Un support de caméra imprimé en 3D, conçu pour résister aux accélérations et aux vibrations pendant le lancement dans l’espace et pour maintenir une caméra et son objectif en position pendant les phases de production d’une imprimante 3D métallique.
L’objectif du projet « Metal3D » est de caractériser les propriétés mécaniques d’un matériau produit en microgravité. Pour mener à bien cette expérience, deux lots d’éprouvettes sont produits par deux imprimantes identiques. Alors que le premier lot sera produit à Toulouse en gravité terrestre, le second sera construit dans l’espace, plus précisément dans le module Columbus de la station spatiale ISS (International Space Station), en microgravité.
OBJECTIF
Positionner et maintenir en place une caméra et son objectif pendant les phases de vol et de fabrication.
APPLICATION
3 axes de positionnement pour un réglage précis du champ de la caméra. Conçu pour résister aux accélérations et aux vibrations pendant le lancement.
CONTEXTE
PROJET « METAL3D
MASSE
70 g
Mission
« Metal3D » est une mission commandée par l’ESA (Agence spatiale européenne) en tant que démonstrateur technologique. Son objectif est de caractériser les propriétés mécaniques d’un matériau utilisé en microgravité réelle. Pour mener à bien cette expérience, deux lots d’éprouvettes sont produits par la même conception d’imprimante. Alors que le premier lot sera produit à Toulouse en gravité terrestre, le second sera réalisé dans l’espace, plus précisément dans le module Columbus de l’ISS en microgravité. Pour réaliser ces deux travaux d’impressions, nous avons conçu et fabriqué deux exemplaires identiques d’une machine de fabrication additive métallique capable de fonctionner dans les deux environnements. L’imprimante que nous avons conçue pour cette mission sera donc la première à imprimer des pièces métalliques dans l’espace.
Procédé
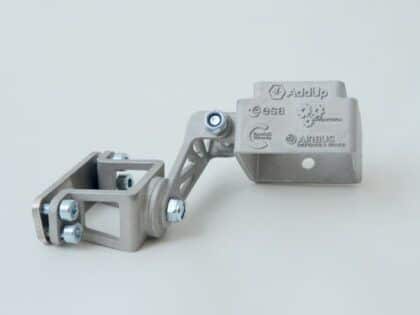
En l’absence de gravité, la majorité des procédés actuels de fabrication additive ne sont plus utilisables. Pour rendre possible la fabrication en microgravité, nous choisissons d’exploiter les forces induites par la tension superficielle. Nous utilisons un laser comme source d’énergie et un fil d’acier comme matière première. Le laser chauffe le substrat pour créer un bain liquide. Dans ce bain liquide, nous immergeons le fil d’acier. En poussant le fil dans le bain liquide, ce dernier se liquéfie également et augmente le volume du bain de fusion. Nous déplaçons ensuite le laser et donc le bain liquide vers la surface du substrat tout en déroulant le fil dans ce bain afin de créer une perle une fois le bain liquide solidifié. Une couche est constituée d’une ou plusieurs billes en fonction de la géométrie de la pièce à réaliser. Une fois la couche terminée, le processus recommence en utilisant la couche précédente comme substrat. De cette façon, couche par couche, une pièce volumétrique est créée.
Nous utilisons un fil 316L. Le laser et le fil sont fixés dans le bâti de la machine. C’est le plateau qui est rendu mobile grâce à 3 axes linéaires et 1 axe rotatif. La machine fonctionne sous azote afin de limiter l’oxydation du matériau et prévenir les risques de combustion. L’accès à l’azote étant limité dans l’ISS, cette atmosphère est recyclée tout au long du processus de fabrication par filtration et refroidissement.
Partenaires
La mission est pilotée par les équipes d’Airbus Defense & Space. L’Université de Cranfield fournit le laser, la chaîne optique et le système d’alimentation en fils du système. Hightech fournit l’enceinte de la machine, qui offre un système étanche et de refroidissement, ainsi que les interfaces entre la machine et le rack auquel elle est connectée. Airbus, en plus de piloter le projet, gère les aspects électroniques et sécurité de la machine.
Sur le plan mécanique, AddUp a la charge de la structure interne et de la partie mobile de la machine. AddUp gère également la carte de contrôle et les capteurs qui surveillent le processus. Du côté logiciel, AddUp a développé l’automate de la machine. Ce logiciel a plusieurs fonctions, il permet de communiquer avec le sol en envoyant différents types de données (mesures, photos, rapports, etc.) depuis la machine et en exécutant les commandes qu’il reçoit.