INDUSTRY
Aerospace
CHALLENGE
Reducing the mass and lead time while optimizing
an Aircraft Floor Bracket
KEY BENEFITS
- 61% mass reduction of the part
- Part printed without any supports
- Industry leading surface finish
Reduced Lead Time
No Support
Weight Reduction
Dieses von Add Up demonstrierte Proof-of-Concept zeigt den Wert des Einsatzes von Additive Manufacturing (AM) für die Luftfahrt, indem es die topologische Optimierung auf eine Flugzeugbodenhalterung anwendet.
Geschichte
Eine Flugzeugbodenhalterung sichert den Kabinenboden am Rumpf und ist in allen Flugzeugen in großen Mengen vorhanden. AddUp hat diesen Proof-of-Concept-Demonstrator entwickelt, um den Wert der Additiven Fertigung für die Luftfahrt zu veranschaulichen, indem eine topologische Optimierungsstudie ohne Stützen durchgeführt wurde. Dieses Teil wiegt traditionell etwa 3 kg und wird normalerweise aus einem 12 kg schweren Metallblock gefertigt.
Herausforderungen
Das Gewicht eines Flugzeugs stellt verschiedene Herausforderungen dar, darunter strukturelle Integrität, Treibstoffeffizienz, Nutzlastkapazität und Leistung bei Start und Landung. Übermäßiges Gewicht kann die Struktur des Flugzeugs belasten, den Treibstoffverbrauch erhöhen, die Nutzlastkapazität begrenzen und längere Start- und Landebahnen erfordern.
Sicherheitsaspekte wie Gleichgewicht und Stabilität sind entscheidend, und auch die Kosten und die Wirtschaftlichkeit des Gewichts müssen berücksichtigt werden. Um diese Herausforderungen zu meistern, konzentrieren sich Flugzeugkonstrukteure und -betreiber auf die Verwendung leichter Materialien, effizienter Konstruktionen und Betriebsverfahren, die ein Gleichgewicht zwischen Gewichtsreduzierung, Leistung und Sicherheit herstellen.
Bei den meisten 3D-Metalldruckmaschinen müssen dem Teil Stützen hinzugefügt werden, um Oberflächen mit einer Neigung von weniger als 45° gegenüber der Horizontalen herzustellen. Diese Stützstrukturen sind mit erheblichen Kosten verbunden und verlängern die Lieferzeit des Teils.
Lösung
Die Topologie-Optimierung, eine mathematische Methode, die das Material innerhalb eines gegebenen Raums mit dem Ziel der Leistungsmaximierung optimiert, wurde eingesetzt, um erhebliche Mengen an Material zu entfernen.
Zunächst wurde ein CAD-Modell erstellt, das die gewünschte Form und die Belastungsgrenzen, denen das Teil standhalten muss, enthält.
Anschließend bewerteten topologische Optimierungsalgorithmen die Spannungsverteilung im gesamten Bauteil und entfernten systematisch überschüssiges Material aus Bereichen mit geringer Spannung, während Bereiche mit hoher Spannung verstärkt wurden.
Das Ergebnis war ein leichtes Design, das die strukturelle Integrität unter den zu erwartenden Belastungen beibehält. Das Teil wurde dann auf der Pulverbettschmelzmaschine FormUp 350 gedruckt, wobei eine Kombination aus feinem Pulver und Walzen verwendet wurde, um den Bedarf an Stützen zu verringern. Diese Kombination sorgte auch für eine glatte und gleichmäßige Oberflächenbeschaffenheit, die für d a s Ermüdungsverhalten von LPBF-Bauteilen von entscheidender Bedeutung ist und den Bedarf an Nachbearbeitung reduziert.
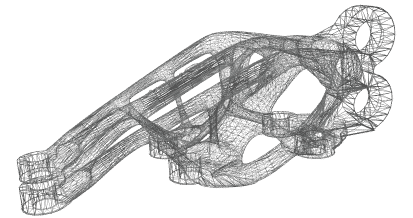
Ergebnisse
Durch die Verwendung der Kombination aus feinem Pulver und Rollertechnologie, die es nur beim FormUp 350 gibt, waren keine Stützstrukturen erforderlich; die Überhänge können bis zu 30° oder sogar 15° betragen. Durch den Wegfall der Stützstrukturen konnten 250 g Rohmaterial eingespart werden. Dies verkürzte die Bauzeit um 3 Stunden und sparte weitere 30 Minuten für die Entfernung der Stützen. Dies senkt auch die Gesamtdurchlaufzeit, eine wichtige Kennzahl in der Luft- und Raumfahrtindustrie.
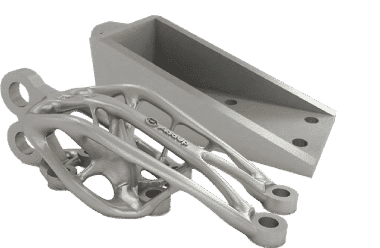
Bauzeit mit der FormUp 350 (bei 50 μm)
11.50 Stunden
Gewichtsreduzierung
Von 3 kg auf 1,17 kg Eine
Gewichtsreduktion von
61%!