Hinzufügen von Merkmalen mit gerichteter Energieabscheidung
INDUSTRIE
Luft- und Raumfahrt / Allgemein
HERAUSFORDERUNG
Kann die gerichtete Energieabscheidung eine optimierte, kosteneffiziente Lösung auf einem Markt bieten, auf dem sich das Pulverbettschmelzen bereits bewährt hat?
KEINE UNTERSTÜTZUNG
KREATIVE GESTALTUNG
REDUZIERTE VORLAUFZEIT
MASSENREDUKTION
Geschichte
Raketendüsen wurden traditionell mit subtraktiven Verfahren wie Fräsen und Drehen hergestellt, doch sind diese Techniken heute meist auf weniger komplexe Düsen beschränkt. Seit Mitte der 2000er Jahre hat sich die additive Fertigung in der Luft- und Raumfahrtindustrie unter Verwendung von Pulverbettfusionstechnologien durchgesetzt, als Luft- und Raumfahrtunternehmen begannen, die Vorteile von PBF für das Rapid Prototyping, die Herstellung komplexer Komponenten und die Produktion flugkritischer Teile zu erkennen.
Herausforderung
Mit der Pulverbettfusionstechnologie können zwar kundenspezifische, optimierte Raketendüsen hergestellt werden, doch ist es schwierig, große Komponenten zu drucken, und es fehlt die Möglichkeit, Merkmale an einem bereits vorhandenen Teil hinzuzufügen oder zu reparieren.
Lösung
Directed Energy Deposition eignet sich gut für die Herstellung größerer und sperrigerer Bauteile. Die Magic 800 wurde ausgewählt, um die Machbarkeit eines optimierten Raketendüsenkonzepts zu testen, da sie über ein großes Bauvolumen von 1200 x 800 x 800 mm verfügt und zusätzliche Merkmale hinzugefügt werden können. Da der Druck eines ganzen Triebwerkskonus mit DED allein zu teuer gewesen wäre, wurde stattdessen eine Kombination aus additiven und herkömmlichen Technologien eingesetzt. Einem traditionell hergestellten Trichterkonus wurde ein Isogitter hinzugefügt, das zur Herstellung einer extrem stabilen, aber leichten Struktur beiträgt, die in der Luft- und Raumfahrtindustrie weit verbreitet ist.
Results
Wir begannen dieses Proof-of-Concept-Projekt mit dem Kauf eines großen, vorgedrehten Trichterkonus aus Edelstahl 304 von einem lokalen Hersteller für 600 $*.
Der Konus wurde auf der Grundplatte der M800 befestigt, und die Isogitterstruktur wurde direkt auf der Oberfläche mit Pulver aus Inconel 625 verschmolzen, einem Material, das in der Luft- und Raumfahrtindustrie für seine Festigkeit und Beständigkeit gegen hohe Temperaturen bekannt ist. Für die Fertigstellung des Musters in 5-Achsen-Konfiguration mit einer Mindestwandstärke von 0,8 mm wurden insgesamt 16 Stunden benötigt.
Nach dem Abkühlen wurde das Teil aus der Maschine entnommen und die obere Spitze des Kegels abgeschnitten, um die Vasenstruktur hinzuzufügen. Dieser letzte Abschnitt wurde in nur 2 Stunden ohne jegliche Stützen gedruckt. DED hat bewiesen, dass es in der Lage ist, zwei verschiedene Materialien und Fertigungstechniken zu kombinieren, um eine kostengünstigere Lösung zu schaffen.
Die endgültige Konstruktion wurde in insgesamt 18 Druckstunden fertiggestellt und hat eine Endgröße von 32 x 30 Zoll.
