Da die Nachfrage nach patientenindividuellen Implantaten weiter wächst, als dass die Hersteller mithalten könnten, schmieden führende Unternehmen des Gesundheitswesens wie die Mayo Clinic und die U.S. Veterans Administration Pläne, eigene Einrichtungen zu errichten und mit dem 3D-Druck von Metallimplantaten vor Ort zu beginnen.
Die häufigsten Anwendungsfälle für die additive Fertigung im Gesundheitswesen sind derzeit die Entwicklung anatomischer Modelle, die Patienten helfen, ihre bevorstehenden Eingriffe zu verstehen, und die Anpassung chirurgischer Instrumente.
Alles deutet auf eine Zukunft hin, in der Gesundheitsorganisationen Geräte am Point of Care (POC) herstellen werden. Das bedeutet, dass Krankenhäuser bald die neuesten Mitglieder der Industrie für die Herstellung von Medizinprodukten (MDM) sein werden, ein Vorhaben, das echte institutionelle und infrastrukturelle Herausforderungen mit sich bringt. „Schließlich sind die Einrichtungen des Gesundheitswesens nicht wirklich dafür ausgelegt“, sagt Severine Valdant, Chief Commercial Officer bei QuesTek Innovations, einem führenden Unternehmen für Werkstofftechnik, und Gründungsmitglied des medizinischen Beirats von AddUp. „Für ein Krankenhaus ist eine andere Denkweise erforderlich.“
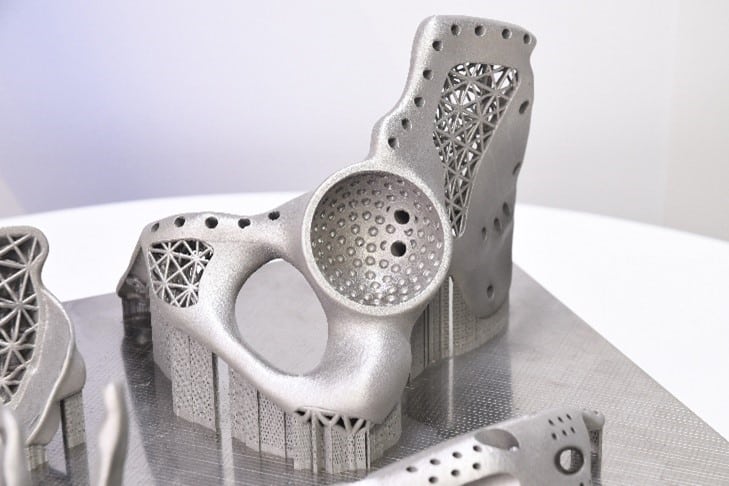
Das AddUp Medical Advisory Board wurde 2023 gegründet, um dem Unternehmen unvoreingenommene, ganzheitliche Perspektiven für die Anwendung von Metall-3D-Drucktechnologien im Gesundheitswesen zu bieten. Severine Valdant bietet Ihnen ihre einzigartige Perspektive als eine der führenden Persönlichkeiten in der Entwicklung von medizinischen Geräten und 3D-Druck. Bevor sie zu QuesTek kam, leitete sie die Umwandlung von Oxford Performance Materials in ein führendes Unternehmen im Bereich der additiven Fertigung und half dem Unternehmen dabei, als erstes Unternehmen die FDA-Zulassung für 3D-gedruckte Polymerimplantate zu erhalten.
Wichtige Akteure erkennen den Wert des 3D-Drucks
Trotz der Herausforderungen, die die additive Fertigung für Organisationen des Gesundheitswesens mit sich bringt, die hoffen, den 3D-Druck am Ort der Versorgung zu nutzen, gewinnt das Konzept unter Führungskräften des Gesundheitswesens und anderen wichtigen Interessengruppen an Akzeptanz.
- Die OEMs machen große Fortschritte. „Wenn die Druckerhersteller eine All-in-One-Lösung anbieten können, ist es viel weniger schwierig, AM am Point of Care zu implementieren, und wir sind nicht mehr weit davon entfernt“, sagt Valdant. Die gute Nachricht ist, dass Unternehmen wie AddUp neue Drucker auf den Markt bringen, die sich problemlos in andere bestehende Systeme und Prozesse integrieren lassen.
- Die FDA ist mit an Bord. „Sie sehen in der Tat einen großen Wert in der POC-Herstellung und arbeiten mit den Akteuren des Gesundheitswesens und den OEMs zusammen, um herauszufinden, welche Vorschriften oder Richtlinien erforderlich sind, um dies zu ermöglichen.
