Hohe Produktivität trifft auf serielle Additive Produktion
Diese Fallstudie befasst sich mit Tibiaplateus in der orthopädischen Fertigung und den Herausforderungen bei der Herstellung hochkomplexer und kundenspezifischer Implantate. Die additive Fertigung (AM) mit biokompatiblen Materialien wie Titan bietet eine Lösung, da sie die Herstellung einzigartiger Implantate in einem kürzeren Zeitrahmen ermöglicht.
INDUSTRY
Medical
CHALLENGE
3D print a plate of tibia implants in Titanium
KEY BENEFITS
- 3D Print customized metal parts
- Titanium is a durable & biocompatible material
- Quality and productivity improved
Custom Shape
Reduced Lead Time
Weight Reduction
Performance
Geschichte
Um die bestmögliche Patientenversorgung zu gewährleisten, muss die moderne Medizin den neuesten Stand der Technik erforschen. Die Medizinindustrie stellt hohe Anforderungen: Komplexität, Präzision der Teile, individuelle Anpassung, biokompatible Materialien und Haltbarkeit. Eine der Herausforderungen in der orthopädischen Fertigung besteht darin, ein Implantat zu entwickeln, das sich schnell in den menschlichen Körper integrieren lässt. Dies wird als Osseointegration bezeichnet und ist mit den heutigen Standardherstellungsverfahren nicht leicht zu bewerkstelligen. Einige dieser medizinischen Produkte sind speziell auf die Bedürfnisse des Patienten abgestimmt. Diese medizinischen Produkte oder Implantate, die in der Chirurgie eingesetzt werden, können individuell angepasst werden, erfordern aber eine lange Entwicklungszeit, was nicht immer zum Vorteil des Patienten ist. Die additive Fertigung (AM) ermöglicht es, einzigartige, maßgeschneiderte Metallteile in kürzerer Zeit und zu einem vernünftigen Preis herzustellen. Jedes Jahr werden mehr als 25.000 Implantate verwendet, die im 3D-Druckverfahren hergestellt wurden. Das am häufigsten verwendete Material in diesem Prozess ist Titan, da es eines der wenigen Materialien ist, das sowohl haltbar als auch für den menschlichen Körper akzeptabel ist. Aus all diesen Gründen ist der medizinische Bereich eine Schlüsselindustrie, die bei der Nutzung der AM-Technologie heute führend ist.
Herausforderungen
Der Zweck eines orthopädischen Implantats ist es, eine Knochenfunktion nahtlos für die Dauer des Lebens des Patienten zu ersetzen. Um dies zu erreichen, muss sich das Implantat vollständig in die Knochen- und Gewebestruktur des Patienten integrieren. Werden herkömmliche Produktionsmethoden angewandt, kann die Bereitstellung solcher Implantate und auf den Patienten abgestimmter Geräte sehr teuer und zeitaufwändig sein. Dank der fortschrittlichen biokompatiblen Materialien, die für die AM- Technologie zur Verfügung stehen, profitieren immer mehr medizinische Anwendungen von dieser Technologie. Aufgrund ihrer geometrischen Komplexität und des Bedarfs an biokompatiblen Materialien können diese von OEMs weltweit entwickelten medizinischen Teile nicht mit herkömmlichen Verfahren hergestellt werden.
Die Wirbelsäulenindustrie setzt AM schon seit Jahren in großem Maßstab ein. Dies ist der Größe und Menge der Implantate zu verdanken, die auf einer Bauplatte untergebracht werden können, sowie dem Volumen der vom Markt benötigten Implantate. Die nächste medizinische Anwendung, die sich für den Erfolg von AM abzeichnet, sind Tibiaplateus. Die Herausforderung bei Tibiaplateus besteht darin, dass der Durchsatz von Standard-AM-Maschinen die Herstellung einer ausreichenden Anzahl von Implantaten in verschiedenen Größen und Formen unwahrscheinlich macht. Der übergreifende Bedarf besteht darin, einen Drucker zu haben, der genügend Tibiaplateus herstellen kann, um die Anforderungen der OEMs zu erfüllen. Typische Bauplatten können nur 9-12 Tibiaplateus aufnehmen. Dies ist nicht geeignet, um den Anforderungen der Industrie gerecht zu werden, ohne dass eine beträchtliche Menge an Kapitalausrüstung hinzugefügt werden muss. Bedenken Sie, dass die durchschnittliche Größe einer Bauplatte in der Industrie etwa 290 Millimeter im Quadrat beträgt.
