La mise au point de nouveaux matériaux utilisables avec la technologie de l’AM est une étape essentielle pour exploiter pleinement le potentiel de l’AM.
La fabrication additive (AM) est une technique de fabrication révolutionnaire qui va remodeler le secteur manufacturier de demain. La liberté de conception, la réduction des déchets et la personnalisation de masse sont quelques-uns des avantages de l’AM. Même si la technologie AM n’est pas encore utilisée par tous les fabricants, le potentiel à venir est énorme. La mise au point de nouveaux matériaux utilisables avec la technologie de l’AM est une étape essentielle pour exploiter pleinement le potentiel de l’AM.
Dans le processus d’évolution de la technologie AM, il est nécessaire de développer des paramètres de fusion pour les alliages standard existants et les alliages nouvellement conçus afin que les propriétés des matériaux atteignent ou dépassent les techniques de fabrication conventionnelles telles que le moulage, le forgeage, le laminage et l’usinage, etc.
Outre le développement de matériaux, une qualification appropriée est nécessaire pour fabriquer des composants critiques pour des applications médicales, aérospatiales et d’outillage. La qualification des matériaux peut prendre beaucoup de temps et coûter cher, selon l’application ou l’industrie. La première étape de ce processus consiste à établir des paramètres de fusion de base pour lesquels des données suffisantes doivent être collectées afin de démontrer que le matériau fonctionnera comme prévu.
Le développement de matériaux pour l’AM des métaux est un processus complexe qui nécessite une compréhension approfondie des températures de fusion et de resolidification et des microstructures correspondantes. Les stratégies de fusion peuvent avoir plusieurs objectifs spécifiques, tels que la qualité des pièces, la productivité et les caractéristiques spécifiques, de sorte qu’il n’est pas possible d’adopter une approche « unique ». Pour le développement de produits spécifiques à une application, il faut garder à l’esprit le cas d’utilisation du client pour le développement des matériaux, du début à la fin.
