Pour l’industrie médicale qui souhaite fabriquer des implants chirurgicaux par impression 3D de métal, de nombreux critères sont à prendre en compte : qualité, sécurité, productivité et traçabilité. Lisez ce blog pour en savoir plus sur l’utilisation de l’AM dans l’industrie médicale.
Qualité, sécurité, productivité, traçabilité… Pour les industriels du médical qui souhaitent fabriquer des implants chirurgicaux par impression 3D métallique, les critères de choix sont nombreux. Dans ce domaine, la machine FormUp® 350 d’AddUp a de nombreux atouts à faire valoir.

FormUp® 350
Le marché des prothèses et implants chirurgicaux est en pleine mutation. Les industriels de ce secteur cherchent à fournir aux médecins des dispositifs toujours plus performants et personnalisés, à des coûts acceptables pour les patients, tout en respectant des exigences de certification particulièrement sévères. Aujourd’hui, les nouvelles générations d’imprimantes 3D atteignent de hauts niveaux de productivité et de qualité, et peuvent produire des pièces dans des matériaux biocompatibles. Elles permettent aux fabricants d’implants d’envisager la migration vers la fabrication additive métallique pour de nombreuses applications.
Des implants imprimés en 3D
Les implants chirurgicaux sont des dispositifs médicaux qui ont la particularité de devoir s’adapter à la morphologie de chaque patient. De plus, leurs surfaces doivent être spécialement étudiées pour s’intégrer à la structure osseuse du patient (on parle d’ostéo-intégration, pour désigner la capacité de l’implant à favoriser une reconstruction solide et durable des os et des tissus). Pour ces raisons, les implants réalisés par des techniques conventionnelles, comme l’usinage, sont très onéreux. En effet, le besoin d’implants personnalisés impose aux fabricants de prévoir de nombreuses variantes pour chaque modèle, avec les outillages associés. Et les surfaces favorisant la reconstruction des tissus s’obtiennent par des traitements de surfaces additionnels à la fois longs et complexes à réaliser.
A l’inverse de l’usinage, l’impression 3D métallique est particulièrement adaptée à la fabrication de pièces complexes et personnalisées. C’est la raison pour laquelle les industriels du médical s’intéressent de près à cette technologie, depuis son apparition au début des années 2000. Les premières applications ont tardé à émerger, d’une part car les autorités de certification médicales imposent des contraintes drastiques en termes de sûreté et de qualité, d’autre part car les niveaux de productivité et de répétabilité des machines ne permettaient pas aux industriels de rentabiliser leurs investissements. Mais ces dernières années, grâce aux progrès récents accomplis par les fabricants de machines d’impression 3D métallique, les applications se multiplient, et la technologie se diffuse rapidement dans tout le secteur.
»Liens vers le case study dans le domaine médical.
Qu’est-ce qu’une machine pensée pour le secteur médical ?
La machine FormUp 350 présente de nombreux atouts pour répondre aux attentes des fabricants d’implants chirurgicaux. Conçue et produite par AddUp, une société créée par les groupes français Michelin et Fives, cette machine est basée sur le principe de la fusion laser sur lit de poudre (L-PBF, pour Laser Powder Bed Fusion). Ce procédé est particulièrement adapté à la réalisation de pièces métalliques complexes, personnalisées, avec des caractéristiques mécaniques élevées. C’est aussi l’une des technologies les plus matures sur le marché de l’impression 3D métallique. En outre, plusieurs constructeurs, dont AddUp, proposent des recettes pour l’utilisation de matériaux biocompatibles, tels que les alliages de titane, et plus particulièrement le titane ELI qui est couramment utilisé pour la fabrication d’implants chirurgicaux.
La FormUp 350 se distingue néanmoins de la plupart des machines du marché par certains aspects :
-La capacité à mettre en œuvre des poudres fines. L’utilisation de poudres métalliques de faible granulométrie (inférieure à 25 microns) permet d’envisager des pièces comportant à la fois des surfaces peu rugueuses, des surfaces poreuses, et des surfaces de type « treillis » qui favorisent l’ostéo-intégration.
