Die additive Fertigung von Metallen, insbesondere die Laser Powder Bed Fusion (L-PBF) Technologie, bietet neue Möglichkeiten für den Formen- und Werkzeugbau. Sie ermöglicht die Herstellung von Formen mit komplexen Geometrien, ineinandergreifenden Teilen und konformen Kühlkanälen, was zu höherer Produktivität, kürzeren Kühlzeiten und besserer Teilequalität führt.
Die Hersteller im Formen- und Werkzeugbau setzen den 3D-Druck inzwischen in großem Umfang ein. Sie verwenden den 3D-Kunststoffdruck für die Herstellung von Prototypen für Spritzguss- oder Wachsausschmelzformen, den 3D-Sanddruck für die Herstellung von Einsätzen oder die Stapelung mehrerer Formschichten zur Herstellung von Etagenwerkzeugen. Die additive Fertigung von Metall hingegen entwickelt sich weniger schnell. Die Laser-Powder-Bed-Fusion-Technologie (L-PBF) bietet jedoch mehrere interessante Vorteile für diese Branchen.
Neue Anwendungen auf dem Gebiet des Spritzgießens
Die PBF-Technologie bietet mehrere Möglichkeiten zur Verbesserung des Spritzgießprozesses. Erstens ermöglicht die Fähigkeit des L-PBF-Verfahrens, Teile mit komplexen Geometrien herzustellen, neue Formen in Betracht zu ziehen. Die Wände der Form, die mit dem Kunststoffteil in Berührung kommen, können an Komplexität gewinnen, sind aber aus zwei Gründen begrenzt: die Notwendigkeit, die Oberflächen mit Bearbeitungs- und Polierwerkzeugen zu bearbeiten, um ihre Rauheit zu verringern, und die Notwendigkeit, Entformungswinkel einzuhalten, da die Formen die Entformung des Teils ermöglichen müssen.
Dennoch gibt es immer noch Möglichkeiten, die es zu erforschen gilt. Da die L-PBF-Technologie die Herstellung von ineinandergreifenden Teilen ermöglicht, können sich Formenbauer neue Arten von Bewegungen in ihren Formen vorstellen, indem sie „Schubladen“ (bewegliche Teile) in Bereichen platzieren, die mit herkömmlichen Techniken nicht erreichbar waren. Auch die Zuverlässigkeit kann verbessert werden. Elemente, die durch Schweißen oder Schrauben zusammengefügt werden, sind in der Regel die Schwachstellen von Formen, die in großen Serien verwendet werden, und der 3D-Metalldruck bietet die Möglichkeit, sie in einem einzigen Arbeitsgang herzustellen und so ihre Lebensdauer zu verbessern.
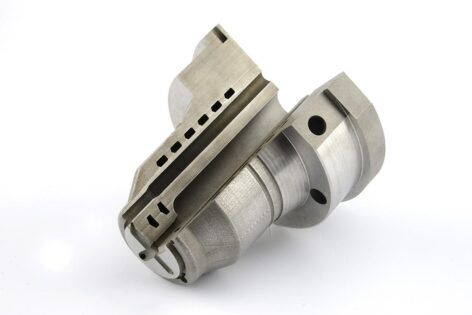
Hersteller, die den Einsatz der additiven Fertigung von Metallen zur Herstellung von Spritzgussformen in Erwägung ziehen, sollten bedenken, dass die PBF-Technologie aus Kostengründen, aber auch wegen der Anhäufung von Wärmespannungen nicht gut für die Herstellung massiver Teile geeignet ist. Sie sollte daher nicht für die Herstellung kompletter Formen eingesetzt werden, s o n d e r n n u r in Bereichen, in denen sie von Interesse ist.