L’ajout de nouveaux matériaux au catalogue existant nécessite des tests et des analyses rigoureuses pour s’assurer que la pièce imprimée répond aux exigences de qualité. Cela nécessite un énorme travail de définition et d’exécution des protocoles d’impression, de test et d’analyse. Ce blog explore quelques-unes des considérations importantes dans le développement des paramètres de fusion.
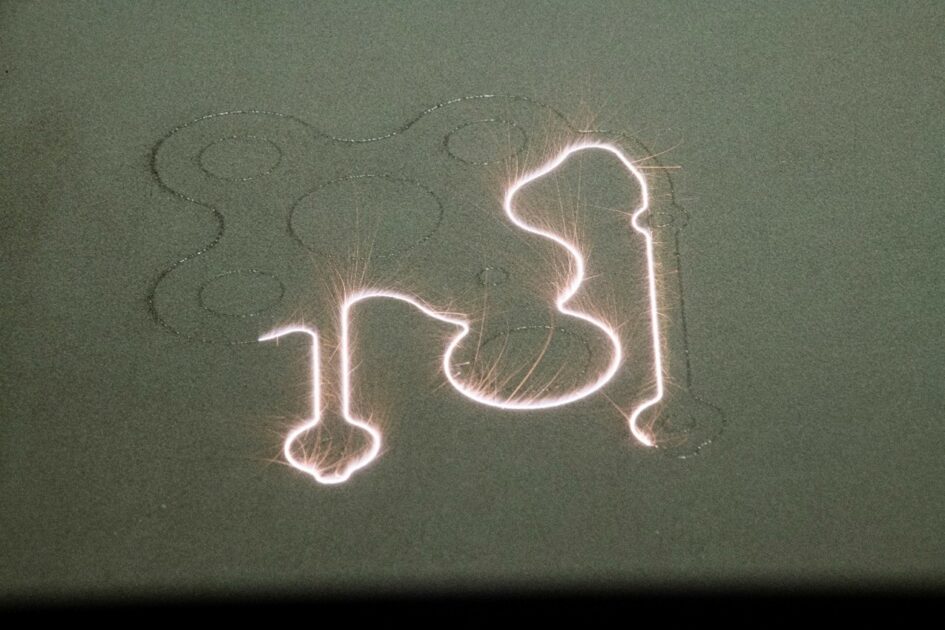
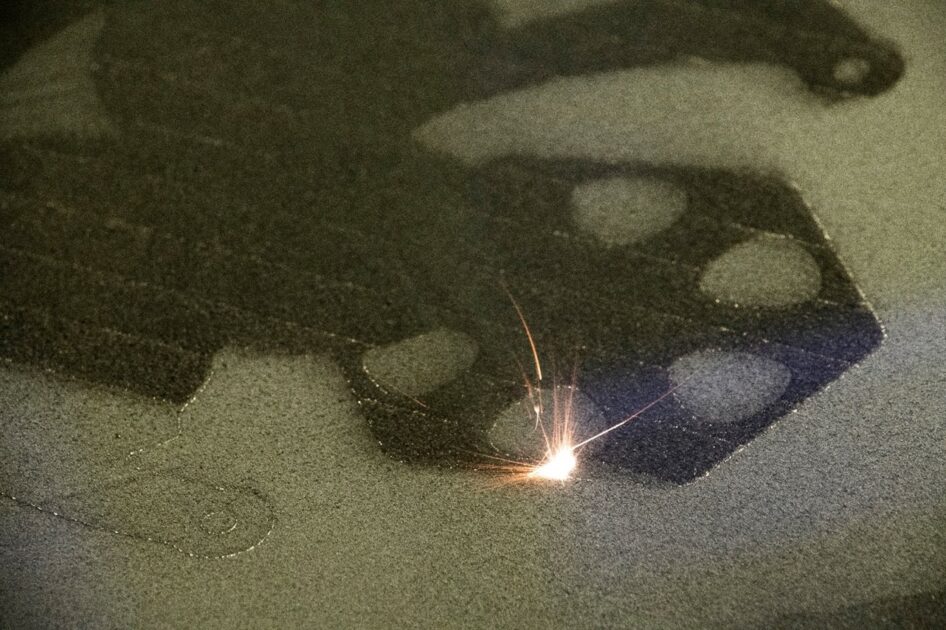
Propriétés des matières premières
La sélection du matériau de base est la première et la plus importante étape du processus d’AM des métaux. Les attributs clés de la poudre métallique, tels que la forme, la taille, la fluidité et la composition chimique, contribuent à l’obtention de pièces de haute qualité. Il est donc important de choisir la bonne poudre en fonction de la fonctionnalité requise de la pièce.
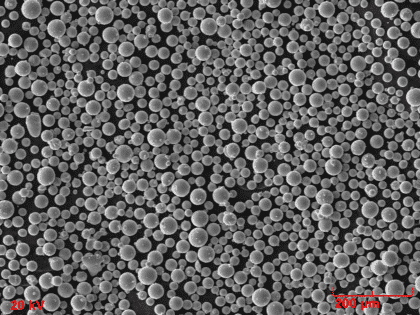
Dimensions de la piscine
Cet aspect du développement mesure les caractéristiques physiques d’un seul passage de perles, ainsi que les dimensions du bain de fusion de chaque perle. Une approche expérimentale statistique combinée à des analyses de simulation peut être utilisée pour identifier les principaux paramètres de fusion afin d’obtenir les dimensions appropriées de la piscine de fusion pour atteindre les densités solides requises.
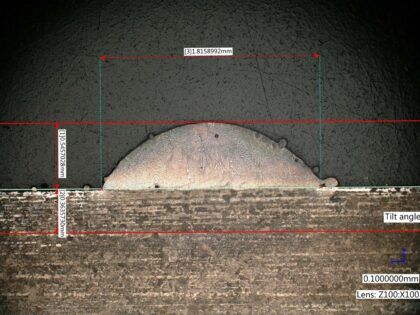
Densité de la partie solide
La densité des pièces solides est une mesure de la porosité à l’intérieur d’une pièce imprimée et s’appuie sur le réglage des billes individuelles en modifiant la façon dont elles sont imprimées les unes à côté des autres. L’épaisseur des couches et les angles de rotation du balayage laser ont un impact significatif sur la manière dont ces passes de fusion interagissent les unes avec les autres. Cela a un impact direct sur la densité et les microstructures des pièces imprimées. La densité des pièces solides peut être testée à l’aide de techniques telles que la métallographie ou le balayage MicroCT.
