AddUp optimise le design d’une tuyère de fusée pour améliorer les performances d’un micro-lanceur.
La fabrication additive métallique peut induire des économies de carburant et de production dans l’aérospatial. Dans cette étude de cas vous verrez comment AddUp a optimisé le design d’une tuyère de fusée pour améliorer les performances d’un micro-lanceur. L’impression 3D est déjà l’avenir de l’industrie spatiale. Lisez l’étude de cas sur une conception optimisée d’une tuyère imprimée en 3D.
Industrie
A&eactue;rospatial
CHALLENGE
Imprimer une tuyère de fusée innovante pour optimiser les performances du moteur dans l’espace
KEY BENEFITS
- Réduction de la masse
- Pièce imprimée avec une géométrie complexe
- Résistance aux hautes températures
Réduction de la masse
Forme complexe
Intégration de fonctions
Performance
Histoire: AddUp et aerospatial
Dans le secteur de l’aérospatial, l’allégement des composants et leur personnalisation peut induire des économies considérables de carburant et de coûts de production, mais aussi des gains de performance, Nombreux sont les industriels à penser que l’impression 3D est l’avenir de la fabrication aérospatiale. Si les satellites ont diminué en taille ces dernières années, la taille et la puissance des fusées n’a fait qu’augmenter. Un micro-lanceur spatial est capable de placer en orbite une charge utile de masse inférieure à cinq cents kilogrammes. Il constitue l’une des facettes les plus prometteuses du New Space : les micro et mini-lanceurs apportent une flexibilité et une réactivité qui en font une solution complémentaire aux lanceurs classiques.
Une tuyère est un élément qui compose les moteurs des fusées ou lanceurs par lequel sont éjectés les gaz de combustion. Correspondant au conduit terminal de la chambre de combustion de la fusée, cette pièce joue un rôle primordial car elle transforme en énergie cinétique l’énergie des gaz de combustion.
Les défis de l’impression de tuyères de fusée innovantes
Ces nouveaux lanceurs font face à de nouveau défis liés à leur architecture nouvelle.
Tout d’abord, le développement d’un moteur de lanceur orbital est un processus long et complexe nécessitant plusieurs itérations de conception, de fabrication, et d’essais en tir statique. Dans le cadre d’un fort contexte très compétitif dans le domaine des micro et mini-lanceurs, la capacité à itérer rapidement est devenue une nécessité technologique et commerciale.
Ensuite, la température élevée à l’intérieur d’une tuyère nécessite un refroidissement des parois au plus proche de la source de chaleur, afin d’éviter que cette dernière ne fonde. Ce refroidissement réalisé via des tubulures rapportées sur la tuyère, se complexifie lorsque cette dernière gagne en compacité pour satisfaire le besoin en propulsion de plus petits lanceurs.
Solution pour une tuyère imprimée en 3D
Les gaz en sortie de la chambre de combustion ont une température très élevée. Dans le cas des tuyères de moteurs-fusées, qui fonctionnent à de très hautes températures (environ 3 000 °C), un processus permettant de refroidir les parois de la tuyère doit être prévu, car aucun alliage n’est capable de résister à une contrainte thermique aussi
élevée. La tuyère intègre ici de façons monolithique toutes les fonctions de refroidissement nécessaires à son fonctionnement à haute température tout en préservant l’intégrité de celle-ci. Ainsi, les ergols stockés à basse température permettent d’obtenir de très bonne performance de refroidissement lors de la circulation dans la double peau de la tuyère, puis sont conservés et réinjectés dans la chambre de combustion afin d’y être brulés.
La pièce est imprimée sur une machine Addup utilisant la technologie de Fusion sur lit de poudre, la FormUp ® 350. Son système de paramètres ouverts et sa capacité à travailler avec plusieurs systèmes de dépose (racleur brosse, racleur silicone, racleur
métallique, rouleau), couplé à l’utilisation de poudre métallique fine ou moyenne, ainsi que le recyclage intégré de la poudre permettent de répondre aux problématiques de développement itératif des tuyères et autres pièces de moteurs de fusées de dernière génération.
Résultats et avantages de la fabrication additive
La fabrication additive métallique a permis de créer des canaux de refroidissement complexes et intégrés ; chose impossible avec les techniques classiques sur des moteurs de dimensions réduites. Une telle pièce, qui nécessite en temps normal des mois de travail avec des méthodes de soudage traditionnelles, n’aura pris que 49h à être produite. Les experts d’AddUp ont choisi d’utiliser l’Inconel® 718 pour imprimer cette nouvelle tuyère. Ce matériau est doté d’excellentes propriétés mécaniques et résiste à des températures très élevées.
Les concepteurs des moteurs de fusée peuvent à présent itérer plus rapidement dans le but d’améliorer la forme de la tuyère et profiter des nouvelles libertés de forme amenées par la fabrication additive, permettant une optimisation efficiente des performances des moteurs.
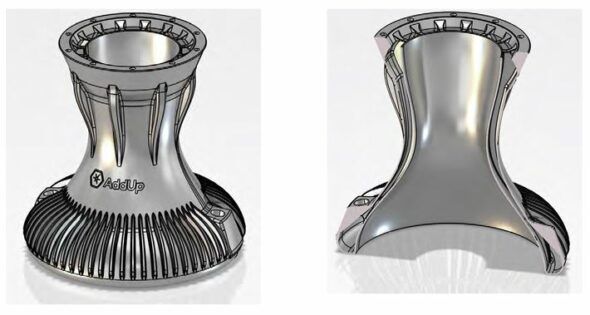
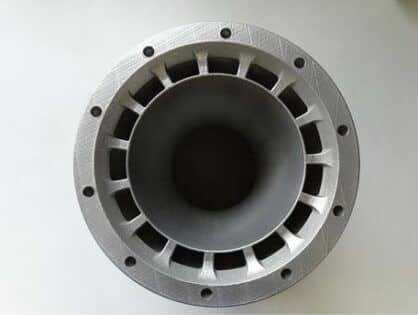