Diese Fallstudie befasst sich mit Wirbelsäulenimplantaten und den Herausforderungen, die sich bei ihrem Herstellungsprozess heute stellen. Die additive Fertigung (AM) bietet Vorteile wie Gitterdesign und Oberflächenrauhigkeit, die zu besseren Patientenergebnissen führen.
INDUSTRY
Medical
CHALLENGE
Significantly reduce production costs when additively manufacturing large spinal implants using a multi laser system and a larger build plate
KEY BENEFITS
- Cut production costs by up to 30%
- Increase the output by 2.61 parts per hour
- Fine feature resolution and optimal osseointegration
- Reduced post-processing
- Lower total part cost
Integrated Features
Reduced Lead Time
No Support
Performance
Geschichte
Große Wirbelsäulenimplantate werden üblicherweise auf kleinformatigen Maschinen im Pulverbettverfahren (Powder Bed Fusion, PBF) gedruckt oder aus Polyetheretherketon (PEEK)-Stangenmaterial gefräst. Bei der additiven Fertigung werden diese größeren Wirbelsäulenimplantate in der Regel auf kleinformatigen Maschinen mit einer kleinen Bauplatte und nur 1-2 Lasern gedruckt. Außerdem werden sie in der Regel mit der Vorderseite nach oben in Z gedruckt. Diese Ausrichtung in Kombination mit dem mehrstufigen Prozess führt zu einem Worst-Case-Szenario. Der Preis steigt, da der Großteil der Kosten durch den Produktionsprozess selbst verursacht wird. Obwohl die Kosten hoch sind, werden die Vorteile der großen Wirbelsäulenimplantate aus der additiven Fertigung (AM) durch das Gitterdesign und die Oberflächenrauheit realisiert, die eine Osseointegration ermöglichen, die zu besseren Patientenergebnissen führt. Ein weiterer Vorteil von AM-Wirbelsäulenimplantaten ergibt sich aus dem Material. AM ermöglicht den Druck von Titan mit höherer Bruchzähigkeit und höherer Zugfestigkeit. Bei der Herstellung von PEEK-Implantaten fehlen diesen Implantaten die idealen osseointegrativen Eigenschaften. In Verbindung mit einer instabilen Materiallieferkette führt dies zu Problemen bei der Herstellung großer Wirbelsäulenfusionsimplantate aus PEEK. Aus diesen Gründen wird häufig die additive Fertigung dieser Implantate bevorzugt.
Herausforderungen
Obwohl AM eine bessere Osseointegration, höherfeste Materialien und bessere Patientenergebnisse bietet, erhöht die Herstellung von LLIF-Implantaten auf kleineren Plattformen mit 1-2 Lasern die Kosten des fertigen Implantats. Diese Implantate sind hoch in Z, was zu einer längeren Bauzeit führt, die s i c h mit einer geringen Anzahl von Lasern noch weiter erhöht. Bei der Verwendung eines Scraper/Brush-Recoating-Verfahrens muss die Unterseite der Frontzahnfläche in der Regel durch abbrechbare Stützen abgestützt werden. Die LLIFs müssen außerdem durch D r a h t e r o d i e r e n (EDM) von der Bauplatte entfernt werden. Beide Verfahren werden dem Kunden in Rechnung gestellt, da sie mit der geringen Baukapazität, der geringen Anzahl von Lasern und den herkömmlichen Wiederbeschichtungssystemen zusammenhängen.
Lösung
Der Einsatz der FormUp 350 PBF-Maschine verkürzt die Produktionszeit und erhöht den Ausstoß um 2,61 Teile pro Stunde im Vergleich zu kleineren Plattformen mit 1-2 Lasern. Dies ist einer 350 Millimeter großen quadratischen Bauplatte zu verdanken, die im Vergleich zu kleineren Plattformen die 1,5-fache Menge an großen Wirbelsäulenimplantaten aufnehmen kann (152 Teile im Vergleich zu 96 Teilen). Durch den Einsatz von 4 Lasern können 152 große Wirbelsäulenimplantate in nur 32 Stunden gedruckt werden.