-La capacité d’utiliser différents dispositifs d’étalement de poudre, dont le dispositif à rouleau. Associé à des poudres fines, ce dernier permet de créer un lit de poudre à la densité élevée, propice à la fabrication de pièces sans support, ce qui réduit fortement les coûts liés aux opérations de post-traitement.
-La capacité à traiter des poudres réactives avec un haut niveau de sécurité. Les alliages de titane, sous la forme de poudres fines, présentent des risques pour les installations comme pour les opérateurs. La FormUp® 350 est la seule machine du marché à permettre l’approvisionnement et le recyclage de la poudre sans aucun contact avec l’air ambiant, ce qui limite les risques d’explosion tout en réduisant l’apparition de défauts dans les pièces.
Au-delà de ces caractéristiques, les machines L-PBF d’AddUp peuvent répondre aux attentes des professionnels des implants étant donné leurs performances en termes de productivité, de qualité, de répétabilité et de traçabilité.
Critères de productivité
Développée par un industriel pour des industriels, la machine FormUp 350 est pensée pour offrir une productivité élevée. D’abord, grâce à l’utilisation de plateaux de grandes dimensions (350 x 350 mm), avec un système de chargement rapide par le dessous qui évite toute perte de surface utile. Ensuite, par la présence de quatre lasers de 500 watts, capables de couvrir toute la surface du plateau. L’avantage pour l’utilisateur est une grande souplesse dans le placement des pièces sur le plateau, et dans l’affectation des lasers aux pièces à fabriquer, avec un ou plusieurs lasers par pièce.
Pendant la fabrication, la machine réduit les temps non productifs grâce à un système d’étalement de poudre bidirectionnel, environ 40 % plus rapide qu’un dispositif d’étalement conventionnel. Les temps d’attente entre deux productions sont également raccourcis au maximum, grâce à des temps d’inertage très courts (de l’ordre de 15 minutes pour atteindre 500 ppm, soit 0,05 % d’oxygène dans l’enceinte), grâce à un système de refroidissement actif de l’axe Z (la plupart des industriels qui impriment du titane chauffent les plateaux pour limiter les contraintes liées aux variations thermiques), mais aussi grâce à un système de référencement rapide des plateaux (quelques secondes suffisent pour mesurer la hauteur de la plateforme), et à une fonction d’aspiration intégrée à l’enceinte de fabrication, entre autres. Les fonctions d’approvisionnement de poudre neuve, tout comme la prise d’échantillons de poudre, se font évidemment en temps masqué, sans interrompre la production.
Critères de qualité
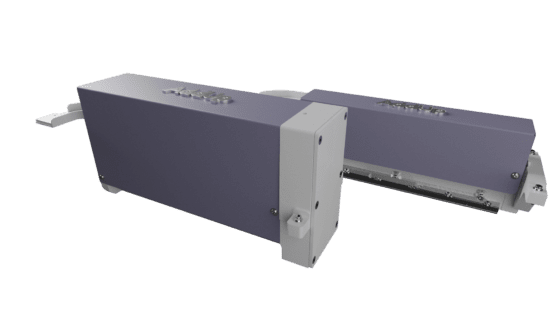
AddUp a mis au point plusieurs technologies pour garantir la qualité des pièces produites. Certaines de ces technologies sont actives. C’est le cas du système de contrôle de la qualité de mise en couche, qui analyse en temps réel l’état de surface du lit de poudre. Des algorithmes développés en interne attribuent un score de qualité à chaque nouvelle couche de poudre. Dès lors qu’un défaut est détecté, qu’il s’agisse d’un dépôt intempestif ou d’un manque de poudre, le système est capable de relancer immédiatement un nouveau cycle d’étalement de poudre. Ce dispositif n’impacte pas la productivité, car l’analyse s’effectue en quelques dixièmes de seconde. Mais surtout, il évite qu’un lot complet de pièces soient mises au rebut, ce qui est le cas lorsque les défauts de mise en couche sont détectés après l’impression.
Parmi les autres technologies actives, citons le système de captation des fumées, qui évite d’éventuelles dérives liées à l’encrassement des filtres grâce à un système de nettoyage automatique des filtres, ainsi que le dispositif Cross Jet qui assure une propreté constante des vitres lasers pendant la fabrication.
