Pièces imprimées en 3d pour l’aéronautique | Blog
En juin 2020, le gouvernement français a lancé le Plan de soutien à la filière aéronautique pour aider les industriels du secteur à surmonter les conséquences de la crise sanitaire, et les inciter à accélérer dans la réduction de l’empreinte carbone de leurs activités. Une enveloppe de 1,5 milliard d’euros sera débloquée sur les trois prochaines années pour soutenir les projets de recherche et développement dans ce domaine.
Impression 3D et aéronautique : pour des avions plus « propres »
Trois leviers principaux sont identifiés pour tendre vers des avions plus « propres » :
- la réduction de la consommation en carburant,
- l’électrification des appareils,
- et la transition vers des carburants neutres en carbone comme l’hydrogène.
Dans ces trois domaines, l’impression 3D peut apporter des réponses aux industriels qui souhaitent dépasser les limites de performances des équipements réalisés par des techniques conventionnelles.
Les industriels de l’aéronautique se sont intéressés très tôt à la fabrication additive (impression 3D), et l’utilisent depuis des décennies. Elle fut d’abord employée pour la fabrication de prototypes, afin de raccourcir les temps de développement des nouveaux appareils. Puis, engagés dans la course à l’allègement, les avionneurs ont commencé à imprimer des pièces fonctionnelles. Aujourd’hui, on trouve à bord des avions des pièces critiques (pièces de moteur, par exemple), voire des pièces structurelles issues de différents procédés d’impression 3D.
Selon un rapport du cabinet Market Research Future, le nombre d’entreprises et de fournisseurs certifiés pour la fabrication additive dans l’aéronautique et le spatial devrait progresser de plus de 20 % par an jusqu’en 2023. Le groupe AddUp compte parmi ces fournisseurs capables de répondre aux exigences de l’industrie aéronautique : notre atelier de production basé à Salon-de-Provence (Bouches-du-Rhône, France) est certifié NF EN 2100 : 2018.
DED et L-PBF, deux technologies complémentaires
Nos gammes de machines sont elles aussi adaptées aux applications aéronautiques. En effet, la technologie de dépôt sous énergie dirigée (DED) est adaptée à la réparation de pièces usées, elle est utilisée pour du rechargement de pièces de moteur d’avion, par exemple. Elle permet aussi de produire des pièces de grandes dimensions, telles que des tuyères ou des tubulures complexes, avec un coût réduit par rapport à l’usinage dans la masse, et une répétabilité améliorée par rapport à la chaudronnerie.
La technologie de fusion laser sur lit de poudre (L-PBF), quant à elle, est utilisée pour la fabrication de pièces de plus petites dimensions, mais avec une grande liberté de formes. Cela permet aux ingénieurs d’envisager des gains de performances dans de multiples domaines, tels que l’allègement, l’amélioration des écoulements de fluides, ou encore l’optimisation des échanges thermiques.
Les deux cas d’applications récents qui suivent, réalisés pour le secteur aéronautique, illustrent bien le type de gains rendus possibles par cette technologie.
Un bloc hydraulique pensé pour l’impression 3D
Récemment, le groupe Airbus a travaillé avec AddUp et Hall32, centre de promotion des métiers de l’industrie, sur l’optimisation d’un bloc hydraulique grâce à la fabrication additive métallique. La pièce d’origine est un collecteur de fluide, traditionnellement usiné à partir d’un bloc de titane. Grâce à la technique de l’optimisation topologique, AddUp et Hall32 sont parvenus à réduire la masse de la pièce de 85 %, tout en améliorant la circulation des fluides.
Mais le projet ne s’est pas arrêté là. La pièce nécessitait une quantité importante de supports pour pouvoir être fabriquée, ce qui impliquait du temps passé en impression (temps de fabrication des supports) et en usinage (temps de retrait des supports). Les ingénieurs d’AddUp et de Hall32 ont donc réalisé une deuxième passe d’optimisation pour prendre en compte les contraintes liées au procédé (on parle alors de DfAM, pour Design for Additive Manufacturing). Dans sa version définitive, le collecteur de fluide est imprimé en 30 heures, contre 52 heures dans sa première version, et le temps d’usinage a été réduit de 6 heures.
