Cette étude de cas explore les avantages de l’utilisation de moules d’injection imprimés en 3D avec des canaux de refroidissement optimisés. Le projet entre Siebenwurst et AddUp visait à améliorer la productivité et la qualité du processus de moulage par injection.
Industrie
Outillage
CHALLENGE
Optimiser des inserts d’un moule en utilisant la fabrication additive pour augmenter les performances thermiques et réduire les temps de cycle.
KEY BENEFITS
- Un refroidissement proche de la paroi du moule
- Une réduction du temps et du coût de production
- Une amélioration de la qualité des pièces moulées
Formes complexes
Intégration de fonction
Performance
Quels sont les avantages de la fabrication additive métallique d’un moule d’injection imprimé en 3D ? Le refroidissement est un critère clé pour la conception d’un moule d’injection plastique, car il impacte à la fois la productivité du moule et la qualité des pièces. Les canaux de refroidissement doivent donc être placés au plus près de la pièce à injecter. Mais ces canaux sont très difficiles à intégrer dans les parties mobiles des moules. Ces éléments, appelés tiroirs, doivent être en contact avec la pièce pendant l’injection et se déplacer avant l’ouverture du moule pour permettre l’éjection de la pièce. AddUp a imprimé en 3D des canaux de refroidissement optimisés dans les parties mobiles du moule, pour permettre un démoulage plus rapide et plus sûr des pièces finales.
Histoire : fabrication de modèles et de moules chez Siebenwurst
Le groupe Siebenwurst est un fabricant de moules d’injection spécialisé dans les produits de haute qualité. Fondé en 1897, il dispose d’une culture de tradition et d’innovation et travaille pour de nombreux clients dans les domaines de l’industrie et de la recherche. Le groupe réalise un chiffre d’affaires annuel de 100 millions d’euros, et emploie environ 700 personnes dans différents sites : en Allemagne à son siège de Dietfurt dans l’Altmühltal, ainsi qu’à Munich, Dillenburg, Rohr, mais aussi au Mexique, en Chine et aux États-Unis.
Défis de la conception d’impression 3D
Siebenwurst a travaillé en étroite collaboration avec AddUp pour optimiser le système de refroidissement d’un élément mobile de moule grâce à la fabrication additive métallique. Pour ce projet lancé par la WBA Tooling Academy, basée à Aachen en Allemagne, les ingénieurs de Siebenwurts devaient simuler le fonctionnement de la pièce à l’aide d’un logiciel d’étude thermique pour valider son efficacité.
L’objectif de ce projet était de se libérer des contraintes associées à la fabrication de tiroirs par des méthodes conventionnelles :
Le besoin de réaliser la pièce en de multiples opérations, sur des machines différentes, qui entraîne des temps de production très longs .
La difficulté de contrôler précisément la température de la paroi moulante.
Avec ses canaux de refroidissement complexes, l’élément réalisé en impression 3D métallique permet un meilleur contrôle de la température de la pièce. En éliminant les points chauds, il entraîne une réduction du temps de refroidissement, et donc du temps de cycle. Ces gains de productivité compensent les surcoûts liés à la technologie de fabrication additive métallique.
Par ailleurs, le refroidissement plus uniforme diminue les phénomènes de déformation des pièces, et génère des états de surfaces plus homogènes. Par ailleurs, il garantit que toutes les pièces sont à la même température lors de l’éjection.
La fabrication additive métallique est encore peu utilisée dans le domaine de l’outillage. Mais ce projet réalisé par Siebenwurst et AddUp apporte une preuve concrète que cette technologie peut apporter de la valeur ajoutée dans ce secteur, tant sur le plan économique que qualitatif.
La réussite de ce projet est due à l’expertise de Siebenwurst dans le domaine de la simulation thermique du procédé d’injection plastique, ainsi qu’aux équipes d’AddUp qui ont créé les formes finales des canaux en prenant en compte à la fois les résultats de simulation thermique et les contraintes de la technologie de fusion laser sur lit de poudre (L-PBF).
Solution pour les canaux de refroidissement optimisés de fabrication additive
AddUp a intégré des canaux de refroidissement optimisés dans les parties mobiles du moule, pour permettre un démoulage plus rapide et plus sûr des pièces finales. Grâce aux tests de simulation et à l’optimisation thermique du design, il a été possible d’imprimer en 3D les canaux de refroidissement avant l’assemblage.
Siebenwurst a utilisé du PM420 / 1.2083, un acier à outils standard qu’AddUp peut traiter sur ses machines à fusion sur lit de poudre (L-PBF). Le PM420 / 1.2083 est déjà couramment utilisé dans les applications de moulage par injection de plastique et est bien connu des fabricants de moules. En plus d’une dureté élevée (52 HRC), cet acier présente une résistance importante à la corrosion et peut facilement être poli.
Résultats et avantages de la fabrication additive
En se basant sur les résultats de simulation thermique, AddUp a pu concevoir des canaux aussi proches que possible de la paroi du moule. Lors des dernières simulations effectuées sur les canaux optimisés, les ingénieurs de Siebenwurst ont calculé que les points chauds pourraient être réduits d’environ 15°C.
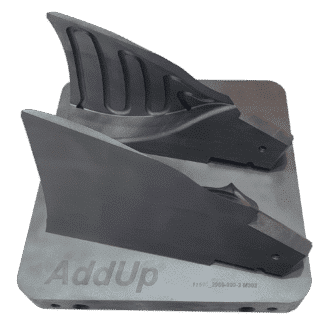
Le moule optimisé a été produit sur une machine FormUp® 350 Nouvelle Génération, une machine L-PBF d’AddUp équipée de 4 lasers. Le temps de fabrication pour deux pièces est d’environ 130 heures.
- Meilleure performance thermique
- Canaux de refroidissement plus proches de la pièce
- Réduction du temps de cycle et des défauts
- Amélioration de l’homogénéité thermique
En savoir plus sur le groupe Siebenwurst ici.