Dans tous les secteurs de la fabrication, la sécurité doit être une priorité absolue. C’est certainement le cas dans le monde beaucoup plus récent de la fabrication additive métallique. Dans notre domaine, la majorité des risques provient de l’utilisation de la poudre métallique – à la fois sous sa forme brute et dans le sous-produit de condensation qu’elle produit au cours du processus de fusion. L’utilisation d’une matière première fine, dont les plus petites particules sont de l’ordre de 1 micron, permet d’obtenir des caractéristiques fines et d’autres libertés de conception, mais présente également la plupart des risques de sécurité auxquels nous sommes confrontés dans le cadre de la fusion sur lit de poudre. Michelin a lancé AddUp pour assurer l’avenir de la fusion sur lit de poudre, et nous examinerons ici son influence sur l’amélioration des caractéristiques de sécurité des flottes de machines les plus récentes.
La poudre de métal sous sa forme brute est dangereuse au toucher et dans l’air. Certaines particules sont suffisamment fines pour que la peau humaine ne serve pas de barrière, de sorte que la poudre sert de récipient aux métaux lourds pour se frayer un chemin à l’intérieur du corps. Les particules les plus fines restent également plus longtemps dans l’air, où elles peuvent pénétrer par les poumons. La sécurité des employés et des clients étant toujours au centre des préoccupations d’AddUp, la conception de toute imprimante 3D utilisée dans ses locaux devait atténuer ces risques pour la santé de ses employés.
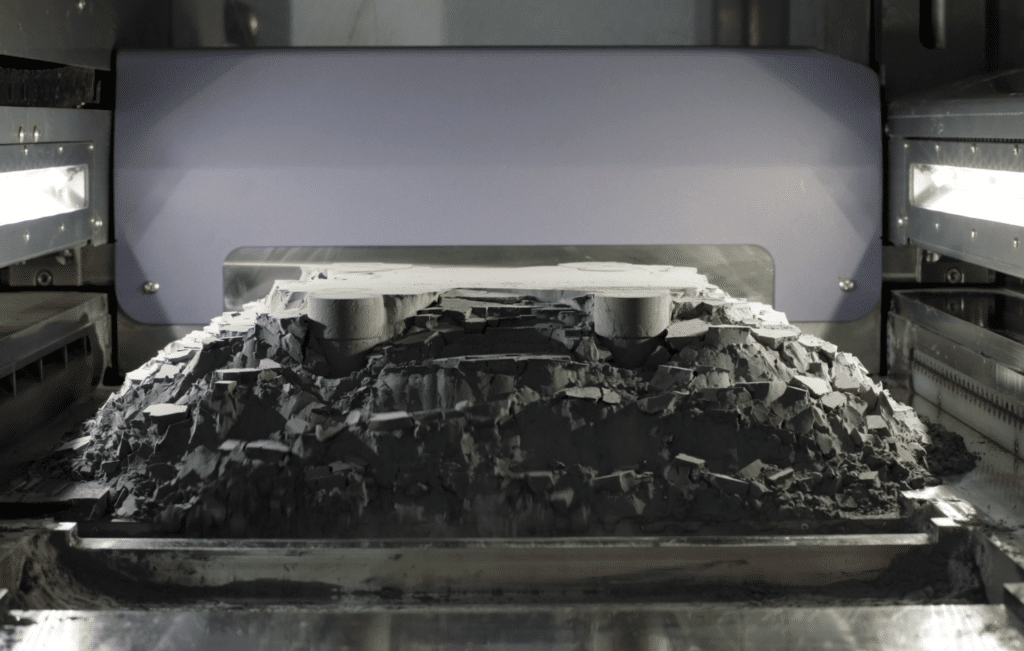
La question qui se pose alors est la suivante : comment minimiser l’exposition de l’opérateur à la poudre sans sacrifier aucune fonctionnalité de la machine ? La réponse d’AddUp est le module de poudre autonome, le système de manutention de la poudre sur la Form Up 350. Les principaux composants de l’APM sont la boîte à gants, la trémie, le tamis et le système d’alimentation, qui sont tous maintenus inertes. La poudre est chargée dans la boîte à gants de l’APM et transférée par aspiration dans la trémie, d’une capacité de 59 litres. Avant la construction, la poudre sort de la trémie et passe à travers le tamis, le système d’alimentation fournissant la poudre tamisée à l’intérieur de la chambre de construction de Form Up.
Une fois la fabrication terminée, l’opérateur aspire la poudre restante à l’aide d’une buse intérieure, renvoyant ce matériau dans la trémie où il peut être utilisé pour la fabrication suivante. L’APM contribue à maintenir un environnement sûr en séparant l’opérateur de la poudre et en maintenant la poudre à l’écart de l’oxygène à tout moment.
Le produit le plus dangereux de la fusion en lit de poudre est le condensat formé pendant le processus de fusion. Le condensat est inflammable, présente un risque d’explosion et réagit facilement avec l’oxygène – le pire scénario étant celui où le titane est le matériau de base. Une solution courante consiste à utiliser des filtres en papier, mais ceux-ci doivent être entretenus et remplacés par une personne. Ces changements de filtres sont à l’origine de nombreux incidents de sécurité. Ce risque a incité AddUp à abandonner les filtres en papier et à s’associer à Herding Filtration. Avec le système Herding, les fumées sont collectées dans le module de fluides et distribuées dans une poubelle métallique (toutes deux maintenues inertes). En plus du condensat, du carbonate de calcium est utilisé pour passiver la substance dangereuse et empêcher toute réaction. Le remplacement du bac à poussière est un processus simple qui prend 1 à 2 minutes et qui est beaucoup plus sûr que le remplacement d’un filtre. Les bacs à poussière sont remplacés environ deux fois par mois, en fonction de l’utilisation de la machine, et le reste du module de fluide peut rester plusieurs années sans entretien.
La gestion des poudres est peut-être l’aspect le plus important de la sécurité dans le domaine de l’AM des métaux, mais d’autres caractéristiques de la machine peuvent également favoriser un lieu de travail sûr. Au fur et à mesure que l’industrie s’est développée et que des utilisateurs experts sont apparus, leurs commentaires ont été utilisés pour incorporer des idées qui répondaient à leurs points faibles. AddUp a facilité le nettoyage de l’intérieur de la chambre de fabrication en intégrant plusieurs portes d’accès. Cela permet d’essuyer et de nettoyer en profondeur l’ensemble de l’intérieur sans avoir à s’étirer pour atteindre les coins arrière. De même, les lentilles laser sont amovibles afin de pouvoir être nettoyées à l’extérieur de la machine. Du point de vue du logiciel, les points de consigne de l’oxygène et les alarmes sont définis lors de la création du fichier de construction, de sorte qu’ils peuvent être personnalisés pour alerter l’opérateur de tout problème potentiel, ou s’arrêter s’il devient un problème de sécurité.
Comme toute nouvelle technologie prometteuse, la technologie additive pour les métaux présente des avantages extrêmement attrayants. L’industrie s’efforce constamment d’extraire tout ce qu’elle peut de ces machines sans mettre qui que ce soit en danger. Les machines et les processus doivent tous être conçus en tenant compte de la sécurité, mais même des mesures de protection avancées ne remplacent pas des opérateurs responsables, des EPI adéquats et une installation appropriée.