Additive Fertigung in der medizinischen Industrie
AM ermöglicht die Herstellung hochkomplexer und individueller Designs, die genau auf die Anatomie des Patienten abgestimmt sind und eine optimale Passform und Funktion gewährleisten. AM ermöglicht auch die geometrische Komplexität, die notwendig ist, um Gitterstrukturen zu schaffen, die nicht nur zur Gewichtsreduzierung, sondern auch zur Schaffung einer porösen Oberfläche erforderlich sind, die die Knochenintegration im menschlichen Körper verbessert. Diese Vorteile der AM verbessern die Ergebnisse für den Patienten und verringern die Notwendigkeit zusätzlicher Operationen oder Modifikationen.
Beherrschung des Prozesses. Perfektion nachbilden
Die Industrialisierung von AM, die eine Serienproduktion ermöglicht, erfordert eine wiederholbare und zuverlässige Plattform. Die FormUp 350 Powder Bed Fusion (PBF) Maschine von AddUp wurde für Produktivität gebaut. Unser 4-Laser-System reduziert die Fusionszeiten um bis zu 75 % im Vergleich zu einem einzelnen Lasersystem und bietet einen maximalen Durchsatz, um den Anforderungen des Marktes für medizinische Geräte gerecht zu werden. Dies führt zu einer höheren Effizienz der Betriebsanlagen (OEE) und insgesamt niedrigeren Gesamtbetriebskosten (TCO).
Der FormUp 350 bietet eine enorme Flexibilität in Bezug auf die Verwendung von Pulver. Er kann mit dem marktüblichen mittleren Pulver verwendet werden, ist aber auch in der Lage, ein feineres Pulver zu verarbeiten. Dank unserer Roller-Recoater-Technologie ist eine glatte Oberfläche mit feinen Merkmalen und Gitterauflösung direkt im Druck möglich. Das AddUp FormUp 350 bietet die Freiheit, Implantate mit geometrischer Komplexität und minimalen Stützstrukturen zu entwerfen, wodurch die Notwendigkeit einer umfangreichen Nachbearbeitung reduziert wird.
Wir verstehen die Bedürfnisse der Hersteller von Medizinprodukten und sind ein zuverlässiger Partner auf dem Weg zur Einführung von AM. Unsere Experten arbeiten mit Ihnen zusammen, um Ihre Anwendung zu entwickeln, und wir verfügen über das Wissen und die Erfahrung, um Ihnen zu helfen, die Zeit bis zur Markteinführung zu verkürzen. Gleichzeitig bieten wir einen Validierungspfad mit IQ-, OQ- und PQ-Prozessen sowie Richtlinien zur Wiederverwendung von Pulver.
Maximaler Durchsatz
Die FormUp 350 verdoppelt die Leistung von Einzellasersystemen um mehr als das Doppelte und erfüllt damit die Anforderungen der medizinischen Industrie bei gleichzeitiger Kostensenkung für die Hersteller von Medizinprodukten.
Hervorragende Oberflächenbeschaffenheit
Erzielen Sie dank unserer Walzenauftragstechnologie eine glatte Oberfläche mit feinen Merkmalen und gitterförmiger Auflösung wie beim Druck.
Reduzierte Stützen
Entwerfen Sie mit Komplexität, Freiheit und minimalen Stützen. Reduzieren Sie die Nachbearbeitungsanforderungen drastisch und sparen Sie Materialkosten.
Ein Partner, dem Sie vertrauen können
Erfahrung und Validierungspfad mit IQ-, OQ- und PQ-Prozessen sowie beschleunigte Qualifizierung dank der zertifizierten Einrichtungen von AddUp.
Offene Maschinenparameter
Einige Konkurrenten halten die Funktionsweise ihrer Maschinen geheim, aber wir nicht. Mit unserer offenen Plattform können Sie mehr erreichen, indem Sie an den Knöpfen drehen und wenden, wie Sie es für richtig halten.