Les machines FormUp proposent également des technologies passives pour le contrôle a posteriori de la qualité des pièces produites. Le système baptisé « Monitoring de fusion » est capable de mesurer trois paramètres essentiels de la fabrication, que sont la variation de position du laser par rapport à sa position théorique, la variation de la puissance délivrée par le laser par rapport à la puissance théorique, et la température du bain de fusion. Toutes ces données sont collectées en continu pendant l’impression, et sont ensuite cartographiées et superposées aux modèles 3D des pièces. Cela permet non seulement de détecter d’éventuels défauts, mais aussi de les situer avec une grande précision pour savoir quelles pièces sont impactées, et si le défaut doit entraîner une mise au rebut de la pièce. En effet, un défaut survenu sur un support, par exemple, pourrait être considéré comme acceptable du point de vue de l’application.
Surveillance du recouvrement
Critères de répétabilité
Les industriels du médical sont soumis à des contraintes extrêmement sévères pour la qualification de leurs applications. Les procédures pour l’obtention d’un dossier de certification, comparables à celles en vigueur dans le secteur aéronautique, sont difficiles à obtenir et imposent aux industriels de mettre sous contrôle l’ensemble des paramètres de fabrication : il s’agit de prouver que le procédé est capable de délivrer des pièces conformes et que cette qualité sera maintenue dans le temps.
Parmi les technologies embarquées dans la FormUp 350 et qui contribuent à la répétabilité de la production, citons les systèmes laser à scanners « 3 axes ». Contrairement aux systèmes passifs qui déforment le plan focal du faisceau laser, les systèmes 3 axes sont capable d’ajuster dynamiquement la longueur focale du faisceau pour garantir une qualité de focalisation homogène en tout point du plateau, et donc une qualité de fusion uniforme quelle que soit la position de la pièce sur le plateau.
De même, le module chargé de la gestion de la poudre s’assure que cette poudre est systématiquement tamisée et séchée avant d’être envoyée dans l’enceinte de fabrication, ce qui évite les variations des propriétés de la poudre qui peuvent survenir lorsque la poudre est stockée dans différents conteneurs.
Enfin, le dispositif d’étalement par rouleau, parce qu’il participe directement de la géométrie de la surface du lit de poudre, est beaucoup plus répétable qu’un système d’étalement par racleur pour lequel une mauvaise manipulation par l’opérateur pourrait entraîner d’importantes variations de la forme du lit de poudre d’une production à une autre.