Diese Einschränkung, die als Hemmnis für den Einsatz dieser Technologie in Formen erscheinen könnte, bietet interessante Perspektiven. Der Entwurf von Formen, bei denen das massive Teil Standard ist und der Bereich nahe der Formwand gedruckt wird, hat Vorteile. Zum einen besteht die Möglichkeit, einen schnelleren Serienwechsel durchzuführen, da die Vorlaufzeiten für die Beschaffung der Formen im Allgemeinen mehrere Monate betragen. Zweitens besteht die Möglichkeit, die Stillstandszeiten zu verringern, da die Lagerung der gedruckten Teile weniger aufwendig ist als die Lagerung der kompletten Formen. Und schließlich ist es die Aussicht auf eine Kleinserienproduktion, die in der Vergangenheit nicht rentabel gewesen wäre. die Investition in eine komplette Form. Oder, auf lange Sicht, zur Herstellung kundenspezifischer Produkte überzugehen, eine Welt, die derzeit für Kunststoffspritzteile schwer zugänglich ist.
Produktivitäts- und Qualitätssteigerung
Bevor man darüber nachdenkt, den 3D-Metalldruck für die Entwicklung neuer Produkte und Dienstleistungen zu nutzen, kann es sinnvoll sein, ihn zur Verbesserung des Bestehenden einzusetzen. Eine der wichtigsten Anwendungen der L-PBF-Technologie in der Welt des Spritzgießens ist eine Technik namens „konforme Kühlung“. Sie besteht darin, die Abkühlzeit von Kunststoffteilen in Spritzgießwerkzeugen zu optimieren, indem Kanäle geschaffen werden, die der Form des zu kühlenden Teils folgen. Diese Kanäle werden so nah wie möglich an der Formwand platziert und ermöglichen es, die Abkühlzeiten zu verkürzen und damit die Produktionsraten zu erhöhen. In einem Spritzgusszyklus ist die Abkühlung des Materials im Allgemeinen die längste Phase. Durch die Verkürzung dieser Zeit können die größten Produktivitätsgewinne erzielt werden. Auch das Aussehen der gespritzten Teile kann verbessert werden, da durch die Platzierung von Kanälen in Bereichen, die normalerweise schwer zu kühlen sind, Schrumpfungen oder Bindenähte vermieden werden können, die durch eine nicht optimale Kühlung verursacht werden.
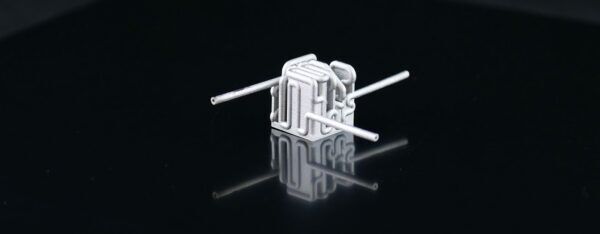
Spritzgussingenieure waren zwar schon immer in der Lage, komplexe Steuerkreise zu entwerfen, aber sie waren durch die Techniken des Formenbaus eingeschränkt. Lange Zeit waren die einzigen verfügbaren Techniken zur Herstellung von Rohren in einem Metallblock das Bohren, die maschinelle Bearbeitung und die Schichtung (die Form wird in separaten Schichten entworfen, von denen jede gefräst und gebohrt wird, so dass die Schichten miteinander verbunden werden, um drei-dimensionale Rohre). Mit den Techniken der additiven Fertigung durch Laserschmelzen auf dem Pulverbett h a b e n die Formenhersteller heute Zugang zu einer völligen Gestaltungsfreiheit für ihre Regulierungskanäle. Es ist anzumerken, dass die Oberflächenbeschaffenheit der durch Laserschmelzen auf dem Pulverbett hergestellten Teile besonders gut für d i e Schaffung von Kühlkanälen geeignet ist: glatt genug, um keine Turbulenzen in den Kanälen, aber rau genug, um die Austauschfläche im Vergleich zu gebohrten Kanälen zu vergrößern.