Qualitätssicherung
Die prozessbegleitende Überwachung gibt unseren Anwendern Sicherheit und Qualitätssicherung in Echtzeit und sorgt für Vertrauen in die Qualität der Teile, sowohl bei der Herstellung als auch bei der Weiterverarbeitung.
„Die FormUp350 ist eine der wenigen Maschinen auf dem Markt, die sowohl den typischen LPBF-Pulverschnitt als auch einen viel feineren Pulverschnitt ausführen kann. Das gibt uns die Flexibilität, bestimmte anspruchsvolle Anwendungen zu erfüllen, auf die wir in Zukunft stoßen könnten.“
Rachel Levine
Schlüsselanwendungen in der medizinischen Industrie
AM kann die Wirksamkeit von Ersatzoperationen verbessern, da additiv hergestellte Implantate leichter und stabiler sind und eine bessere Osteointegration aufweisen. Dies bedeutet, dass die Implantate eine längere Lebensdauer haben und das Risiko von Defekten oder Implantatkomplikationen geringer ist, so dass sie dem Patienten ein besseres Ergebnis und eine höhere Lebensqualität bieten.
Der FormUp 350 wird derzeit von AddUp-Kunden auf der ganzen Welt eingesetzt, um jedes Jahr Hunderte von zertifizierten orthopädischen Implantaten herzustellen. AddUp hat umfangreiche Erfahrung mit großen orthopädischen Implantaten, einschließlich Hüftpfannen, Tibiaknieimplantaten und Schulterimplantaten. Wir haben auch Erfahrung mit einer Vielzahl von Wirbelsäulenimplantaten sowie mit patientenspezifischen (maßgeschneiderten) Implantaten. Das FormUp 350 bietet eine größere Produktdifferenzierung und fortschrittliche Designmerkmale dank unserer Walzenauftragstechnologie, die feine Merkmale und eine gitterartige Auflösung ermöglicht.
Pfannen für Hüftgelenke
Diese Implantate werden bei einer Hüftgelenkersatzoperation eingesetzt, die am häufigsten zur Behandlung von Arthritis, Osteoarthritis und rheumatoider Arthritis benötigt wird. Mit der FormUp 350 von AddUp können 34 Hüftimplantate in nur 12 Stunden hergestellt werden, dank einer 350 mm großen quadratischen Bauplatte und 4-Laser-Funktionen. Diese Implantate werden ohne Stützstrukturen auf der Unterseite hergestellt, wodurch sich der Nachbearbeitungsaufwand und der Materialverbrauch drastisch verringern.
Tibiaplateu für das Knie
Die Tibiaplatte ist ein wichtiger Teil des Implantats, das für eine Kniegelenkersatzoperation benötigt wird. Bei der additiven Fertigung sorgt diese Komponente des Implantats für eine verbesserte Osseointegration, was zu besseren Ergebnissen für den Patienten nach der Operation führt. Mit dem FormUp 350 können 22 Tibiaplatten in nur 17 Stunden hergestellt werden. Diese Implantate werden mit minimalen Stützen gedruckt, wodurch sich der Nachbearbeitungsaufwand erheblich verringert und die Gesamtkosten für den Gerätehersteller sinken.
Schulter-Implantate
Schulterimplantate sind ein entscheidender Faktor für den Erhalt der Schulterfunktion. Das Schultergelenk eines jeden Patienten weist einzigartige Merkmale auf, und die Möglichkeit der individuellen Anpassung von Implantaten ist ein wesentlicher Vorteil der AM. AM ermöglicht die individuelle Anpassung dieser Implantate an die Anatomie des einzelnen Patienten, wobei komplizierte interne Strukturen und poröse Oberflächen für eine bessere Integration mit dem umgebenden Knochen berücksichtigt werden.
