Cette étude de cas se concentre sur les plateaux tibiaux dans la fabrication orthopédique et les défis rencontrés dans la production d’implants hautement complexes et personnalisés. La fabrication additive (AM) utilisant des matériaux biocompatibles comme le titane offre une solution en permettant la production d’implants uniques dans un délai plus court.
Industrie
Médical
CHALLENGE
Imprimer en 3D une plaque d’implants de tibia en titane
KEY BENEFITS
- Impression 3D de pièces métalliques personnalisées
- Le titane est un matériau durable et biocompatible
- Amélioration de la qualité et de la productivité
Formes complexes
Temps de production
Réduction de poids
Performance
Histoire
Pour garantir aux patients les meilleurs soins possibles, la médecine moderne doit exploiter les technologies les plus avancées. L’industrie médicale a des exigences élevées : complexité et précision des pièces, personnalisation, biocompatibilité des matériaux et durabilité. Des exigences que les techniques de fabrication conventionnelles peuvent difficilement satisfaire. Le domaine de la chirurgie orthopédique est particulièrement concerné, car il s’agit de réaliser des implants capables de s’intégrer rapidement et durablement dans le corps humain, ce que l’on appelle l’ostéointégration, et qui nécessite de générer des surfaces d’une grande complexité. En outre, les patients ont besoin d’implants personnalisés, mais pour toutes les interventions urgentes les chirurgiens ne peuvent se satisfaire de délais de plusieurs semaines. La fabrication additive permet de produire des pièces métalliques complexes et personnalisées en un temps réduit et pour un prix raisonnable. Plus de 25 000 prothèses imprimées en 3D sont implantées chaque année dans le monde. Le matériau le plus couramment employé est le titane, car il a la caractéristique d’être à la fois léger, résistant et acceptable par le corps humain. Pour toutes ces raisons, le domaine médical est un secteur dans lequel l’impression 3D métallique connaît un très fort développement.
Défi technique
L’objectif d’un implant orthopédique est de remplacer une fonction osseuse de manière transparente pour toute la durée de vie du patient. Pour ce faire, l’implant doit s’intégrer totalement à la structure osseuse et tissulaire du malade. Si des méthodes de production traditionnelles sont utilisées, la fourniture de tels implants et de dispositifs adaptés au patient peut être très coûteuse et prendre beaucoup de temps.
L’industrie médicale utilise la fabrication additive métallique à grande échelle depuis quelques années car cette haute technologie permet de créer des implants aux géométries complexes, avec différents états de surface, en utilisant des métaux biocompatibles. Ces pièces imprimées en 3D sont impossibles à produire avec des technologies traditionnelles.
L’une des applications émergentes de l’impression 3D orthopédique est la fabrication de plateaux tibiaux, qui remplacent la partie supérieure du tibia.
Le défi, pour les industriels qui réalisent ces implants tibiaux, est qu’il s’agit de pièces relativement encombrantes, donc difficiles à imprimer avec un bon niveau de rentabilité. En effet, la taille moyenne des plateformes de fabrication additive métallique est d’environ 290 millimètres (11,5 pouces) de côté. Avec entre 9 et 12 prothèses fabriquées par jour, les industriels ne peuvent ni répondre à la forte demande des chirurgiens ni rentabiliser leur investissement dans la machine de fabrication additive métallique.
SOLUTION
La fabrication additive métallique permet de fabriquer des implants personnalisés dont les surfaces sont recouvertes d’une fine structure en treillis. Ce type de structure présente des intérêts multiples : elle favorise l’ostéointégration, elle permet d’obtenir des implants plus légers, et elle est plus rapide à fabriquer qu’un volume de matière dense. Surtout, elle est directement fonctionnelle en sortie d’impression, et ne nécessite aucun traitement de surface.
Pour obtenir des surfaces aux propriétés similaires par des techniques conventionnelles, il faudrait appliquer aux pièces différents traitements de surfaces à la fois longs et coûteux à réaliser.
La FormUp® 350, une imprimante 3D AddUp utilisant la technologie de fusion sur lit de poudre (PBF), montre ses capacités à travers la qualité et la productivité des plateaux de tibias.
Le plateau de production de la FormUp 350 mesure 350 millimètres carrés et peut contenir plus de deux fois plus de plateaux de tibias que les plaques de construction typiques disponibles. L’utilisation de 4 lasers offre également un avantage concurrentiel car il permet l’impression de plus de 20 plateaux de tibias en moins d’une journée. Le rendement fait partie intégrante de la fabrication aujourd’hui. La FormUp 350 utilise un système d’étalement de poudre par rouleau qui autorise une grande liberté géométrique avec un minimum de supports. Il permet d’obtenir des surfaces peu rugueuses, donc de réduire les coûts d’usinage après impression.
Résultats
Le plateau d’implants de tibia fabriqué sur le FormUp 350 a présenté une structure poreuse et un état de surface optimale pour améliorer l’intégration osseuse globale. Le système de mise en couche par rouleau a permis d’augmenter la productivité et réduit le post-traitement, ce qui permet d’économiser du temps et de l’argent.
