Une buse optimisée imprimée en 3D en une seule pièce qui délivre un flux de liquide de refroidissement à des endroits précis. La buse a été installée officiellement sur la meule, optimisant ainsi ses performances.
INDUSTRIE
Outillage et moules
CHALLENGE
Imprimer en 3D une buse d’injection de fluide de coupe
aux géométries internes complexes
KEY BENEFITS
- Flux optimal fourni sur la zone de coupe
- Imprimé en jours, plutôt qu’en semaines
- Pièce monobloc pour une résistance accrue
- Résistance à la corrosion
FORMES COMPLEXES
TEMPS DE PRODUCTION
INTÉGRATION DE FONCTIONS
PERFORMANCE
Histoire
Fives est un groupe international d’ingénierie industrielle qui compte plus de 200 ans d’expérience. Il a su s’adapter et se transformer pour offrir des produits et des solutions innovants, qui permettent à de grands groupes industriels à travers le monde d’être toujours plus performants.
Fives Landis Corp est une filiale du groupe Fives reconnue dans le monde entier pour ses systèmes de rectification de haute précision. Elle a travaillé avec AddUp, une joint-venture créée par Fives et Michelin et spécialisée dans la fabrication additive métallique, pour concevoir et imprimer en 3D un nouveau modèle de buse d’injection de liquide de refroidissement.
Défi technologique
Avec les procédés de production traditionnels, fabriquer une buse à la géométrie optimisée est à la fois complexe et coûteux. Cela nécessite de décomposer la pièce en plusieurs sous-ensembles, et les concepteurs ne peuvent créer des parois internes aux formes aussi complexes qu’ils le souhaitent. L’impression 3D métallique permet de réaliser ce type de pièce en une seule opération, plus rapidement qu’avec les procédés conventionnels, et avec une liberté de conception. La nouvelle buse imprimée en 3D permet de projeter le liquide de coupe de manière optimisée, améliorant le refroidissement et la lubrification de l’outil et de la pièce pendant la rectification, tout en s’adaptant à l’architecture complexe de la machine. Les nouvelles rectifieuses nouvellement équipées voient leurs performances augmentées.
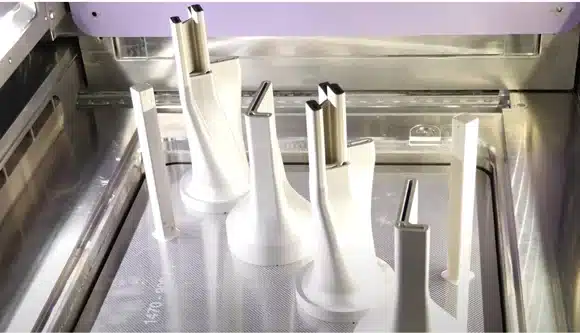
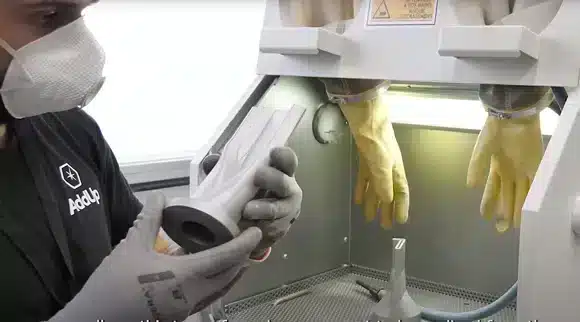
Solution
Les équipes d’AddUp ont utilisé le logiciel de préparation de fabrication AddUp Manager afin d’adapter le positionnement de la pièce et la stratégie de fusion pour trouver le meilleur compromis entre productivité et qualité de surface. Puis le projet a été fabriqué sur une FormUp® 350, la machine de fusion laser sur lit de poudre d’AddUp.
La buse est imprimée en acier inoxydable, à l’aide de la FormUp 350, en quelques heures seulement. Dans cette machine, les pièces sont fabriquées par couches horizontales successives. Pour chaque couche, de la poudre métallique est étalée sur le plateau de production et un laser fait fondre les zones qui doivent être solidifiées.
Après impression, la pièce est séparée de son plateau de fabrication par électroérosion (découpe par fil). Après un traitement de la surface par microbillage, la pièce peut être assemblée sur la machine de rectification.
Le FormUp garantit une performance précise et répétable de la pièce grâce à :
- une résolution jusqu’à 0,1 mm- une densité du matériau de 99,99 %.
- des angles de production de 15 degrés
- un état de surface jusqu’à 4 Ra µm
Résultats
Le résultat final est une buse de refroidissement optimisée en une seule pièce qui délivre avec précision le flux de liquide de coupe à des endroits précis. La buse a été officiellement installée sur une rectifieuse Landis LT2 reconstruite, optimisant ainsi les performances de la machine.
Les nouvelles buses permettent d’injecter le fluide avec précision au plus près de la zone de coupe, même pour des meules aux formes complexes. Il a été prouvé qu’elles avaient la résistance et l’intégrité requises pour fonctionner en production de masse pendant plus d’un an sans aucune défaillance. L’examen des buses ne montre aucun signe de fatigue ou de corrosion.
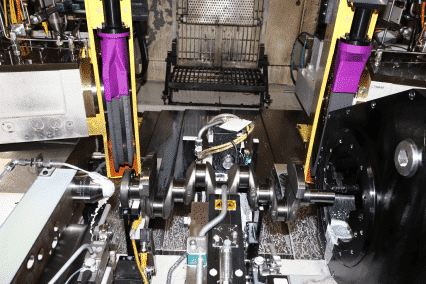
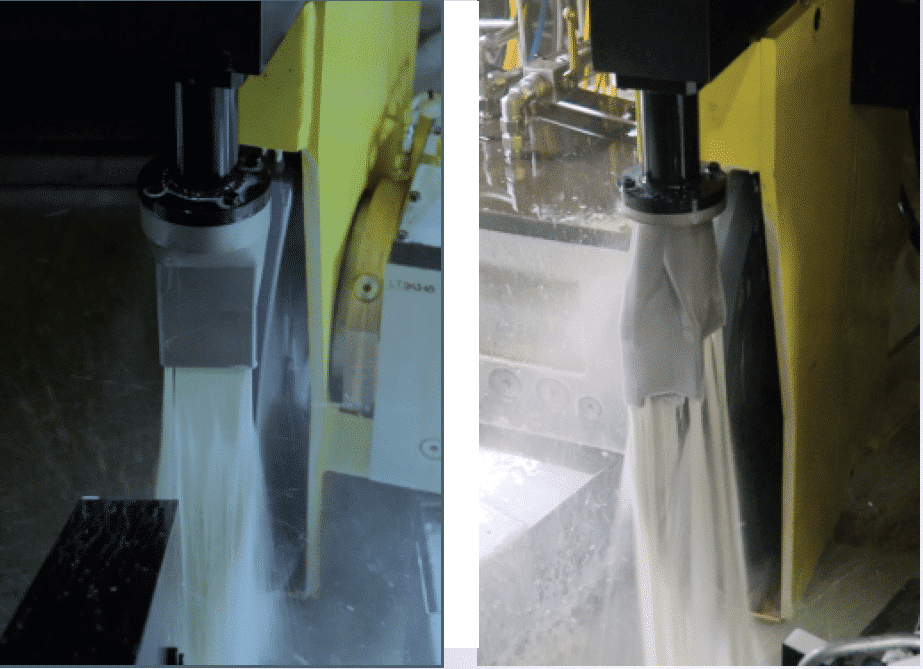