Wirbelsäulenimplantate
Bei der Wirbelsäulenversteifung werden zwei oder mehr Wirbel mit Hilfe von Knochentransplantaten in einem Titanimplantat zusammengefügt. Mit diesem Eingriff können Erkrankungen wie degenerative Bandscheibenerkrankungen, Skoliose, Wirbelgleiten und Frakturen behandelt werden. AddUp verfügt über umfangreiche Erfahrung in der Herstellung von Wirbelsäulenimplantaten unterschiedlicher Größe mit einzigartigen abbrechbaren Stützstrukturen. In Verbindung mit der Produktivität, die mit dem FormUp 350 erreicht werden kann, führt dies zu einer Kostenreduzierung für Hersteller von Medizinprodukten. Mit dem FormUp 350 können 152 große Wirbelsäulenimplantate in nur 32 Stunden gedruckt werden.
Patientenspezifische Implantate
Patientenspezifische Implantate (PSI) sind Implantate, die aus den CT-Scandaten eines Patienten in eine CAD-Datei übertragen und dann additiv hergestellt werden. PSI sind in der Regel zu komplex, um sie maschinell zu bearbeiten und zu schneiden, daher werden sie idealerweise durch AM hergestellt. AddUp hat Erfahrung in der Herstellung von patientenspezifischen Knöcheln, Schultern und Wirbelsäulenfusionsgeräten. Die FormUp 350 verfügt über eine große Bauplatte, die es ermöglicht, viele verschiedene Implantate in unterschiedlichen Formen und Größen auf demselben Bauplatz zu drucken. Die Möglichkeit, mehrere individuelle chirurgische Fälle auf einer einzigen Bauplatte herzustellen, rationalisiert den Prozess vom Herstellungsort bis zum Krankenhaus. Auf diese Weise kann jedem Patienten ein vollständig maßgeschneidertes Implantat zur Verfügung gestellt werden, das seinen individuellen Bedürfnissen entspricht und gleichzeitig die Operationskosten und Genesungszeiten reduziert.
Luft- und Raumfahrt & Aeronautik
Cassegrain-Antenne
Flugfertige Antenne im Pulverbettverfahren Thales Alenia Space ist ein französischer Luft- und Raumfahrthersteller, der seit mehr als 40 Jahren eine bedeutende Rolle in der Weltraumforschung spielt. Da neue Technologien eine […]
Michelin Tires Sipes
Entdecken Sie, wie Michelin über eine Million Reifenlamellenformen pro Jahr für seine Produktionsformen mithilfe des 3D-Metalldrucks herstellt
3D-gedruckte Raketendüsen
AddUp hat das Design einer Raketendüse optimiert, um die Leistung einer Mikro-Trägerrakete zu verbessern.
Wirbelsäulenimplantate
Diese Fallstudie befasst sich mit Wirbelsäulenimplantaten und den Herausforderungen, die sich bei ihrem Herstellungsprozess heute stellen. Die additive Fertigung (AM) bietet Vorteile wie Gitterdesign und Oberflächenrauhigkeit, die zu besseren Patientenergebnissen führen.
Luft- und Raumfahrt
Isogrid Fallstudie
This case study presents the development of an optimized heat exchanger for the Form Up® 350 machine,. The goal was to improve heat dissipation and adapt the dimensions for easy installation.
