En utilisant l’impression 3D de métaux pour la réparation de pièces, les fabricants peuvent surmonter les défis de la chaîne d’approvisionnement, réduire les coûts de production et assurer une disponibilité rapide des pièces complexes.
Lorsqu’une pièce casse, la conséquence immédiate peut être un arrêt de la production, voire une perte de chiffre d’affaire ou d’un client. Il est impératif de maintenir ses installations en conditions opérationnelles dans un environnement compliqué, que ce soit dans le secteur de l’Oil & Gas, de l’énergie ou de la défense.
Réparer des équipements endommagés, produire des pièces de rechange à la demande… Autant de promesses de l’impression 3D métallique dont on parle depuis des décennies, mais qui restaient peu exploitées jusqu’ici dans le monde industriel. Ces dernières années, de véritables applications industrielles de la réparation par fabrication additive commencent à émerger, aidées par les gains de performance et de robustesse des machines de fusion laser sur lit de poudre (PBF) et de dépôt sous énergie dirigée (DED).
Comment la fabrication additive permet d’optimiser la supply-chain ?
Début 2021, le groupe français Orano, un des leaders mondiaux de l’exploitation du combustible nucléaire, publie les résultats d’un projet mené en partenariat avec AddUp. Ensemble, ils analysent la faisabilité et la rentabilité de la production de pièces de rechange par impression 3D métallique. L’étude porte sur plusieurs pièces complexes. Parmi celles-ci, un bloc de distribution de vapeur dont les délais d’approvisionnement sont particulièrement longs, ce qui implique de disposer à tout moment d’un stock suffisant de pièces de rechanges. Les ingénieurs d’Orano ont fait produire les pièces sur une FormUp 350, machine de fusion laser sur lit de poudre. Ils ont effectué différents tests sur ces blocs distributeurs, notamment des tests de résistance, afin de valider que les pièces imprimées présentaient les mêmes caractéristiques mécaniques que les pièces d’origine. Ces tests furent concluants, ce qui a permis d’éluder une idée reçue selon laquelle les pièces issues d’impression 3D métallique sont moins performantes que des pièces usinées. Surtout, l’industriel a fait ses calculs : sur ce type de pièces aux géométries complexes, la production de 16 pièces par fabrication additive à l’identique, équivaut au prix de 3 pièces usinées.
Afin de faire face à l’obsolescence de certains équipements nous avons fait appel à AddUp pour imprimer en 3D nos pièces de rechange métalliques. Le résultat est inespéré : même design avec géométries complexes, mêmes caractéristiques mécaniques et surtout gain de 50% du coût de production par rapport à l’usinage. Grâce à la fabrication additive métal, Orano possède maintenant une filière d’approvisionnement de pièces de rechange supplémentaire, agile, fiable et économique
Ana-Paula Serond, Ph.D., Innovation Manager – Direction Innovation, Orano
TÉLÉCHARGER L’ÉTUDE DE CAS ORANO
Les enjeux auxquels fait face Orano, et qui ont conduit au lancement de ce projet, sont récurrents dans l’industrie. Dans les usines d’assemblage ou les industries de process, par exemple, les temps d’approvisionnement pour des pièces complexes se comptent généralement en semaines, et peuvent entraîner des pertes d’exploitation considérables lorsque des usines complètes se trouvent arrêtées. Sans oublier que les industriels exploitent leurs machines sur plusieurs décennies. Il n’est pas rare que sur ces durées d’exploitation les plans des pièces ne soient plus disponibles, ou que les fournisseurs de ces équipements n’existent plus.
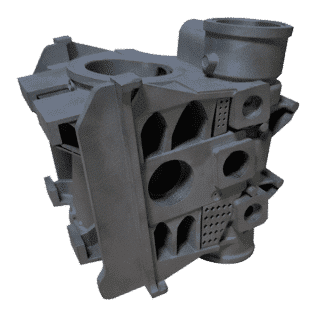
Les enjeux auxquels fait face Orano, et qui ont conduit au lancement de ce projet, sont récurrents dans l’industrie. Dans les usines d’assemblage ou les industries de process, par exemple, les temps d’approvisionnement pour des pièces complexes se comptent généralement en semaines, et peuvent entraîner des pertes d’exploitation considérables lorsque des usines complètes se trouvent arrêtées. Sans oublier que les industriels exploitent leurs machines sur plusieurs décennies. Il n’est pas rare que sur ces durées d’exploitation les plans des pièces ne soient plus disponibles, ou que les fournisseurs de ces équipements n’existent plus.
Des projets qui se multiplient dans la défense et le spatial
Ces besoins de mise à disposition rapide de pièces de rechange se retrouvent chez d’autres industriels, comme par exemple les exploitants de plateformes pétrolières. Pour eux, les enjeux sont moins centrés sur la complexité des pièces que sur la capacité à les approvisionner rapidement dans des zones isolées.
Citons également le secteur de la Défense : partout dans le monde, les forces armées étudient la possibilité de disposer d’unités de fabrication additive mobiles, capables de suivre les opérations et de produire des pièces de rechange à la demande au plus près des champs de bataille.
Le secteur du spatial, enfin, évalue depuis plusieurs années maintenant la possibilité d’embarquer des moyens de fabrication additive métallique à bord de missions spatiales, et plusieurs projets sont sur le point d’aboutir, dont un actuellement développé en partenariat avec AddUp.
