Verbesserung der Hotspots von Spritzgießwerkzeugen für optimale Kühlung mit additiver Fertigung
INDUSTRY
Tooling & Molding
CHALLENGE
Improving injection mold hotspots for optimal cooling capabilities with additive manufacturing.
INCREASED PRODUCTIVITY
REDUCED MANUFACTURING TIME
CONFORMAL COOLING
Geschichte
Als führender deutscher Modell- und Formenbauer bietet Siebenwurst für Ihre Kunden mehr als nur eine gute Form. Sie verbinden Tradition mit Hightech und bieten intelligente und innovative Komplettlösungen.
Siebenwurst steht seit über einem Jahrhundert für höchste Qualität im Modell- und Formenbau und liefert vom Designmodell bis in die Serienproduktion perfekte Werkzeuge. Modernen Methoden und Fertigungstechnologien garantieren schnellste Werkzeuganfertigungen. Erste AM-Tooling Anwendungen wurden in den letzten zwei Jahren mit AddUp entwickelt und ausgewertet.
Herausforderung
Die konventionelle Auslegung von Kühlsystemen stößt bei kritischen Formteilen aufgrund der Komplexität der Geometrie an ihre Grenzen. Deshalb ist es mit einer konventionellen Innenkühlung schwierig, alle Konturenabschnitte ausreichend und gleichmäßig zu kühlen. Dies kann zu einer inhomogenen Temperaturverteilung in der Anwendung führen und es können Hot-Spots im Bauteil entstehen.
Hot-Spots sind entscheidend für die Zykluszeit und die Qualität in der Produktion und müssen für gute Ergebnisse vermieden werden. Bei unzureichend temperierten Formen und gewünscht gleicher Qualität, steigt die Zykluszeit und das Werkzeug wird unweigerlich unproduktiver.
Lösung
Das Pulverbettschmelzen ermöglicht neue Gestaltungsfreiheiten, an die die konventionelle Bearbeitung nicht heranreicht. Formen können mit parallelen Kühlkreisläufen gebaut werden, die den Konturen der Formoberfläche folgen, unabhängig von der Form des fertigen Teils. Diese neue Art von Kühlkreisläufen wird als Conformal Cooling bezeichnet.
Die konforme Kühlung ermöglicht es, die Querschnitte der Kanäle zu reduzieren. Dies ist möglich, weil mehrere Kanäle parallel vom Einlass zum Auslass verlaufen können und so die Formoberfläche homogen abbilden. Die Kanäle können leicht so gestaltet werden, dass sie perfekt in die komplexen Zonen der Form passen. Die Haltbarkeit und Herstellbarkeit der Formen soll mit der konventionellen Methode vergleichbar, wenn nicht sogar besser sein.
Die additive Herstellung des Werkzeugs selbst ist zwar mitunter teurer als die Herstellung mit anderen Verfahren, aber diese Mehrkosten werden durch die erhöhte Produktivität und Langlebigkeit des Werkzeugs bei der Herstellung des Endprodukts wieder wettgemacht.
Prozess
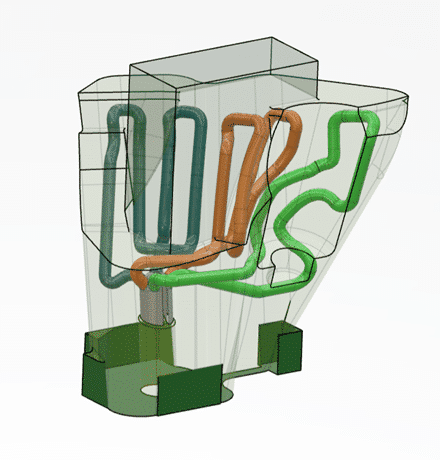
Um die Vorteile des 3D-Drucks voll auszunutzen zu können, musste der Schieber neu konstruiert und die CAD-Datei geändert werden. Das neue Design beinhaltet balancierte Kühlkreisläufen mit einzelnen, parallel angeordneten Kanälen. Auf diese Weise kann das Kühlmittel näher an die zu kühlenden Teile heranfließen, unabhängig von ihrer Form. Die Abkühlungsraten sind schneller, aber auch homogener im gesamten Teil, da die Kanäle einen gleichmäßigen Abstand zu den Merkmalen haben. Mit anderen Worten: keine heißen Stellen mehr.