Ein weiterer Vorteil der konformen Kühlung besteht darin, dass das Gesamtvolumen des zu kühlenden Metalls reduziert wird, indem die Regelkanäle so nahe wie möglich am Formhohlraum platziert werden. Dadurch erreicht die Form schneller ihre Betriebstemperatur und verkürzt die Zeit vom Anfahren der Maschine bis zum ersten produzierten Gutteil, was zu Produktivitätssteigerungen und einer Minimierung der Anzahl fehlerhafter Teile führt.
Werkzeuge zur Produktionsunterstützung
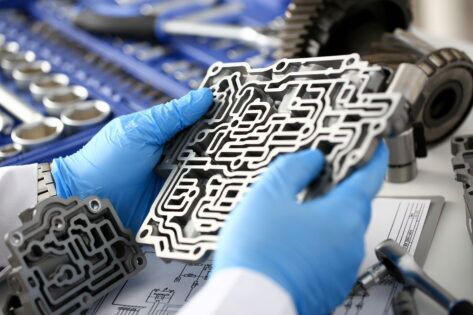
Was auch immer die Gründe für das Interesse eines Herstellers am 3D-Druck sind, es ist immer so, dass die aus einem Projekt gewonnenen Erfahrungen zu weiteren Ideen führen, manchmal in anderen Abteilungen des Unternehmens. Wenn wir über die an die Kunden verkauften Produkte und die zu ihrer Herstellung benötigten Formen hinausgehen und das Produktionswerkzeug betrachten, können wir erhebliche Gewinne erzielen. In jeder Produktionswerkstatt gibt es eine Vielzahl von Aufgaben, die dank maßgeschneiderter Werkzeuge vereinfacht, verbessert oder gesichert werden können.
Von Vorrichtungen, die die Montage erleichtern, über leichte Handwerkzeuge mit Griffen, die an die Hand des jeweiligen Bedieners angepasst sind, bis hin zu kodierten Werkzeugen, die Fehler bei der Montage vermeiden… Die additive Fertigung bietet viele Möglichkeiten, die Produktionszeiten zu verkürzen, die Produktqualität zu verbessern oder das Risiko von Muskel-Skelett-Erkrankungen zu verringern.
Das Gleiche gilt für Hersteller, die Roboter einsetzen oder automatisierte Montagelinien betreiben: Wenn ein bewegliches Teil leichter gemacht werden kann, führt dies zu weniger Vibrationen, weniger Verschleiß, geringerem Energieverbrauch und kürzeren Produktionszeiten. Die additive Fertigung bietet Antworten auf diese Leichtbauanwendungen, indem sie Aussparungen in Volumina schafft, Leichtbaustrukturen (Gitterstrukturen) erzeugt oder die topologische Optimierung nutzt.
Um all diese „indirekten“ Anwendungen der additiven Fertigung zu entwickeln und sie für die Herstellung von „Werkzeugen“ im weitesten Sinne des Wortes zu nutzen, ist es eine gute Praxis, alle Bediener und Techniker zu ermutigen, die Kultur der additiven Fertigung im Unternehmen zu teilen, nicht nur in den Konstruktionsbüros, so dass alle Mitarbeiter in der Lage sind, Ideen zur Verbesserung des Produktionswerkzeugs vorzuschlagen.
Schlussfolgerung
Die Anwendungen der additiven Fertigung von Metallen im Bereich der Werkzeugherstellung dürften sich in den kommenden Jahren weiter entwickeln, zumal täglich Fortschritte bei der Produktivität, der Prozesssteuerung und der Entwicklung von Rezepten für Metalle erzielt werden, die traditionell von den Herstellern in diesem Sektor verwendet werden. Diese Anwendungen werden sehr vielfältig sein, da sie die Industrialisierungszeiten, die Qualität der Teile, die Produktionsraten, das Anlagevermögen und die für die Kunden erbrachten Dienstleistungen betreffen können.
WERKZEUGBAU & EINSPRITZUNG