Cette démonstration de faisabilité réalisée par Add Up met en évidence l’intérêt de la fabrication additive pour l’aéronautique en appliquant l’optimisation topologique à un support de plancher d’avion.
Industrie
Aérospatiale
CHALLENGE
Optimisation d’un support de plancher d’avion en réduisant la masse et le délai de fabrication
KEY BENEFITS
- Réduction de 61% de la masse de la pièce
- Pièce imprimée sans support
- Le meilleur état de surface obtenu en 3D métal (L-PBF)
Réduction du post-traitement
Pas de support
Réduction de la masse
HISTOIRE
AddUp a développé ce démonstrateur pour illustrer à la fois l’intérêt de l’impression 3D pour l’optimisation de pièces structurelles aéronautiques et pour démontrer les avantages de la machine FormUp 350 qui permet de réaliser des pièces sans aucun support.
DÉFI
Afin d’initier les industriels de l’aéronautique aux réductions de poids rendues possibles par l’impression 3D, les ingénieurs d’AddUp ont réalisé une étude d’optimisation topologique sur un support de plancher de cabine d’avion. Cette pièce, qui fixe le plancher de la cabine au fuselage, est présente en grande quantité et dans tous les avions. Traditionnellement, cette pièce de 3 kg est usinée à partir d’un bloc de métal de 12 kg.
SOLUTION
L’optimisation topologique est une méthode mathématique qui permet d’optimiser la répartition de la matière dans un espace de conception donné et pour un ensemble donné de charges, de conditions limites et de contraintes, tout ceci dans le but de maximiser les performances du système. En appliquant cette technique, les ingénieurs d’AddUp ont réduit de 61 % le poids d’un support de plancher d’avion.
L’utilisation de la fabrication additive évite le gaspillage de matières premières, contrairement à l’usinage. Le gain total en matière première pour la pièce optimisée est de 10,83 kg. Grâce à la machine FormUp 350 d’AddUp, équipée d’une poudre fine et d’un système de recouvrement par rouleaux, le support de plancher peut être fabriqué sans aucun support.
Dans la plupart des machines d’impression 3D en métal, des supports doivent être ajoutés à la pièce pour permettre de produire les surfaces dont l’inclinaison est inférieure à 45° par rapport à l’horizontale. Ces supports représentent un coût important. Sur ce support d’avion, les supports représenteraient une perte de 250 g de matière première. De plus, le gain de temps de fabrication est important : la présence de supports aurait ajouté trois heures au temps de production, et 30 minutes supplémentaires auraient été nécessaires pour retirer ces supports par usinage en post-process.
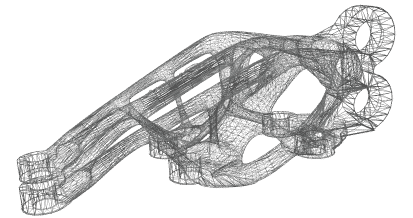
RÉSULTATS
Grâce au dispositif de mise en couche par rouleaux de la FormUp 350, aucun support n’est nécessaire, ce qui réduit le temps de construction de 3 heures et évite les temps de dé-supportage en post-process. Cela permet de réduire les délais d’exécution, un paramètre important dans l’industrie aéronautique.
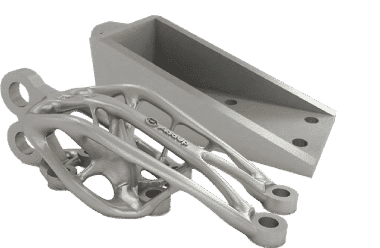
Temps de construction sur le FormUp 350 (à 50 μm)
11,50 heures
Réduction du poids
De 3 kg à 1,17 kg
Une réduction de poids de 61% !
Économies de matières premières
10,83 kg
Temps gagné
3+ heures