation du paramètre « downskin » d’AddUp permet au logiciel de tranchage de reconnaître les surfaces critiques orientées vers le bas avec une valeur d’angle en dessous d’un seuil défini par l’utilisateur. Ce paramètre « downskin » applique généralement une densité d’énergie plus faible aux régions de fusion décalées par rapport au bord des surfaces orientées vers le bas et ce pour un nombre donné de couches . Lors de l’impression avec de l’Inconel 718, une structure de support sur le fond de la roue était nécessaire. AddUp a imprimé un test de simulation de 9 roues à aubes avec de l’Inconel 718. Après post-traitement, deux roues ont été sélectionnées pour être soumises à un test d’équilibre.
RÉSULTATS
Les résultats ont indiqué que les roues produites dans le cadre de cette étude ont passé le test de tolérance et qu’elles pouvaient être correctement équilibrées en utilisant la même procédure que les roues fabriquées de manière traditionnelle. Le test a également indiqué que les pièces pouvaient survivre à un test de rotation à haute vitesse à température ambiante.
Paramètres du modèle de coût en fonction de la production de pièces.
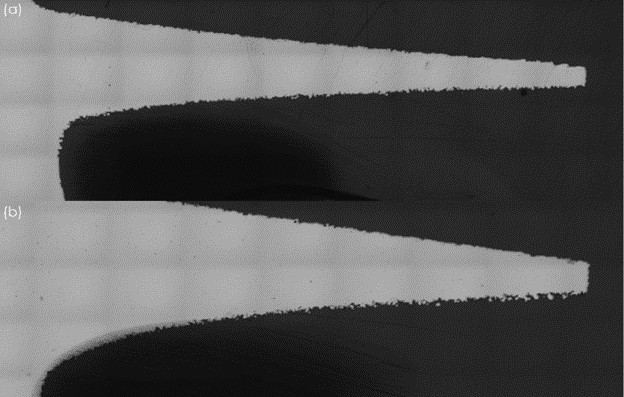
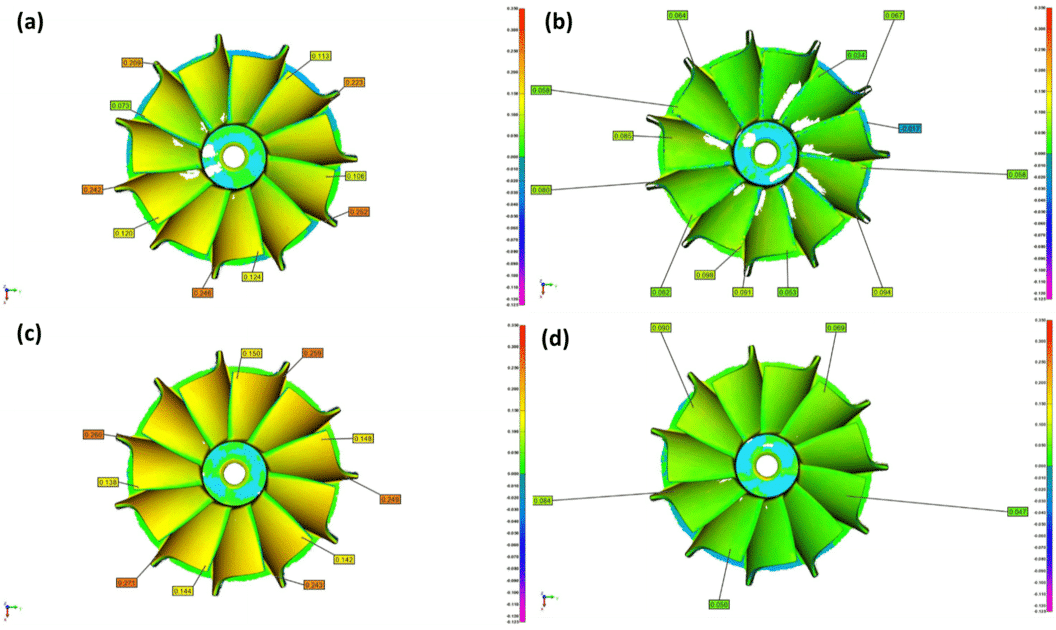
(a) Micrographie optique d’une surface « downskin » ayant subi une seule passe de contour et
(b) micrographie optique d’une surface « downskin » ayant subi cinq passes de contour. Bien qu’un plus grand nombre de passes de contour puisse être utile, la position du contour extérieur détermine l’état de surface, comme le montrent les particules partiellement fondues qui adhèrent à la surface.
Tolérances géométriques mesurées par balayage lumineux de roues turbo dont le contour extérieur s’étend sur la distance suivante au-delà des limites de la CAO :
- (a) #08 à 36µm
- (b) #11 à 11µm
- (c) #13 à 61µm et
- (d) #19 à 36µm, mais fondu de l’extérieur vers l’intérieur
Nom de la piece | Roue |
---|---|
Modele crim rlante 3D | AddUp Form Up 350 |
Construction Taille de la plaque | 350 x 350 mm |
Nombre de pieces par lot | 25 |
Temps d'impression par lot | 32,28 heures |
Estimation du coOt des materiaux pour l'Inconel 718 | 70 $/kg |
Masse de la piece | 0.311 kg |
Masse des supports | 0.05 kg |
Temps de depoudrage par lot | 0,5 heure |
Temps de retrait des supports par lot | 30 heures |
Temps de post-traitement par lot (traitement thermique) | 12 heures |
Volume annuel requis | 100 000 unites par an |