Die FormUp 350 verwendet eine Pulverwalzen-Technologie, die geometrische Komplexität mit minimalen Stützen ermöglicht und zu einer optimalen Oberflächengüte führt. Mit der FormUp 350 lassen s i c h komplexe Strukturen und Oberflächenrauhigkeiten realisieren, die zu besseren Patientenergebnissen beitragen. Es besteht keine Notwendigkeit mehr für eine trabekuläre Oberfläche auf Basis eines plasmaporösen Sprays oder einer Platte, und die Oberflächenrauhigkeit ist kein Nebenprodukt des Prozesses. Dies trägt zur Verringerung der
Fertigungsprozesse bei, die zur Herstellung eines fertigen Produkts erforderlich sind. Die Teile kommen näher an der Nettoform aus dem Drucker und erfordern weniger manuelle Bearbeitung und/oder Entfernung von Stützen. Diese Kombination aus einem 4-Laser-Bauvolumen von 350 mm3 und einem endkonturnahen Teil direkt aus dem Drucker vereinfacht die Fertigungsschritte. Die Reduzierung der Prozesse trägt zu einer besseren Designumsetzung, kürzeren Vorlaufzeiten und somit zu niedrigeren Teilekosten bei. Dies trägt zur Kostensenkung in allen Teilen der Lieferkette bei und unterstützt effizientere Patientenergebnisse.
Ergebnisse
Große Wirbelsäulenimplantate, die mit einer kleinen Baukapazität, einer geringen Anzahl von Lasern und herkömmlichen Wiederbeschichtungssystemen hergestellt werden, kosten mehr als solche, die mit der FormUp 350 hergestellt werden.
Die FormUp 350 Maschine ist ideal für medizinische Anwendungen, da sie ein verbessertes und kosteneffizientes Verfahren für die Massenproduktion von hochkomplexen und/oder kundenspezifischen medizinischen Teilen bietet.
Erfahren Sie mehr über FormUp 350 für medizinische Teile:
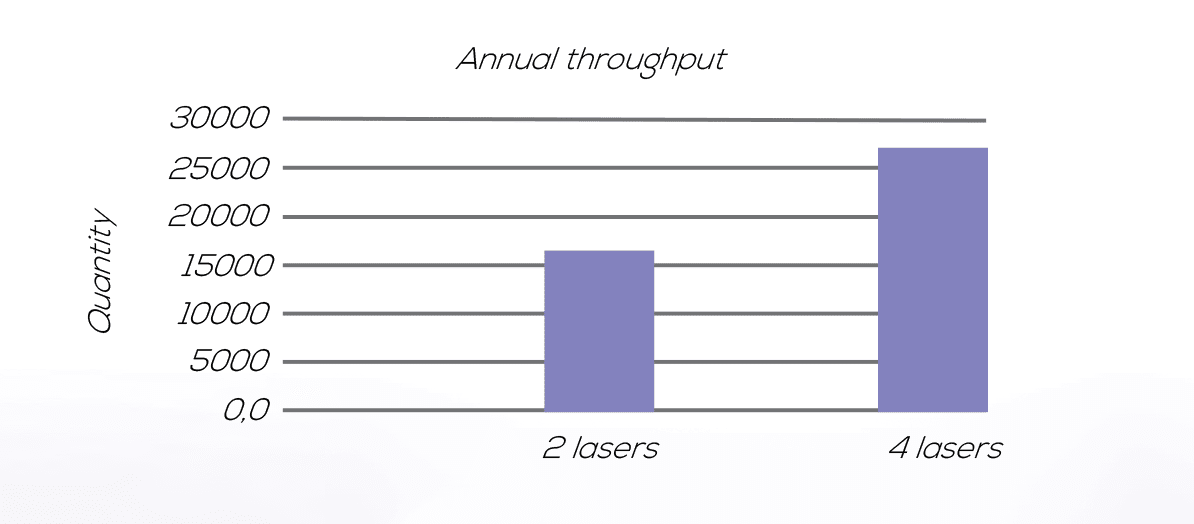
- Teile, die per Laser auf dem FormUp 350
- 2 Laser gebaut werden – 76
- 4 Laser – 38
- Zeit, auf den FormUp 350 2 Laser
- zu bauen – 52.95
- 4 Laser – 32,35
- Jahresdurchsatz auf dem FormUp 350
- 1 Schicht pro Tag für 52 Wochen pro Jahr 1 –
- 1,5 von Laser aus bis Laser an (build flip)
POWDER | 2 Lasers | 4 Lasers |
---|---|---|
Medium, 30μm powder (hrs) | 52.95 | 32.35 |
Annual throughput | 16.845 | 27.408 |