Der Einsatz von Überwachungslösungen während des Prozesses könnte den Umfang der nach der Produktion erforderlichen Inspektionen ersetzen oder zumindest verringern und das Vertrauen in die Fertigungsqualität erhöhen. Diese Art von Software-Innovation wird entscheidend dazu beitragen, AM zu einer voll industrialisierten Technologie zu machen.
Author: Mathieu Roche, Software Manager, AddUp
Es ist kein Wunder, dass AM in den letzten zehn Jahren einen derartigen Umbruch in der Fertigungsindustrie verursacht hat. Die Fähigkeit, komplexe Geometrien herzustellen, die mit konventionellen Fertigungsverfahren nicht erreicht werden können, verbunden mit kurzen Fristen und oft zu geringeren Kosten, bietet viele Gründe, warum AM in einer Vielzahl von Branchen ganz oben auf der Agenda steht. Auf dem Weg zur Massenanwendung dieser Technologie gibt es jedoch eine Lücke: die Qualitätssicherung. Wenn ein Teil mit Hilfe von AM hergestellt wird, müssen viele Prüfungen nach der Produktion stattfinden, um die Konformität und die Einhaltung der geometrischen Toleranzen, den Grad der Porosität, die Erkennung von Fehlern und die Reproduzierbarkeit sicherzustellen. Die meisten dieser Prüfungen werden an Coupons und Mustern durchgeführt, die im Produktionslayout enthalten sind und unter den gleichen Bedingungen wie die Hauptteile hergestellt werden. Diese Proben werden dann auf Porosität, Ermüdung und viele andere Aspekte geprüft, um die Erwartungen des Auftraggebers zu erfüllen. Die Repräsentativität Ihres Hauptteils und die damit verbundene Qualität kann jedoch begrenzt sein, insbesondere wenn man die Verwendung von Multilaser-Produktion in Betracht zieht. Darüber hinaus sind diese Prüfungen oft teuer und langwierig, was sich auf die Durchlaufzeit und die Produktivität auswirken kann.
AM, und insbesondere PBF, eignet sich gut für den Einsatz von Überwachungslösungen während der Produktion. Bei einer durchschnittlichen Schichtdicke von 60 µm werden für eine typische Produktion etwa 3000 aufeinanderfolgende Schichten benötigt, bis sie abgeschlossen ist. Auf dem Papier scheint dies ein langsamerer Prozess im Vergleich zu konventionellen Herstellungsverfahren zu sein, aber zusätzlich zu all den bereits bekannten Vorteilen von AM, wie komplexe Geometrie, Vorlaufzeit … bieten die aufeinanderfolgenden Verschmelzungen dieser dünnen Materialschichten eine einzigartige Perspektive auf den Zustand d e s Teils während der Herstellung. Der Einsatz von Überwachungslösungen während des Prozesses könnte die Anzahl der erforderlichen Nachkontrollen ersetzen oder zumindest reduzieren und das Vertrauen in die Fertigungsqualität erhöhen. Diese Art von Software-Innovation wird entscheidend dazu beitragen, dass sich AM zu einer voll industrialisierten Technologie entwickelt.