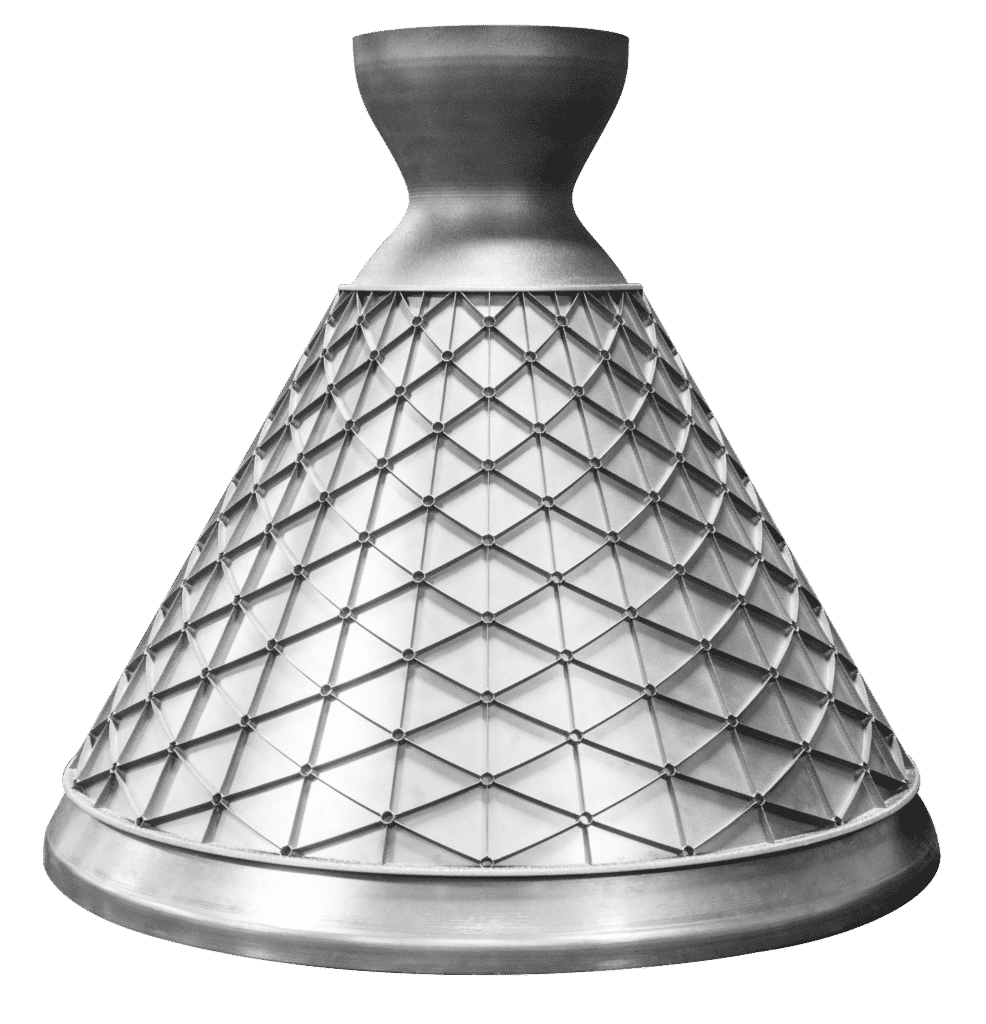
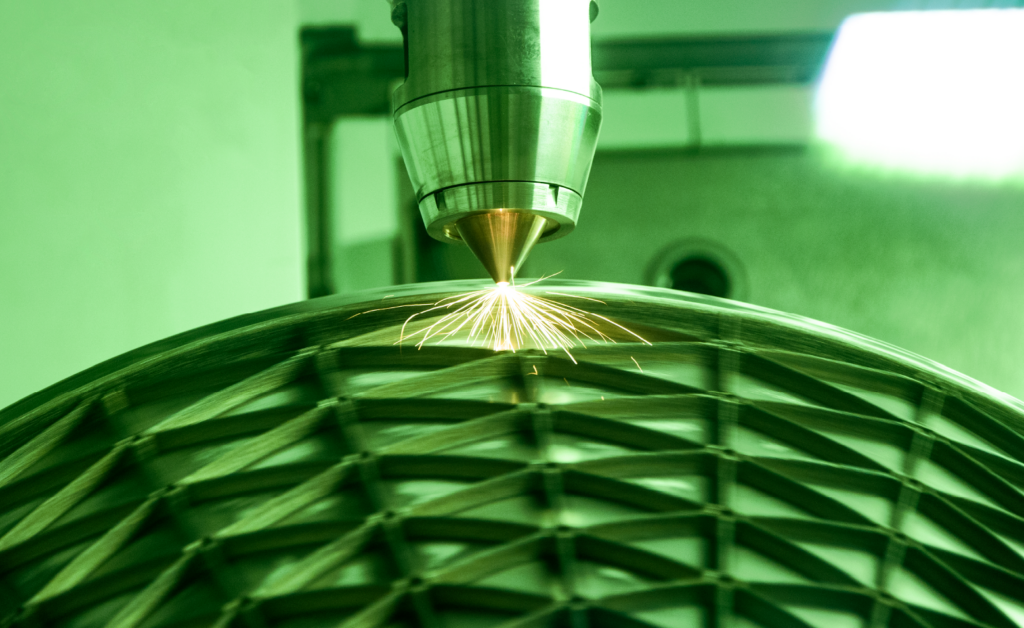
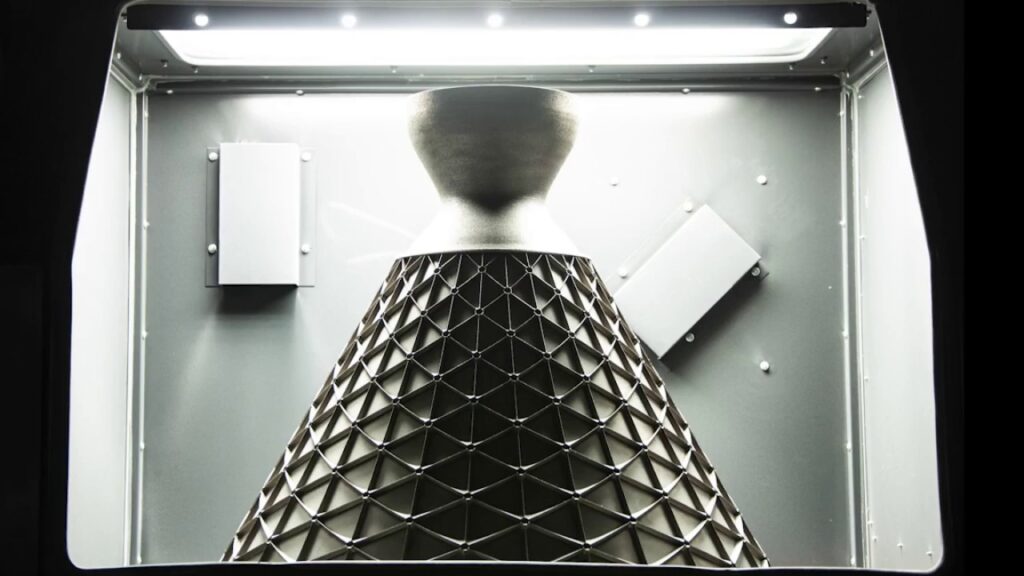