Critères de traçabilité
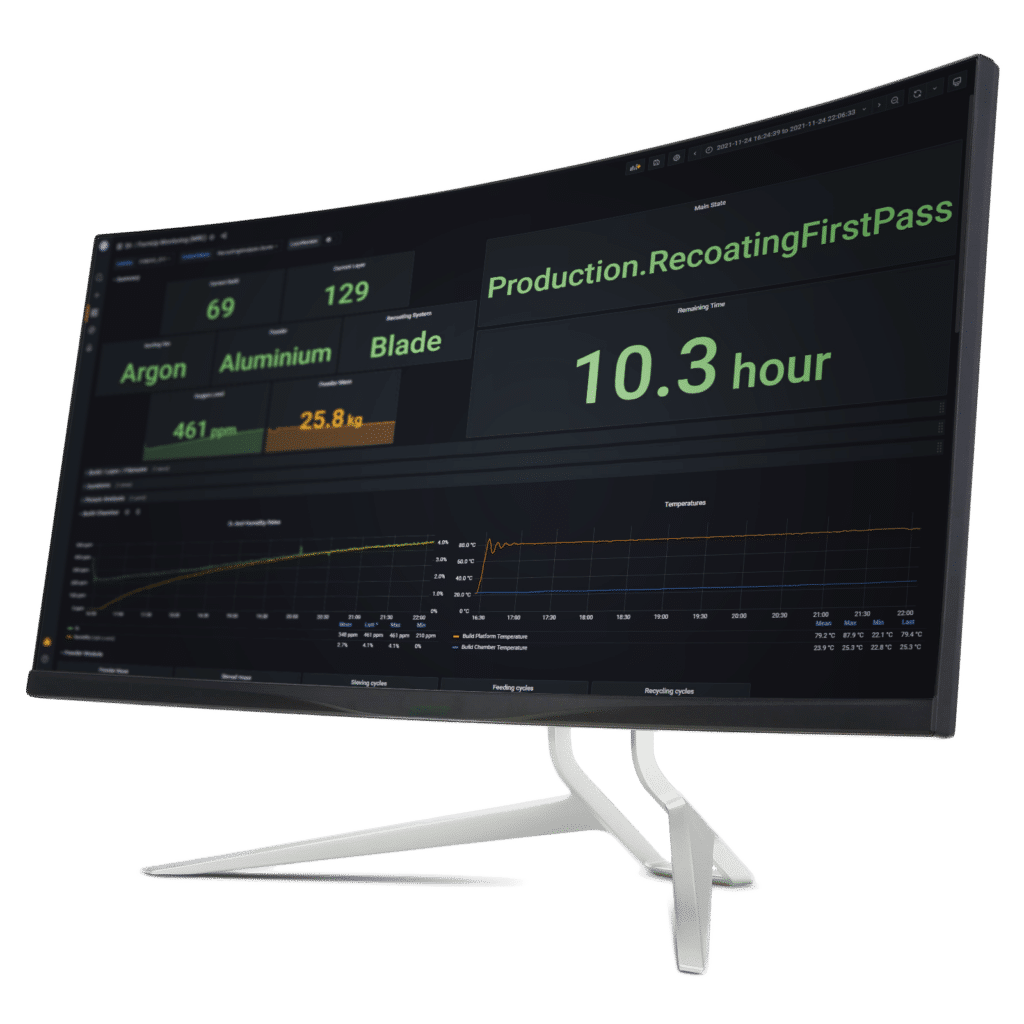
Lorsque les autorités de certification ont validé la qualification d’une application, les fabricants d’implants doivent mettre en place des systèmes garantissant une traçabilité sans faille de toutes les pièces produites. Mais le procédé L-PBF est complexe, avec de nombreux paramètres influents et des interactions multiples entre ces paramètres. Pour aider les industriels dans le suivi de tous les paramètres de leurs fabrications, AddUp propose le logiciel AddUp Dashboards, une solution de traçabilité et d’analyse de l’ensemble des données de production. Plus de 80 paramètres sont suivis, horodatés avec une grande précision et stockés sans limite de temps dans une base de données. Les utilisateurs peuvent alors réaliser toutes sortes de tableaux de bord, que ce soit pour le suivi des machines, la détection et l’analyse d’aléas de production, ou la création de rapports de toutes sortes.
Contrairement aux autres systèmes, AddUp Dashboards permet d’accéder au GUID (Globally Unique Identifier), un label unique de 128 bits pour le fichier de construction qui a été exécuté. Le GUID change automatiquement lorsque le projet est modifié, ce qui rend impossible l’imitation ou la récupération d’une valeur périmée. Cela garantit le fait que le projet a été réalisé comme prévu, sans modification des géométries, des paramètres laser ou des réglages de la chambre de fabrication.
En conclusion, si les machines FormUp 350 héritent de l’expérience du groupe Michelin, qui les utilisent pour la fabrication en grandes séries de pièces de moules de pneumatiques, on constate que leurs caractéristiques les rendent parfaitement applicables au secteur médical.
En effet, ces machines ont été pensées dès les premières phases de leur conception pour atteindre de hauts niveaux de productivité et de qualité, mais elles ont aussi été améliorées au fil des années. Notamment grâce à l’expérience acquise dans les ateliers d’AddUp, qui utilise ses propres machines pour proposer à ses clients des services de fabrication de pièces. Aujourd’hui, les FormUp 350 sont utilisées par un des leaders mondiaux de la fabrication d’implants, qui s’est équipé dans différents ateliers en Europe et aux Etats-Unis, et réalise des fabrications qualifiées et en grande série.
» Lien vers le cas d’application sur les lamelles de pneumatiques.