Der Arbeitsablauf der Additiven Fertigung erfordert auch einige Anpassungen am CAD-Modell. Alle Referenzen und Spannflächen, die in nachgelagerten Bearbeitungsprozessen verwendet werden sollen, müssen in das Modell integriert werden. Diese Merkmale müssen möglicherweise angepasst werden, wenn sich das Design des Teils ändert.
Produktion
Die Schieberkopfeinsätze werden mit der folgenden Maschinenkonfiguration gedruckt:
- FormUp 350 mit 4 Lasern
- Werkzeugstahl 1.2709 / Maraging 18Ni300 (46-50HRC)
- Feines Pulver (5-25µm)
- Roller Recoating Technologie
Für ein Werkzeug werden verschiedene Schieberformen benötigt, von denen alle 8 auf eine FormUp-Bauplattform (350x350mm) passen, die noch Platz für Prüfkörper bietet. Dank der großen Bauplatte und 4 Lasern können alle Einsätze in einem Produktionsauftrag gedruckt werden. Die Fertigstellung aller benötigten Teile in einem Arbeitsgang bedeutet eine enorme Zeit- und Kostenersparnis bei der Inbetriebnahme des Druckers.
Die Roller Abziehtechnologie ermöglicht die Verwendung von feinem Pulver, das in Verbindung mit einem herkömmlichen Klingen- oder Schaberbeschichter verklumpt. Die Verwendung des Rollers ist einzigartig für AddUp.
Die Roller Abziehtechnologie hat den Vorteil, dass durch eine höhere Verdichtung und gleichmäßige Verteilung der einzelnen Pulverschichten beste Oberflächen- und Konturqualitäten erzielt werden. Bei dieser Anwendung konnte Siebenwurst die Oberflächenbearbeitung deutlich reduzieren, was zu einer Kosteneinsparung von 42% in diesem Bereich führte.
