Découvrez comment cet inducteur imprimé en 3D a répondu à toutes les exigences de qualité et comment ses performances industrielles ont dépassé les attentes initiales.
Une bobine de chauffage par induction est un outil de production qui permet d’effectuer un traitement thermique local sur des pièces métalliques ; ici, elle est utilisée pour braser les pointes de contact sur des pièces en cuivre ou en laiton, qui sont ensuite assemblées dans des disjoncteurs et contacteurs. L’usine 4.0 de Schneider Electric du Vaudreuil, située en Normandie, est une vitrine de la nouvelle révolution industrielle. Identifiée comme l’une des usines les plus développées dans le monde, elle utilise les dernières avancées technologiques en matière d’IloT, de mobilité, de détection, de cloud, d’analyse et de cybersécurité. Cette usine fabrique 40 000 contacteurs par jour.
INDUSTRIE
Energie
CHALLENGE
Imprimer un inducteur « Plug & Play » avec un temps
de production court
KEY BENEFITS
- Pièce aux géométries complexes
- Amélioration des performances
- Reduction du temps de production de la pièce
FORMES CRÉATIVES
TEMPS DE PRODUCTION
POIDS
PERFORMANCE
Défi technologique
Schneider Electric a conçu un nouvel inducteur pour maximiser toutes ses performances techniques et industrielles. L’objectif de l’opération est d’atteindre la bonne température au niveau de la soudure sans abimer le support, dans un temps de cycle souhaité.
Il était impossible de fabriquer cette pièce complexe avec les procédés classiques, et l’impression 3D a permis de s’affranchir de ces contraintes de fabrication. Schneider Electric a fait appel à AddUp pour assurer la facilité de production de cette pièce complexe et dans des délais courts.
Les principales exigences fonctionnelles d’un inducteur sont les suivantes :
- Être un bon conducteur de courant (c’est le courant qui circule dans l’inducteur qui induit le champs électromagnétique responsable de la chauffe)
- Être étanche (de l’eau circule dans l’inducteur
pour le refroidir) - Être robuste et durable (stabilité dimensionnelle,
durée de vie, aptitude aux changements d’outils…).
Solution
En utilisant la machine FormUp 350, AddUp a pu imprimer un inducteur en cuivre selon les contraintes et besoins de Schneider Electric et en un temps plus réduit.
Intégrée ensuite à une ligne de production, la nouvelle pièce a subi les essais suivants :
- Test de fuite et mesure du débit d’eau
- Mise sous tension et brasage de pièces, analyse
des points chauds avec une caméra infrarouge - Mesure du temps de cycle
Schneider a enfin contrôlé les pièces imprimées en 3D, notamment la qualité des brasures (contrôle visuel, test d’arrachement, contrôle ultrasons, coupe micrographique et dureté des échantillons).
Résultats
Enfin, il a été constaté que l’inducteur fabriqué de manière additive a pu être intégré avec succès dans la ligne de production.
L’inducteur a répondu à toutes les exigences de qualité et ses performances industrielles ont dépassé les attentes initiales.
“L’inducteur fourni par AddUp a été facilement intégré dans notre système, directement, sans aucune retouche sur la pièce. Le temps de production a été réduit, ce qui offre une réactivité très intéressante, surtout pour des pièces à géométrie complexe. Enfin, il est à noter que la performance industrielle est bien au rendez-vous : la cadence cible est atteinte et l’inducteur n’a pas été changé au cours des 4 derniers mois. Ceci est significatif car un inducteur fabriqué de manière conventionnelle est généralement changé tous les 6 mois“.
~Guillaume Fribourg, Expert matériaux et procédés, Chef de projet Fabrication Additive, Schneider Electric
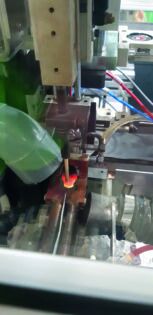