Alors que la demande d’implants spécifiques aux patients continue de croître au-delà de la capacité des fabricants à suivre, des leaders du secteur de la santé comme la Mayo Clinic et la U.S. Veterans Administration sont en train d’élaborer des plans pour créer leurs propres installations et commencer à imprimer en 3D des implants métalliques sur place.
Actuellement, les cas d’utilisation les plus courants de la fabrication additive dans le domaine de la santé sont le développement de modèles anatomiques pour aider les patients à comprendre les procédures à venir et la personnalisation de l’instrumentation chirurgicale.
Tout indique qu’à l’avenir, les organismes de soins de santé fabriqueront des dispositifs sur le lieu de soins (POC). Cela signifie que les hôpitaux seront bientôt les nouveaux membres de l’industrie de fabrication de dispositifs médicaux (MDM), une proposition qui comporte de véritables défis institutionnels et d’infrastructure. « Après tout, ce n’est pas vraiment la vocation des établissements de santé », explique Severine Valdant, directrice commerciale de QuesTek Innovations, une société d’ingénierie des matériaux de premier plan, et membre fondateur du comité consultatif médical d’AddUp. « Il faut une autre façon de penser pour un hôpital.
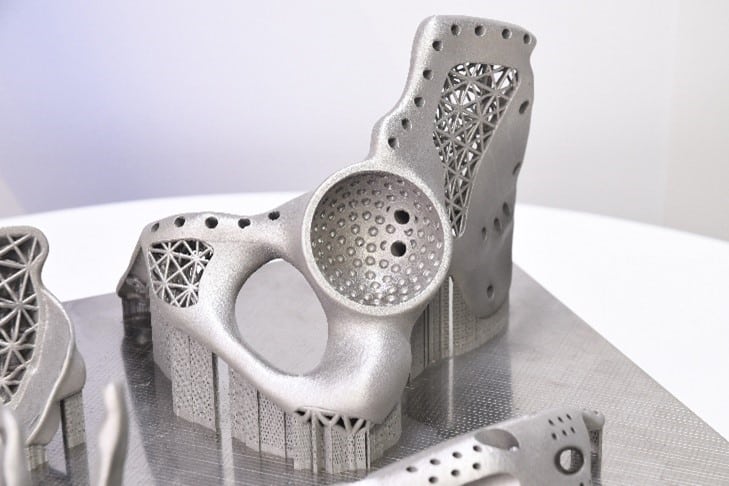
Le comité consultatif médical d’AddUp a été créé en 2023 afin de fournir à l’entreprise des points de vue impartiaux et holistiques sur l’application des technologies d’impression 3D de métaux aux soins de santé. Severine Valdant apporte son point de vue unique en tant que leader dans le développement de dispositifs médicaux et de l’impression 3D. Avant de rejoindre QuesTek, elle a dirigé la transformation d’Oxford Performance Materials en un leader de la fabrication additive, l’aidant à devenir la première entreprise à recevoir l’approbation de la FDA pour des implants polymères imprimés en 3D.
Les principaux acteurs reconnaissent la valeur de l’impression 3D
Malgré les défis que la fabrication additive pose aux organismes de santé qui espèrent tirer parti de l’impression 3D sur les lieux de soins, le concept est de plus en plus largement accepté par les responsables des soins de santé et d’autres acteurs clés.
- Les équipementiers font de grands progrès. « Si les fabricants d’imprimantes peuvent proposer une solution tout-en-un, il sera beaucoup moins difficile de mettre en œuvre l’AM sur le lieu de soins, et nous n’en sommes plus très loin », affirme M. Valdant. La bonne nouvelle, c’est que des entreprises comme AddUp mettent sur le marché de nouvelles imprimantes qui peuvent être facilement intégrées à d’autres systèmes et processus établis.
- La FDA est de la partie. « En fait, ils voient une grande valeur dans la fabrication de POC et ils travaillent avec les acteurs du secteur des soins de santé et des équipementiers pour déterminer quelles réglementations ou lignes directrices sont nécessaires pour que cela se produise.
- Les chirurgiens sont enthousiastes quant aux possibilités offertes. « J’ai parlé à beaucoup d’entre eux et ils sont très enthousiastes à propos des outils électroniques, mais nous devons veiller à ce qu’ils ne cessent pas d’être médecins pour devenir ingénieurs », poursuit M. Valdant.