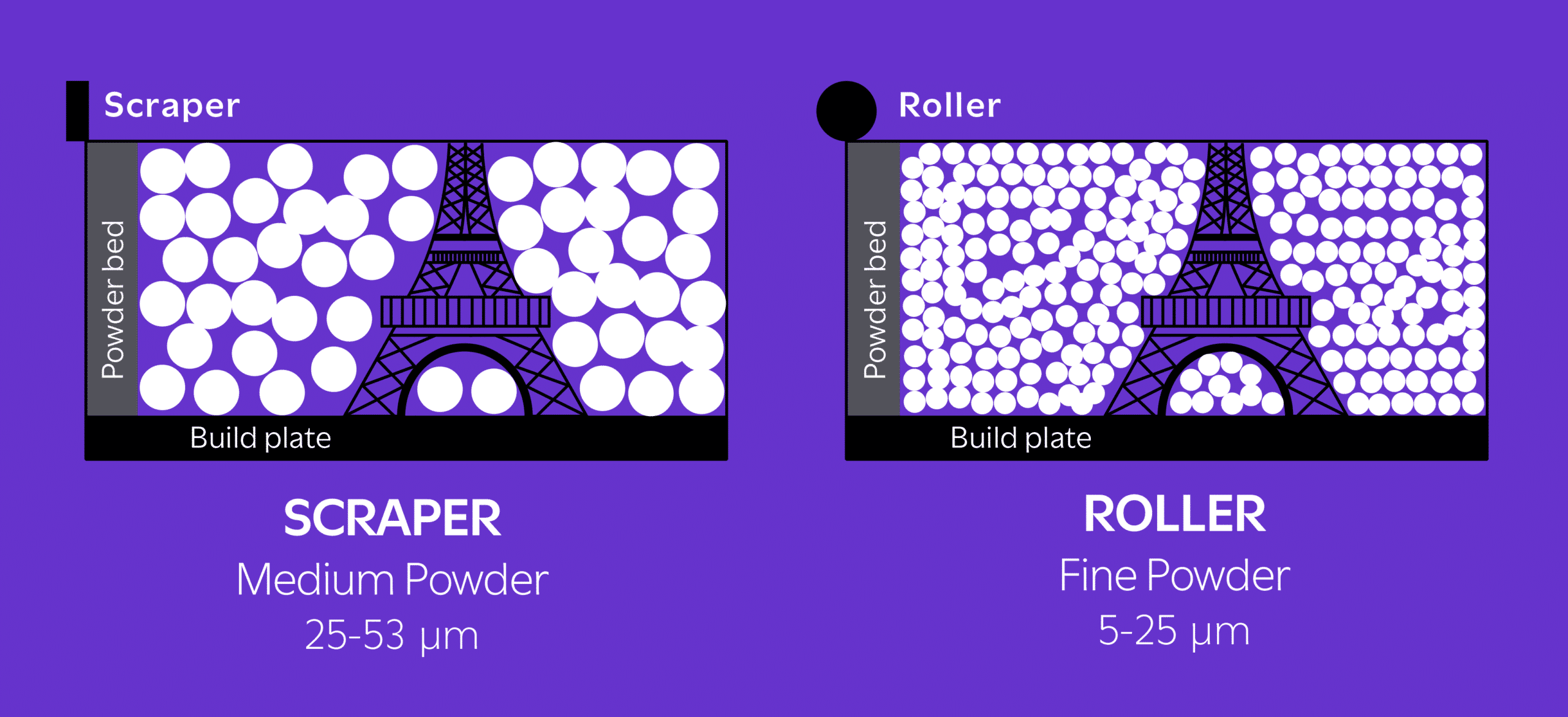
Ein weiterer Schwerpunkt bei diesem Bauteil ist die Konturqualität mit dem Ziel, die Nachbearbeitung auf ein Minimum zu beschränken und die geometrische Abweichung so gering wie möglich zu halten.
Die Bounding Box des Teils ist 100x65x50 mm3 und die maximale Abweichung von der Konturdefinition beträgt 0,12mm Siebenwurst führte die komplette Nachbearbeitung der Schieber und die Bemusterung der Kunststoffteile durch. Die vorherige Bemaßung und Fertigbearbeitung funktionierte einwandfrei und die Bemusterung konnte problemlos im Originalwerkzeug durchgeführt werden.
Die folgenden Bilder zeigen die erzeugte Oberfläche und die Präzision der gedruckten Kontur.
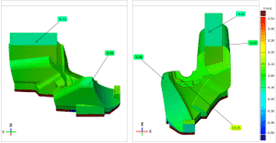
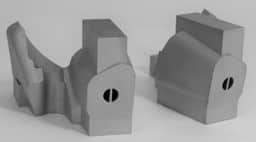
Results
Early trials show the maximum temperature recorded at the insert dropping by 16°C, a clear mark of improvement and a sign that the hot spot was eliminated in the new design. The printed part held to the expected geometric tolerance and allowed for a significant reduction in surface finishing expenses. As the study continues, cycle time and tool longevity will be studied as well.
The success of this project inspired further cooperation between AddUp and Siebenwurst in the near future, and has opened the doors for Siebenwurst to pursue more AM applications.
