L’objectif est de réaliser un réservoir étanche pouvant contenir du gaz et qui peut tenir la pression de fonctionnement de 60 bars pour des applications de boucle fluide.
ADS (Airbus Defence and Space) s’associe à AddUp pour produire un réservoir étanche capable de supporter une pression de 60 bars. Ce réservoir peut équiper un système de transport de chaleur diphasique. A température ambiante, le fluide de travail contenu dans le système est au-dessus de sa température critique. Il est de fait entièrement gazeux. Ce réservoir a pour vocation d’augmenter le volume du système, la boucle fluide, afin de limiter la pression interne pour une température donnée. Lisez l’étude de cas pour connaitre les avantages d’imprimer des pièces en fabrication additive.
INDUSTRY
Aerospatial
CHALLENGE
Imprimer en 3D un reservoir etanche capable de supporter une pression de 60 bars pour des applications de boucle de fluide.
KEY BENEFITS
- Une seule piece, imprimee en une seule fats
- Imprimee sans support a l’interieur de la piece
- Reduction de la masse de la piece
REDUCTION DE LA MASSE
Performance
Histoire: AddUp et ADS
ADS (Airbus Defence and Space) est une division d’Airbus Group qui est l’un des 10 principaux acteurs mondiaux du secteur de la défense et du spatial. Elle est spécialisée dans les avions militaires, les drones, les missiles, les lanceurs spatiaux et les satellites artificiels. ADS souhaite évaluer la faisabilité de fabriquer une sphère creuse en inox. L’objectif est de réaliser un réservoir étanche pouvant contenir du gaz et qui peut tenir la pression de fonctionnement de 60 bars pour des applications de boucle fluide utilisant des fluides en état supercritique aux températures maximales non-opérationnelles du système.
Ce réservoir peut équiper un système de transport de chaleur diphasique. A température ambiante, le fluide de travail contenu dans le système est au-dessus de sa température critique. Il est de fait entièrement gazeux. Ce réservoir a pour vocation d’augmenter le volume du système, la boucle fluide, afin de limiter la pression interne pour une température donnée.
Défi de l’impression d’un réservoir étanche
La technique existante consiste à avoir un cylindre et des coques hémisphériques usinées soudés ensemble. La masse d’un tel réservoir est actuellement trop élevée et les zones de soudures sont des zones de surcontrainte lors de la mise sous pression. ADS a donc demandé à AddUp de produire un réservoir en utilisant la fabrication additive métallique dans le but final de pouvoir s’affranchir des contraintes de tous les procédés conventionnels et obtenir un réservoir sphérique, la forme idéale pour résister à la pression.
Le cahier des charges:
- Impression en 316L
- Résister à une pression de 60 bars
- Imprimée en un seul morceau, sans assemblage, ni supports de fabrication à l‘intérieur
- Pièce légère (à l’épaisseur mini théorique pour supporter la totalité de la pression)
- Pièce en forme de sphère
Solution d’un réservoir sphérique imprimé en 3D
Pour permettre de fabriquer la sphère, l’utilisation de la FormUp® 350 s’est imposée car elle peut être équipée d’un système de mise en couche de type rouleau et utiliser de la poudre fine. Cette machine, dans cette configuration, permet de construire de grandes surfaces en contre-dépouille sans supports. Le 316L, acier inoxydable, a été choisi pour cette application car il adapté pour contenir un fluide et résiste à la corrosion, ce qui permet une durée de vie élevée de la pièce.
Résultats et avantages de la fabrication additive
La géométrie de la pièce est conforme au design souhaité par ADS. Il n’a pas été nécessaire de l’aménager pour réussir à produire la pièce, dont les dimensions sont de 78 mm de diamètre interne, avec une épaisseur de 2,2 mm.
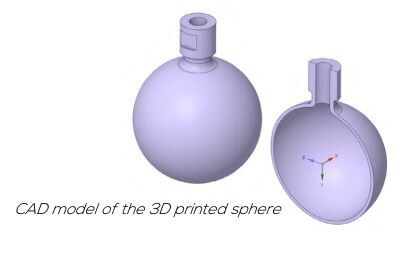
En savoir plus sur Airbus Defence and Space ici.
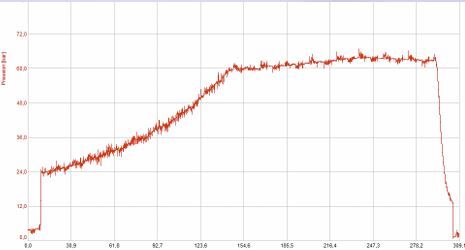
L’utilisation couplée du rouleau et de la poudre en granulométrie fine ont permis de produire des parois fines avec un très bon état de surface. Ce dernier à l’intérieur de la pièce est suffisamment propre pour ne pas avoir à l’améliorer par une opération supplémentaire.
Les deux pièces imprimées en 3D ont tenu la pression de 60 bars à l’eau pendant deux minutes. La pièce a été testée sur banc d’essai. L’extérieur de la nouvelle pièce métallique a été repris en usinage pour garantir une épaisseur constante sur l’ensemble de la sphère et supprimer les défauts d’états de surface inhérents au procédé.
“Airbus Defence and Space a une grande expérience dans le développement de solutions innovantes en fabrication additive en collaboration avec AddUp. Ce nouveau démonstrateur montre l’expertise technique d’AddUp dans la fabrication de designs innovants pour permettre à ADS de proposer des applications disruptives à forte valeur ajoutée. Cette conception n’aurait pas été réalisable sans la combinaison du rouleau et de la poudre fine développée par AddUp. Cela ouvre la porte à des conceptions toujours plus innovantes. “
~ Delphine Carponcin, Manager de projet fabrication additive Airbus Defence and Space