Lösung
Mit der AM-Technologie können hochkomplexe und individuelle medizinische Teile mit einer Gitterstruktur gedruckt werden, um die Osseointegration zu verbessern, die Produktionszeit zu verkürzen und die Oberflächenbeschaffenheit zu verbessern, um die Nachbearbeitung zu reduzieren. AM ermöglicht geometrische Komplexität, um Gitterstrukturen für medizinische Implantate zu schaffen, die eine poröse Oberfläche zur Verbesserung der Knochenintegration bei gleichzeitiger Gewichtsreduzierung des Implantats erzeugen. Bei der herkömmlichen Herstellung kann es für die Osseointegration erforderlich sein, eine Beschichtung auf das Titan aufzubringen, was teuer, zeitaufwendig und schwer zu validieren ist. Außerdem werden durch AM die Herstellungsschritte und die Anzahl der Komponenten reduziert, wodurch die Produktionszeiten und -kosten sinken.
Der AddUp FormUp® 350, ein 3D-Metalldrucker mit Pulverbettfusionstechnologie (PBF), stellt seine Fähigkeiten anhand der Qualität und Produktivität der Schienbeinschienen unter Beweis.
Die Bauplatte des AddUp FormUp® 350 ist 350 Millimeter im Quadrat groß und kann im Vergleich zu herkömmlichen Bauplatten mehr als die doppelte Menge an Tibiaplatten aufnehmen. Der Einsatz von 4 Lasern bietet ebenfalls einen deutlichen Vorteil, so dass mehr als 20 Tibiaplatten in weniger als einem Tag gedruckt werden können. Der Durchsatz ist heute ein wesentlicher Bestandteil der Fertigung.
Wenn der Platz begrenzt und die Nachfrage hoch ist, sind Maschinen wie die AddUp FormUp® 350 eine willkommene technologische Ergänzung. Die FormUp 350 nutzt eine Pulverwalzen-Technologie, die geometrische Komplexität mit minimalen Stützen ermöglicht und zu einer optimalen Oberflächengüte und einer Reduzierung der Nachbearbeitung führt. Diese Reduzierung s p a r t Zeit- und Produktionskosten.
Ergebnisse
Das auf dem FormUp 350 hergestellte Tibia-Tray-Implantat wies eine poröse Struktur und eine optimale Oberflächenbeschaffenheit auf, um die Knochenintegration insgesamt zu verbessern. Die vergrösserte Bauplatte und die Pulverwalzentechnologie ermöglichten eine höhere Produktion sowie Zeit- und Kosteneinsparungen durch weniger Nachbearbeitung.
