Lisez cette étude de cas pour comprendre comment obtenir un échangeur de thermique aux bonnes propriétés thermiques et mécaniques, dans un délai réduit.
AddUp et PrintSky s’associent pour augmenter le niveau de préparation technologique (TRL) d’un échangeur thermique de nouvelle génération. Grâce à la fabrication additive métallique, ils ont conçu et imprimé en 3D une pièce haute performance aux géométries complexes, en aluminium. Lisez cette étude de cas pour comprendre comment obtenir un échangeur de thermique aux bonnes propriétés thermiques et mécaniques, dans un délai réduit.
INDUSTRIE
Aeronautique
CHALLENGE
Imprimer en 3D un echangeur thermique a la geometrie complexe, avec des canaux internes
KEY BENEFITS
- Bonne resistance a la corrosion
- Reduction de masse
- Liberte de design
REDUCTION DE MASSE
FORME COMPLEXE
PERFORMANCE
Histoire
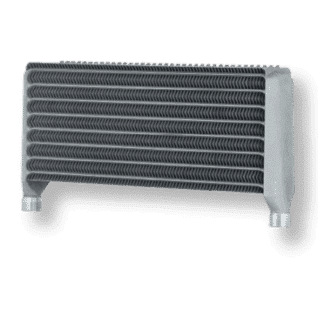
PrintSky est une joint-venture entre le groupe AddUp expert en fabrication additive métallique et Sogéclair, un des leaders internationaux dans l’intégration de solutions à haute valeur ajoutée dans les domaines de l’aéronautique, de l’espace, du transport civil et militaire. PrintSky s’est appuyé sur l’héritage de AddUp et SOGECLAIR pour augmenter le niveau de maturité technologique (TRL : Technology Readiness Level) d’un échangeur thermique nouvelle génération. Cette pièce au design innovant signé Printsky, permet l’échange thermique entre de l’eau glycolée d’un côté et un flux d’air, d’un autre. L’échangeur est destiné à être installé dans une veine d’air, dans un rack placé sur un hélicoptère.
Un échangeur thermique est un système utilisé pour transférer la chaleur entre une source et un fluide. Les échangeurs thermiques sont utilisés dans les procédés de refroidissement et de chauffage. Selon l’application, les fluides peuvent être séparés pour éviter qu’ils ne se mélangent ou ils peuvent également être en contact direct. Dans l’industrie aéronautique, les échangeurs thermiques ont pour fonction de prélever la chaleur du circuit d’huile des moteurs afin de chauffer le carburant froid.
Défi Techno
En premier lieu, il est important de savoir que la conception d’échangeur thermique par des procédés classiques d’estampage, brasage, usinage, etc, limite fortement les possibilités de design. Se libérer des contraintes de design permet de rechercher des concepts plus performants et surtout mieux adaptés à chaque cas. La fabrication additive métallique permet cette réelle liberté de design.
Par ailleurs, traditionnellement l’échangeur thermique nécessite la création d’outillages couteux. Ne plus être dépendant de ces outillages, grâce à l’impression 3D, permet de réduire les coûts et les délais de mise sur le marché.
Solution
La fabrication additive offre la possibilité de créer des échangeurs plus compacts et plus performants. Pour améliorer les performances, il faut à la fois réduire les pertes de charges lors de l’écoulement, et par ailleurs augmenter les surfaces d’échanges tout en évitant la création d’une couche limite trop épaisse. L’alliance de la connaissance en fabrication additive sur des machines FormUp®350 et des lois de thermo-fluidiques permet la création de structures innovantes capables de concilier toutes ces contraintes pour atteindre un optimum de performance.
Imprimer sur une FormUp 350, permet aussi d’optimiser les délais de production. Une mise à jour du design – par exemple : pour augmenter ou réduire la puissance d’échange – ne nécessite pas la re-conception d‘outillage, et la mise en mouvement d’une industrie lourde. Une simple actualisation du design peut être suivie d’une impression afin d’obtenir un échangeur thermique viable, dans un délai réduit.
La vaste gamme de poudre utilisable sur les machines FormUp 350 permet d’adapter le matériau au cas d’utilisation. Ici, les températures ainsi que les contraintes de masse et de corrosions nous ont mené vers l’utilisation de la poudre d’alliage d’aluminium AlSi7Mg.
Les bonnes caractéristiques mécaniques et thermiques de cet alliage, et sa fine granulométrie permettent d’atteindre des états de surfaces lisses et des épaisseurs optimisées.
Résultats
La pièce a été imprimée sur une FormUp® 350, une machine construite par AddUp, et qui utilise la technologie de fusion sur lit de poudre. Son système de mise en couche par rouleau doublé de l’usage d’une poudre à granulométrie fine permet d’imprimer des pièces avec un très bon état de surface. L’échangeur thermique est sorti avec des parois étanches, fines de 0.5 mm, ainsi que des ailettes externes de 0.2 mm et interne de 0.35 mm.
Voici les avantages à imprimer en 3D un échangeur :
- Indépendance vis-à-vis des fournisseurs
- Mise au point des systèmes facilitée
- Moins d’outillage
- Une seule conception permet de couvrir un large panel de cas d’utilisation
Le défi à relever est réussi avec la production d’une nouvelle pièce métallique optimisée, en utilisant le moins de matériau possible. De plus, la fabrication additive métallique permet à un industriel de s’affranchir des contraintes imposées par la fonderie ou la forge, et de produire des pièces performantes aux géométries complexes.