Cette étude de cas se concentre sur les implants rachidiens et les défis auxquels ils sont confrontés dans leur processus de fabrication aujourd’hui. La fabrication additive (AM) offre des avantages tels que la conception en treillis et la rugosité de la surface, ce qui permet d’améliorer les résultats pour les patients.
Industrie
Médical
CHALLENGE
Reduction significative des couts de production lors de la fabrication additive d’implants rachidiens de grande taille à l’aide d’un système multi-laser et d’une plateforme de fabrication de plus grande dimension.
KEY BENEFITS
- Réduction des coûts de production jusq’à 30%
- Augmentation du redement de 2,61 pièces par heure (2,09 à 4,7)
- Création de structures avec une fine résolution et une ostéo-intégration optimale
- Réduction du post-traitement
- Réduction du coût total de la pièce
Fonctions intégrées
Temps de production
Sans support
Performance
HISTOIRE
Les dispositifs de fusion vertébrale de grande taille sont traditionnellement imprimés sur des machines de petit format utilisant la technologie de fusion sur lit de poudre (PBF) équipées de 1 à 2 lasers, ou usinés à partir de barres de polyétheréthercétone (PEEK). Ils sont généralement imprimés avec leur face antérieure dirigée vers le haut (en Z). Cette orientation, combinée au processus d’impression couche par couche, ne représentent néanmoins pas la meilleure méthode. Le prix est relativement élevé car la majeure partie du coût est dû au temps du processus de production lui-même. Par contre, bien que le coût soit plus élevé, Les avantages de la Fabrication Additive (FA) pour ce type d’implants vertébraux sont : la possibilité d’intégrer une structure en treillis et la rugosité de la surface, ce qui favorise l’ostéo-intégration et donc l’assurance de meilleurs résultats pour le patient. Un autre avantage de la Fabrication Additive est lié aux matériaux utilisables. La FA permet d’imprimer du titane avec une plus grande résistance à la fissuration et à la traction. La fabrication de ces implants de grande dimension en PEEK ne présente pas des caractéristiques idéales pour l’osthéo-intégration. Cela, associée à l’instabilité de la chaîne d’approvisionnement de la matière, posent des problèmes lors de la fabrication de ces dispositifs de fusion vertébrale de grande taille utilisant le PEEK. Pour ces raisons, la production en FA de ces implants est généralement préférée.
DÉFI TECHNIQUE
Bien que la FA permette une meilleure ostéo-intégration, avec l’utilisation de matériaux plus résistants et la garantie de meilleurs résultats pour les patients, la fabrication des dispositifs LLIF sur des machines de petite dimension avec seulement 1 ou 2 lasers augmente sensiblement le coût de l’implant fini.
Ces implants ont une hauteur importante (en Z), ce qui augmente les temps de fabrication, qui sont encore plus longs avec l’utilisation d’un petit nombre de lasers. Lors de l’utilisation d’un système de mise en couche par racleur ou rouleau, le dessous de la face antérieure nécessite, généralement, l’utilisation de supports. Les LLIF doivent également être retirés de la plateforme de fabrication à l’aide d’une machine d’électroérosion à fil (EDM). Ces 2 éléments de post-process rentrent dans le prix final de la pièce et leur impact est directement lié à la capacité de fabrication réduite des petites machines, au petit nombre de lasers et au système de mise en couche utilisé.
SOLUTION
L’utilisation de la machine PBF FormUp® 350 permet de réduire le temps de production et d’augmenter le rendement de 2,61 pièces par heure par rapport aux plates-formes plus petites équipées de 1 ou 2 lasers. La différence : un plateau de production de 350 millimètres carrés qui peut contenir 1,5 fois (152 pièces contre 96 pièces) la quantité de grands implants rachidiens par rapport aux plateformes plus petites. L’utilisation de 4 lasers permet d’imprimer 152 grands implants rachidiens en seulement 32 heures. La FormUp 350 utilise aussi une technologie de mise en couche par rouleau qui permet
d’obtenir une complexité géométrique élevée, tout en utilisant le minimum de supports et la garantie d’un état de surface optimal. La FormUp 350 permet de réaliser des structures complexes et d’obtenir une rugosité de surface qui contribue à de meilleurs résultats pour le patient. Il n’est donc plus nécessaire d’obtenir une surface trabéculaire poreuse au plasma par pulvérisation ou par feuille, et la rugosité de la surface n’est plus un sous-produit du processus. Les pièces sortent de l’imprimante plus proches de la forme finale et nécessitent moins de traitement manuel et/ou d’enlèvement de supports. La combinaison d’un volume de construction de 350 mm3 avec 4 lasers et d’une pièce personnalisable, sortant directement de l’imprimante, simplifie les étapes de fabrication. La réduction du nombre de procédés nécessaires contribue à une meilleure conception et à une réduction des délais d’exécution, ce qui se traduit par une baisse du coût des pièces. Tout cela permet de réduire les coûts tout au long de la chaîne d’approvisionnement et d’optimiser les pièces pour les patients.