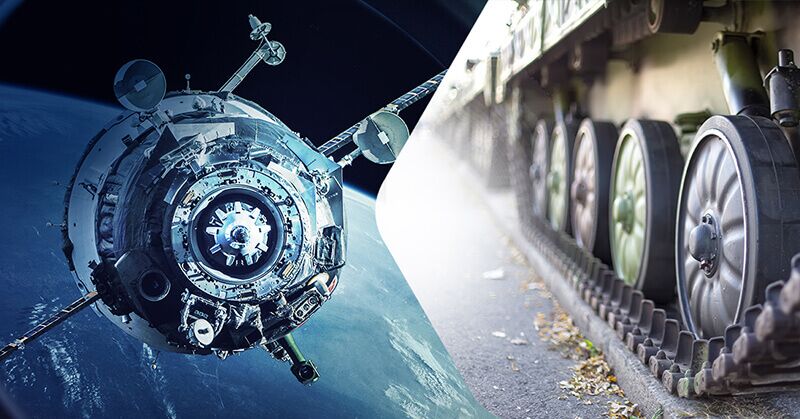
Finalement, l’impression 3D métallique peut démontrer un vrai potentiel :
- Limiter les coûts liés au stockage des pièces
- Réduire les temps de fabrication
- Diminuer les temps de transport
- Construire des chaînes d’approvisionnement de pièces de rechanges plus agiles et plus respectueuses de l’environnement
L’Agence De l’Environnement et de la Maîtrise de l’Energie (ADEME) a publié en 2017 une étude encourageant tous les acteurs français de l’impression 3D à développer des services de réparation de pièces.
Réparer des pièces grâce au DED
Tous les projets évoqués jusqu’ici portent sur des fabrications de pièces à la demande. Mais on ne peut traiter du sujet de la fabrication additive appliquée aux activités de maintenance sans évoquer la technologie DED, qui permet des applications de réparation de pièces existantes. Il faut dire que la réparation constitue déjà 15 % des cas d’application de la technologie DED. Le DED permet de déposer des cordons de métal sur des pièces existantes. Bien sûr, la réparation de pièces usées par ajout de matière (réparation par rechargement) n’est pas nouvelle. Depuis plusieurs décennies déjà, les industriels utilisent des robots de soudage pour déposer des cordons de soudure sur des pièces endommagées. Mais alors pourquoi utiliser le DED à la place du soudage ? Aujourd’hui, grâce à la technologie DED, la réparation de pièces gagne en précision.
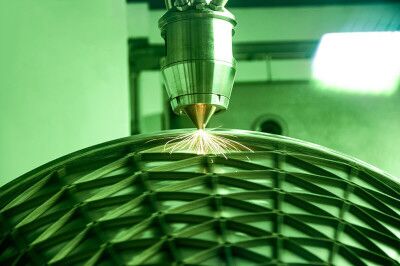
Le fait d’utiliser un faisceau laser permet de créer des cordons de métal très fins, de l’ordre de 1 mm de large, contre plusieurs millimètres pour les techniques de soudage traditionnelles qui utilisent des arcs électriques pour faire fondre le métal.
Les cordons sont également moins épais qu’en soudage, ce qui permet de :
- déposer la juste épaisseur de matière nécessaire,
- de limiter les temps de reprise en usinage (pour ramener la pièce à ses cotes d’origine),
- et surtout d’engendrer moins de déformations dans les pièces.
En effet, la zone affectée thermiquement, qui est la partie de la pièce qui subit une élévation de température susceptible de modifier ses propriétés, est moins importante avec le DED qu’avec le soudage traditionnel, ce qui limite le risque de dégrader les caractéristiques mécaniques des pièces.
À l’instar de la technologie de fusion sur lit de poudre, la technologie DED n’a plus aujourd’hui à démontrer sa capacité à produire des pièces aux caractéristiques mécaniques très élevées. Pour preuve, AddUp compte parmi ses clients un industriel de l’aéronautique, secteur parmi les plus exigeants en matière de qualité métallurgique des pièces, qui a qualifié une application de réparation sur une des pièces les plus critiques qui soient : un rotor de moteur d’avion. Cet industriel a pu prouver aux autorités de certifications que le rotor, au lieu d’être remplacé après 10 000 heures de vol, pouvait être rechargé par DED et réusiné, et ceci jusqu’à quatre fois, ce qui porte désormais sa durée de vie à 50 000 heures.
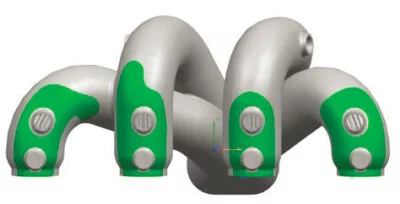
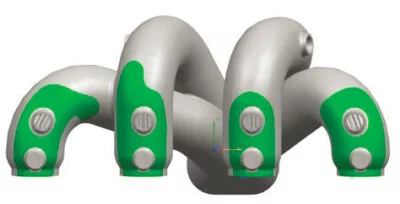
Conclusion
Pour conclure, quelle que soit la technologie d’impression 3D utilisée, L-PBF ou DED, les applications récentes dans les domaines de la maintenance, de la réparation et de la production de pièces de rechange montrent que la fabrication additive métallique a dépassé le stade des études, pour devenir une réalité industrielle.