Pièces fabriquées additives à l’intérieur des machines | Blog
AddUp, fabricant d’imprimantes 3D en métal, propose non seulement des services de production de pièces, mais utilise également ses propres machines pour fabriquer des composants pour ses imprimantes 3D.
AddUp est un constructeur de machines d’impression 3D qui exploite ses propres machines dans ses ateliers, pour proposer des services de production de pièces à ses clients. Mais saviez-vous que ces ateliers servent également à fabriquer des composants pour de nouvelles machines ? La FormUp 350 compte ainsi de nombreuses pièces imprimées en 3D, qui sont représentatives des différentes possibilités offertes par la technologie.
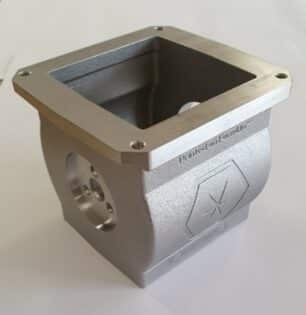
Des pièces produites sur la FormUp 350, pour la FormUp 350
AddUp est l’un des seuls fabricants de machines d’impression 3D métallique à proposer également des services de production de pièces, grâce à plusieurs ateliers en Europe et aux Etats-Unis. Quand elles ne sont pas utilisées pour produire des pièces pour des clients, les machines FormUp fabriquent des pièces… pour de nouvelles machines FormUp. « Générer de la valeur grâce à des pièces qui cumulent plusieurs fonctions, sont plus performantes ou présentent des délais d’approvisionnement plus courts, ce n’est pas qu’un discours que nous portons auprès de nos clients, c’est aussi un cercle vertueux que nous appliquons en interne, affirme Léopold Barry, chargé de projet FormUp 350 deuxième génération chez AddUp. Tous ces développements ont pour but de faire de cette machine une vitrine des différentes possibilités offertes par l’impression 3D. »
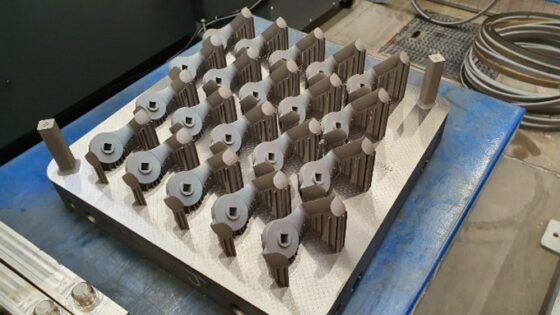
En effet, de nombreuses pièces de cette machine sont réalisées par fabrication additive, à commencer par le système d’approvisionnement en poudre, qui compte à lui seul quatre composants imprimés. D’abord, citons les trémies de dosage. Il s’agit des réserves de poudre qui évitent toute rupture d’alimentation en poudre de la chambre de fabrication. Le design de ces pièces a été adapté de sorte qu’elles puissent être réalisées soit en fonderie, soit en fabrication additive, pour répondre à des besoins de temps d’approvisionnement courts.
A l’intérieur de ces trémies de dosage, on trouve une pièce qui est quant à elle systématiquement imprimée en 3D, quelle que soit la machine. Il s’agit d’une pièce chargée de maintenir la poudre en mouvement afin d’éviter toute agglomération qui pourrait interrompre la production. Pour cette pièce à la géométrie complexe, la fabrication additive était tout indiquée. D’autant qu’un plateau de fabrication standard de 350 x 350 mm permet d’imprimer une vingtaine de ces pièces, et donc de constituer rapidement des stocks de pièces de rechange sur cette référence
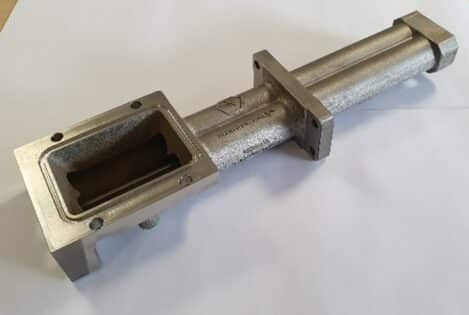
Juste en dessous des trémies de dosage se trouvent les vis de dosage, dont le rôle est de déposer la poudre de manière précise et uniforme à la surface des « tiroirs » qui transportent la poudre devant le dispositif d’étalement du lit de poudre. Ces vis de dosage sont installées dans un fourreau, également imprimé en 3D. « Ce système imprimé en une seule opération présente une alternative intéressante à son équivalent réalisé par fonderie, car il nous permet de tester rapidement de nouveaux designs sans surcoûts liés au développement de nouveaux moules d’injection. De plus, cette pièce monobloc ne nécessite plus d’opérations assemblage, et présente une meilleure étanchéité », commente Léopold Barry.
