Im Juni 2020 hat die französische Regierung einen Plan zur Unterstützung der Luftfahrtindustrie aufgelegt, um die Hersteller in diesem Sektor bei der Bewältigung der Folgen der G e s u n d h e i t s k r i s e z u unterstützen und sie zu ermutigen, die Verringerung des CO2-Fußabdrucks ihrer Aktivitäten zu beschleunigen. (Plan de soutien à la filière aéronautique) 1,5 Milliarden Euro werden in den nächsten drei Jahren zur Verfügung gestellt, um Forschungs- und Entwicklungsprojekte in diesem Bereich zu unterstützen.
3D-Druck und Luftfahrt: auf dem Weg zu „saubereren“ Flugzeugen
Es wurden drei Haupthebel identifiziert, um zu „saubereren“ Flugzeugen zu gelangen:
- Verringerung des
- Kraftstoffverbrauchs die Elektrifizierung von Geräten
- der Übergang zu kohlenstoffneutralen Kraftstoffen wie Wasserstoff
In diesen drei Bereichen kann der 3D-Druck Antworten für Hersteller liefern, die die Leistungsgrenzen von mit herkömmlichen Techniken hergestellten Geräten überwinden wollen.
Die Luft- und Raumfahrtindustrie hat sich schon früh für die additive Fertigung (3D-Druck) interessiert und setzt sie seit Jahrzehnten ein. Zunächst wurde er zur Herstellung von Prototypen verwendet, um die Entwicklungszeit neuer Flugzeuge zu verkürzen. Im Zuge der Bemühungen, Flugzeuge leichter zu machen, begannen die Flugzeughersteller dann, Funktionsteile zu drucken. Heute sind kritische Teile (z. B. Triebwerksteile) und sogar Strukturteile, die mit verschiedenen 3D-Druckverfahren hergestellt wurden, an Bord von Flugzeugen zu finden.
Laut einem Bericht von Market Research Future wird die Zahl der für die additive Fertigung in der Luft- und Raumfahrtindustrie zertifizierten Unternehmen und Zulieferer bis 2023 voraussichtlich um mehr als 20 % pro Jahr steigen. Die AddUp-Gruppe ist einer dieser Lieferanten, die in der Lage sind, die Anforderungen der Luft- und Raumfahrtindustrie zu erfüllen: Unsere Produktionsstätte in Salon-de-Provence (Bouches-du-Rhône, Frankreich) ist nach NF EN 2100: 2018 zertifiziert.
DED und L-PBF, zwei sich ergänzende Technologien
Unser Maschinenangebot eignet sich auch für Anwendungen in der Luft- und Raumfahrt. Die DED- Technologie eignet sich zum Beispiel für die Reparatur verschlissener Teile und wird für die Aufarbeitung von Flugzeugtriebwerksteilen verwendet. Sie kann auch zur Herstellung großer Teile wie Düsen oder komplexer Rohre verwendet werden, und zwar zu geringeren Kosten als bei der Bearbeitung von Grund auf und mit besserer Wiederholbarkeit als beim Kesselbau.
Die Laser-Powder-Bed-Fusion (L-PBF)-Technologie wird für die Herstellung kleinerer Teile verwendet, die jedoch eine große Formfreiheit aufweisen. Dies ermöglicht es den Ingenieuren, Leistungssteigerungen in vielen Bereichen zu berücksichtigen, z. B. Gewichtsreduzierung, verbesserte Flüssigkeitsströmung und optimierter Wärmeaustausch.
Die folgenden zwei aktuellen Anwendungsfälle aus dem Luftfahrtsektor veranschaulichen die Art von Gewinnen, die mit dieser Technologie möglich sind.
Ein für den 3D-Druck konzipierter Hydraulikverteiler
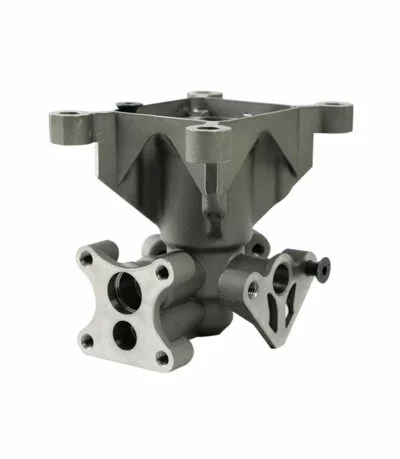
Kürzlich arbeitete die Airbus-Gruppe mit AddUp und Hall32, einem Zentrum für die Förderung industrieller Berufe, an der Optimierung eines Hydraulikverteilers mit Hilfe der additiven Fertigung von Metall. Das Originalteil ist ein Flüssigkeitsverteiler, der traditionell aus einem Titanblock gefräst wird. Dank der Technik der topologischen Optimierung gelang es AddUp und Hall32, die Masse des Teils um 85 % zu verringern und gleichzeitig den Flüssigkeitsdurchfluss zu verbessern.