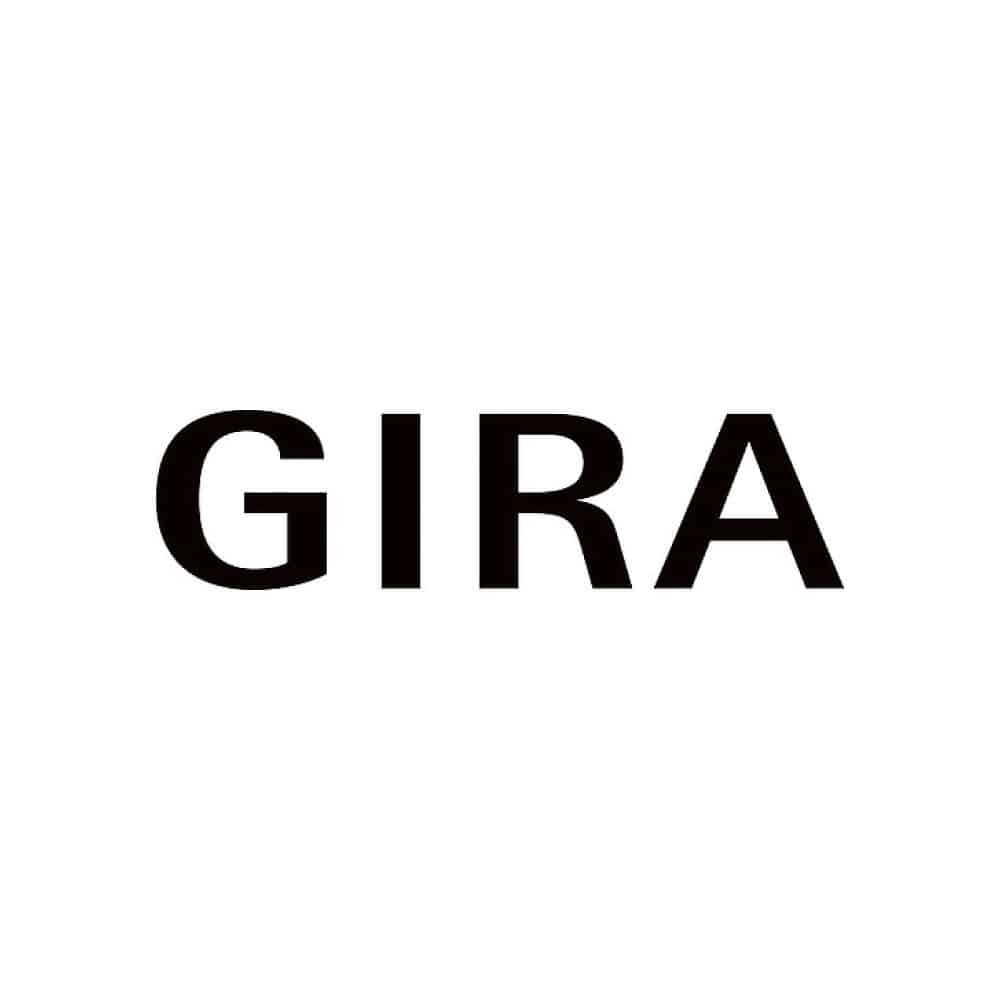
Werkzeuge und Gussformen
Gira Fallstudie
Kombination von traditioneller und additiver Fertigung – Hinzufügen von Merkmalen mit gerichteter Energieabscheidung
Automobilindustrie
Multi-Metall-, Multi-Technologie-Kolbenkopf
In dieser Fallstudie wird die Entwicklung eines optimierten Wärmetauschers für die Form Up® 350-Maschine vorgestellt. Ziel war es, die Wärmeableitung zu verbessern und die Abmessungen für eine einfache Installation anzupassen.
FormUp Wärmetauscher
In dieser Fallstudie wird die Entwicklung eines optimierten Wärmetauschers für die Maschine Form Up® 350 vorgestellt. Ziel war es, die Wärmeableitung zu verbessern und die Abmessungen für eine einfache Installation anzupassen.
In der medizinischen Industrie verwendete Materialien
Typische Materialien, die für orthopädische Implantate verwendet werden, müssen leicht, haltbar und sehr biokompatibel sein. Die bei der Herstellung von chirurgischen Instrumenten verwendeten Materialien müssen haltbar und kostengünstig sein und eine lange Lebensdauer haben.
Titan Ti64ELI
Titan Ti64ELI wird aufgrund seiner Eigenschaften am häufigsten für orthopädische Implantate verwendet. Es ist ein starkes, leichtes Material, das sehr biokompatibel ist. AddUp hat die Parameter für dieses Material sowohl für 30- als auch für 60-Mikrometer-Schichten optimiert.
Rostfreier Stahl 316L
Edelstahl 316L ist ein chirurgischer Stahl und kann für die Herstellung kostengünstiger chirurgischer Instrumente verwendet werden.
Rostfreier Stahl 17-4 PH
Edelstahl 17-4 PH ist auch ein gutes Material für die Herstellung chirurgischer Instrumente. Er ist nicht nur kosteneffizient, sondern hat auch eine außergewöhnliche Festigkeit.