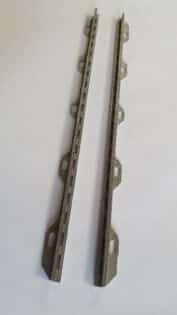
Autre élément essentiel du système d’approvisionnement en poudre : les rails sur lesquels coulissent les tiroirs chargés d’apporter la poudre dans l’enceinte de fabrication. Eux aussi sont fabriqués sur machines FormUp dans les ateliers d’AddUp. L’avantage ici est l’autonomie gagnée sur la gestion de cette référence, avec des délais d’approvisionnement raccourcis au maximum car la fabrication tout comme l’usinage sont réalisés en interne.
Optimisation topologique et intégration de fonctions
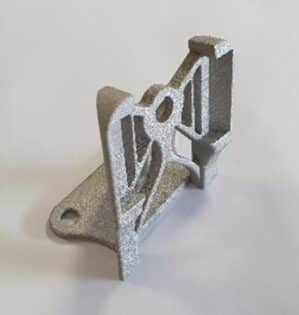
Si les ingénieurs d’AddUp ont su utiliser la fabrication additive pour le système d’approvisionnement en poudre, qui est une des fonctions clés de la machine, ils ont fait de même pour certaines pièces plus simples, comme des supports pour caméras. Sur les FormUp 350 nouvelle génération, les deux caméras sont installées sur des supports imprimés. Premièrement, la caméra de prise d’images, qui réalise des photographies de fin de fusion et de fin d’étalement de poudre, est placée sur un support conçu par optimisation topologique. Cette technique consiste à utiliser un logiciel de simulation qui génère automatiquement une forme optimale pour la pièce, en utilisant la quantité de matière juste nécessaire pour assurer la fonction de mise en position de la caméra.
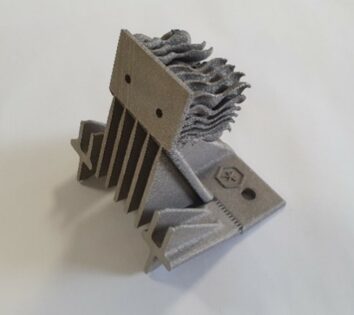
Deuxièmement, le support de la caméra vidéo a été conçu en utilisant une autre possibilité offerte par l’impression 3D : l’intégration de fonctions. « Lors du développement des machines prototypes, nos équipes ont travaillé sur le refroidissement de cette caméra vidéo, qui est placée au-dessus de l’enceinte de fabrication, explique Léopold Barry. Nous avons conçu une nouvelle version de ce support, qui intègre à la fois la fonction de maintien en position de la caméra et la fonction de refroidissement. » Cette dernière fonction est assurée par des lamelles métalliques qui jouent le rôle de radiateur. Leur surface, impossible à réaliser par des techniques conventionnelles, présente une grande surface d’échange avec l’air ambiant, et évite toute surchauffe de la caméra.
Des pièces pour les machines de série, mais aussi pour les prototypes

AddUp a su tirer parti des possibilités offertes par la fabrication additive à tous les stades du développement de sa nouvelle machine, y compris lors des phases de prototypage. Elles ont été l’occasion de tester un nouveau type de bloc hydraulique. Cette pièce, chargée de distribuer le liquide de refroidissement dans la machine, a fait l’objet d’une étude de reconception complète. Ce qui était auparavant une imposante pièce de métal brut, percée de canaux rectilignes, est devenue un système optimisé, tant du point de vue de la masse que de la gestion des flux à l’intérieur des canaux. Et l’orientation des connecteurs permet de réduire l’encombrement des nombreux tuyaux. Des travaux sont toujours en cours pour améliorer encore la pièce avant de l’intégrer aux machines de série. En attendant, le travail sur ce bloc hydraulique et les tests réalisés en conditions réelles de fonctionnement font office de démonstrateur pour des industriels d’autres secteurs confrontés à des impératifs de réduction de masse sur des systèmes similaires.
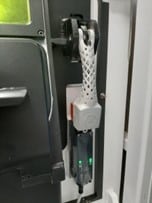