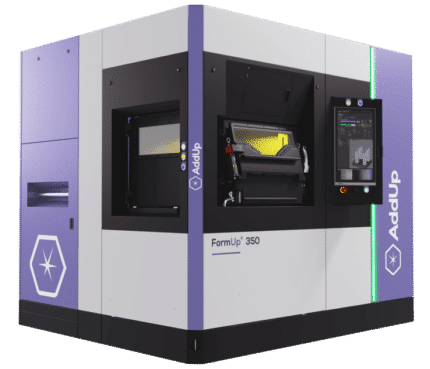
AM ist eine ziemlich komplexe Technologie, die es zu beherrschen gilt, weil wir es mit verschiedenen Maßstäben zu tun haben: Wir müssen Millionen von Vektoren erzeugen, die kilometerlangen Flugbahnen entsprechen, die mit einer Geschwindigkeit von mehreren Metern pro Sekunde von einem „Stift“ mit dem Durchmesser eines Haares gezeichnet werden. Darüber hinaus müssen Dutzende von Komponenten wie die Plattform, der Laser und der Luftstrom für die Inertisierungsbedingungen zusammenwirken, um das Teil wie erwartet herzustellen. Aus diesen Gründen wäre ein einstufiger Ansatz für die Prozessüberwachung unzureichend, um das Niveau der Qualitätssicherung zu gewährleisten, das von einer voll industrialisierten Technologie verlangt wird. AddUp’s komplette Suite von Überwachungslösungen wurde entwickelt und gebaut, um das volle Potential von
die FormUp® 350 Powder Bed Fusion (PBF) Maschine. Das Herzstück der AddUp Überwachungsstrategie sind 3 Schlüsselelemente.
Die erste ist eine Makroansicht dessen, was in der Maschine vor sich geht. AddUp’s Die FormUp® 350 PBF-Maschine verfügt über Dutzende von Sensoren, die Daten in Echtzeit erfassen:
Sauerstoffgehalt, Luftfeuchtigkeit, Zustand der Laser, gemessene Kräfte in allen beweglichen Komponenten, Pulververbrauch, Gasfluss usw. In der Vergangenheit waren diese Datensätze unvollständig und wurden erst nach der Produktion konsolidiert, wodurch das Handlungspotenzial während der Produktion eingeschränkt wurde. Aber jetzt können sie in Echtzeit auf einer intuitiven Plattform visualisiert werden, genannt: AddUp Dashboards. Das Sammeln und Auswerten dieser Daten kann einen aussagekräftigen Hinweis auf die Qualität des Teils geben und bietet ein vollständiges Verständnis der Produktionsbedingungen.
Diese Lösung kann auch auf die unterschiedlichen Bedürfnisse der verschiedenen Fertigungsbereiche zugeschnitten werden. Das Wartungspersonal wird Drifts für bewegliche Komponenten verfolgen und Die Produktionsleiter werden die Auslastung ihrer Werkstätten verfolgen und sicherstellen, dass es zu keinen Engpässen oder Problemen in der Lieferkette kommt.
Unterbrechungen. Qualitätsexperten haben Zugriff auf einen Build-Bericht, der jedes einzelne Ereignis während der Produktion enthält, wobei automatisch ein OK / INCOMPLETE / FLAG-Status generiert wird. Und schließlich haben die Prozessexperten die volle Kontrolle über Dutzende von Variablen, mit fortschrittlichen Funktionen für Querverweise auf wichtige Prozessparameter oder KPPs. Es ist wichtig zu erwähnen, dass all diese Daten dank des AddUp GUID-Systems, das die Konformität der Produktionsdatei von Anfang bis Ende verfolgt, den höchsten Rückverfolgbarkeitsstandards entsprechen.
Doch all dies ist nur der erste Schritt.
Der nächste Schritt ist die Analyse der Ausführung der Produktion, aber auf mikroskopischer Ebene. AddUp misst KPPs mit einer sehr hohen Frequenz: die physische Position des Laserspots, die tatsächlich vom Laser gelieferte Leistung und die Emissivität des Schmelzbads. Meltpool Monitoring ermöglicht die Charakterisierung von Defekten, ohne das Bauteil zu zerstören, was insbesondere für einzigartige Einzelanfertigungen nützlich ist. Die Datenmenge, die mit dieser Überwachungslösung erzeugt wird, kann sehr groß sein, deshalb bietet AddUp eine Reihe von PNG-Dateien an, ein leichteres und einfacher zu lesendes Format als Rohdaten, die in AddUp Manager, der CAM-Lösung für FormUp, visualisiert werden können. Diese Visualisierungen werden in Echtzeit nach jeder nachfolgenden Schicht bereitgestellt. Diese Bilder werden automatisch neu positioniert und mit der nominalen Scanstrategie überlagert, was einen Vergleich mit den erwarteten Trajektorien ermöglicht. Bei der Massenproduktion kann diese Art der Überwachung dazu verwendet werden, einen Referenz-Fingerabdruck zu erstellen, der als Vergleichspunkt für zukünftige Produktionsaufbauten verwendet werden kann.
