Die additive Fertigungstechnologie FormUp 350 von AddUp revolutioniert die Produktion von Hüftpfannen, indem sie effiziente Laser Powder Bed Fusion (LPBF)- Funktionen bietet, die herkömmliche Methoden und die Elektronenstrahltechnologie (EBM) übertreffen.
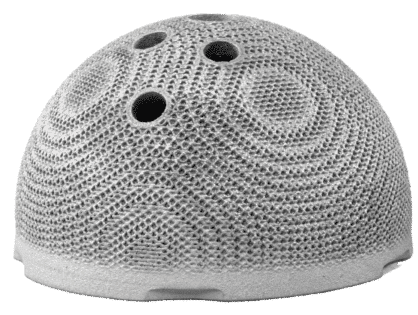
Einführung
Hüftgelenkspfannen, wesentliche Bestandteile von Hüftgelenksprothesen, werden traditionell durch Gießen und Schmieden hergestellt. Diese Methode war zwar effektiv, aber umständlich und kostspielig und erforderte lange Vorlaufzeiten und komplexe Validierungen. Das bahnbrechende FormUp 350 von AddUp hat dieses Bild jedoch verändert und zeigt, wie additive Fertigungstechnologien diesen Bereich revolutionieren können.
Traditioneller Herstellungsprozess
In der Vergangenheit beruhte die Herstellung von Hüftgelenkpfannen auf dem Wachsausschmelzverfahren, einem arbeitsintensiven Prozess, der zu langsamen Durchlaufzeiten und zusätzlichen, kostspieligen Verarbeitungsschritten führte. Das Endprodukt erforderte eine poröse Struktur, die sowohl teuer in der Herstellung als auch schwierig in der Validierung war, was den Fortschritt in diesem Bereich erheblich behinderte.
Das Aufkommen der additiven Fertigung und die Grenzen der Elektronenstrahltechnologie
Die additive Fertigung brachte einen bedeutenden Wandel in der Produktion von Hüftpfannen mit sich, wobei die Elektronenstrahltechnologie (EBM) eine vielversprechende Alternative zu den herkömmlichen Verfahren darstellt. Die EBM bietet eine vielversprechende Alternative zu den herkömmlichen Verfahren. Allerdings sind mit der EBM auch Herausforderungen verbunden, wie z. B. unvorhersehbare Fehler und komplexe Validierungsprozesse, die die Gesamtzeit und – kosten der Produktion in die Höhe treiben können.
Die spielverändernde Wirkung von AddUps FormUp 350: Ein überragender Sprung in der Herstellung von Hüftpfannen
Auf der Suche nach effizienteren und präziseren Fertigungsmethoden hat sich die FormUp 350 von AddUp als überlegene Alternative zum EBM erwiesen. Diese innovative Maschine, die mit der Laser Powder Bed Fusion (LPBF)-Technologie arbeitet, liefert endkonturnahe Teile, die keine Stützen benötigen, was die Nachbearbeitung und die Vorlaufzeiten drastisch reduziert. Sie bietet eine größere Bauplatte und mehr Laser als EBM-Drucker, was den Durchsatz verdoppeln und die Produktionsprozesse optimieren kann.
Der FormUp 350 zeichnet sich durch eine feine Auflösung und einen Walzenbeschichter aus, der das Drucken einer Gitterstruktur im Implantat ermöglicht. Dieses Hauptmerkmal verbessert die Osseointegration erheblich, was zu länger haltbaren Implantaten und besseren Ergebnissen für die Patienten führt.
Revolutionierung der Medizinprodukteindustrie: Die Auswirkungen von FormUp 350
Die FormUp 350 von AddUp hat die Medizinprodukteindustrie tiefgreifend verändert. Durch die Verkürzung der Vorlaufzeiten und die Verbesserung der Präzision ermöglicht es diese Maschine den Herstellern, schnell auf die Marktanforderungen zu reagieren und Produkte von höchster Qualität zu liefern. Die Möglichkeit, Gitterstrukturen zu drucken, erhöht nicht nur die Leistung der Implantate, sondern verbessert auch die Ergebnisse für die Patienten. Diese Entwicklung führt zu weniger Revisionseingriffen und damit zu Kosteneinsparungen sowohl für die Patienten als auch für die Gesundheitsdienstleister.
Schlussfolgerung
Der FormUp 350 von AddUp bietet eine Durchsatzleistung, die derzeit auf dem Markt unangefochten ist. Dies wird in der untenstehenden Hip Cup Produktivitätsstudie deutlich. Die gezeigten Teile wurden mit einer Druckwalzen-Technologie in 30um-Schichten aus Ti6Al4V ELI gedruckt. Im Vergleich zur EBM-Technologie hat das AddUp 350 eine kürzere Laufzeit von 12:41 im Vergleich zu 15:23 (EBM), was zu einem verbesserten jährlichen Durchsatz von 9.309 (16.403 LPBF, 7.094 EBM) führt. Da sich die Medizintechnikbranche ständig weiterentwickelt, unterstreicht dieser konkrete Beweis für die Überlegenheit des FormUp 350 sein transformatives Potenzial für die Zukunft der Hüftgelenkersatzoperationen und darüber hinaus.