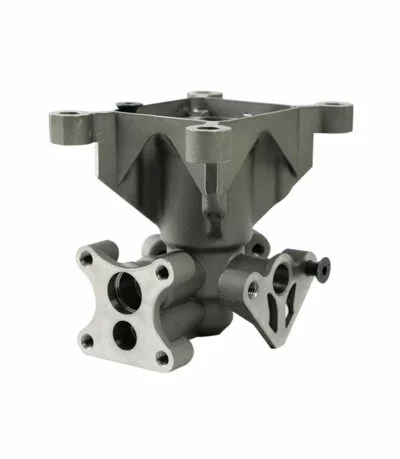
Un échangeur thermique innovant
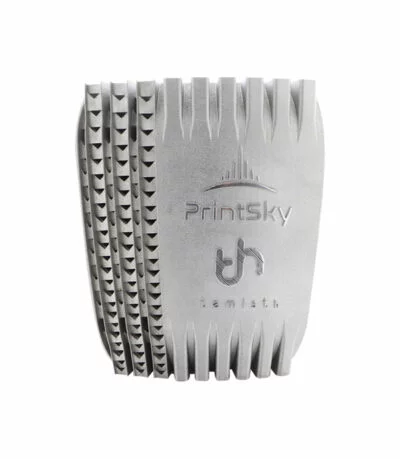
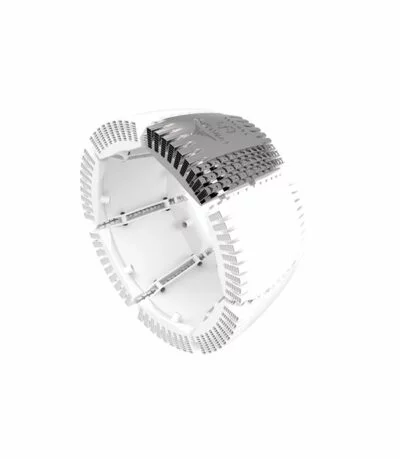
HEWAM est un concept d’échangeur thermique développé par Printsky et Temisth. PrintSky est une joint-venture entre le groupe AddUp, expert en fabrication additive métallique, et Sogéclair, un des leaders internationaux dans l’intégration de solutions à haute valeur ajoutée dans les domaines de l’aéronautique, de l’espace, du transport civil et militaire. Temisth, quant à elle, est une entreprise spécialisée dans le développement de solutions thermiques personnalisées utilisant la fabrication additive. L’objectif du projet HEWAM était de démontrer la capacité des deux partenaires à concevoir et fabriquer un échangeur thermique innovant avec le procédé PBF.
La production a été confiée à AddUp qui a imprimé en 3D cette pièce aéronautique sur une machine FormUp 350. Les experts d’AddUp ont utilisé une poudre d’Inconel® 718 de fine granulométrie afin de produire des parois minces avec de bons états de surface, et ainsi atteindre des performances thermiques élevées. Ces parois minces (150 µm) forment des canaux à la géométrie complexe, ce qui permet à HEWAM de présenter une grande capacité d’échange thermique dans un encombrement réduit.
Au-delà des performances, HEWAM propose aussi une nouvelle manière de gérer la dissipation thermique à bord des avions. D’abord grâce à son design modulaire. Plusieurs échangeurs peuvent être disposés les uns à côté des autres afin de délivrer la puissance thermique nécessaire à l’application. Ensuite, grâce à sa forme courbe, qui permet à HEWAM d’être installé dans les mâts réacteurs tout en laissant de l’espace au centre pour le passage des câbles nécessaires au fonctionnement des moteurs. Par son rapport performance/encombrement et sa modularité, HEWAM représente une alternative intéressante pour les constructeurs d’avions qui s’intéressent à l’optimisation des échanges thermiques à bord de leurs appareils.