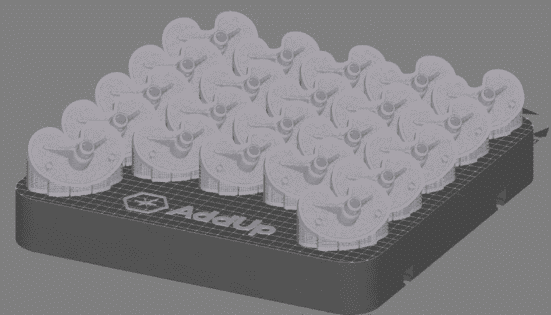
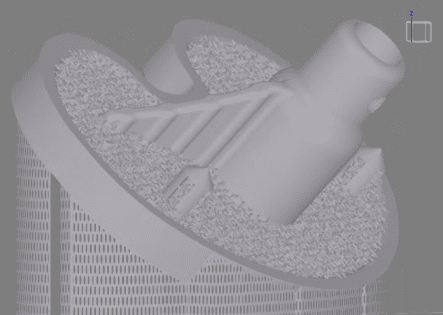
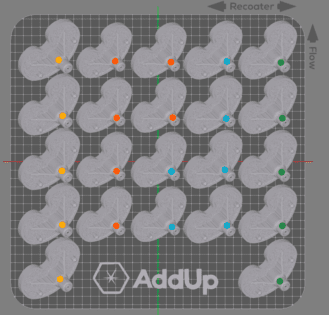
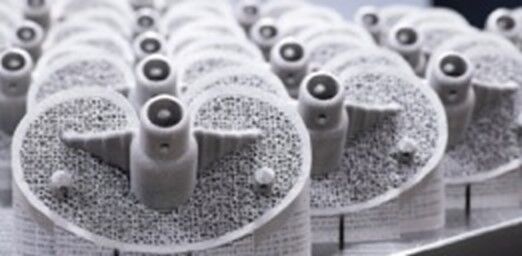
ANNUAL THROUGHPUT PER LASER BAR GRAPH
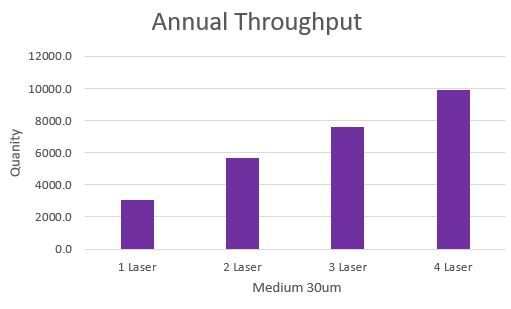
-
Production accrue – un plateau de fabrication plus grand, moins de composants et moins d’étapes de fabrication, y compris moins de post-traitement, signifient que les temps de production sont raccourcis !
-
Complexité géométrique – la FormUp 350 offre la liberté de concevoir des implants à géométrie optimisée en utilisant des structures en treillis et des surplombs, le tout en minimisant le nombre de de supports.
-
Réduction des structures de support – avec la FormUp 350, les structures de support ne sont plus nécessaires, ce qui permet de réduire l’usinage post-traitement, et donc de gagner du temps et de l’argent !
-
État de surface optimal – grâce à la mise en couche par rouleau dans la FormUp 350, l’état de surface est idéale dès la sortie de l’imprimante, ce qui permet de réduire le temps et les coûts de post-traitement !
-
Intégration fonctionnelle – la fabrication additive crée une structure poreuse et un état de surface idéale qui améliorent l’intégration osseuse globale pour les applications médicales.
-
Matériaux biocompatibles – la FormUp 350 permet d’utiliser une variété de matériaux différents et a déjà optimisé le Ti64ELI (couches de 30 et 60 microns).
La machine FormUp 350 est une solution parfaitement adaptée aux applications médicales, car elle offre aux industriels de ce secteur la possibilité de réaliser en grande série, avec un haut niveau de productivité et de rentabilité, des prothèses à la fois complexes et personnalisées.
Volume
- 1 pièce
- 25,604 cm3
- Le plateau complet
- 25,604 cm3 x 22 pièces = 563,288 cm3
- Bounding Box avec orientations (image)
- 86,7 mm x 56,7 mm x 52,4 mm (XxYxZ)
- Pièces imprimées selon le nombre de laser
- 1 Laser – 22 pièces
- 2 Lasers – 11 pièces
- 3 Lasers – 7-8 pièces
- 4 Lasers – 5-6 pièces
- Temps de production avec une poudre moyenne (30-micron)
- 1 Laser – 49,36 heures
- 2 Lasers – 28,92 heures
- 3 Lasers – 20,91 heures
- 4 Lasers – 16,76 heures
- Capacité annuelle par laser
- Fonctionnement d’une équipe par jour pendant 52 semaines par an
- 1h à 1h30 de délai entre deux productions
Powder | 1 LASER | 2 LASER | 3 LASER | 4 LASER |
---|---|---|---|---|
Medium, 30um powder (hrs) | 49,36 | 28,92 | 20,91 | 16,76 |
Annual throughput | 2612 | 4424 | 6077 | 7536 |