Amélioration des points chauds des moules d’injection pour des capacités de refroidissement optimales avec la fabrication additive
INDUSTRY
Tooling & Molding
CHALLENGE
Improving injection mold hotspots for optimal cooling capabilities with additive manufacturing.
INCREASED PRODUCTIVITY
REDUCED MANUFACTURING TIME
CONFORMAL COOLING
L’histoire
En tant que leader allemand de la fabrication de modèles et de moules, Siebenwurst offre à ses clients bien plus qu’un bon moule. Elle associe la tradition à la haute technologie et propose des solutions complètes intelligentes et innovantes.
Depuis plus d’un siècle, Siebenwurst est synonyme de la plus haute qualité dans la fabrication de modèles et de moules. dans la fabrication de modèles et de moules et fournit des outils parfaits, du modèle de conception à la production en série. Les méthodes et technologies de fabrication modernes garantissent une production d’outils aussi rapide que possible. Les premières applications d’outillage AM ont été développées et évaluées avec AddUp au cours des deux dernières années.
Défi
La conception conventionnelle des systèmes de refroidissement atteint ses limites avec les pièces moulées critiques en raison de la complexité de la géométrie. Par conséquent, il est difficile, avec un refroidissement interne conventionnel, de refroidir suffisamment et uniformément toutes les sections du contour. Cela peut conduire à une distribution inhomogène de la température dans l’application et à l’apparition de points chauds dans la pièce.
Les points chauds sont un facteur critique dans la détermination du temps de cycle et de la qualité de la production, et doivent être évités pour obtenir de bons résultats. Si les moules sont insuffisamment tempérés et que l’on souhaite obtenir la même qualité, le temps de cycle augmente et le moule devient inévitablement moins productif.
La solution
La fusion en lit de poudre permet de nouvelles libertés de conception que l’usinage conventionnel ne pourrait jamais toucher. Les moules peuvent être construits avec des circuits de refroidissement parallèles qui suivent les contours de la surface du moule, quelle que soit la forme de la pièce finale. . Ce nouveau style de circuits de refroidissement est connu sous le nom de refroidissement conforme.
La conception du refroidissement conforme permet de réduire la section des canaux. En effet, plusieurs canaux peuvent se dérouler en parallèle de l’entrée à la sortie, ce qui permet de couvrir la surface du moule de manière homogène. Les canaux peuvent être facilement conçus pour s’adapter parfaitement aux zones complexes du moule. La durabilité et la fabricabilité des moules devraient être comparables à celles de la méthode conventionnelle, voire meilleures.
Bien que la production additive de l’outil lui-même soit parfois plus coûteuse que s’il était fabriqué par d’autres méthodes, ce coût supplémentaire sera récupéré dans la production de la pièce finale grâce à l’augmentation de la productivité et de la longévité de l’outil.
Processus
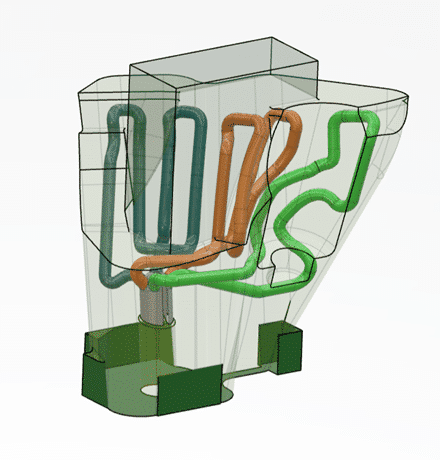
Afin d’exploiter au maximum les avantages de l’impression 3D, la vanne à glissière a dû être redessinée et le fichier CAO modifié . La nouvelle conception intègre un système de circuits de refroidissement équilibrés avec des canaux individuels disposés en parallèle. . Cette approche permet au liquide de refroidissement de s’écouler plus près des éléments à refroidir, quelle que soit leur forme. . Les taux de refroidissement seront plus rapides, mais aussi plus homogènes sur l’ensemble de la pièce parce que les canaux sont à une distance constante de ces caractéristiques. En d’autres termes, il n’y a plus de points chauds.
Le flux de travail de la fabrication additive nécessite également quelques ajustements du modèle CAO. Les références et les surfaces de serrage qui seront utilisées dans les processus d’usinage en aval doivent être incorporées dans le modèle. Ces caractéristiques peuvent devoir être ajustées lorsque la conception de la pièce change.