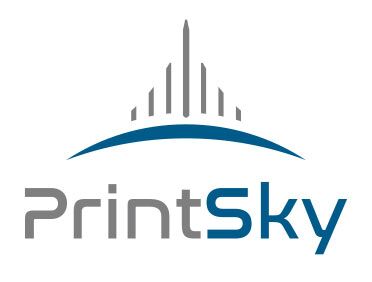
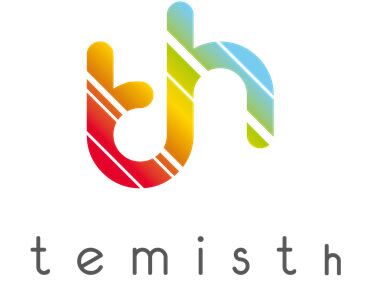
Autres avantages de l’impression 3D
Un système fonctionnel qui demandait avant l’assemblage de plusieurs petites pièces peut maintenant être imprimé en 3D en une seule fois, en un seul cycle de production. Plus besoin d’assemblage, ni de soudure et donc on diminue le risque de casse en plein vol. L’utilisation de matériaux certifiés permet également de s’assurer que les pièces imprimées sont prêtes à l’emploi et capables de supporter les rigueurs d’une application dans le monde réel.
Afin d’éviter que les avions ne restent immobilisés au sol, des stocks de pièces de rechange ont toujours été prévus. Or nombre d’entre elles sont finalement inutilisées voire obsolescentes. L’impression 3D permet de pallier une partie de ce problème en créant des pièces de rechange à la demande, en fonction du besoin et là où cela est nécessaire.
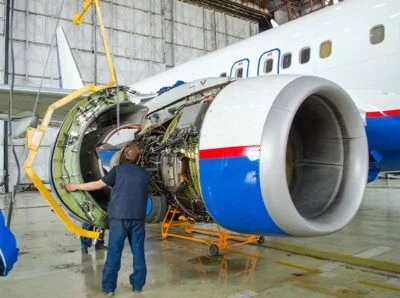
L’impression 3D métallique semble avoir de nombreaux atouts pour permettre à l’industrie aéronautique de retrouver son essor
De l’intégration de pièces métalliques aux géométries complexes, en passant par la réduction du poids des avions grâce à l’utilisation de métaux légers permettant de faire des économies de carburant, nombreux sont les bénéfices de la fabrication additive pour répondre aux objectifs financiers et écologiques de l’aéronautique.
En introduisant la Fabrication Additive dans la production, l’optimisation topologique, la complexité à faible coût, la diminution du nombre de pièces, les stocks plus faibles, c’est toute la chaîne de valeur du secteur aéronautique qui va connaître une véritable évolution.
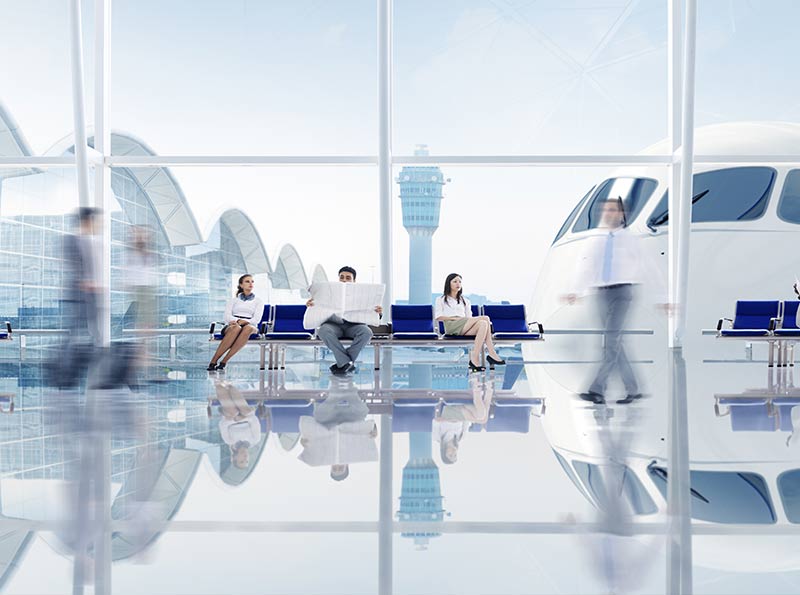