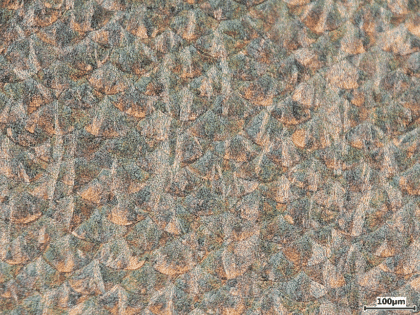
Performance des matériaux
Les performances des matériaux imprimés doivent être testées de manière approfondie lors de la mise au point de nouveaux paramètres de fusion. Cela comprend la collecte de données physiques et mécaniques à partir de divers tests. En outre, il est nécessaire de vérifier le gauchissement et tout autre écart dimensionnel de la pièce imprimée avant et après les conditions post-thermiques. Cela permet de comprendre les sous-produits des contraintes internes et l’efficacité des conditions post-thermiques sur la géométrie de la pièce.
Ces données préliminaires sur les dimensions, la densité, l’état de surface et la résistance à la traction permettent de valider la qualité de la stratégie de fusion avant de passer à un processus de qualification coûteux spécifique à l’application.
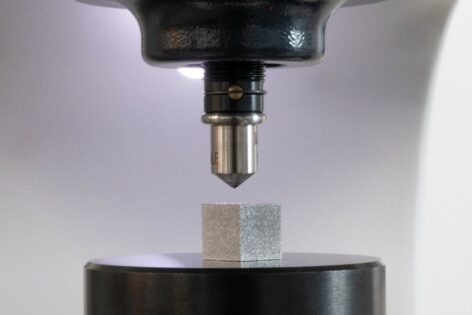
Optimisation des cas d’utilisation spécifiques
Si des paramètres de fusion de base optimisés sont nécessaires pour imprimer la plupart des pièces, des mesures supplémentaires doivent être prises en cas d’exigences de qualité spécifiques. Il est essentiel d’intégrer les exigences de production et de qualité des pièces, telles que l’état de surface, la productivité, la résolution des caractéristiques, etc. dès le début du développement.
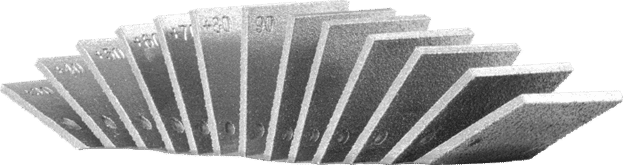
La différence AddUp
Le catalogue de matériaux d’AddUp comprend un mélange varié de différents alliages d’acier, de titane, d’aluminium, d’Inconel, etc. Nous travaillons en permanence au développement et à l’optimisation des paramètres de fusion pour de nouveaux matériaux afin de répondre aux besoins de l’industrie. AddUp utilise une approche entièrement fondée sur les données et des données spécifiques à l’application pour développer de nouveaux matériaux ou modifier les stratégies de fusion existantes. Grâce à notre équipe d’experts en ingénierie des matériaux et à nos capacités d’essai internes, nous pouvons élaborer rapidement et efficacement des stratégies de fusion pour des matériaux nouveaux ou existants. Dans ce processus, nous sommes ouverts à la collaboration avec des partenaires industriels et des chercheurs universitaires.
Regardez cette vidéo présentant une partie de notre processus de développement de matériaux pour Zeda en acier inoxydable 17-4 PH dans notre AddUp Solution Center à Cincinnati, OH.
En savoir plus sur les capacités du FormUp 350.