Meltpool Visuelle Daten
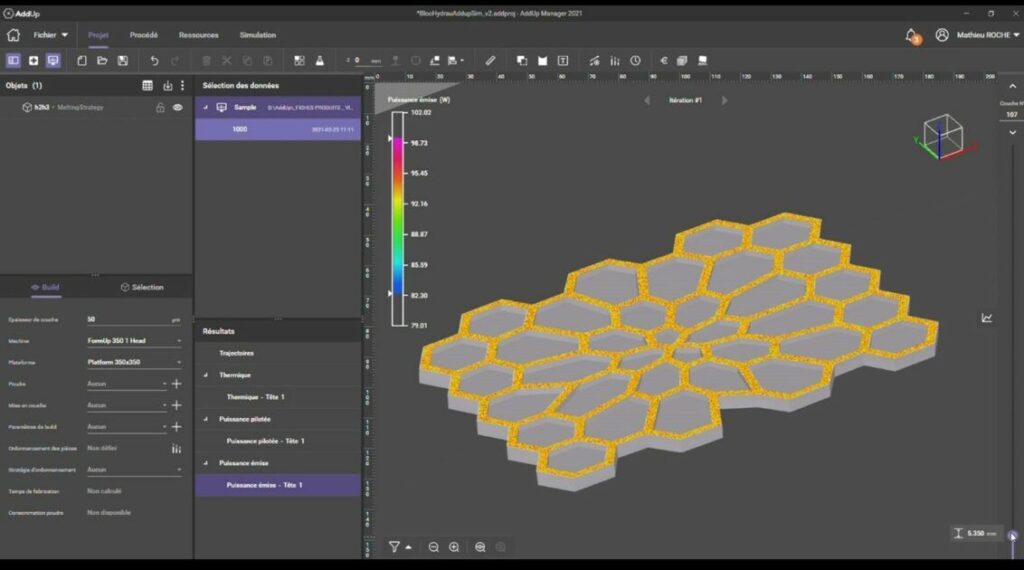
Das letzte Schlüsselelement in der AddUp Monitoring Suite ist die Analyse der Qualität der Beschichtung. Die innovative Technologie von AddUp (Recoat Monitoring) korrigiert proaktiv Fehler während der Produktion. Dieses Element wurde entwickelt, um die Produktivität der Teile zu verbessern. Wie bereits erläutert, basiert AM auf der Erzeugung von mehreren tausend aufeinanderfolgenden Schichten. Wenn die Qualität des Pulverbettes aufgrund einer Vielzahl von Problemen unter den Standards liegt, kann es nach einigen Stunden der Produktion zu einem Ausfall des Bauteils kommen. Die Auswirkungen können dramatisch sein. Das AddUp Recoat Monitoring System prüft nicht nur die Homogenität des Pulverbettes und zeigt mögliche Ablagerungen oder Pulvermangel auf, sondern löst bei Bedarf auch eine Korrektursequenz aus, die sicherstellt, dass das Pulverbett schön und glatt ist, bevor der Schmelzvorgang fortgesetzt wird. Diese Wiederbeschichtungskorrekturen werden vollständig nachverfolgt und in AddUp Dashboards und in jedem Bauteil-Bauprotokoll ausgewiesen.
Die Kombination dieser drei Schlüsselelemente wird die Akzeptanz der Technologie beschleunigen, da sie nicht nur das Vertrauen in die Qualität fehlerfreier Teile bei Kleinserienanwendungen, sondern auch bei der Massenproduktion von AM-Teilen stärkt.