Cette étude explore l’utilisation de la fabrication additive, en particulier la fusion sur lit de poudre (PBF), pour créer des filières d’extrusion avec des performances et des capacités de refroidissement améliorées.
Industrie
Outillage et moulage
CHALLENGE
Augmenter la longévité et les performances d’une filière d’extrusion tout en augmentat la flexibilité afin de pouvoir produire des filières et des produits finaux de différentes tailles grâce à la fabrication additive.
KEY BENEFITS
- Le taux d’extrusion du produit final a augmenté de 25%
- La température maximale est inférieure de 20° C sur la couvelle filiè grâce à l’optimization du refroidissement
- Performance d’usure x6 : 2 semaines → 12 semaines
Intégration de fonctions
Performance
Ajouter de la vie
HISTOIRE
L’extrusion est une méthode de fabrication très utilisée pour les pièces à profil constant. Les tuyaux en PVC et les balais d’essuie-glace sont quelques exemples de pièces dans le monde des plastiques, mais les métaux et les composites peuvent également être extrudés. La matière première est forcée à travers le profil de la filière pour lui donner la forme de la pièce finale.
Dans l’extrusion des matières plastiques, il est courant d’usiner la filière d’extrusion en aluminium. En raison des contraintes de liées à l’usinage traditionnel, la filière d’extrusion est souvent plus grande et plus encombrante que nécessaire et ne dispose pas de canaux de refroidissement avancés.
La géométrie simple de ces canaux entraîne de mauvaises performances de refroidissement, car le liquide de refroidissement ne peut souvent pas s’approcher du profil intérieur de la matrice, ce qui le rend beaucoup moins efficace. Il est également coûteux et fastidieux de créer des programmes, des gabarits et des montages différents pour des pièces de tailles différentes. Et la création de filières d’extrusion de tailles spécifiques serait trop coûteuse sans la flexibilité offerte par la fabrication additive.
DÉFI
La fabrication traditionnelle des filières d’extrusion est limitée aux matériaux faciles à usiner. Les restrictions liées à l’usinage traditionnel permet difficilement d’optimiser les performances de la filière, notamment en ce qui concerne les propriétés d’usure et la durée de vie de l’outil. Le défi consiste donc à utiliser la fabrication additive (FA) pour créer une filière fabriquée à partir d’un matériau améliorant la durabilité et augmentant la durée de vie en production. La matrice doit également permettre un refroidissement optimisé (conformal cooling) afin d’améliorer les performances thermiques. Enfin, le coût global de fabrication de la matrice doit être réduit favorisant les modifications de conception sur une variété de lignes de fabrication et de machines.
SOLUTION
La fusion sur lit de poudre (PBF) permet d’imprimer n’importe quel profil 2D, ce qui permet d’obtenir n’importe quelle forme pouvant être extrudée. Comme la technologie PBF ne nécessite pas d’outillage de réglage, elle offre une plus grande liberté dans la fabrication de multiples pièces de formes différentes, ce qui est parfait pour l’obtention de tailles spéciales et pour les nouvelles filières d’extrusion, et ceci sans investissement supplémentaire. Les filières d’extrusion peuvent également être fabriquées en minimisant le nombre de pièces assemblées, ce qui simplifie le processus de fabrication et réduit les coûts liés à la gestion des pièces de rechange. Le refroidissement optimisé (conformal cooling) constitue un autre avantage des possibilités géométriques de la FA. En effet, des canaux de refroidissement complexes, impossibles à usiner, sont implantés sur le contour de la pièce pendant l’impression. L’optimisation de ces canaux permet un contrôle uniforme de la température, ce qui améliore le refroidissement et par conséquent les performances. De plus, la pièce est imprimée en Inconel 718, un alliage à base de nickel très résistant à l’usure et à la corrosion et qui peut fonctionner à des températures élevées.
RÉSULTATS
La nouvelle filière d’extrusion créée par FA permet un gain de 20°C par rapport à une filière fabriquée selon les méthodes traditionnelles, grâce à la conception optimisée du refroidissement. La température plus basse a permis d’extruder le produit dans la filière 25 % plus rapidement, ce qui a entraîné une augmentation considérable de la productivité sans sacrifice sur la qualité. Sur le plan thermique, il est encore possible d’augmenter la vitesse d’extrusion, mais les autres équipements de la ligne constituent désormais le goulot d’étranglement et non plus la filière elle-même. La nouvelle filière a également vu sa durée de vie multipliée par 6 par rapport à la précédente, soit 12 semaines au lieu de 2, même en fonctionnant à une vitesse supérieure. La fusion en lit de poudre s’est donc révélée être un atout précieux, prêt à répondre à de nombreux défis de l’industrie de l’extrusion.
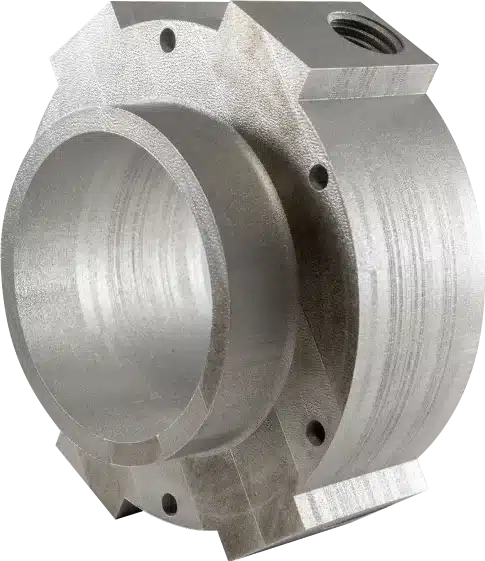
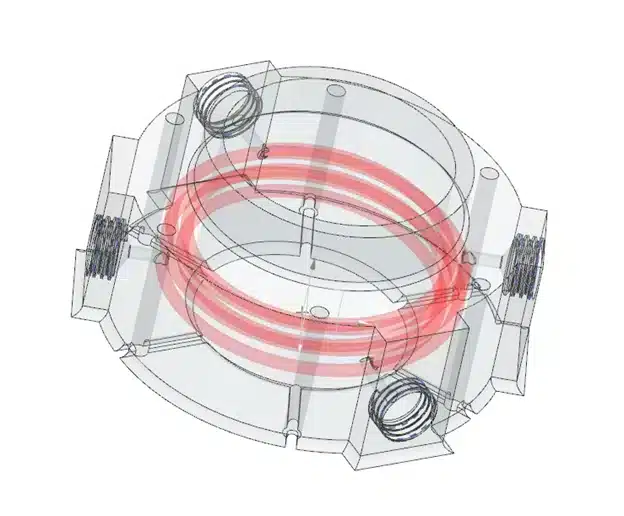