Industrielle Maschinen
Mit mehr als 20 Jahren Erfahrung im Bereich der additiven Fertigung wurden unsere Maschinen so konzipiert, dass sie Details meistern und die Produktivität optimieren.
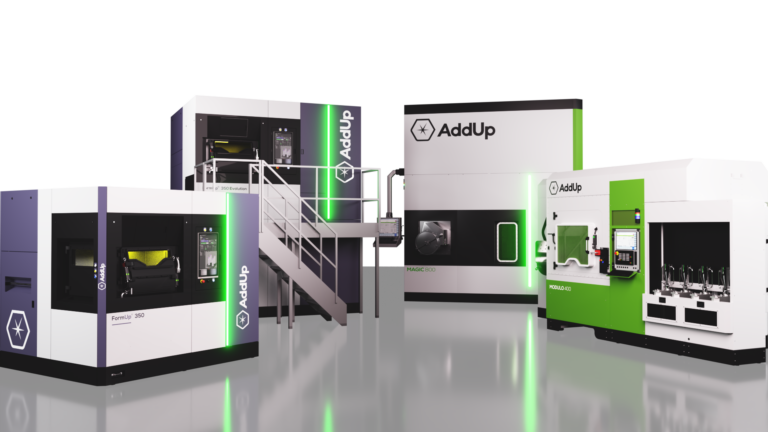
Intelligente Software
In der medizinischen Industrie ist die Qualifizierung und Regulierung von Implantaten und Geräten obligatorisch. AddUp ist führend bei der prozessbegleitenden Überwachung und bietet eine zuverlässige Teilequalität mit einer vollständigen Suite von Qualitätssicherungssoftware, um die Notwendigkeit strenger Tests nach dem Drucken eines Teils zu verringern oder sogar zu eliminieren. Von der Teilevorbereitung über die Simulation und Überwachung bis hin zur Produktion bietet jedes Glied der digitalen Kette von AddUp ein hohes Leistungsniveau mit benutzerfreundlicher Software.
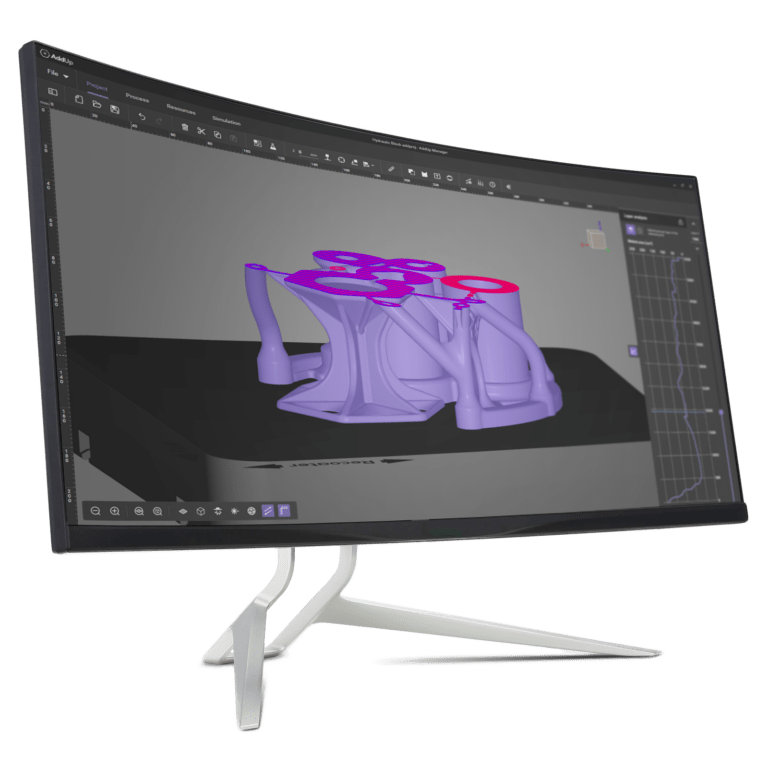
Starten Sie mit AddUp
Erkennen Sie das Potenzial der digitalen Fertigung. Starten Sie mit AddUp und erfahren Sie, wie AM innovative Lösungen für die schwierigsten Herausforderungen der Hersteller liefert.