Production
Les inserts de tête de glissière sont imprimés avec la configuration de machine suivante :
- FormUp 350 avec 4 lasers
- Acier à outils 1.2709 / Maraging 18Ni300 (46-50HRC)
- Poudre fine (5-25µm)
- Technologie de rechargement des rouleaux
Différentes formes de glissières sont nécessaires pour un outil, toutes les 8 s’adaptent à une plate-forme de construction FormUp (350x350mm) avec de l’espace pour les spécimens d’essai. Ainsi, grâce à la grande plaque de construction et aux 4 lasers, tous les inserts peuvent être imprimés en un seul travail de production. La réalisation de toutes les pièces nécessaires en une seule fois permet de réaliser des économies considérables en termes de temps et de coûts liés à la mise en route de l’imprimante.
La technologie de revernissage à rouleaux permet d’utiliser une poudre fine qui s’agglomère lorsqu’elle est associée à un dispositif de revernissage à lames ou à raclettes plus courant. L’utilisation d’un rouleau est unique à AddUp.
Le revêtement au rouleau offre l’avantage d’obtenir les meilleures qualités de surface et de contour grâce à un meilleur compactage et à une distribution uniforme des différentes couches de poudre. Pour cette application, Siebenwurst a pu réduire considérablement ses processus de finition de surface, ce qui lui a permis de réaliser 42 % d’économies dans ce domaine.
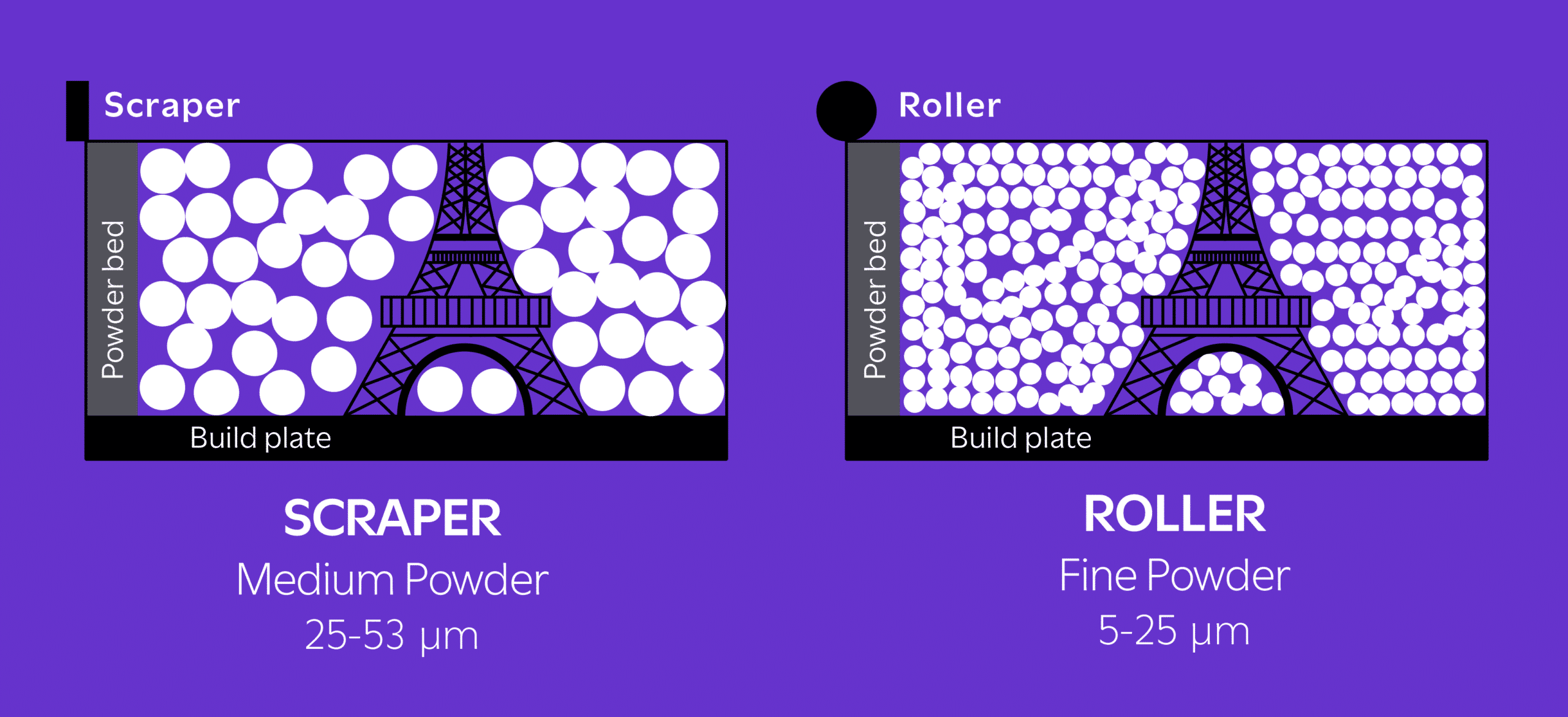
Pour cette pièce, la qualité du contour est un autre point important, l’objectif étant de réduire au minimum le post-traitement avec le moins d’écart géométrique possible.