- Les administrateurs jouent un rôle clé. « Ce sont eux qui prennent les décisions les plus importantes. Si nous apportons l’AM au point de soins, ils doivent voir un bon retour sur investissement ».
Applications futures
L’avenir des soins de santé est à la médecine personnalisée et la fabrication de POC y jouera un rôle important. Nous nous attendons à ce que de nombreux nouveaux cas d’utilisation se profilent à l’horizon, qui repousseront les limites de la technologie et élargiront ses possibilités. Il s’agit notamment d’avancées dans la fabrication juste à temps d’instruments à usage unique, spécifiques aux procédures et aux patients, afin de remplacer les systèmes traditionnels à des coûts abordables.
Les applications futures de l’AM POC se concentreront sur les procédures pour lesquelles il n’existe pas d’option d’implant pratique ou efficace disponible sur le marché, notamment les chirurgies complexes de reconstruction du genou, de la hanche et du bassin, les chirurgies de la colonne vertébrale et la modélisation des tumeurs pour les patients atteints d’un cancer.
En outre, l’IA et l’apprentissage automatique permettront bientôt d’automatiser les flux de travail et d’accélérer la production d’implants spécifiques aux patients, en améliorant les délais de développement, qui passeront de 18 mois à quelques jours. Cela devrait améliorer de manière exponentielle les résultats pour les patients, tout en réduisant les temps opératoires et la nécessité d’effectuer des chirurgies correctives supplémentaires.
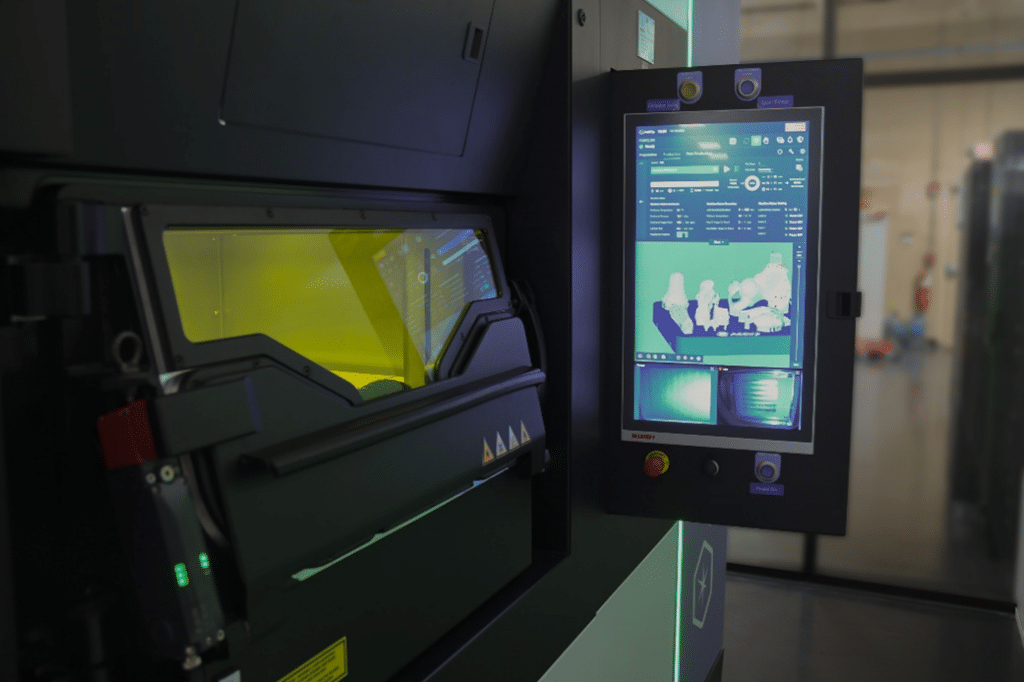
Le bon OEM
La fabrication de POC devra être un partenariat efficace entre l’établissement de santé et l’équipementier. « Je pense que nous sommes beaucoup plus avancés qu’il y a dix ans, parce que la collaboration entre les deux se met en place », poursuit M. Valdant. « Grâce à notre connaissance approfondie du marché médical et à une solution très efficace et intégrée, AddUp sera un excellent partenaire pour les équipementiers.