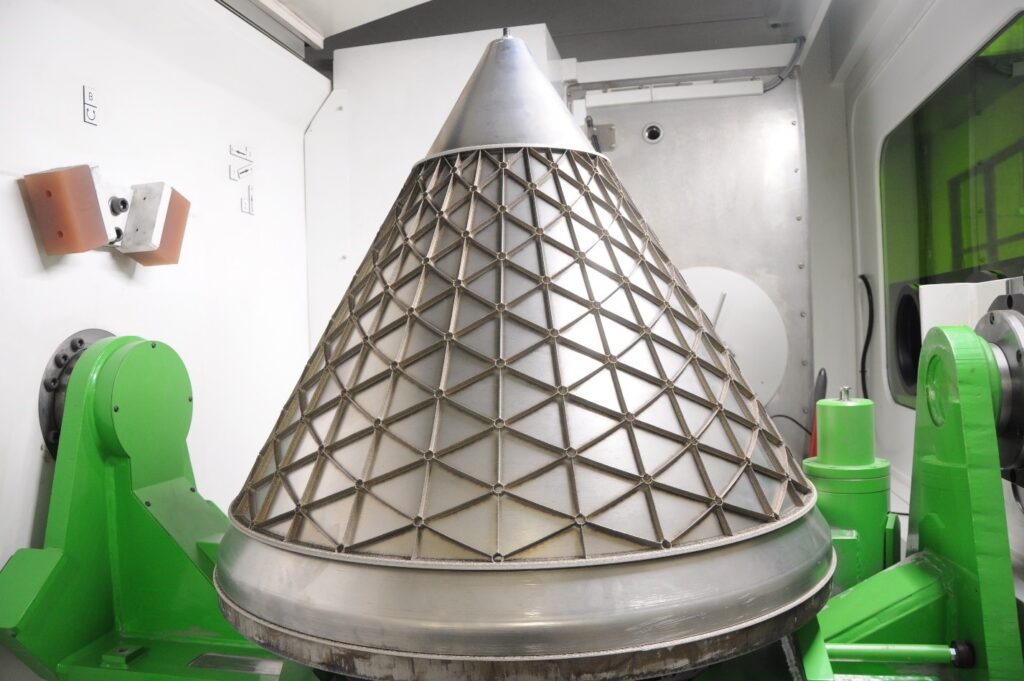
Reduziertes Gewicht
Größere Materialauswahl
Weniger Abfall