La boîte de délimitation de la pièce est de 100x65x50 mm3 et l’écart maximal par rapport à la définition du contour est de 0,12 mm. Siebenwurst a réalisé la reprise complète des vannes et l’échantillonnage des pièces en plastique. Le dimensionnement et l’usinage de finition précédents ont parfaitement fonctionné et l’échantillonnage a pu être réalisé sans problème dans l’outil d’origine.
Les images suivantes montrent la surface générée et la précision du contour imprimé.
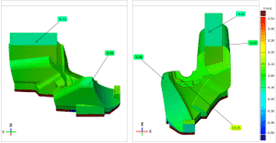
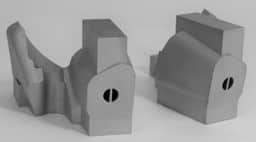
Results
Early trials show the maximum temperature recorded at the insert dropping by 16°C, a clear mark of improvement and a sign that the hot spot was eliminated in the new design. The printed part held to the expected geometric tolerance and allowed for a significant reduction in surface finishing expenses. As the study continues, cycle time and tool longevity will be studied as well.
The success of this project inspired further cooperation between AddUp and Siebenwurst in the near future, and has opened the doors for Siebenwurst to pursue more AM applications.
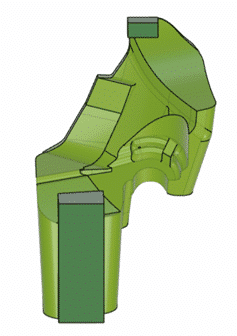
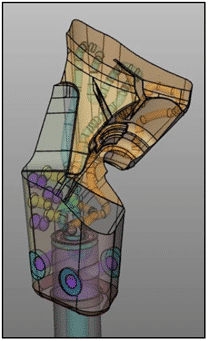
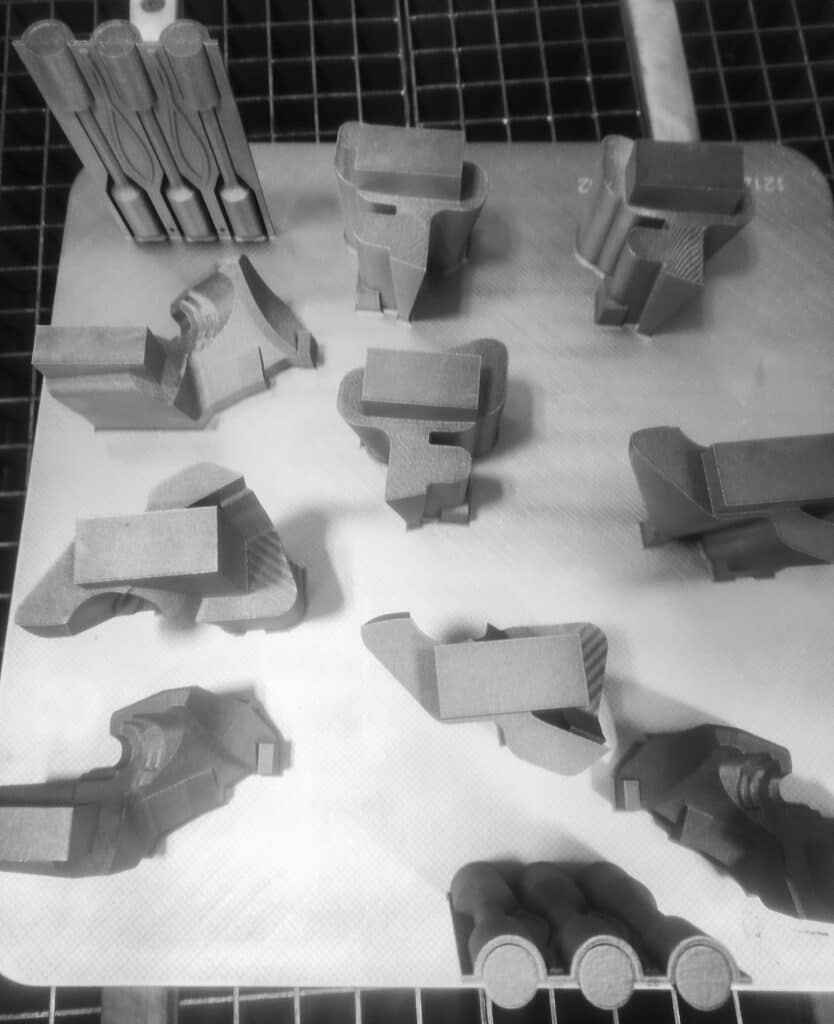
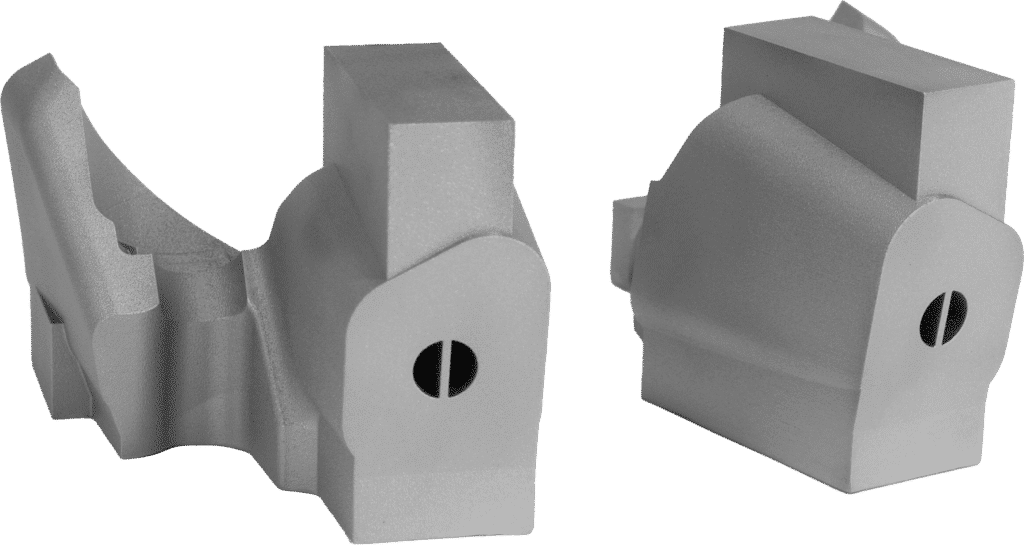
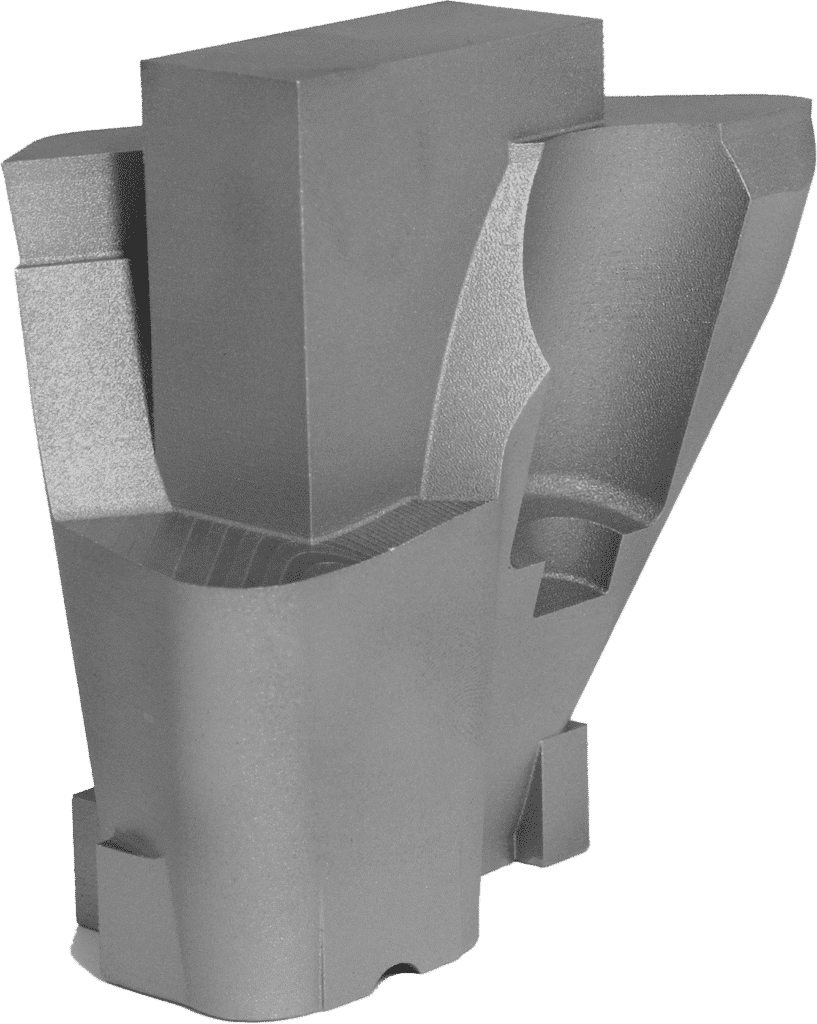
Reduction of the slide valve temperature from 62°C to 46°C
Elimination of temperature hotspot in slide gate area
Surface finishing cost reduction of 42%