RÉSULTATS
Les grands implants rachidiens, produits avec peu de lasers et faisant appel à des process de revêtement traditionnels, coûtent plus cher que lorsqu’ils sont produits à l’aide de la FormUp 350. La machine FormUp 350 est idéale pour toutes les applications médicales de ce type, car elle offre un processus amélioré et rentable pour la fabrication en série d’implants médicaux très complexes.
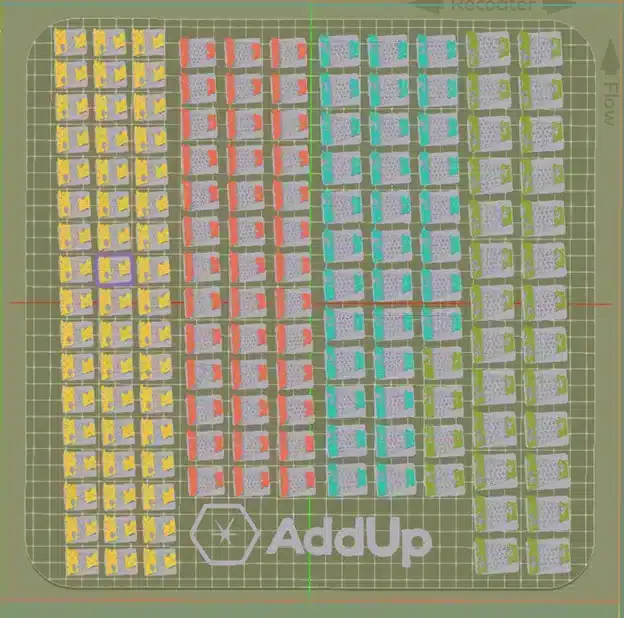
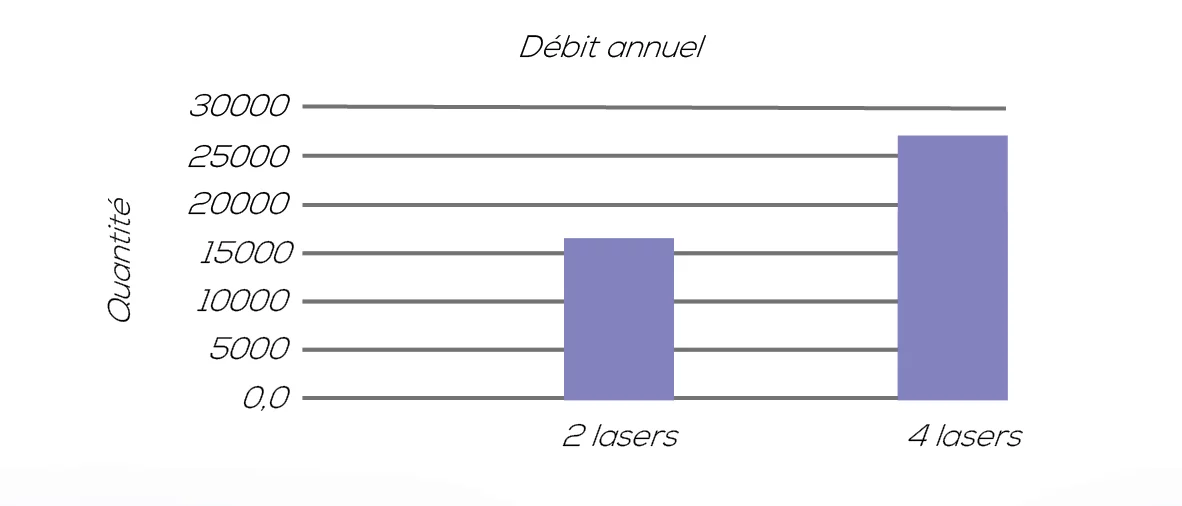
- Pièces fabriquées par laser sur le FormUp 350
- 2 Laser – 76
- 4 Laser – 38
- Il est temps de développer la FormUp 350
- 2 laser – 52.95
- 4 laser – 32.35
- Débit annuel sur le FormUp 350
- fonctionnement d’une équipe par jour pendant 52 semaines par an
- 1 – 1.5 de l’arrêt du laser à l’allumage du laser (build flip)
Poudre | 2 Lasers | 4 Lasers |
---|---|---|
Poudre moyenne, 30μm (hrs) | 52.95 | 32.35 |
Débit annuel | 16.845 | 27.408 |