L’objectif est de démontrer l’intérêt de la technologie PBF pour créer des échangeurs de chaleur plus compacts, ayant de bonnes performances thermiques et imprimés en 3D en une seule fois.
Répondre aux problématiques thermiques de l’industrie aérospatiale par la technologie de fusion sur lit de poudre (procédé PBF), c’est ce que proposent Temisth et PrintSky – la Joint-Venture AddUp SOGECLAIRE – dans le cadre d’un partenariat avec l’Agence spatiale européenne. Dans cette étude, l’objectif était de répondre aux besoins de l’industrie spatiale. La pièce a été produite en aluminium sur une machine FormUp 350® fournie par AddUp.
OBJECTIF
Développer un échangeur de chaleur utilisant tout le potentiel du procédé PBF
RÉSULTATS
- Bonne performance thermique pour un volume réduit par rapport aux échangeurs » classiques « .
- Imprimé en une seule fois
DIMENSIONS
116x116x60 mm Masse : 244 g Puissance de l’échangeur : 2,3 kW (résultat simulé)
AVANTAGES DE L’IMPRESSION 3D MÉTAL:
La fabrication additive est pertinente pour les équipements thermiques. Elle permet de créer des canaux aux formes complexes, et donc d’améliorer les performances thermiques tout en diminuant le volume.
Cet échangeur thermique présente des parois fines (250 µm) et des canaux à double courbure impossibles à réaliser par des techniques conventionnelles.
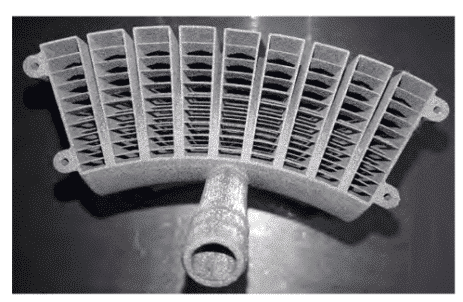
Les tests réalisés sur banc d’essai ont permis de valider l’étanchéité de la pièce, ainsi que ses performances, très élevées au vu de la compacité de l’échangeur.
PrintSky a obtenu un accord de partenariat avec l’ESA (Agence Spatiale Européenne) pour le développement de cette pièce en aluminium.