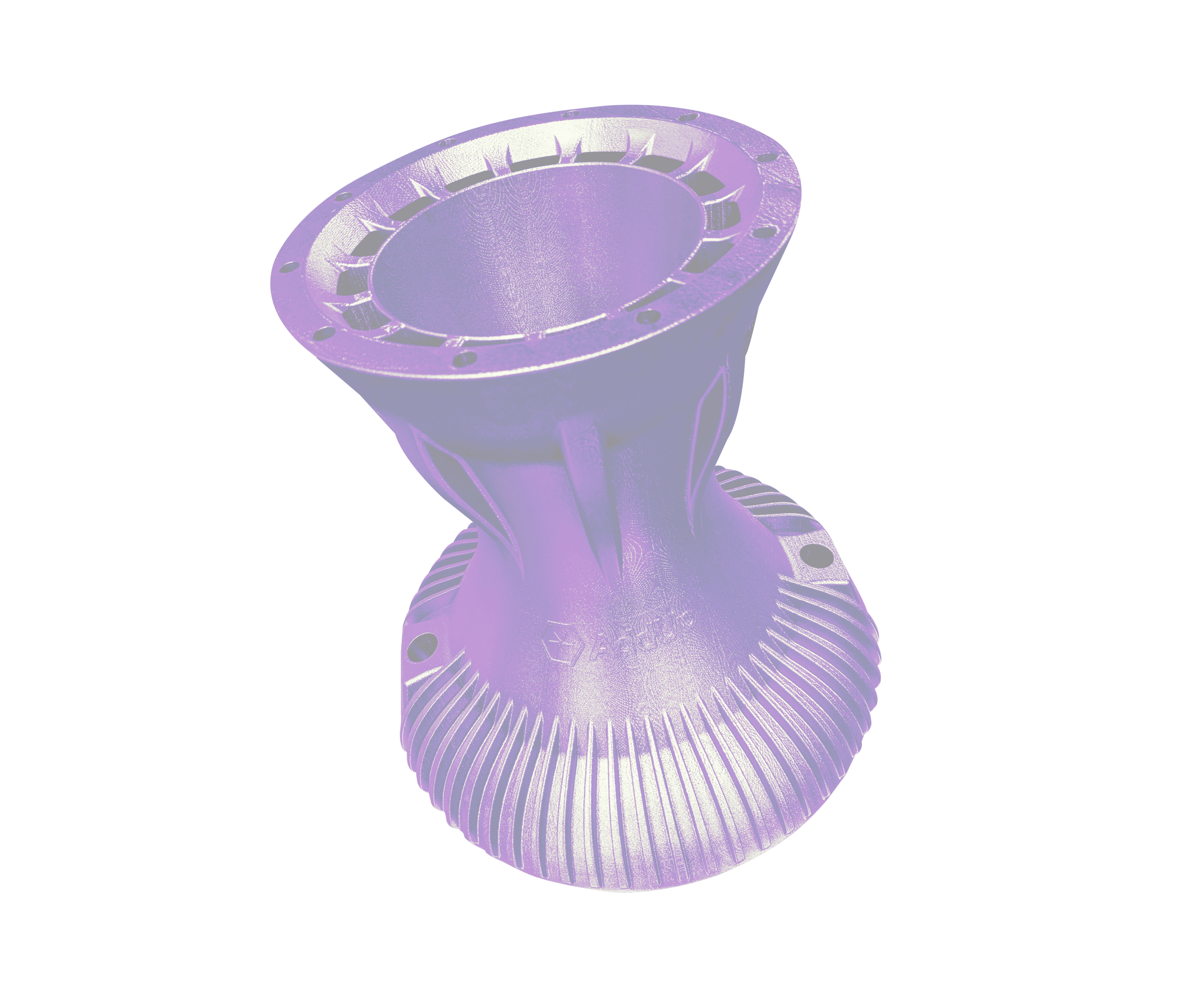