Das Projekt war damit noch nicht zu Ende! Das Teil erforderte die Herstellung einer großen Anzahl von Stützen, was Zeit für das Drucken (Zeit für die Herstellung der Stützen) und die Bearbeitung (Zeit für das Entfernen der Stützen) bedeutete. Die AddUp- und Hall32-Ingenieure führten daher einen zweiten Optimierungsdurchgang durch, um die mit dem Prozess verbundenen Zwänge zu berücksichtigen (dies wird DfAM genannt, für Design for Additive Manufacturing). In der endgültigen Version wird der Flüssigkeitsverteiler in 30 Stunden gedruckt, im Vergleich zu 52 Stunden in der ersten Version, und die Bearbeitungszeit wurde um 6 Stunden reduziert.
Ein innovativer Wärmetauscher
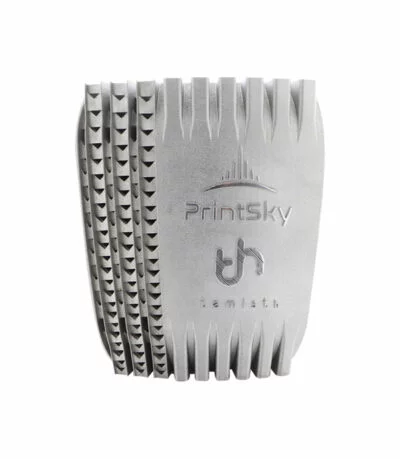
HEWAM ist ein von Printsky und Temisth entwickeltes Wärmetauscherkonzept. PrintSky ist ein Joint Venture zwischen der AddUp-Gruppe, einem Experten für die additive Fertigung von Metallen, und Sogéclair, einem der international führenden Unternehmen für die Integration von Lösungen mit hohem Mehrwert in den Bereichen Luft- und Raumfahrt sowie ziviler und militärischer Transport.
Temisth ist ein Unternehmen, das sich auf die Entwicklung von maßgeschneiderten thermische Lösungen durch additive Fertigung. Ziel des HEWAM-Projekts war es, die Fähigkeit beider Partner zu demonstrieren, einen innovativen Wärmetauscher mit dem PBF-Verfahren zu entwickeln und herzustellen.
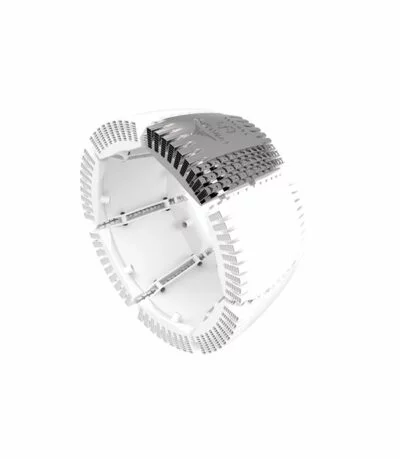
Die Produktion wurde AddUp anvertraut, die dieses Luftfahrtteil auf einer FormUp 350-Maschine 3D-gedruckt haben. Die Experten von AddUp verwendeten ein feinkörniges Inconel® 718-Pulver, um dünne Wände mit guter Oberflächengüte zu erzeugen und so eine hohe thermische Leistung. Diese dünnen Wände (150 µm) bilden Kanäle mit einer komplexen Geometrie, die es HEWAM ermöglicht, eine hohe Wärmeaustauschkapazität auf kleinem Raum zu erreichen.
Über die Leistung hinaus bietet HEWAM auch eine neue Art des Wärmeableitungsmanagements an Bord von Flugzeugen. Dieses Abwärmemanagement ist vor allem seinem modularen Aufbau zu verdanken. Mehrere Wärmetauscher können nebeneinander platziert werden, um die für die jeweilige Anwendung erforderliche Wärmeleistung zu liefern. Außerdem kann HEWAM dank seiner gebogenen Form in den Triebwerkspylonen installiert werden, wobei in d e r Mitte Platz für die zum Betrieb der Triebwerke erforderlichen Kabel bleibt. Sein L e i s t u n g s – / P l a t z v e r h ä l t n i s und seine Modularität machen HEWAM zu einer interessanten Alternative für Flugzeughersteller, die den Wärmeaustausch an Bord ihrer Flugzeuge optimieren wollen.