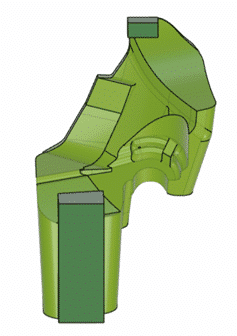
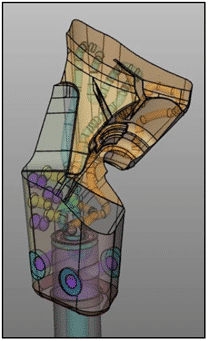
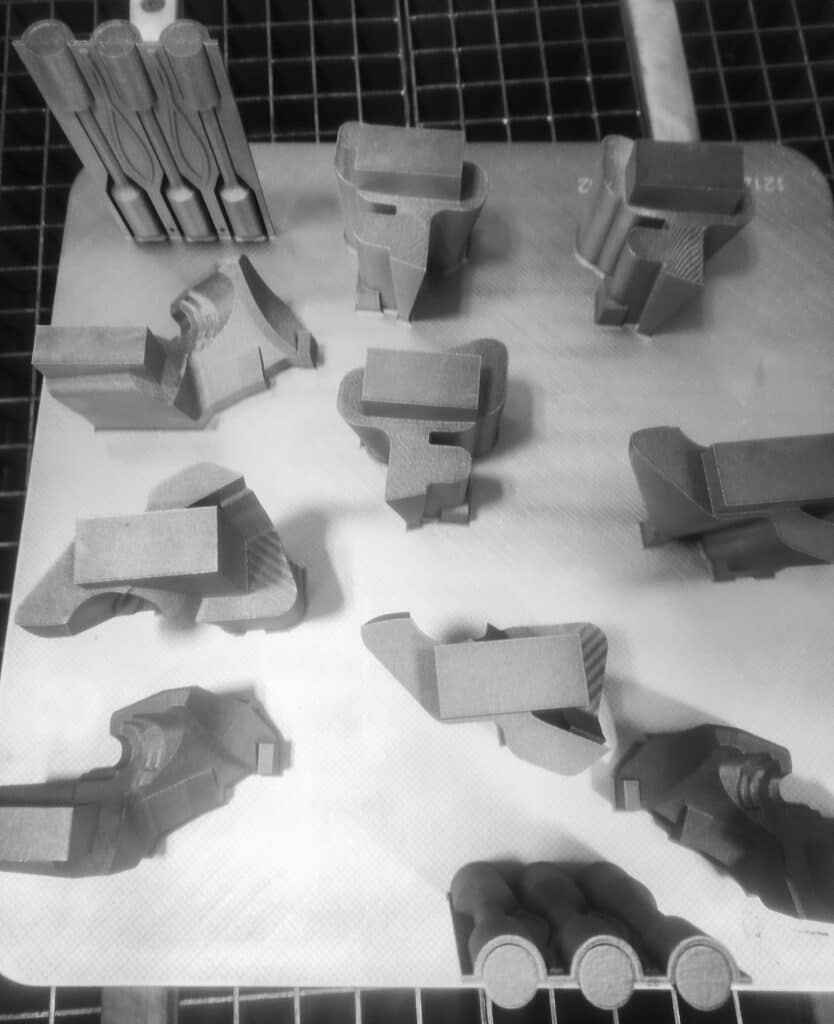
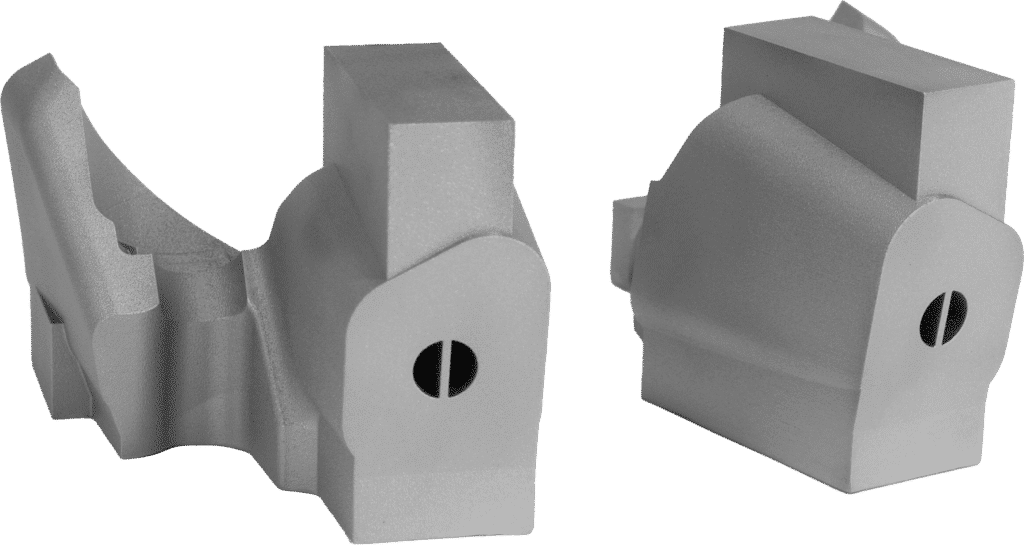