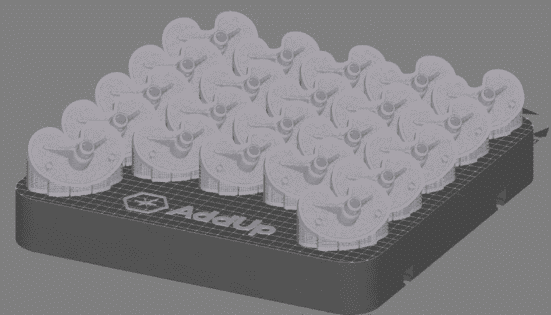
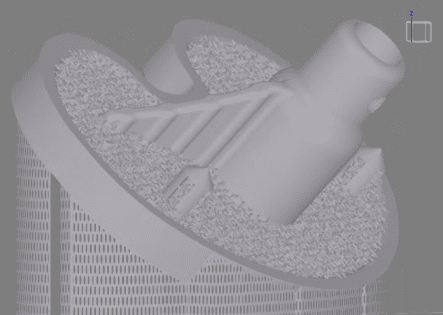
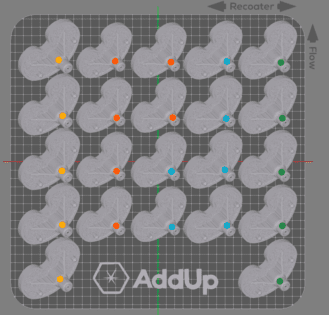
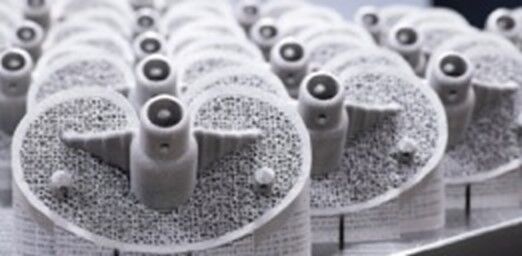
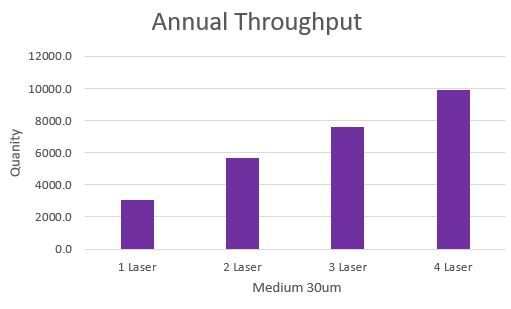
Gesteigerte Produktion – eine größere Bauplatte, weniger Komponenten und weniger Fertigungsschritte, einschließlich weniger Nachbearbeitungen, bedeuten kürzere Produktionszeiten!
Geometrische Komplexität – die AddUp FormUp® 350 bietet die Freiheit, Implantate mit Hilfe von Gitterstrukturen und Überhängen geometrisch zu optimieren, und das bei minimalen Stützstrukturen.
Reduzierung der Stützkonstruktionen – mit der AddUp FormUp® 350 sind keine umfangreichen Stützkonstruktionen mehr erforderlich, was zu einer geringeren Nachbearbeitung führt und somit Zeit und Kosten spart!
Optimales Oberflächenfinish – dank der Pulverrollentechnologie der FormUp 350 ist das Oberflächenfinish direkt aus dem Drucker ideal, was zu weniger Nachbearbeitungszeit und -kosten führt!
Funktionsintegration – das AM-Verfahren und die Materialien schaffen eine poröse Struktur und eine ideale Oberflächenbeschaffenheit, die die gesamte Knochenintegration für medizinische Anwendungen verbessert.
Biokompatible Materialien – die FormUp 350 ermöglicht die Verwendung einer Vielzahl verschiedener Materialien und hat bereits Ti64ELI sowohl für 30- als auch für 60-Mikrometer-Schichten optimiert.
Die FormUp 350 Maschine ist ideal für medizinische Anwendungen, da sie ein verbessertes und kosteneffizientes Verfahren für die Massenfertigung hochkomplexer und/oder kundenspezifischer medizinischer Teile bietet.
Volume
- Einzelner Teil: 25.604 cm3
- Vollständige Bauplatte: 25.604cm3 * 22 parts = 563.288 cm3
Bounding Box
- Mit Orientierung (Bild): 86.7 mm x 56.7 mm x 52.4 mm (XxYxZ)
1 LASER | 2 LASER | 3 LASER | 4 LASER | |
---|---|---|---|---|
Gebaute Teile pro Laser | 22 Teile | 11 Teile | 7-8 Teile | 5-6 Teile |
Bauzeit mit mittlerem 30- Mikron-Pulver (Schmelzen + recoating) | 49,36 Stunden | 28,92 Stunden | 20,91 Stunden | 16,76 Stunden |
Mittel, 30um Pulver (Stunden) | 49.36 | 28.92 | 20.91 | 16.76 |
Jährlicher Durchsatz | 2612 | 4424 | 6077 | 7536 |