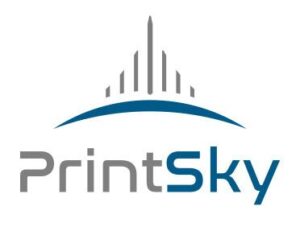
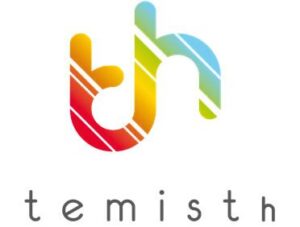
Weitere Vorteile des 3D-Drucks von Metall
Ein funktionsfähiges System, das früher den Zusammenbau mehrerer kleiner Teile erforderte, kann jetzt in einem einzigen Produktionslauf 3D-gedruckt werden. Es muss nicht mehr zusammengebaut oder geschweißt w e r d e n , und das Risiko, dass die Teile in der Luft zerbrechen, ist geringer. Durch die Verwendung zertifizierter Materialien wird außerdem sichergestellt, dass die gedruckten Teile einsatzbereit sind und den harten Anforderungen einer realen Anwendung standhalten.
Um Flugzeuge vor einem Flugverbot zu bewahren, werden seit jeher Ersatzteilvorräte angelegt. Viele dieser Teile sind jedoch unbenutzt oder sogar veraltet. Der 3D-Druck e r m ö g l i c h t e s , dieses Problem teilweise zu entschärfen, indem Ersatzteile je nach Bedarf und Einsatzort auf Abruf hergestellt werden.
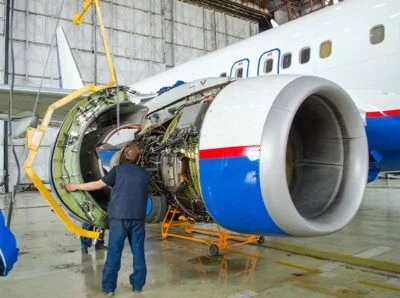
Der 3D-Metalldruck scheint viele Vorteile zu haben, die es der Luftfahrtindustrie ermöglichen, wieder in Schwung zu kommen
Von der Integration von Metallteilen mit komplexen Geometrien bis hin zur Gewichtsreduzierung von Flugzeugen durch den Einsatz von Leichtmetallen, um Treibstoff zu sparen, bietet die additive Fertigung zahlreiche Vorteile, um die finanziellen und ökologischen Ziele der Luft- und Raumfahrtindustrie zu erreichen. Durch die Einführung der additiven Fertigung in die Produktion werden topologische Optimierung, kostengünstige Komplexität, weniger Teile, geringere Lagerbestände und die gesamte Wertschöpfungskette des Luftfahrtsektors eine echte Evolution erfahren.
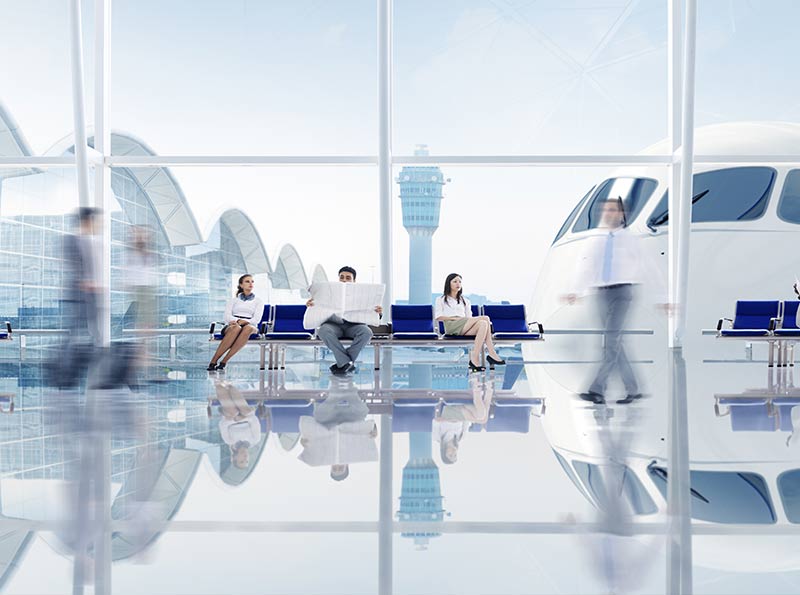