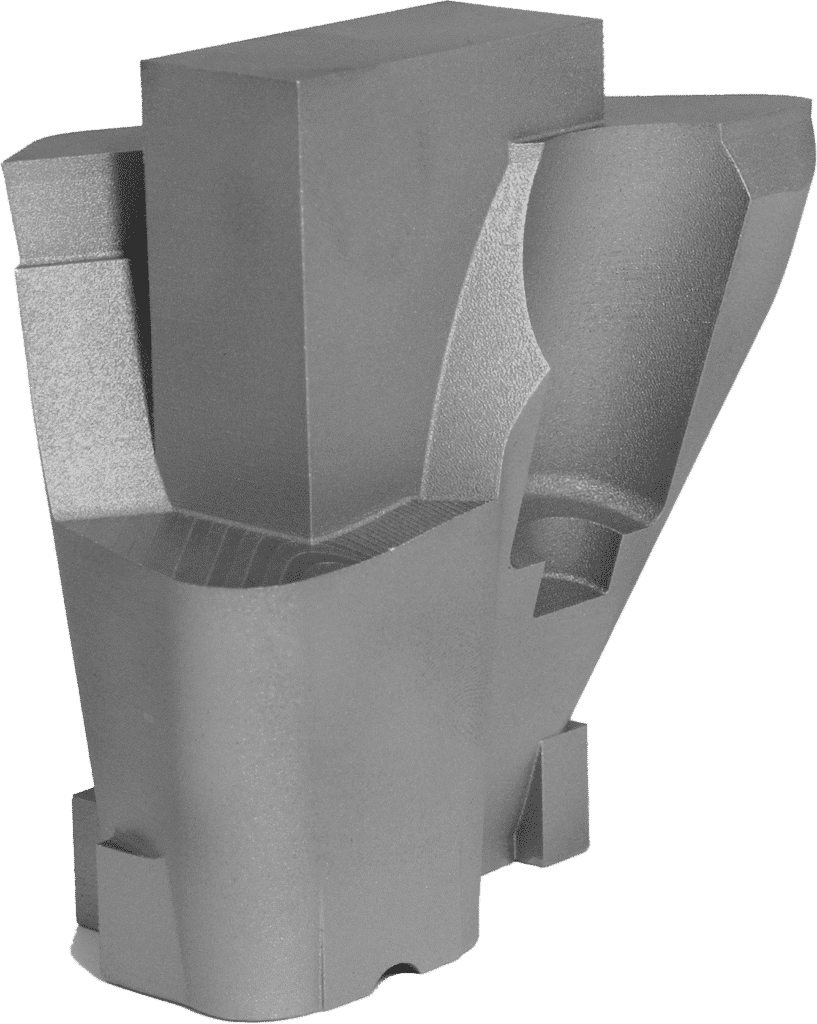
Reduction of the slide valve temperature from 62°C to 46°C
Elimination of temperature hotspot in slide gate area
Surface finishing cost reduction of 42%