AddUp hat das Design einer Raketendüse optimiert, um die Leistung einer Mikro-Trägerrakete zu verbessern.
Die additive Fertigung von Metallen kann in der Luft- und Raumfahrt zu Treibstoff- und Produktionseinsparungen führen. In dieser Fallstudie sehen Sie, wie AddUp das Design einer Raketendüse optimiert hat, um die Leistung einer Mikro-Trägerrakete zu verbessern. Der 3D-Druck ist bereits die Zukunft der Luft- und Raumfahrtindustrie. Lesen Sie die Fallstudie über ein optimiertes Design einer 3D-gedruckten Raketendüse.
INDUSTRY
Aerospace
CHALLENGE
To print an innovative rocket nozzle to optimize engine performance in space
KEY BENEFITS
- Mass reduction
- Printed parts with complex geometries
- Resistance to high temperatures
Mass Reduction
Creative Shape
Function Integration
Performance
Geschichte: AddUp & Luft- und Raumfahrt
In der Luft- und Raumfahrtindustrie ermöglicht die neue Designfreiheit, die mit der additiven Fertigung einhergeht, leichtere Teile, was zu Treibstoffeinsparungen führt. Auch die Möglichkeit der individuellen Anpassung und das Fehlen von Werkzeugen werden in dieser Branche, in der die Produktionsmengen recht gering sind, als Vorteil angesehen. Luft- und Raumfahrtexperten sind der Meinung, dass die Leistungssteigerung und die geringeren Produktionskosten dazu führen werden, dass sich der 3D-Druck in dieser B r a n c h e als Fertigungsmethode durchsetzen wird.
Einer der wichtigsten Trends im Bereich des Raumtransports ist die Entwicklung kleinerer Trägerraketen, die Nutzlasten von weniger als 500 kg in die Umlaufbahn befördern können. Dies ist einer der vielversprechendsten Aspekte des neuen Weltraums: Mikro- und Mini-Trägerraketen bieten eine Flexibilität und Reaktionsfähigkeit, die sie zu einer ergänzenden Lösung zu herkömmlichen Trägerraketen machen.
Herausforderungen beim Druck innovativer Raketendüsen
Eine Düse ist eine Komponente einer Rakete, die für die Schuberzeugung verantwortlich ist. Heiße Abgase werden aus der Brennkammer durch eine engere Kontraktion beschleunigt und dann aus dem Ausgang expandiert. Bei diesem Vorgang wird die Energie der Verbrennungsgase in kinetische Energie umgewandelt.
Die vollständige Entwicklung eines Triebwerks für eine Orbitalrakete ist ein langwieriger und komplexer Prozess, der mehrere Iterationen von Entwurf, Fertigung und statischen Zündungstests erfordert. Dies stellt eine anspruchsvolle Aufgabe für die Projektleitung dar.
Da sich der Bereich der Mikro- und Mini-Trägerraketen zu einem derart wettbewerbsintensiven Umfeld entwickelt hat, ist eine schnelle Iteration sowohl eine technologische als auch eine kommerzielle Notwendigkeit.
In Anbetracht der technischen Herausforderungen: Die hohe Temperatur im Inneren einer Düse erfordert eine Kühlung der Wände so nahe wie möglich an der Wärmequelle, um ein Schmelzen der Komponenten zu vermeiden. Diese Kühlung erfolgt in der Regel über an der Düse angebrachte Rohre und wird komplexer, wenn die Düse kompakter ist, um den Antriebsanforderungen kleinerer Trägerraketen gerecht zu werden.
Lösung für eine 3D-gedruckte Raketendüse
In den Düsen von Raketentriebwerken erhitzen sich die Abgase auf etwa 3000 °C. Bei der Konstruktion der Düse war es wichtig zu bedenken, dass alle verfügbaren Legierungen b e i so hohen Temperaturen nicht standhalten würden.
Alle Kühlfunktionen wurden in die Düse integriert, so dass sie die heißen Gase leiten kann und dabei ihre Form und Leistung beibehält. Vor der Verbrennung dient der Treibstoff als Kühlmittel. Die Treibstoffe werden bei niedriger Temperatur gelagert und durch die internen Kanäle der Düse geleitet, bevor sie aufgefangen und zur Verbrennung in die Brennkammer eingeleitet werden.
Ergebnisse und Vorteile der additiven Fertigung
Das Teil wurde auf einer PBF-Maschine (Laser-Pulverbett-Fusion) gedruckt, der FormUp® 350 von AddUp. Dieses System mit offenen Parametern und einem integrierten Pulverrecyclingmodul fördert schnelle Iterationen und verkürzt die Zeit zwischen den Bauvorgängen, indem es die Vorbereitung der Baudatei schnell und einfach macht. Die verschiedenen Wiederbeschichtungssysteme (Rolle, Bürste und Silikonklinge) ermöglichen minimale Designeinschränkungen und eine große Auswahl an Metallpulvern. Diese Vorteile sind entscheidend für die Entwicklung von Düsen und anderen Raketenkomponenten.
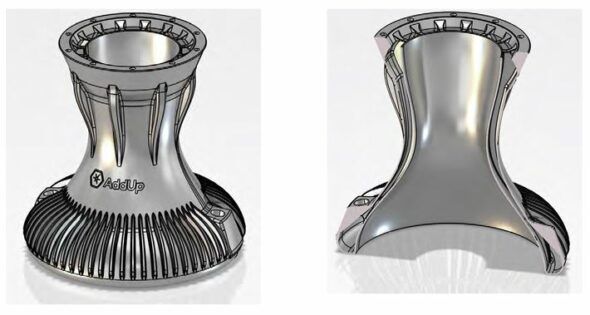
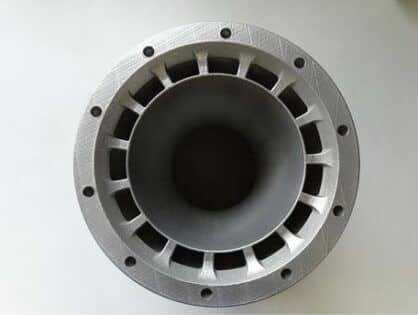
Die additive Fertigung von Metallen ermöglichte es, komplexe, integrierte Kühlkanäle zu schaffen; was mit herkömmlichen Techniken bei kleinen Motoren unmöglich ist. Die Herstellung dieser Düse, die normalerweise monatelange Arbeit mit herkömmlichen Schweißmethoden erfordert, dauerte nur 49 Stunden. Die Experten von AddUp haben sich beim Druck dieser neuen Düse für Inconel® 718 entschieden. Dieses Material hat hervorragende mechanische Eigenschaften und kann sehr hohen Temperaturen standhalten.
Die Konstrukteure von Raketentriebwerken können nun schneller die Düsenform verbessern und mehr Tests in einem kürzeren Zeitraum durchführen. Die Ingenieure können auch die neue Designfreiheit nutzen, die die additive Fertigung mit sich bringt, und so die Triebwerksleistung weiter optimieren.