Comment le processus de rétro-ingénierie couplé à l’impression 3D métal a permis de produire à l’identique une pièce stratégique et durable pour un bateau.
CHALLENGE
Reproduire à l’identique une pièce plus en stock.
SOLUTION
Rétroconception de la pièce (d’un dessin manuel à un fichier CAO numérique) et impression 3D avec la machine de fusion sur lit de poudre FormUp 350® d’AddUp.
KEY BENEFITS
- Tolérances : +-0.4mm, selon la demande
- Caractéristiques mécaniques similaires, meilleure durabilité
- Equilibrage global maintenu de la pièce imprimée
Custom Shape
Lead Time
Integrated Features
Performance
Contexte
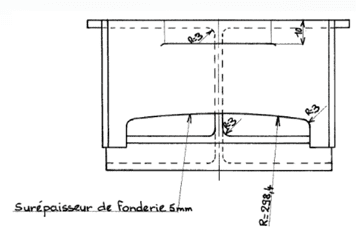
Le Ministère des Armées a créé en 2018 l’agence innovation de défense pour favoriser l’innovation dans les armées, une priorité pour y diffuser les dernières technologies plus rapidement. Sous cette impulsion, les divers services se sont tous dotés de cellules pour dynamiser l’innovation adaptée à chaque métier. Le Service de Sou-tien à la Flotte (SSF) a mis aussi en place une telle structure depuis 2020 chargée de piloter les innovations pour le maintien en condition opérationnelle des navires de la flotte.
Une des problématiques de la Marine consiste à déterminer com-ment produire une pièce métallique nécessaire et en rupture de stock. Pour répondre à cette demande, la Marine (le SSF et le Service logistique de la Marine (SLM)) avait besoin de s’appuyer sur un groupe industriel solide maîtrisant toute la chaîne de valeur. C’est la raison pour laquelle la Marine s’est tournée vers AddUp, fabriquant de machines et de pièces, expert en impression 3D métallique.
Pour cette mission, la Marine a choisi un racleur d’huile des paliers porteurs de la ligne d’arbre d’hélice d’une Frégate, pièce dont le rôle est important dans le graissage continue des paliers porteurs. Des contacts répétés avec le disque de barbotage d’une part et le corps de paliers d’autre part, peuvent conduire à une usure prématurée. Cette pièce est indispensable au fonctionnement de la Frégate. Cette pièce a l’intérêt de ne pas présenter de contrainte mécanique critique pour la sécurité du navire ce qui autorise une telle tentative de production expérimentale. Enfin, le faible stock de rechanges a été un élément complémentaire et motivant pour le choix de cette pièce.
Les advnatages de la fabrication additive
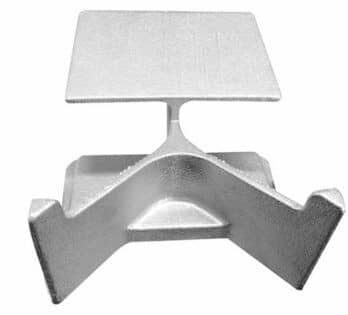
Ainsi une pièce à l’identique a été imprimée en 3D, en aluminium. La pièce d’origine était moulée sur une épaisseur de fonderie et avait besoin d’usinage, ce qui rallongeait le délai de production. La nou-velle pièce a été produite en une seule fois, en un seul bloc, donc avec un gain de temps significatif. Le recours à une FormUp 350, couplé à un moyen de dépose de poudre fine au rouleau, a permis de produire une pièce dotée d’une précision géométrique d’un très bon état de surface (supérieur à la fonderie) afin de minimiser les étapes de post-traitement. Addup a maîtrisé la chaîne complète de réali-sation : conception, fabrication additive, post-traitement et contrôle qualité.
« L’expérimentation de fabrication additive métallique avec AddUp s’est déroulée de manière optimale. Les tests d’endurance sur navire étant positif, AddUP est doré-navant référencé comme fournisseur de racleurs au même titre que d’autres four-nisseurs qui produisent ce matériel avec des techniques classiques. L’analyse des couts montre que ce mode de produc-tion est compétitif. Le délai de livraison est similaire voire inférieur. La collabora-tion a été parfaite et permet d’envisager d’autres cas d’application.»
~ Jean-Marc QUENEZChargé de mission innovation performanceService de Soutien de la FlotteMarine Nationale
Les advantages d’AddUp
La fine granulométrie de la poudre utilisée dans la machine FormUp 350 couplée à l’utilisation d’un rouleaupermettent d’imprimer des pièces avec un excellent état de surface.