- Chirurgen sind von den Möglichkeiten begeistert. „Ich habe mit vielen von ihnen gesprochen und sie sind ziemlich begeistert von den etools, aber wir müssen aufpassen, dass sie nicht aufhören, Ärzte zu sein und Ingenieure werden“, fährt Valdant fort.
- Administratoren spielen eine Schlüsselrolle. „Sie sind die großen Entscheidungsträger. Wenn wir AM an den Point of Care bringen, müssen sie einen guten ROI sehen.“
Zukünftige Anwendungen
Die Zukunft des Gesundheitswesens ist die personalisierte Medizin und die POC-Herstellung wird dabei eine wichtige Rolle spielen. Wir erwarten, dass es viele neue Anwendungsfälle am Horizont gibt, die die Grenzen der Technologie erweitern und ihre Möglichkeiten ausbauen werden. Dazu gehören Fortschritte bei der Just-in-Time-Herstellung von verfahrens- und patientenspezifischen Einweginstrumenten, die herkömmliche Systeme zu erschwinglichen Kosten ersetzen.
Der Sweet Spot für künftige Anwendungen von POC AM werden Verfahren sein, für die es keine bequeme oder effektive Implantatoption von der Stange gibt – einschließlich komplexer Operationen für Knie-, Hüft- und Beckenrekonstruktionen, Wirbelsäulenoperationen und Tumormodellierung für Krebspatienten.
Darüber hinaus werden KI und maschinelles Lernen schon bald die Automatisierung von Arbeitsabläufen ermöglichen und die Produktion von patientenspezifischen Implantaten beschleunigen, wodurch sich die Entwicklungszeiten von 18 Monaten auf wenige Tage verkürzen. Es wird erwartet, dass sich die Ergebnisse für die Patienten exponentiell verbessern, während gleichzeitig die Operationszeiten und die Notwendigkeit zusätzlicher Korrektureingriffe reduziert werden.
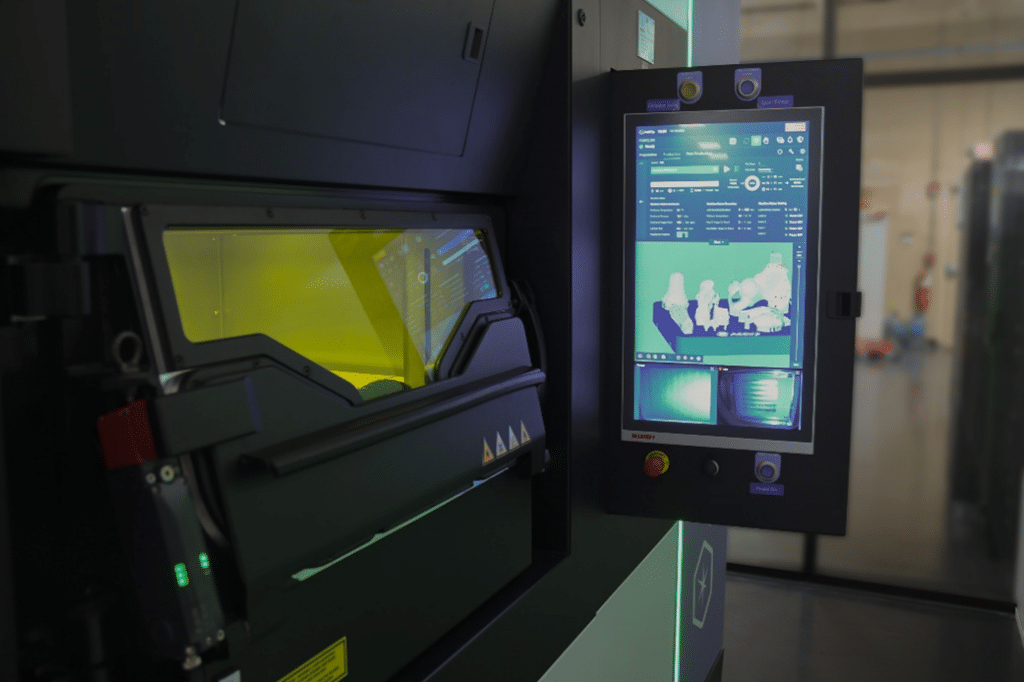
Der richtige OEM
Die POC-Herstellung muss eine effektive Partnerschaft zwischen Gesundheitseinrichtung und OEM sein. „Ich glaube, wir sind heute viel weiter als vor 10 Jahren, weil die Zusammenarbeit zwischen den beiden stattfindet“, fährt Valdant fort. „Mit unserer tiefen Kenntnis des medizinischen Marktes und einer sehr effizienten und integrierten Lösung wird AddUp ein großartiger Partner auf der OEM-Seite sein.“